Thread: Chronos Small Lathe Chucks - Any first-hand experience |
02/10/2023 18:12:36 |
Posted by Andy H
In the search for a replacement chuck for my small lathe (a Flexispeed Mk 2)
I am currently considering Chronos options.
I wonder if anyone has any first hand experience
(including like/avoid views) of the following two chucks?
NEW- 50mm 3 Jaw Chuck ON A 2 MT or
Soba 70mm 3 Jaw Scroll Chuck 14 x 1mm Thread
Andy
-------------------------------
I have 2 off 50 mm three jaw chucks and 1 4 jaw
52 mm self centering chuck ,all three are quite well made
and good value ,the 2 three jaw chucks mounted on their
arbors center to within a couple of tenths , look here at the
photo the fit between the jaws when they are closed
all three are the same.
This 80 mm 4 jaw independent chuck seen here also a Soba
chuck from Chronos is very well made.
John
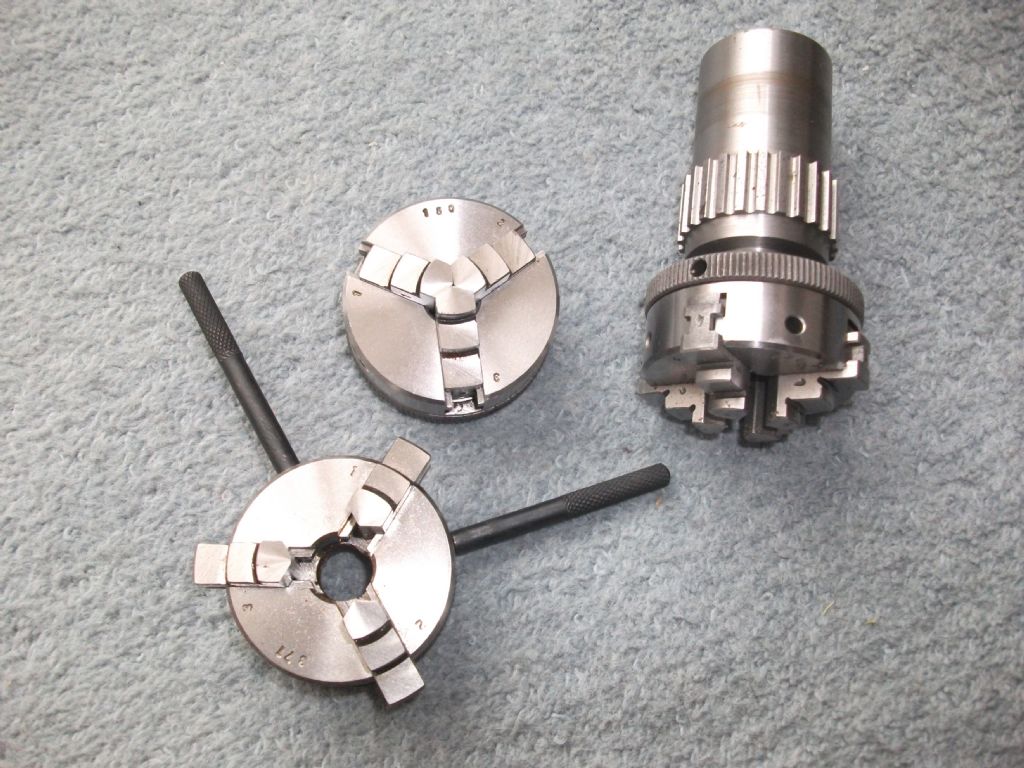
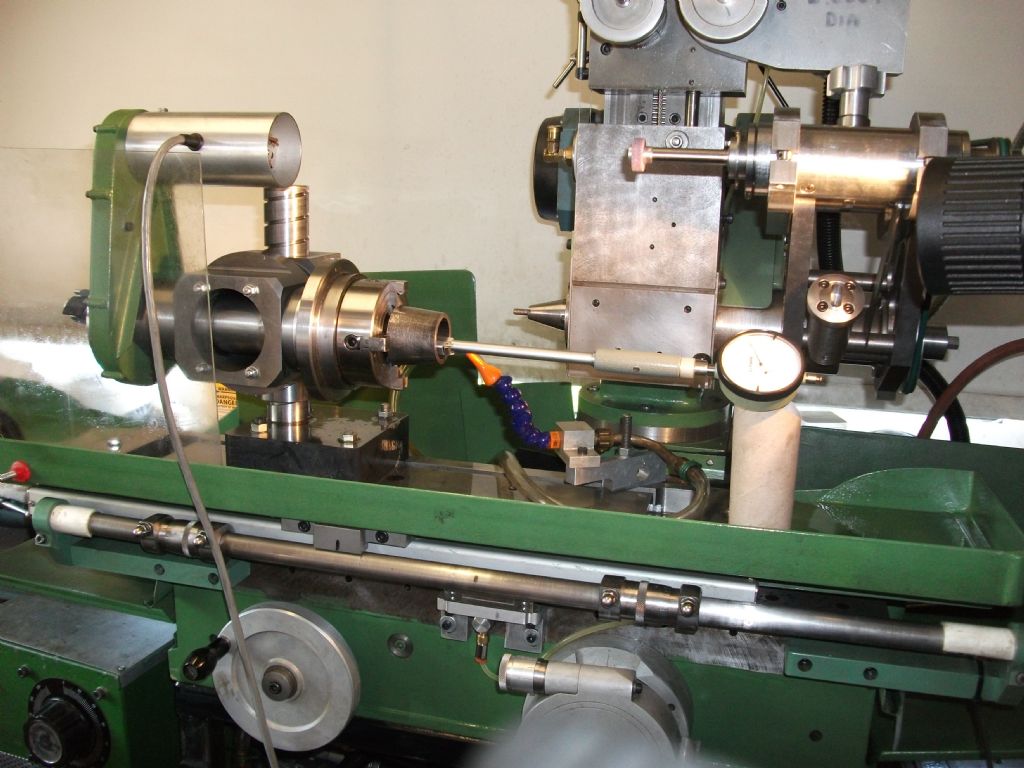
|
Thread: Boil in the Bag : Funerals |
03/07/2023 08:33:00 |
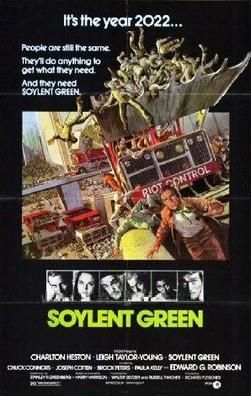
|
Thread: A tool for sharpening milling bits. |
27/03/2023 13:33:59 |
Hi John
Sorry don't know how to link this.
The Quorn site seems a little clunky to use ,but here go's
Log on , go to, Your groups then to Quorn owners,
along the left side listing click on Photo's
If the setting in the right hand box is [Sort by Created v ] (Arrow down )
You should see in the top row far right Cnc cutter grinder build photos
49 photos and below on the left Cnc cutter grinder drawings 47 photos.
I made an error in the last post the text for the build and operation
is in the list below the photo icon as files click on this
and scroll down to (cutter grinder build notes) it is about 25 files
down the list.
click on Cnc flute grinder .txt and it should download the file.
HTH
John
|
27/03/2023 10:26:09 |
The drawings for the machine that Duncan mentioned
can be found in at
https://groups.io/g/Quorn-Owners
including an improved text from that which was published
in MEW around 2008 .Shows how to grind tapered endmills
and methods to check the clearance angles.
It may be necessary to sign up and log in to see the
the photo albums.
The drawings and build notes and instructions for use are in
2 photo albums as jpeg files and can easily be downloaded.
It is as well to point out that the machine uses a Quorn
grinding head and was only made to regrind the side
fluted edges ,the ends are ground on the Quorn grinding machine.
The machine will grind flute edges from about 2mm to 19 mm dia
as seen here.
Some more photo's in my album Quorn and cnc cutter grinder.
John
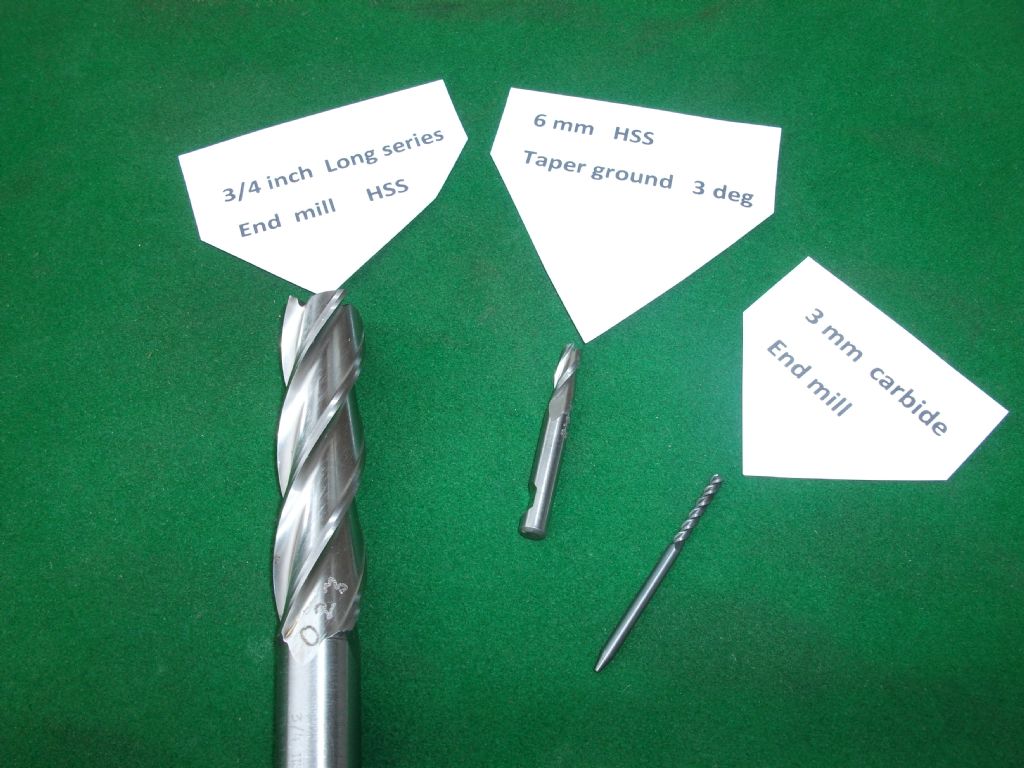
|
Thread: Forum Platform Changes - PLEASE READ |
16/03/2023 15:53:10 |
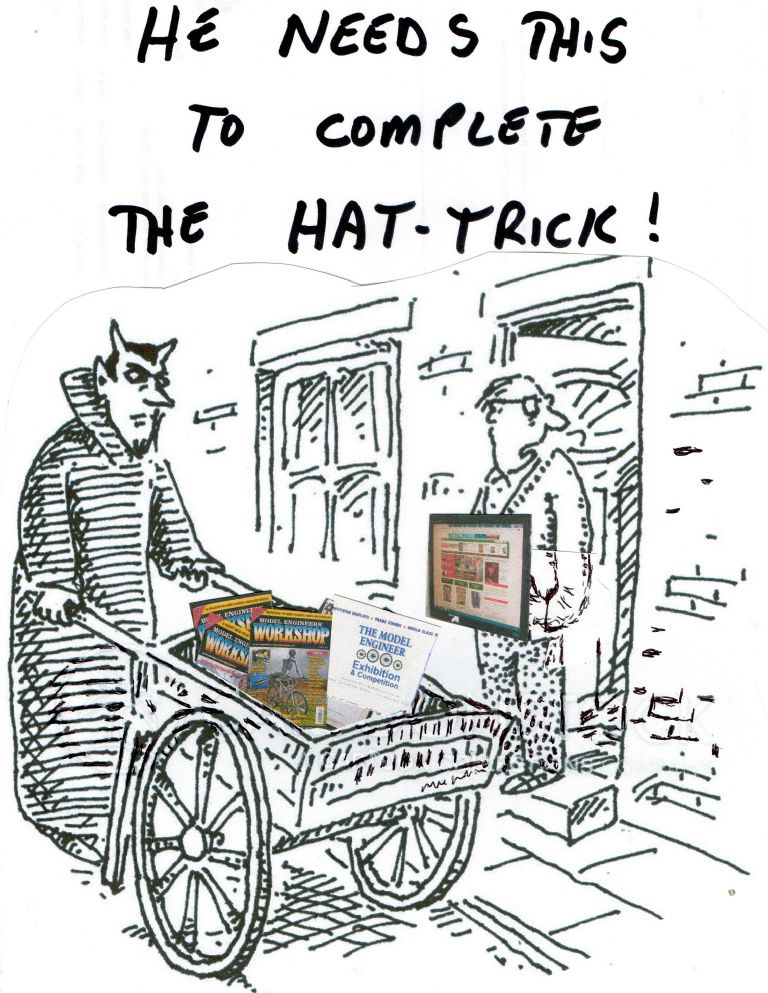
|
Thread: Using a Dividing head |
08/03/2023 14:47:43 |
Without knowing what type of milling machine that you have or dividing head
it would be difficult to answer that question.
For example if the leadscrew on your mill was 8 tpi and the dividing head
was 40 to 1 ratio you would need to gear up from the leadscrew to the
dividing head at 5 to 1 .It is unlikely this could be done in one step
with a toothed belt as the pulley sizes will be large,some additional gearing
would probably be needed as well as a tumbler reversing for left and right
hand thread.
I have done here almost the same as what you are trying to do at 1.480" dia
and 3/4" pitch but with cnc which is a much easier solution as you can
get to any pitch with just a little number juggling.Cant remember what the slot width but was climb milled to finish leaving a perfectly finished thread.
John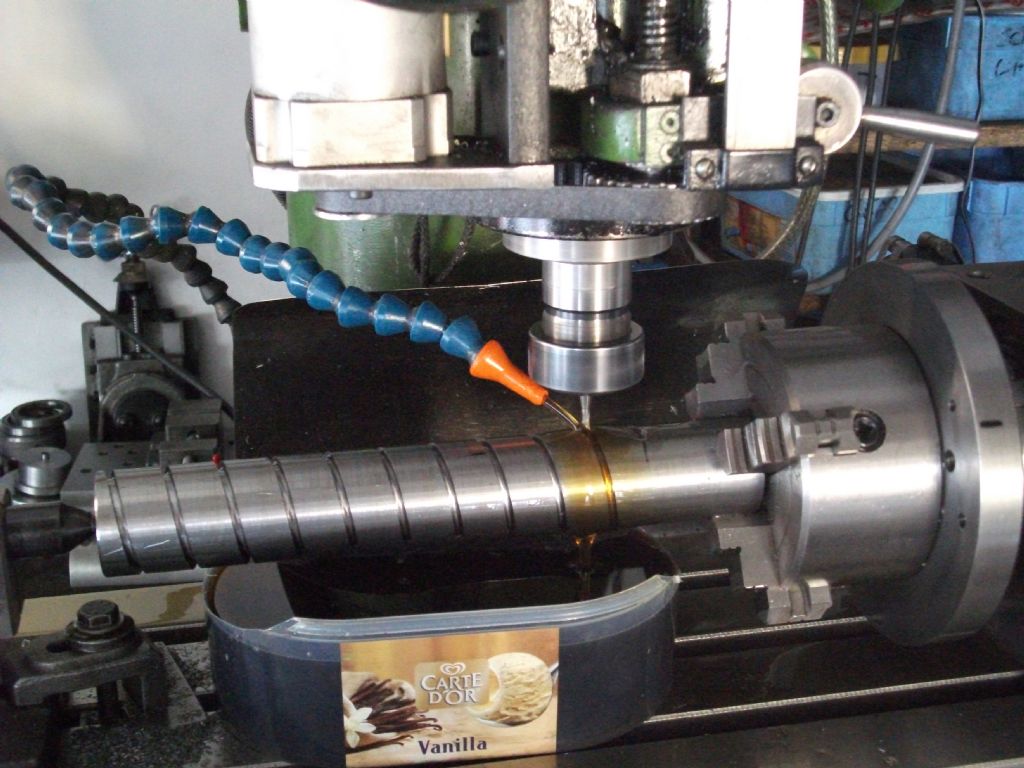
|
Thread: Adjustable device for describing a low angle helix along a shaft |
22/01/2023 10:12:13 |
Hi John,
This video here uses the same mechanism as in the patent.
https://www.youtube.com/watch?v=Pb14T-bDB1g
John
|
21/01/2023 13:43:09 |
This is one of these type of mechanisms that will do what you want
https://patents.google.com/patent/US2503926A/en
The cnc route is by far the easiest the drawings for my own
machine can be found in at
https://groups.io/g/Quorn-Owners
including an improved text from that which was published
in MEW around 2008 .Shows how to grind tapered endmills
and methods to check the clearance angles.
The only thing that you never need to know when doing this is the
helix angle of the flutes /cutter.
John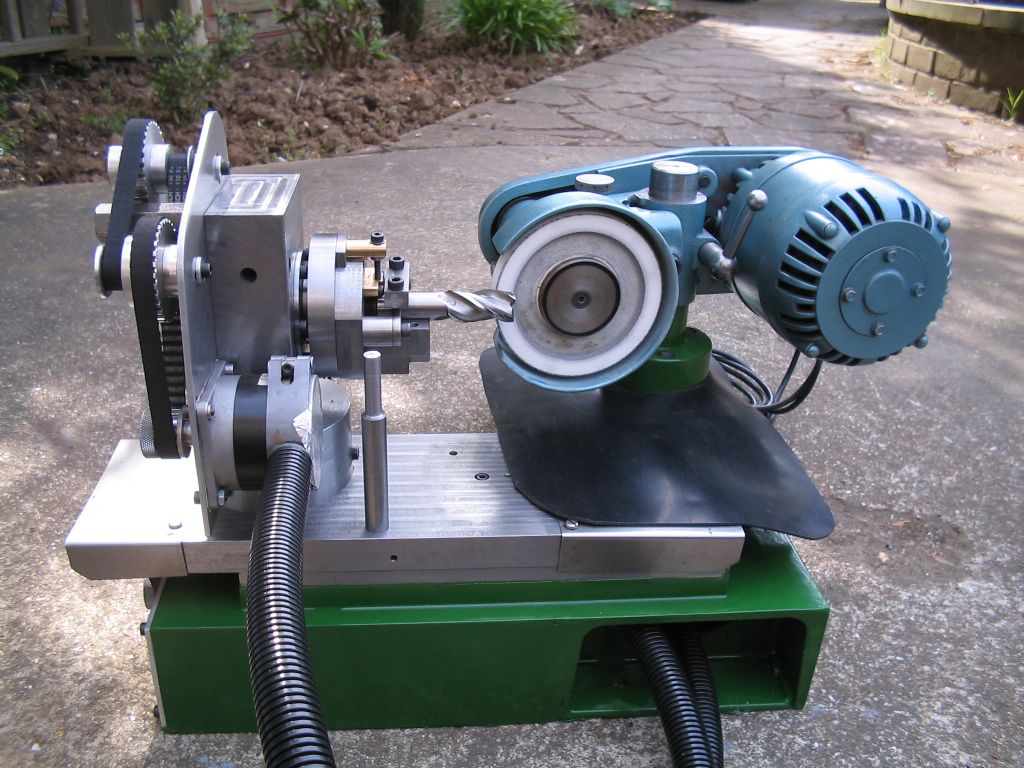
|
Thread: Aliexpress/Bangood and import duty |
09/12/2022 13:15:43 |
It is explained here.
https://www.gov.uk/goods-sent-from-abroad/tax-and-duty
John
|
Thread: Myford S7 with stepper on cross-slide |
01/12/2022 10:20:10 |
Hi Matt,
If you decide to modify your machine in this way and have a rear
mounting bracket there is one other thing that you may need to do.
The rear shear oil nipple is located in position 13 in the handbook
will be difficult to access with a rear bracket in place.
I modified mine and re-positioned close to the locking bolt as in the photo ,it just needs some
careful drilling this needs to be done with the saddle off the machine
at the same time i drilled through a small hole from each of the
diagonal slots on the lower part of the slide through to the dovetail
ways of the crosslide so when the machine is oiled some lube
finds it way to the crosslide.
As far as i can remember the crosslide stepper motor came from
RS was 23 size @ 1.2Nm and on a unipolar system it has always
had enough power ,Myfords can be a problem with cnc it is very
easy to dig in and stop the spindle , mine only has a 1/2 Hp motor
the real problem is the belt drive will probably slip first unless
you have it really tight.
I have the same on a larger Warco gear head lathe it only has a single
stack 34 size motor even with the 1.5 Hp motor it still has enough
power to overcome the spindle.
John
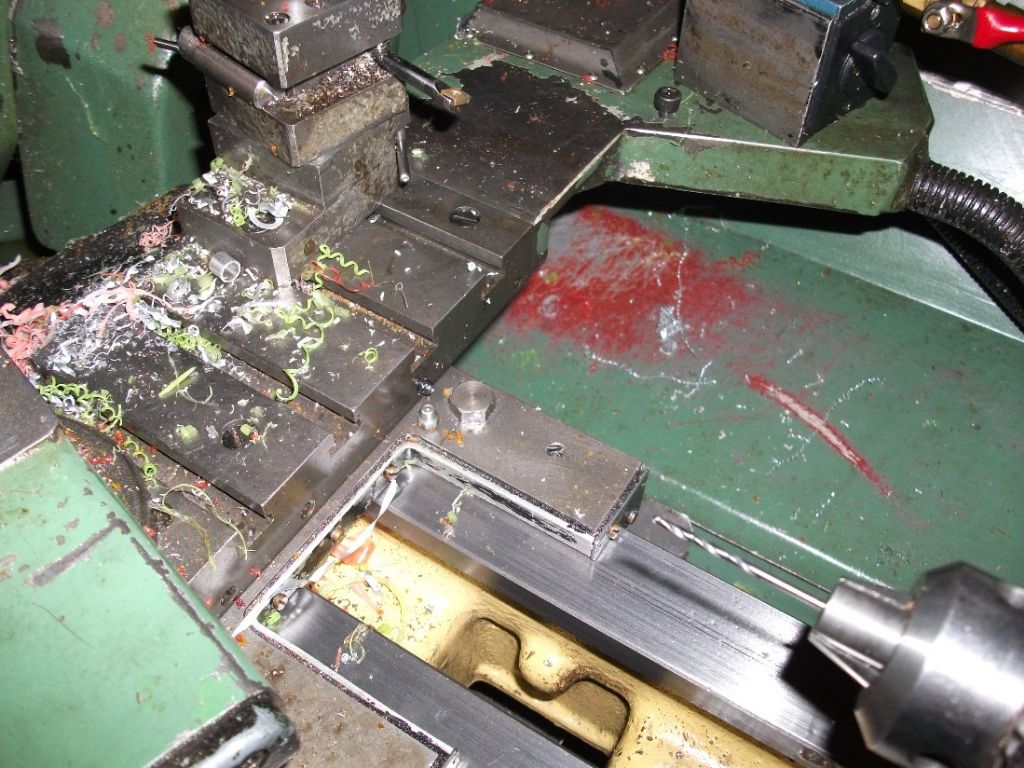
|
30/11/2022 16:32:42 |
Here are some better photo's ,the rear bracket is just fixed with 2 screws ,originally
it was just the location for the BW electronics wire DRO ,when i converted to the
cnc setup i had to alter the bracket to this "Y" shape to be able to fit
the stepper motor and and also the encoder .Fitting at the back of the machine
allows the cabling to be out of the way and you don't have the motor hanging out
half way across the workshop.
I made a new leadscrew to fit the existing nut and it has a top hat oilfilled nylon
nut piggy backed on the original nut ,the small peg hanging down in the photo 3
allows the second nut to rotate to adjust the backlash ,the retaining housing uses the
existing screw fixings and clamps up the second nut to retain it .You can see
here in photo 4 the plain part of the new leadscrew and the solid coupling.
It is not really necessary to use a ball screw if you are intending to keep the machine
as part manual use it would be better off to retain the existing setup ,its 17 years
since i changed this screw there is very little wear present ,in any case it is only £7
of material and few hours work to make a new one .
I have 7 machines that have been made or converted to cnc none of them
have ballscrews all except 2 are part manual use ,they all use the same cnc
system "Compucut" an old system now but still very reliable, on the Myford
i unplug the crosslide axis when it is used manually and use the Compucut
system to drive the leadscrew for power feed.
John
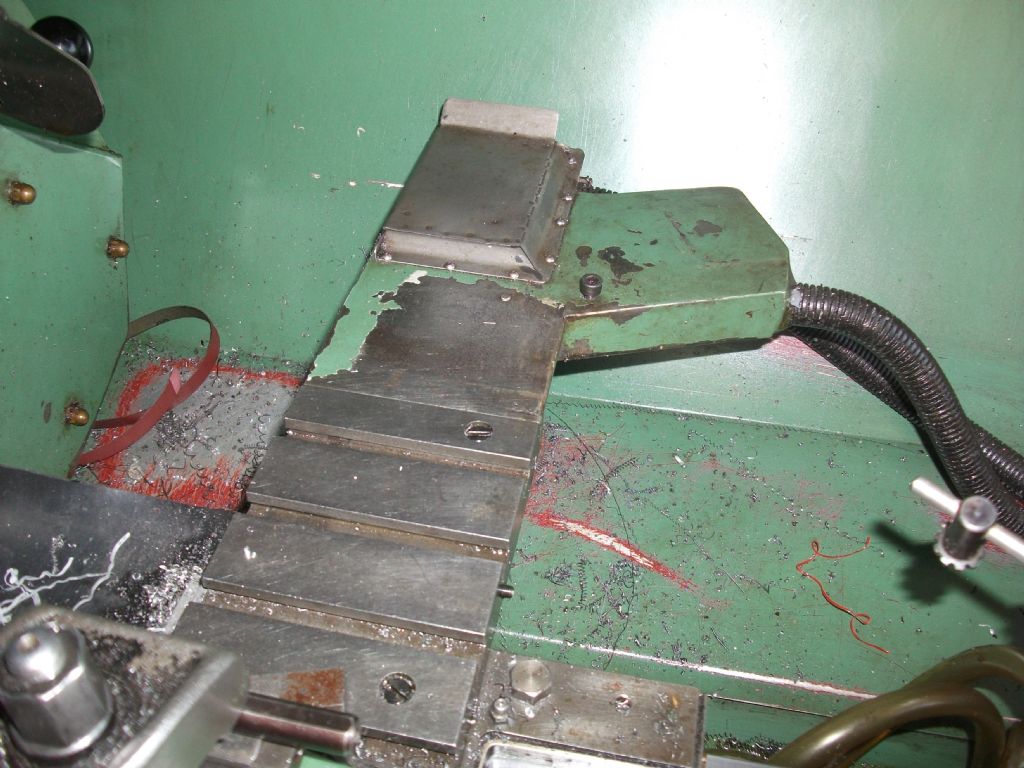
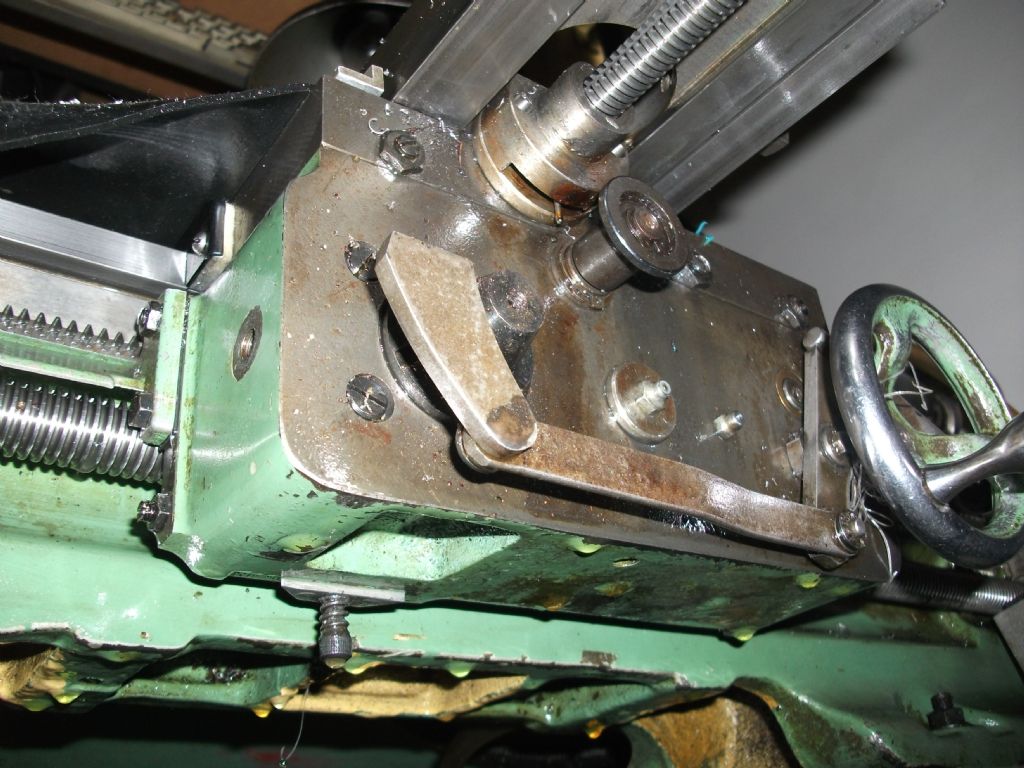
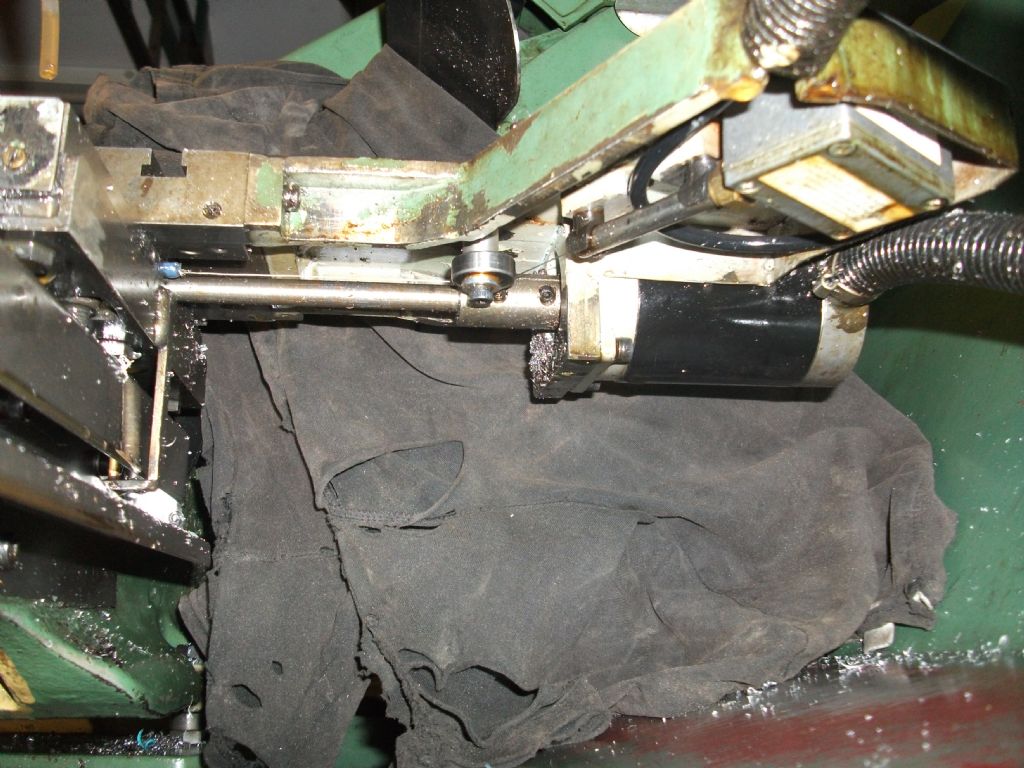
|
29/11/2022 16:29:35 |
I converted my Myford about 17 years ago the stepper motor is
mounted on the rear bracket at the back of the crosslide.I made a complete
new leadscrew and anti backlash nut and new front bracket to keep
the slide clear of swarf, the motor is joined to the leadscrew with a solid coupling.
John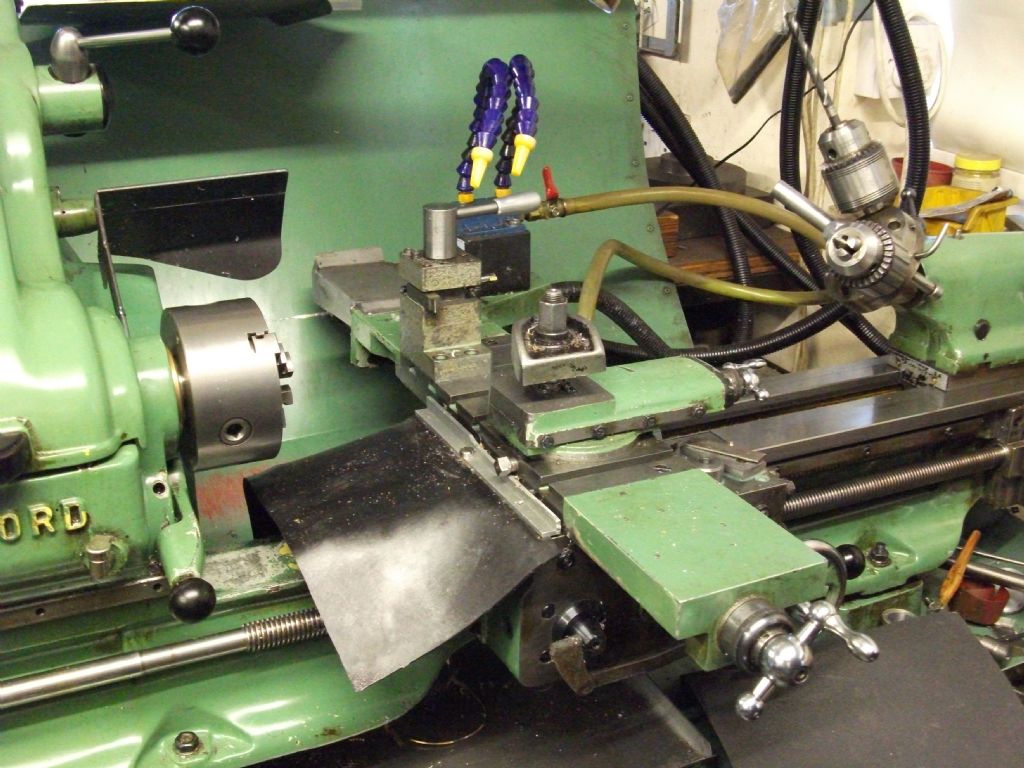
|
Thread: Looking for a cylinder hone. |
25/11/2022 10:22:28 |
I made this honing tool that was published in Mew 207 .Made up
from scrap oddments , has strips of abrasive paper or cloth and
lead strips glued to pressed out pre-formed shoes .Simple to make
works well.
Used to hone the cylinder of this hot air engine.
John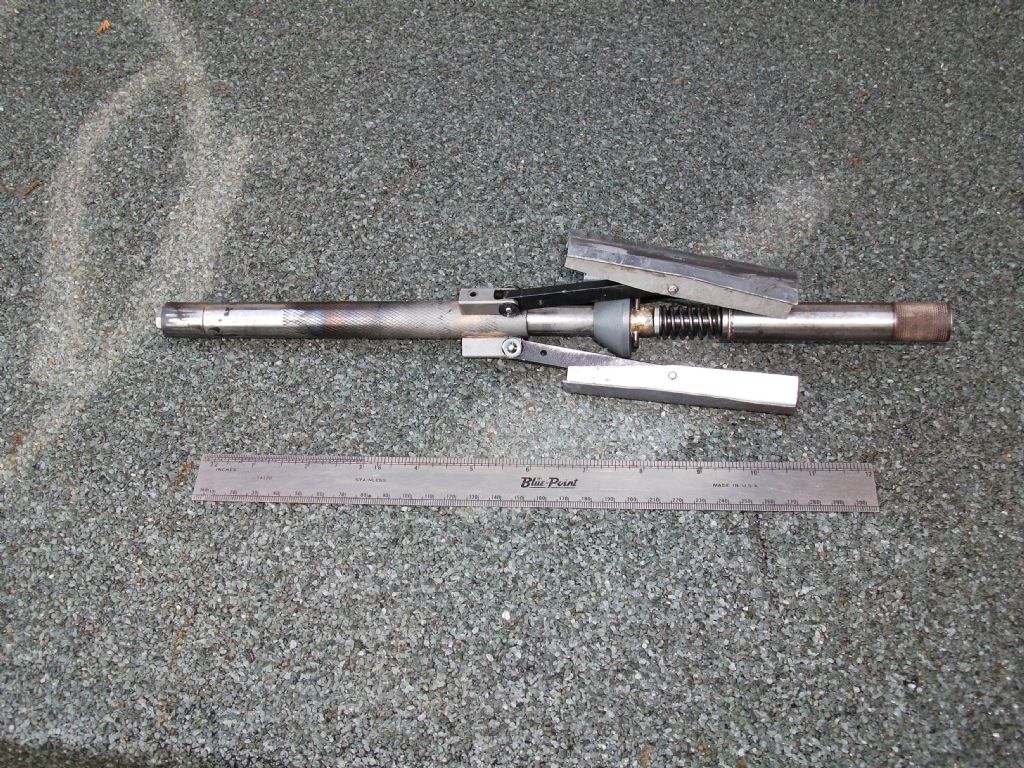

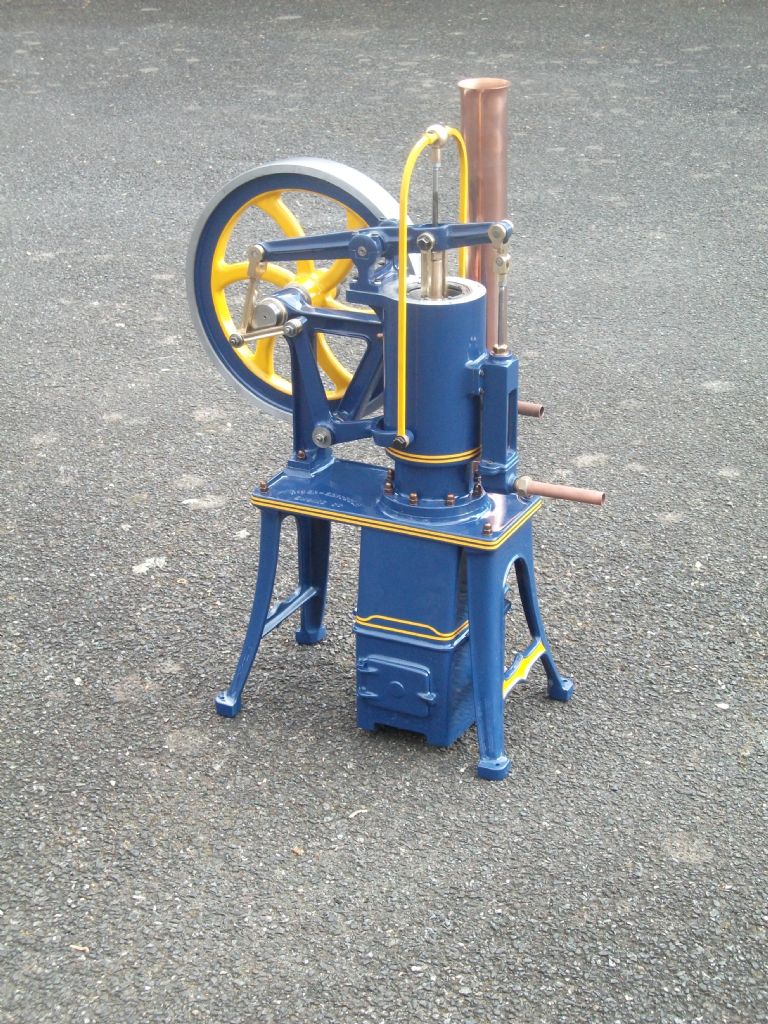
|
Thread: Hobbing on horizontal mill |
23/11/2022 19:15:08 |
Posted by Bazyle 23/11/2022 18:41:45
This comes up every now and again on here and on the HSM forum but can be buried in
threads with obscure titles.
There isn't a simple plug and play system nor even a simple
Arduino/pi/other system for sale like the electronic leadscrew options.
John initially
had a pure TTL logic chip solution but later converted to a computer based system
somebody developed for him, which as far as I know has not been made
commercially available.
However a couple of people on here I think have got it sorted, but they
are advanced electronics tinkerers.
----------------------------------------------------------------------------
This part is not true
"There isn't a simple plug and play system nor even a simple
Arduino/pi/other system for sale like the electronic leadscrew options"
Richard Bartlett designed and made the "Compucut Syncron" system
which i have ,it did not have the shortcomings of the published
circuit that was in MEW 108 but is a system that actually works
properly.
As far as i know the system is still available ,when i spoke to
Richard a few years ago he still had about 10 or 12 pcb
boards.
You still have to make up the head and work holding spindle to
suit the machine application ,was in Mew 193 also some
photo's in album gears.
John
|
Thread: Retro-fit speed control to battery grinder? |
20/11/2022 15:06:26 |
Don't know if it is even worth trying to make something as in the last posting as you can buy this from Aliexpress for about £8
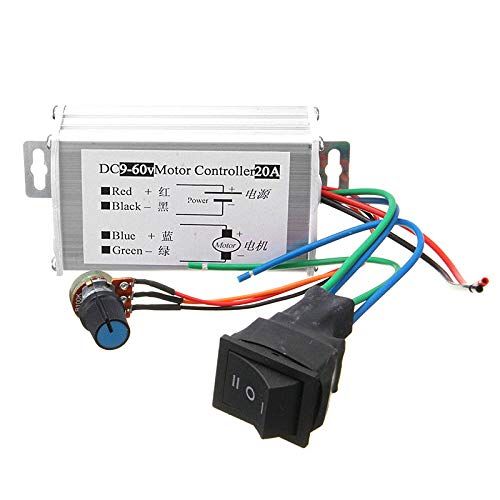
Won't put up the reference number as it will probably be taken down if you need it just send PM.
John
|
20/11/2022 10:15:13 |
Found this circuit out there for soft start motor control at 48 volt but uses
2 x 555 ic .
https://www.homemade-circuits.com/pwm-motor-soft-start-circuit/
may be of some use.
John
|
Thread: VMC Mill spindle runout |
13/11/2022 16:46:46 |
Posted by John D 13/11/2022 15:58:27
Thank you for the reply, Brian. It's an R8 taper and I don't have any R8 drills, only ER32 and
Clarkson Autolock collets. I don't seam to be getting much worse a reading when the quill
is lowered. I have measured on the inner edge of the taper and the outer edge of the spindle
nose and get the same reading. I bought it from a guy who i thought reputable and well
thought of on here. I've spent ages fitting a 3 axis DRO and now gutted to find this.
I can't find much info on line about the Myford Taiwan imports and which other branded
models might share the same spindle. (e.g. it doesn't have fine feed quill) Is there any
way of re-machining the taper to take out the runout? Is replacing the spindle the
answer - if indeed i could find one? The parts diagram is pretty unclear - i'm not sure
how to remove the spindle.
-------------------------------------------------------------------------------
The spindle on my Warco A2F has about .0002" run out at the lower edge,the
top end the parallel part has some runout also ,i just make arbors to suit
what i need and finish them in situ as there is a locating pin they allways fit
back is the same place with zero runout.
Lowering the spindle won't make any difference to the run out reading.
It would be possible to regrind the tapered part of the spindle in its
own bearings on the machine as you can set over the head to
the required angle and use a toolpost grinder mounted on the table
providing the bearings are good , but is not possible to regrind the
upper parallel part for obvious reasons .
There is in my album for the A2F mill the complete handbook
which has a parts list ,i don't know if these machines are identical,Chester
still sell this machine as as the 830 VS so may have or be able to get parts.
John
|
Thread: Test dial brand query |
02/11/2022 09:09:20 |
I bought two similar indicators from "express with Ali" for £16 delivered , they are still available now at £9 each.
John
|
Thread: Manual for Warco GH750 or Chester Cub 630 |
16/10/2022 13:49:22 |
Hi ,
Did you manage to get a copy of the manual for this machine.
John
|
Thread: Myford VMC rough rise fall Z axis/ knee |
16/10/2022 12:06:09 |
Posted by John D 15/10/2022 21:51:34
Does anyone know if it might be possible to obtain the elevation gears for the Myford
VMC anywhere? I suppose best bet is knowing which machines it was the same as
(at least in respect of the gearing for Z axis). Mine has some roughness when
lowering the knee and, although better on raising, still not perfect. You hear a
click click click on when lowering. Everything has been cleaned but i cannot
see any way of adjusting the gears.
Wondering if they are all like this?
Photo of gears cleaned up and with the retaining washer and nut removed.
All greased up with fresh grease but no different.
--------------------------------------------------------------------------------------------------
Those gears look about normal and are much the same on my Warco
2 AF mill ,the backlash on my machine is shown as 0.0015 " on the
index dial so you look to have excessive backlash on your machine.
As far as adjustment goes the knee and gear shaft sleeve as depicted
in the following images are 2 separate parts 102 and 105 ,i expect the adjustment
for the backlash is made on assembly after which the these parts are filled
and eventually painted over to look as one piece.
You can soon tell if this is so as if you feel up inside the casting you may
find the holes or bolts protruding.
Even if you find a supply of new gears they may fit exactly the same if
the adjustment was out from new.
It may well be possible to adjust the mesh unfortunately it would mean
digging through the filler and paint to find the bolts to dismantle and
adjust.
When i got my A2f from Warco these 2 gears were very rough in operation,
i mixed some green label fine Timesaver abrasive in with the grease and
after a short time they were as smooth as silk ,this abrasive is non imbedding
and can be left on as it eventually becomes inert , i use this grease on these
gears "Rocol 18302 Tufgear Universal Open Gear" it is more suitable.
You could turn off about 1/8" off the top of lead screw gear and refit it with
a 1/8" washer underneath likewise also with the input gear to
establish a new contact point on the gears.
John
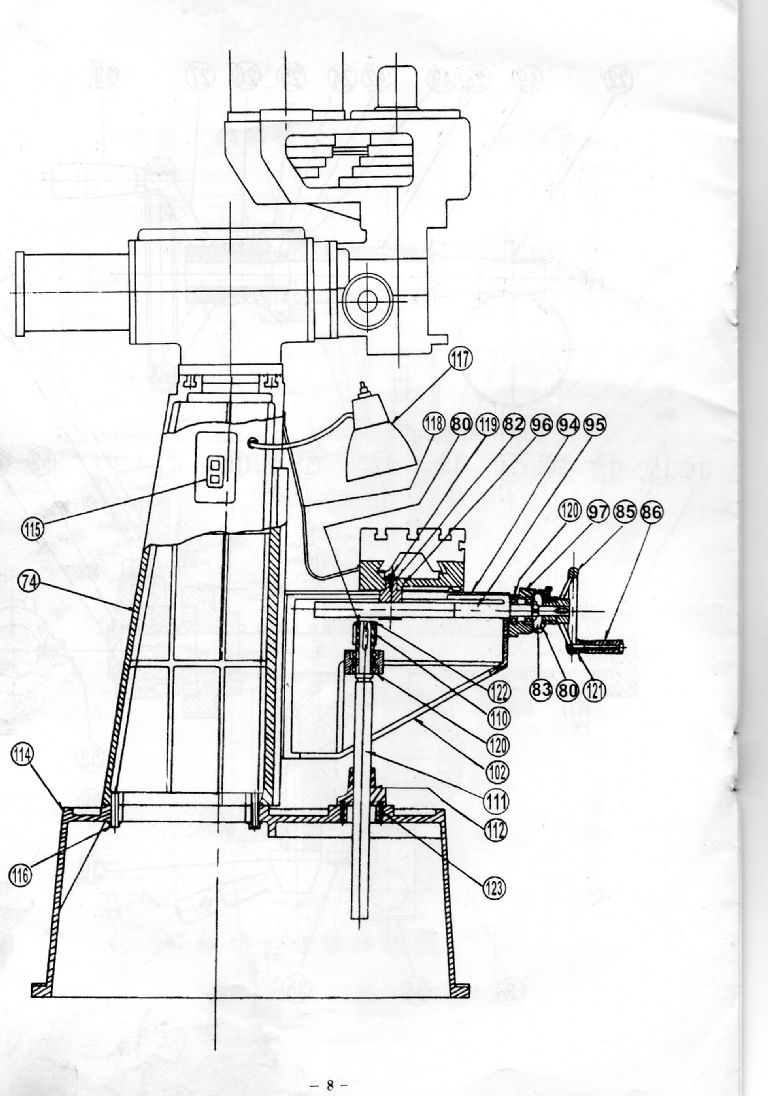
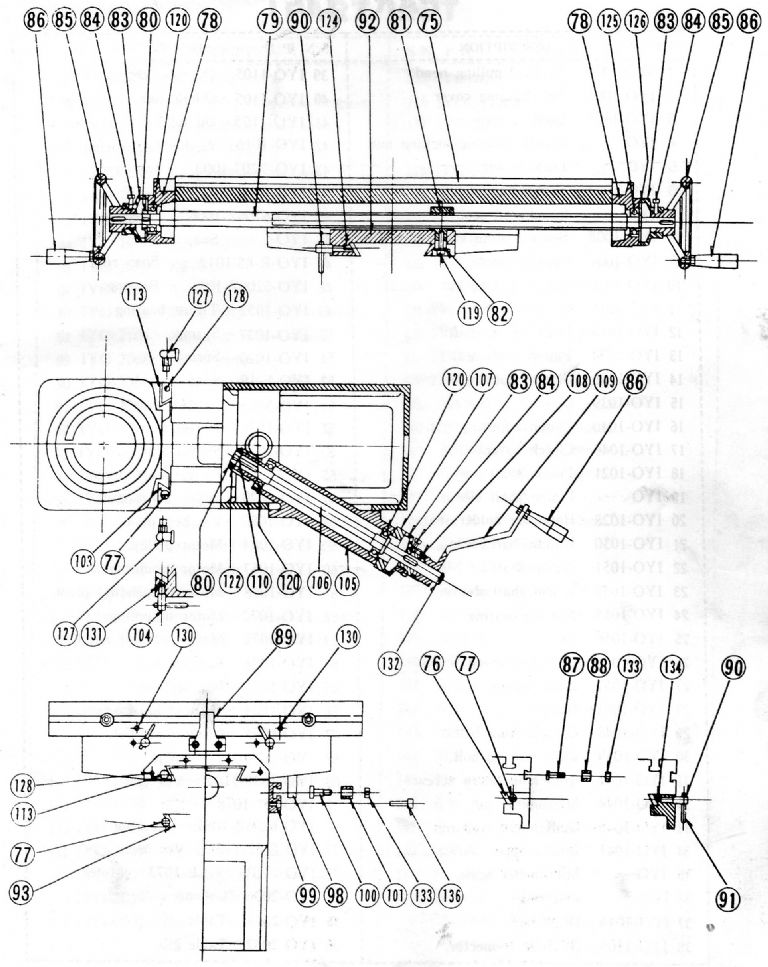
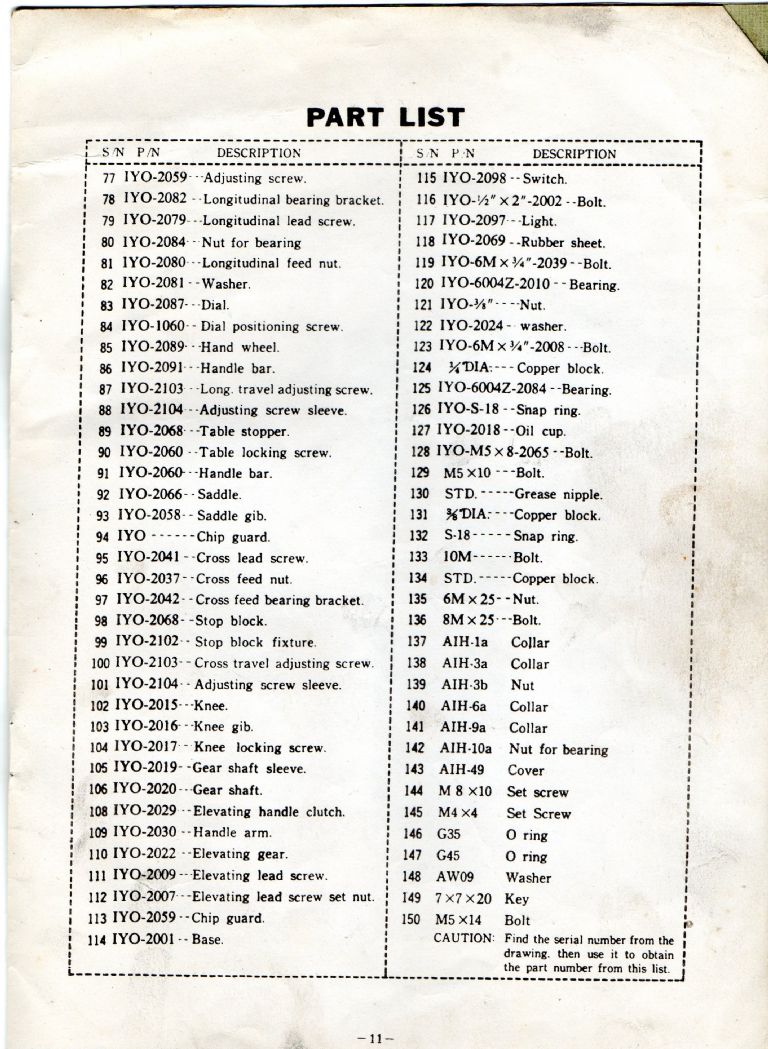
Edited By John P on 16/10/2022 12:07:02 |