Thread: cutting spur gears on a mill |
19/08/2021 12:51:52 |
Posted by brian jones 11 19/08/2021 12:05:43
"Seems too good to be true"
That's probably because it is ,the way forward is for you to give it a try
and let us all know how you get on.
Most good engineering requires some commitment in time and inevitably
some cost for tooling .
Here is a photo of some spur gear hobbing ,i can tell you where you can
get all of the items needed to do this , some of the links will
be taken down almost instantly by the North Koreans so if you want to
know you will have to send a PM.
John 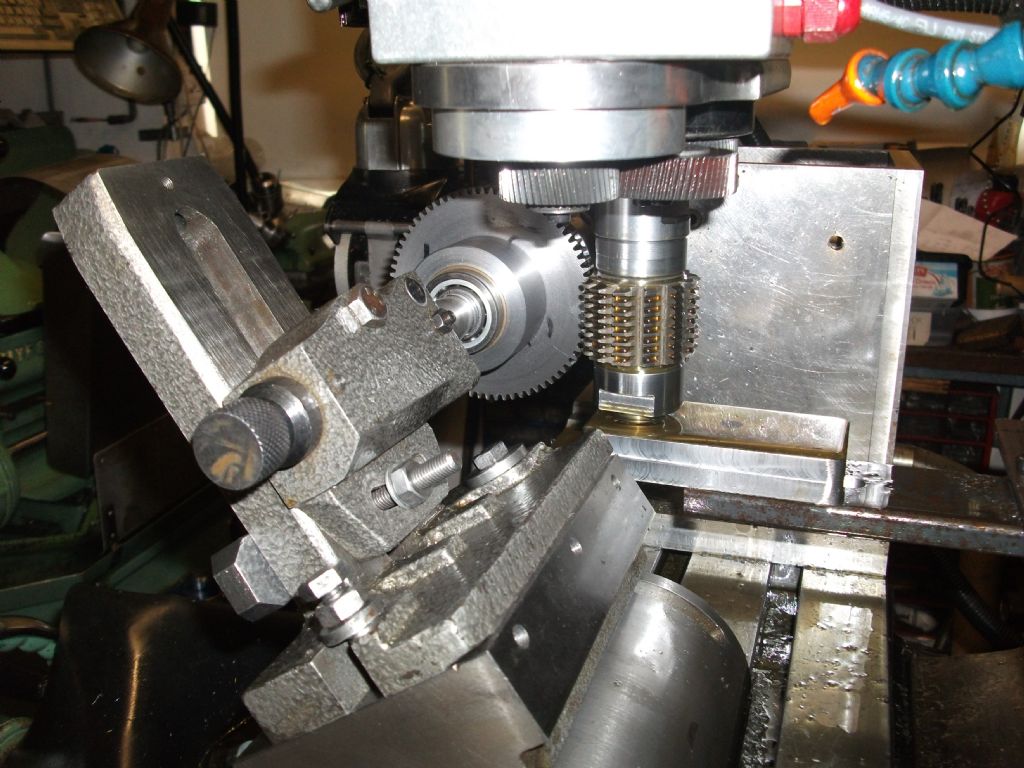
|
Thread: small toothed belts |
19/08/2021 10:23:37 |
If you are able to find a copy of MEW 164 there is an article in there "form
relieved toothed belt cutters " June 2010 for making cutters for
1/5 " XL ,3/8" L and 5 mm HTD pulleys and the calculations
for the pulley sizes.
John
|
Thread: CNC Lathe Scratch Build |
17/08/2021 09:11:05 |
Hi Joe,
The dovetail cutter you mention was back in 2017.
Here is a photo of the two cylinders as you can see
the construction is very simple, i only needed a connecting tube
of 4mm OD as the grinder movements are small and fairly slow,
the down feed when in cnc mode is 0.00001 inch. per motor step,
perhaps more important is the tube does not place any load
on the in feed axis of the grinding wheel as this can feed in increments
of much less than 1 um if needed, i would think that if you were to use
a similar system a larger connection tube would be needed to cope
with the greater axis speed.
John
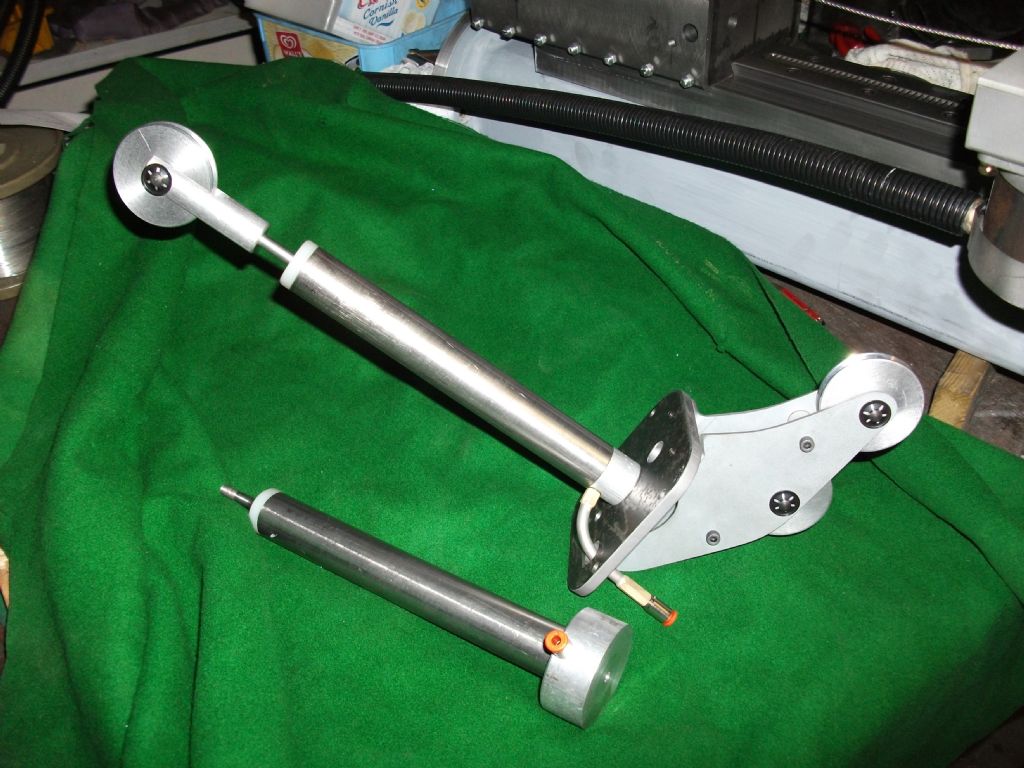
|
16/08/2021 22:36:46 |
Posted by Joseph Noci 1 17/07/2021 20:52:35
The ATC weighs around 7kg. That is quite a lot of weight at a 45deg slope on the X axis. I
am looking for some way to counterweight the X axis. A counter weight and pulley
arrangement won't work as the weight would have to move with the Z axis and so
flail about...I am looking at the possibility of a gas strut mounted in the plane of the
yellow line in the image below - Anyone had any experience with such an implementation?
Or any other ideas?
Hi Joe,
I faced a similar problem with the Zaxis down feed on the Universal grinding machine
that i made ,except the axis was vertical and the weight it had to counterbalance
was about 80 lb ,there was not enough room within the hollow column for a suitable
size weight . A pair of cylinders were made from some smooth bore stainless
tube and just using O rings for seals .the sketch shows the layout ,the 2 cylinders
are connected with some nylon tube ,just used 32 grade oil ,the pressure in the
system is just over 350 psi and has worked well for over 8 years.
One hydraulic cylinder fits inside the column the other is remote in the corner
of the shop out of the way.
As you can see here in the photo the cable supports the the head slide both
grinding spindles and the motor and drive assembly.
This did appear as an article in the Model engineer
hydraulic counterbalance published 4494 30 oct 2014 and 4496 28 nov 2014
they made a complete mess of the article drawings missing some redrawn
and published twice the photo's were just ruined.
The force remains constant over all of the travel as it is just gravity and it
is simple enough to adjust to the load that you require.
The counterbalance weight can be remotely located in any convenient
spot.
John
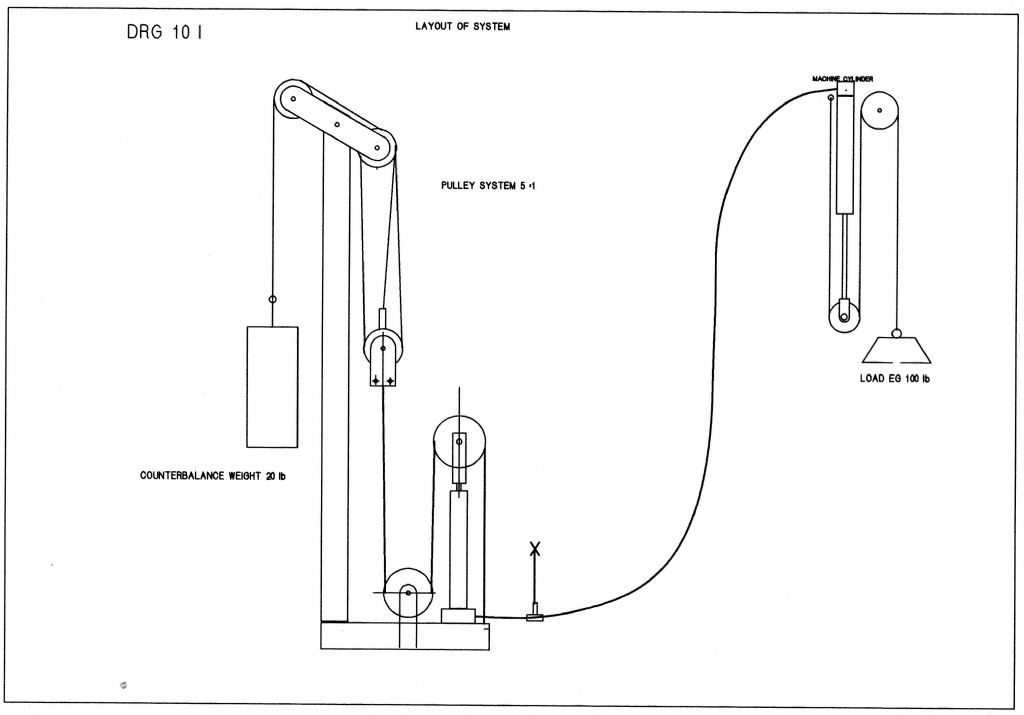
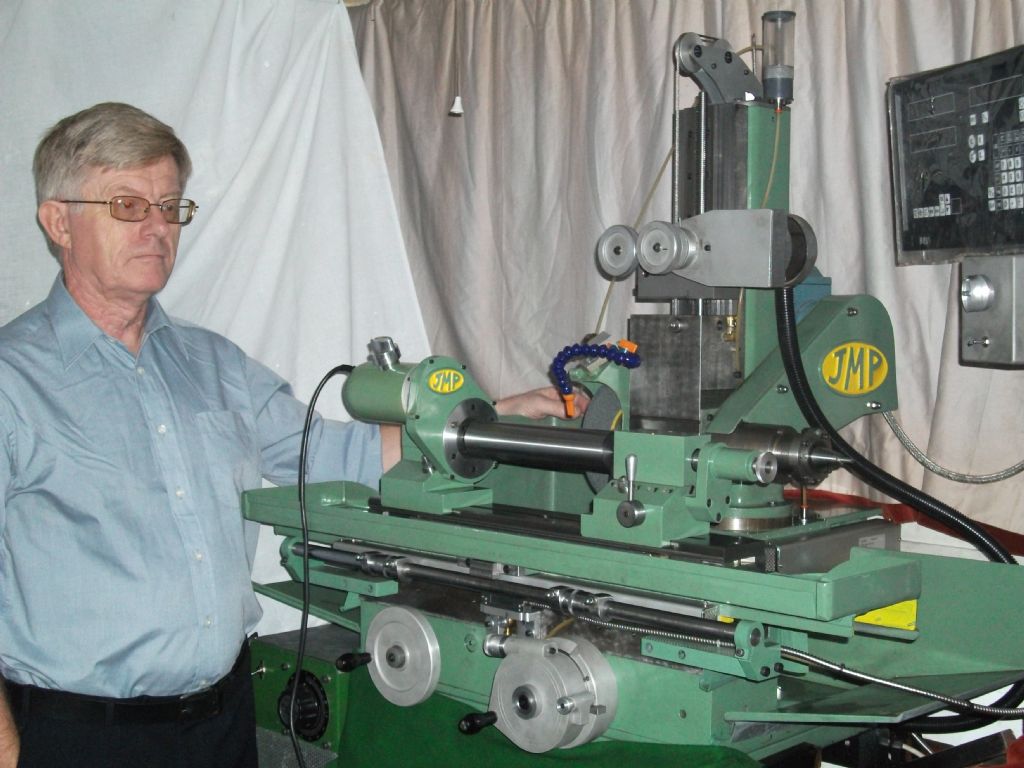
|
Thread: surface grinder |
11/08/2021 09:57:32 |
Grinding it seems to be a much neglected subject on the forum here and also
in the magazines.
I looked at the Warco surface grinder some while back when it was just over a £1000,
they seem to be well made but with only a 12" x 6" is a bit small for some things.
I think they derive originally from the "Macson" surface grinder in Lathes UK and are seen
as Warco, Tormac and various other clones ,difficult to use with any sort of coolant
systems without some extensive modifications.
The 540 machine great if you have room for it and can find one for a good price they seem to
be around the price of the Warco machine and upwards ,don't know how good they are at
that price range you may be lucky or end up with a lemon ,in any event the spares
are expensive have a look at JUBILEE MACHINE TOOLS their starting price
for one of these is around 18K.
The other option is to make your own or modify an existing machine tool ,some
issues back in MEW Alan Jackson used a Dore Wesbury mill as a base
for a small surface grinder.
Arc Euro sell replacement milling tables,it would not take much to fabricate
a small machine using one of these or similar ,would make an interesting
project.
John
|
Thread: DIY Compression spring |
10/08/2021 09:08:27 |
If it fails you can get a suitable spring from here for about £4
<online>
John
Edited By Neil Wyatt on 12/08/2021 19:31:36 |
Thread: Custom Thread Sizes |
06/08/2021 19:03:11 |
Posted by ALLAN QURASHI 06/08/2021 14:35:45
ega, your right about a travelling steady, especially on a twangy 1ft length of mere 1/2" dia, and
worse still if cutting an acme thread I suspect. I was going to try and make one, but hopefully
will be getting a real one soon.
To avoid all of this have a look at the articles in MEW 241 to 243 Milling lead screws.
Cut to full depth in a single pass, left or right hand makes no difference,
3 off lead screws here all 10 tpi longest is 20 inches of thread 1/2" dia in EN 8.
John
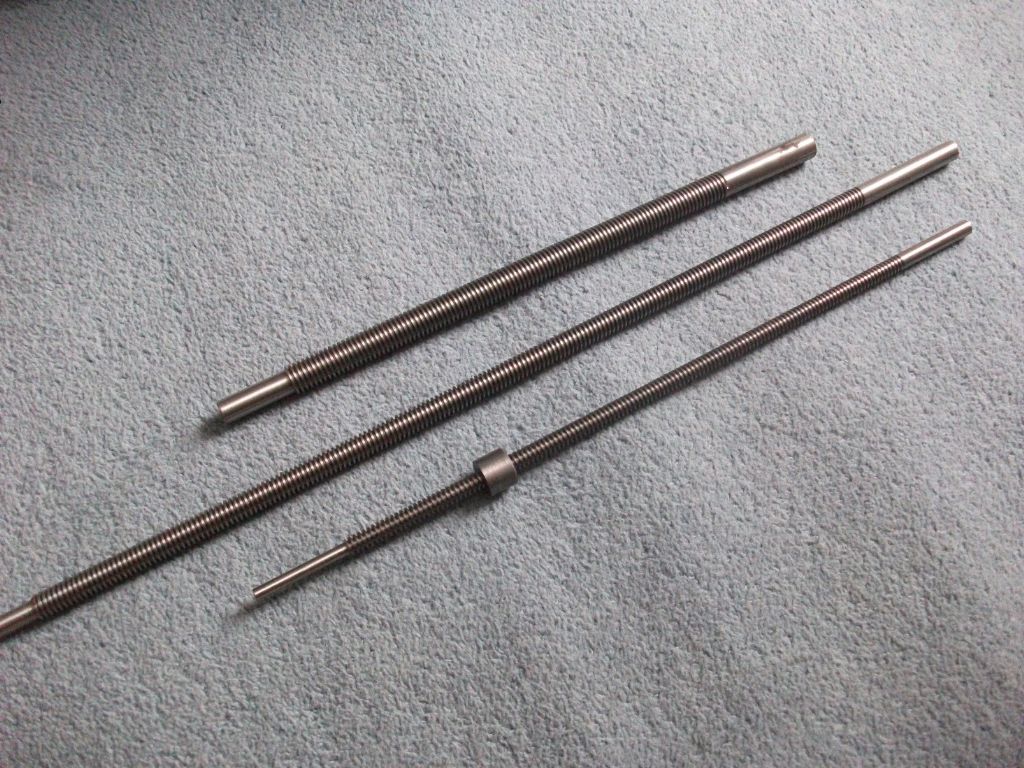
|
Thread: Install & commission of a Chester Cub 630 (Warco GH750) |
18/07/2021 19:12:08 |
Hi Callum,
Here is the D15 socket on my Warco lathe ,the only makings here are
as you can see ,when the two marks align the stud is unlocked.
The photo that you have shown is a more normal representation
for a D mount arrangement the two > < indicate the position
of the mark on the spindle flange providing the socket line is within the
two marks the chuck is locked.
I would guess that your chuck has been tightened for some time
and the studs seem over time to grip quite strongly ,as you have said
from the open position at the 12 o'clock the socket is rotated
clockwise to stop at about 5 o'clock in the locked position.
Is there any reason that they should be rusty ,is there any rust showing
around the chuck or anywhere else.
The key shown here has a lever shaft of 10 mm dia and a bit tougher
than mild steel.
John
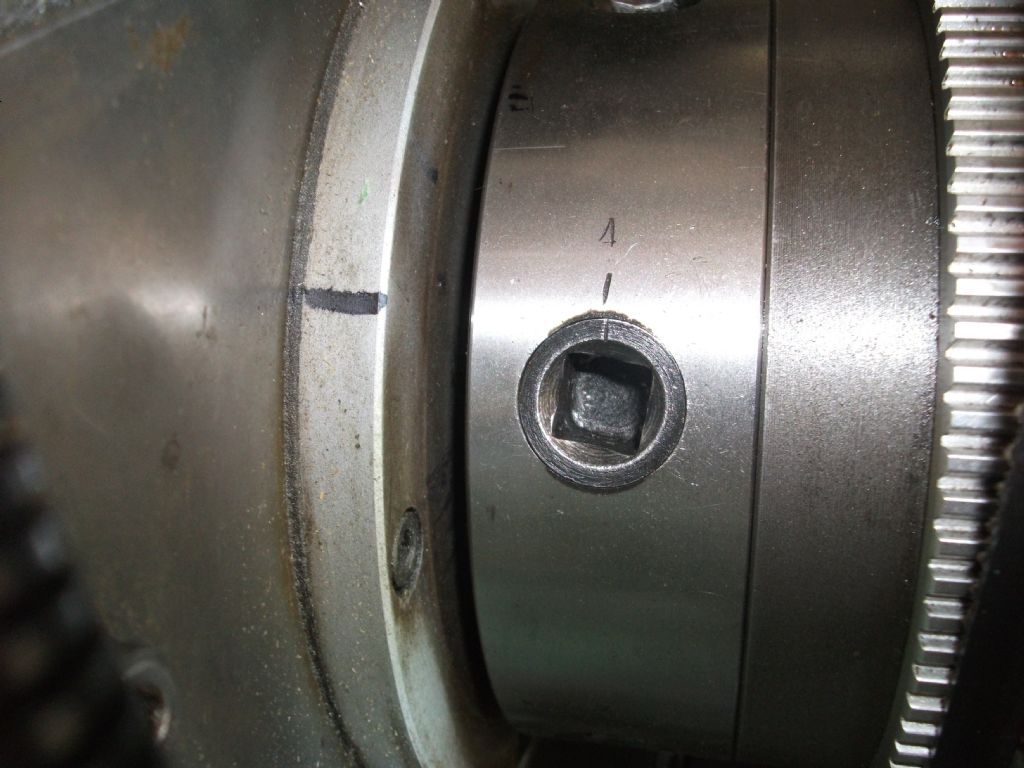
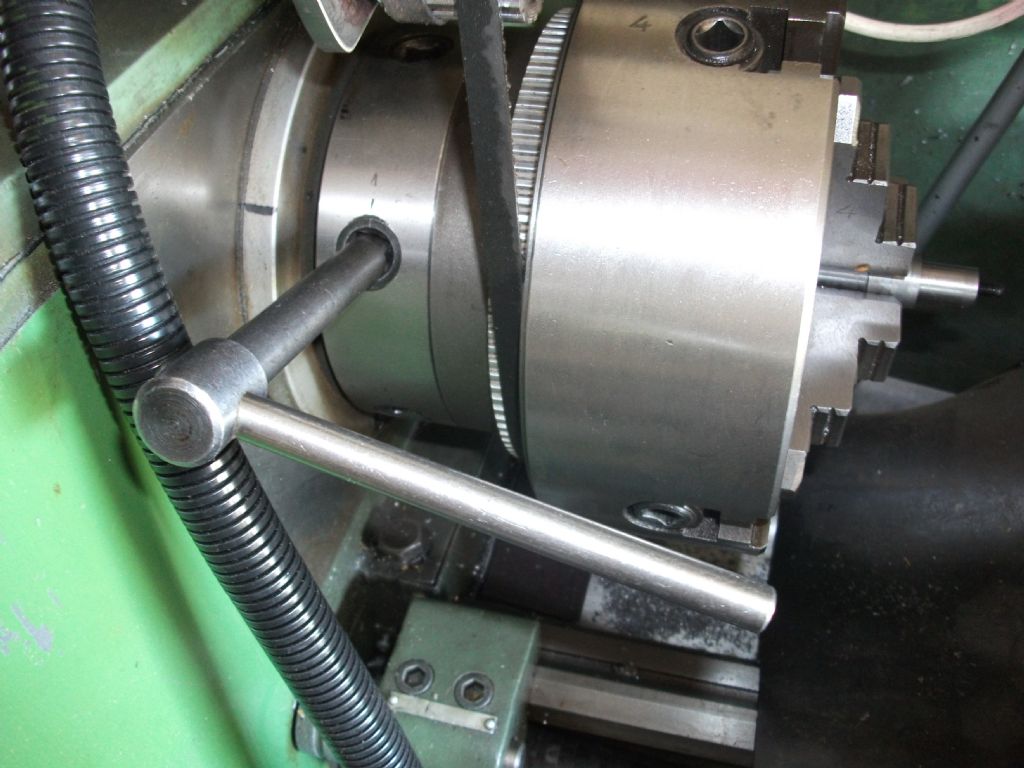
|
Thread: Lower back issues |
18/07/2021 11:13:46 |
This was in the Daily mail a few months ago ,it seems still to be in the trial stage ,hopefully it will eventually get out there to relieve some of these problems.
John

|
Thread: Cylinder drain cock thread? |
09/07/2021 19:58:43 |
Posted by Bill Davies 2 09/07/2021 15:12:46
Mike now has many options for reproducing the thread; does anyone have a
design for a shadowgraph type projector?
Bill
Not really a shadowgraph but a cheap alternative.
Was in MEW 189 to 191 in 2012.
A ground screw cutting toolbit comparison with a 55 deg
12 Tpi Whitworth thread gauge.
John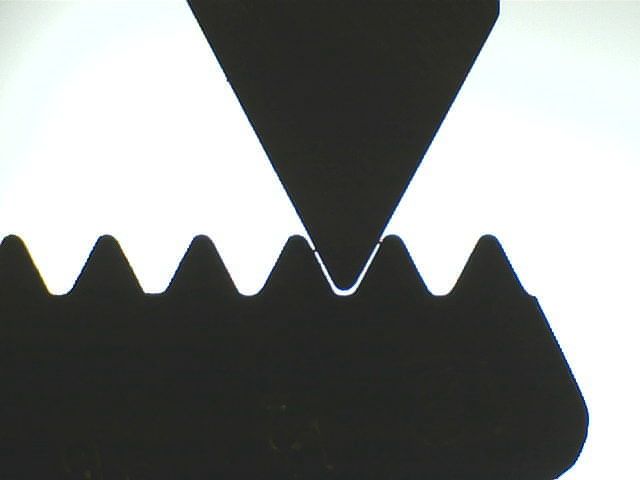
|
Thread: Install & commission of a Chester Cub 630 (Warco GH750) |
06/07/2021 09:42:52 |
H Calum,
Previously i had written ,
If you look at the 3rd panel down on the change wheel chart 8 columns along mm per rev
you will see the listing 2,4,8 and above A36 B27 D28 E30 .
On reflection it may be possible to do all of the metric pitches from 0.5 through
to 9 mm as you have the 28 ,30 and 36 tooth gear the B gear in those columns
that show as A,B and C , the B is the idler providing you can bridge the gap between
The A and C gears with one of the remaining gears it will work.
My machine is similar in that the splined hubs revolve on the plain shafts and as
such could be replaced as in your situation where that you do not have a full set
of change wheels, you will have to remake or modify the hub that is the A gear
stud this links the 45 tooth 2.25 module gear that provides the drive from
the lathe spindle via the 2 17 tooth gears . The 45 tooth gear
is also mounted on this same splined hub as the A gear.
The drive out from the machine here is at 1/4 spindle speed and i expect
that is why the change wheel gears are 2.5 module as the speed drops
so the load goes up in the same proportion. The bonus here is the
change wheels are very quiet in operation as even at top spindle speed
at 2000 rpm the change wheels are at only 500 rpm.
It would still be worth trying to get the missing change wheels to avoid
a lot of extra work.
It is well to note the outer diameter of the splined hubs are the reference diameter
for the gears to run on ,so if you were to make the internal splines in the
gear blanks this diameter needs to be concentric with the gear teeth.
I faced a similar problem when i made some of the gears for the 127 gear
metric /imperial conversion , i made a fabricated spline as seen here in
the photo the inner part is milled and the hub can be used as a gauge ,an
outer ring is fitted over and loctited in place with a keeper in place
to hold the parts until the loctite sets ,then 6 m3 screws are drilled and
tapped into each spline segment before parting off ,the gear is pre-made.
Providing care is taken to get the parts sized properly and the inner ring
bored and turned at the same setting a perfectly good fitting splined gear
will result , a little tedious to do but probably easier than cutting an
internal spline .
The layout of the gearbox and the change wheels is a little odd compared
with most lathes ,i suspect that there are many more combinations of
pitches that are not listed, with the permutations of gears that
increment 1 tooth at a time , i think that the 45 tooth gear is the largest
that can fit on the machine without fouling the mounting studs but 18
tooth is just possible and still fitting on the splined hub , if you had
all the numbers from 18 to 45 and that could be fitted that would be
a lot extra pitches i expect some would be of no use, but just using
a pocket calculator and juggling the positions of some gears can see
pitch increments of less than 0.002 ".
It looks a tidy machine that you have there ,i think you will be well
pleased with it.
John
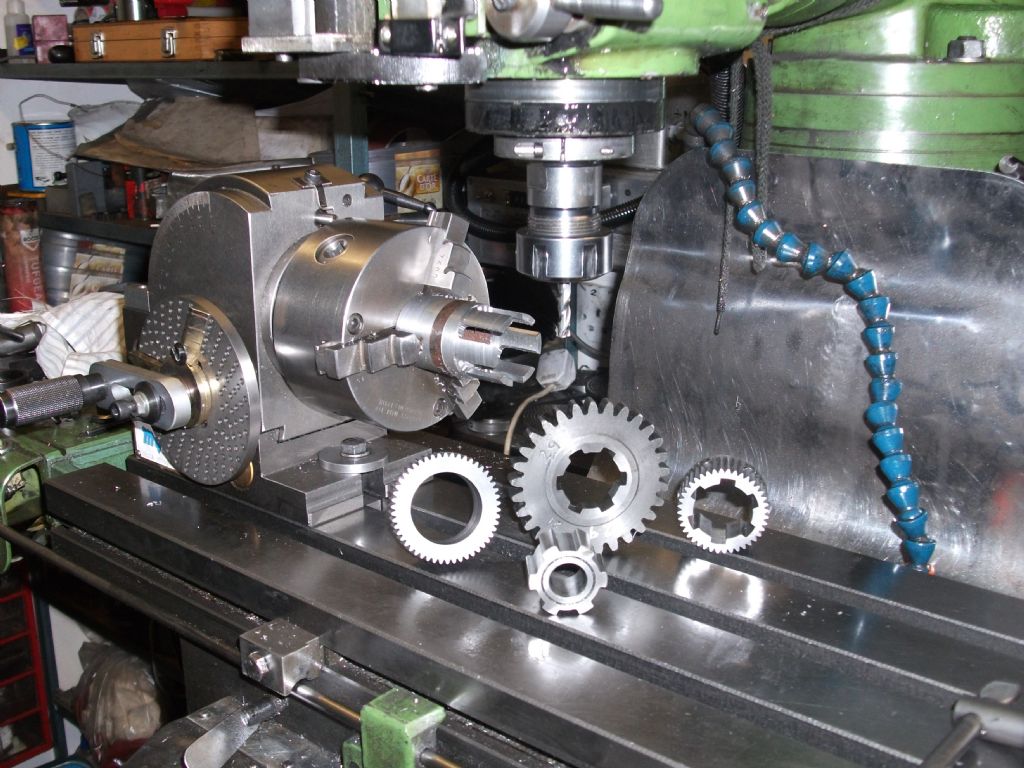
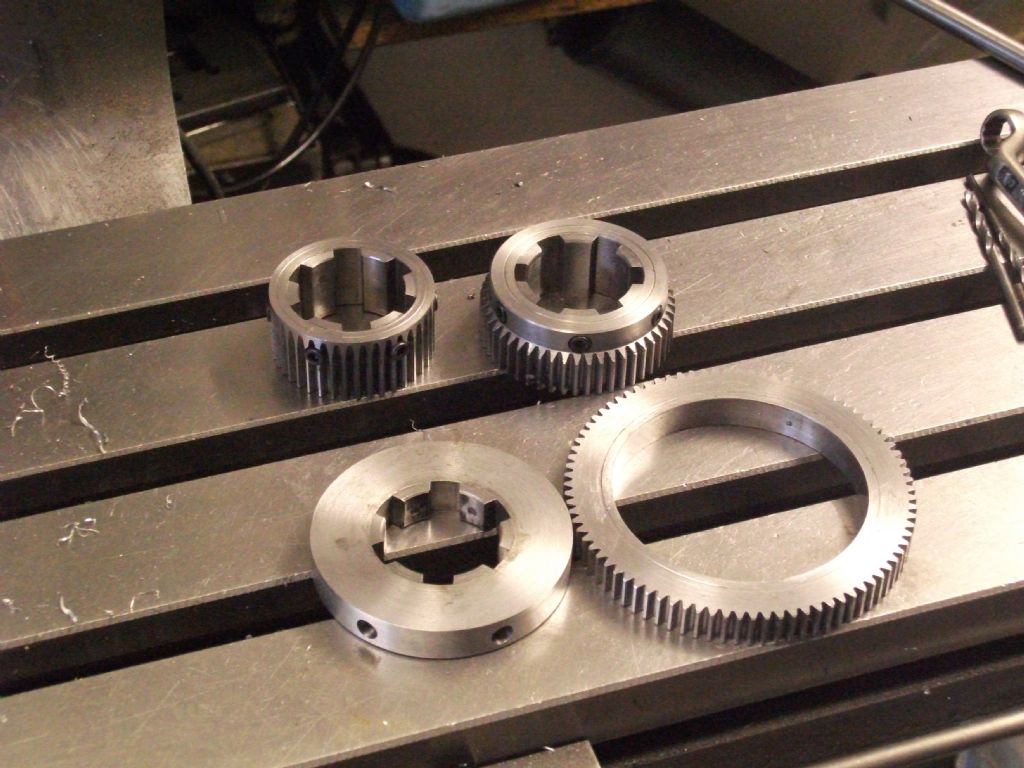
|
05/07/2021 11:58:33 |
As far as the change wheels go your best bet would be to inquire at Warco or Chester,i would
be surprised if they had these as a stock item in their stores these machines are not that
common especially from Warco ,they only sold these machines for a couple of years.I had
a problem with a pair of the head stock gears around about 2009 and they had to order some
gears from China back then ,if you look through handbook you have at page 4 of 29 you
will probably see the notes that i made on the page.
The change wheels are 2.5 module at 20 deg PA and it is unlikely that you will find another
machine that uses these sizes at only 10mm wide.
The real problem if you have to make them is if the Chester variant of this machine is the
same as the Warco is the Six spline hub used for the mounting , see the photo in the
last post i made on the 26/06/2021 10:40:54 .
The machine has not got a Norton gearbox ,the feed change gearbox has 9 speeds ,the
diagram here shows the output for 1 revolution input as you may see in position 3 and III
is 3.5 revolutions output.
The calculation using the change wheels , outputs the size in mm = pitch for 1 revolution
of the chuck.
From your posting...
"I got the change wheels off, and I've got a 26, 27, 28, 30, and a 36, so I'll need to acquire the
rest at some point. Again, not a major issue. Odd thing is that doesn't seem to be a listed
combination for anything on the front panel charts!"
If you look at the 3rd panel down on the change wheel chart 8 columns along mm per rev
you will see the listing 2,4,8 and above A36 B27 D28 E30 ,these are the only screw cutting
pitches that you can do with the change wheels that you have.
You can not change to imperial thread cutting as Howard suggests by fitting a 127 tooth and
complementary gear ,on this machine it just will not work at the lead screw end of the
gearbox when changing the drive from the feed screw shaft to the lead screw ,the change
in position engages a 45 tooth to 21 tooth gear which ruins any calculation.The machine
however with the full change wheel set can do a fair number of imperial pitches with
a very small error on a 10 tpi pitch the error on 10 inches of thread is
only 0.00027 inches.
An article written by me was in MEW 257 to obtain a true metric to imperial conversion
and required 4 gears the results were limited to 10 and 8 tpi the only sizes that i
really needed.
The photo here shows the gears.
Some other articles on this machine have appeared in MEW :
Cnc conversion MEW 207 to 212
Large fixed steady and boring bar MEW 207 to 208
Milling attachment for milling lead screws /worms MEW 241 to 243.
John
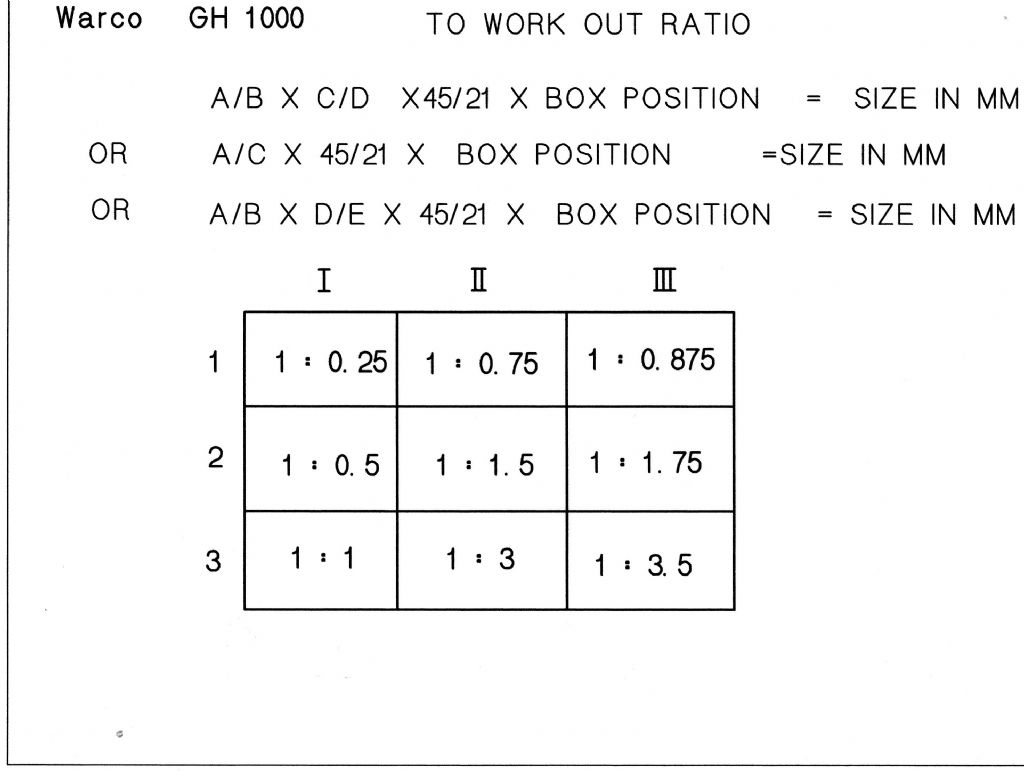
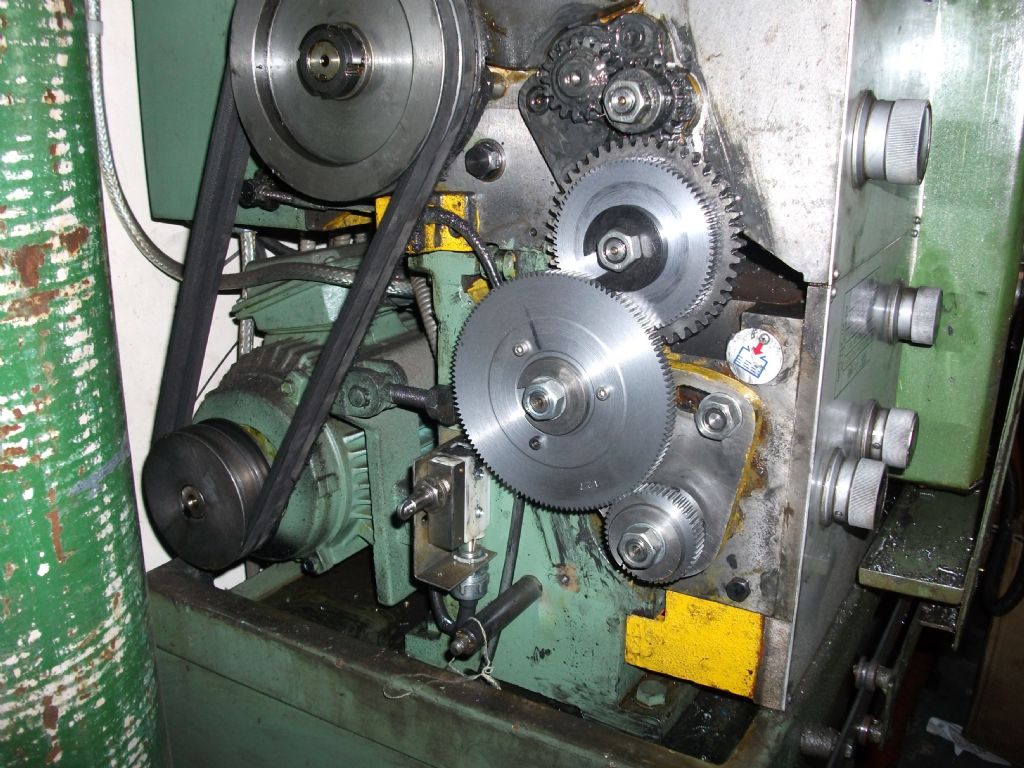
|
Thread: Super7 Power Cross Feed Problem |
04/07/2021 21:44:20 |
Hi Robert,
It is quite possible for them to lap even with a brass or bronze type nut ,yellow label Timesaver abrasive is used just for this ,quite useful stuff and does not embed and can be used on whitemetal bearings.
Hope that Myford will be able to help you ,let us know how you get on.
John
|
04/07/2021 19:41:55 |
Hi Robert ,
On seeing this i had sort of come to same conclusion,
"For what it's worth, i think there is a lack of concentricity with the screw, the nut or bore in the saddle?"
When you look at the product on the Myford page they claim to lap the nut and the screw together
so they are a pair, there would not have to be much of a mis-alignment in these parts to give a
problem if that is so.
The bore in the end of the nut should be concentric with the outer diameter of the body
of the nut that fits within the apron similarly the threads should be the same these are the only
parts left to look for the problem and this only seems to occur when you push the nut right
home.
I don't think you have anywhere left to look.
When you refit the the screw and the bracket as their advice is to leave the screws
loose for the bracket to settle into position and then tighten the screws, you could just
try to bias the bracket up a little and tighten the screws and also try the same down
and to each side in turn to see if there is any difference.
Clutching at straws here but worth a try to see at any difference in any of these positions.
John
|
30/06/2021 11:10:22 |
Hi Robert ,
Seeing your posting it seems the problem is with the lead screw and or nut.
The depth of the slot in the lead screw only needs to be deep enough as in the
sketch "A" ,i can't remember how much clearance there is in the inner bore
of the gear bush and lead screw the last time that i had mine apart was in
2005 when i converted the machine to part cnc.
If you fit the gear /bush on to the lead screw and look endwise with the
lead screw pushed hard towards the the key the screw should be able to
touch the inner wall of the bush and just still have a gap between the bottom
of the slot and the top of the key as in "A" , if you have a situation as in
the sketch "B" where the slot is not deep enough in the lead screw then the
screw would be forced off centre ,as you have said and i would agree there
may be a problem with the axial alignment between the bush bore and the
thread in the nut if that is so with a situation as in "B" and that would probably
result in cyclical binding.
Just have a look at this to see if it is the cause.
John
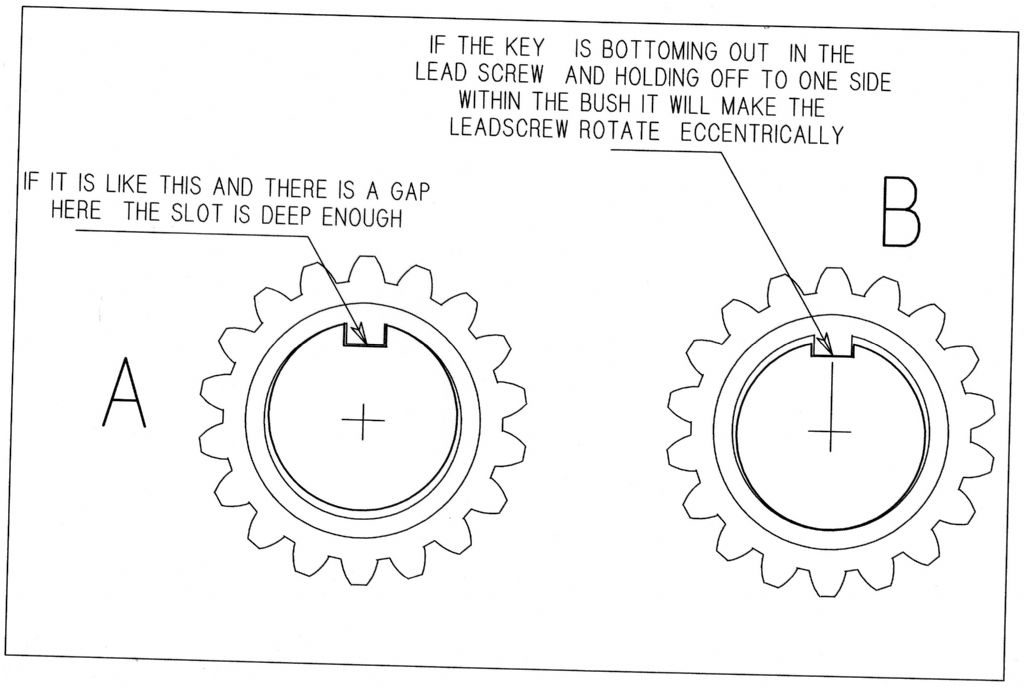
|
Thread: Dressing / Truing a resin diamond wheel |
29/06/2021 10:01:51 |
Try these
https://www.youtube.com/watch?v=W5W1_96lOuM
https://www.arceurotrade.co.uk/projects/d_wheels/dwdoc2.html
Or Google dressing resin diamond wheels plenty of options
John
|
Thread: Re-making a centre hole in a small crackshaft |
28/06/2021 09:45:41 |
Posted by Nigel Graham 2 27/06/2021 22:13:47
Incidentally you learn something new every day here! I have never previously heard of a "spring dog" yet lo and bohld, there is one, on the drawing of the lathe set-up. As the "words and music" bear out, it holds the work back onto the live centre, since the outer end is not constrained axially.
Hi Nigel,
The illustration there is from a re-print of a book that is nearly 100 years old ,back then folk really new how to do things.
I have not used this for turning operations but have for grinding,here in the photo this worm shaft is hardened ,the open end has a small chamfer which is a centre ,the OD 's are ground between centres
the fixed steady is placed in position and the pads adjusted.Two driving dogs are fitted one for the driving the other has 2 coil springs to provide the tension to hold against the head stock centre,
the tail stock is removed to allow the internal wheel to finish grind the bore.The springs have about 15 to 20 lb tension which would be enough even for turning operations, obviously some care would be needed on long slender work to prevent the springs pulling and bending the work.
I suppose for that crankshaft job the fixed steady pads could be profiled with an end mill or reamer fitted in the chuck to provide a better contact around the area of the slot on the end of the shaft.
Setting up would involve no more than holding the job on the headstock centre and gripping the
shaft end in the drill chuck in the tail stock and the bringing the fixed steady pads to support the shaft.
Providing the centre was turned with a small boring tool the slight misalignment if any would be no worse
than turning a tapered shaft with an offset tailstock.
John
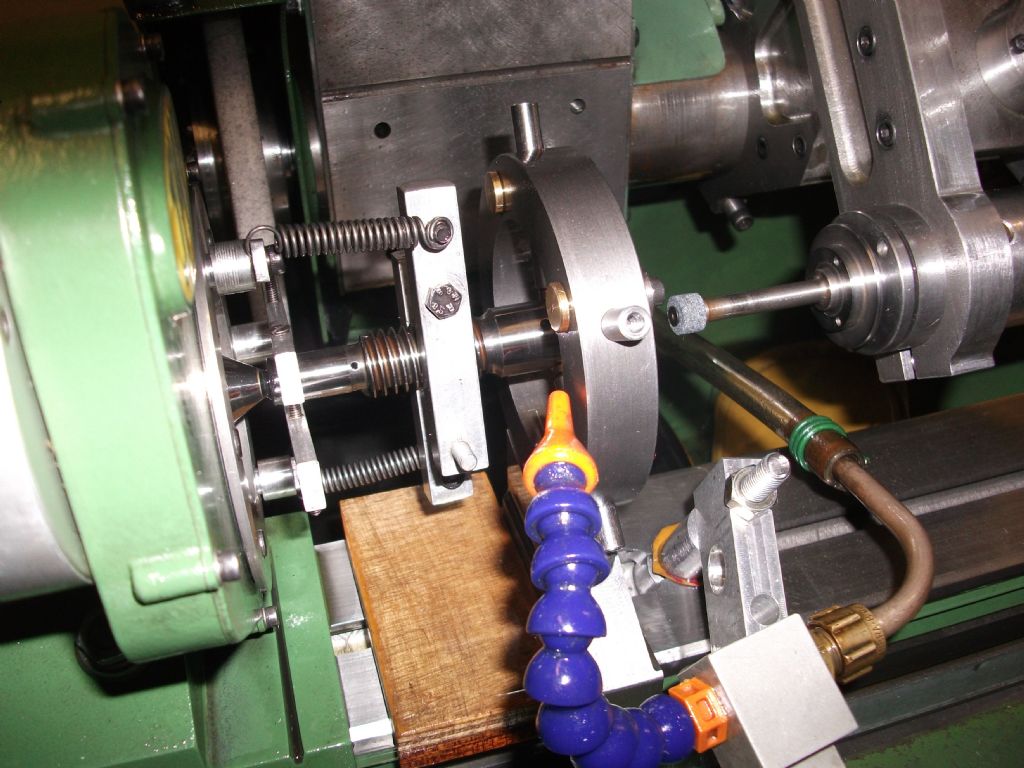
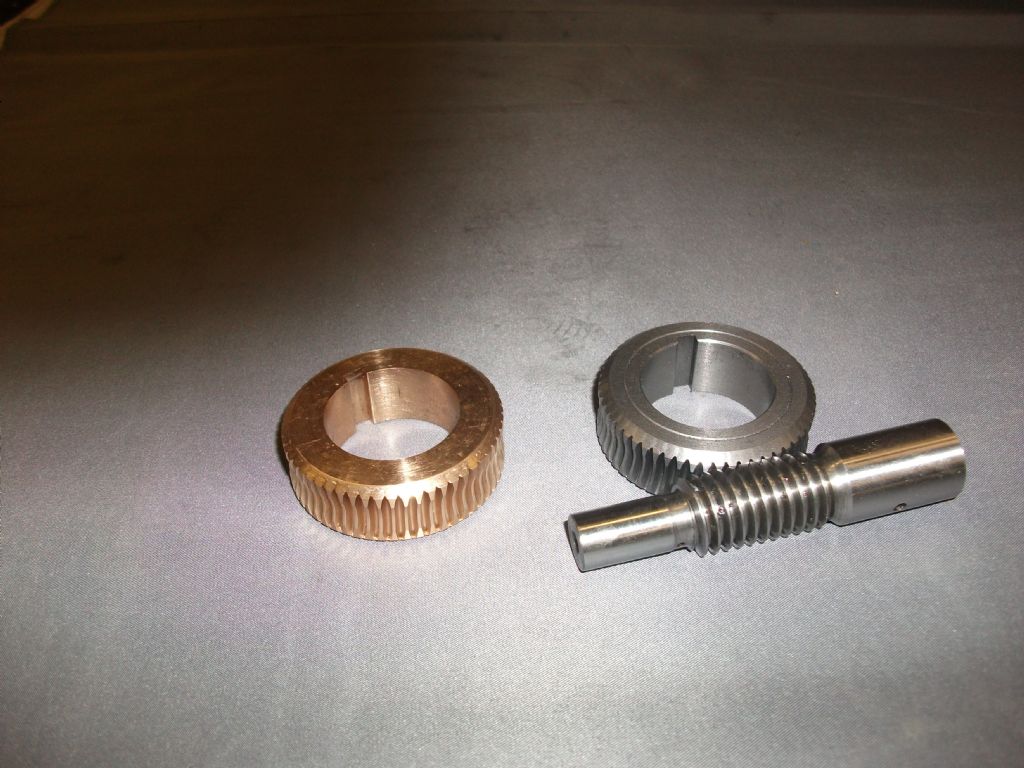
|
27/06/2021 14:31:00 |
On the assumption that you have a lathe with a large enough swing you could try this ,using a spring dog as in the photo below to hold the good end in a headstock centre and a fixed steady to support the unworn good end directly or with a bush would be and easy job the drill and then machine a new centre with a small boring tool set over in the topslide.
John

|
Thread: Lead Screw cover/infringements Chinese Lathe |
27/06/2021 10:51:46 |
Hi,
When i got my Warco lathe with a similar D1 5 mount some clown probably during the final assembly whacked in a reference mark on the side of the spindle with a chisel ,this had raised a burr on the face of the flange which needed stoning off , similar markings were also present on the chuck mountings and faceplate etc . Worth checking for.
Some of these lathes have a short movement on the topslide ,the acme screw on mine was left with a long plain portion that reduced the travel ,if so it is a fairly simple matter to remove it and re-cut some extra thread to move the topslide further forward.
John
|
Thread: Install & commission of a Chester Cub 630 (Warco GH750) |
26/06/2021 10:40:54 |
Hi Calum,
You should have the changewheels listed here as a set in the second line
down ,there is unlikely to be a 26 tooth i think is is a printing error as there
no listing in the changewheel setup for a 26 gear .
There are some differences between the Warco machines and the Chester
supplied ones , i see the motor is mounted now in the lower plinth ,mine
sits on the back of the lathe bed , the Warco machines have some small
tool lockers in the front and rear plinths.
I guess the lathe itself will be very similar the changewheels have a six
spline hub as in the photo .the gear alongside is one of a set for a true
metric to imperial conversion and has a fabricated spline.
The key here is for the D1 5 socket ends the square is 11 mm and 13.5 mm
long the stem length is 130 mm ,unfortunately there are no markings to indicate
the closed positions of the cams as on some British machines and no detents
either to hold in the open position so you need to ensure the scribed lines
are in alignment before trying to remove the chuck.
They are clockwise to tighten i suppose you already know this ,it is just
possible that they may have been tightened up in the other direction they
will hold just not very well so just check as you will never get them off
if this is so.
John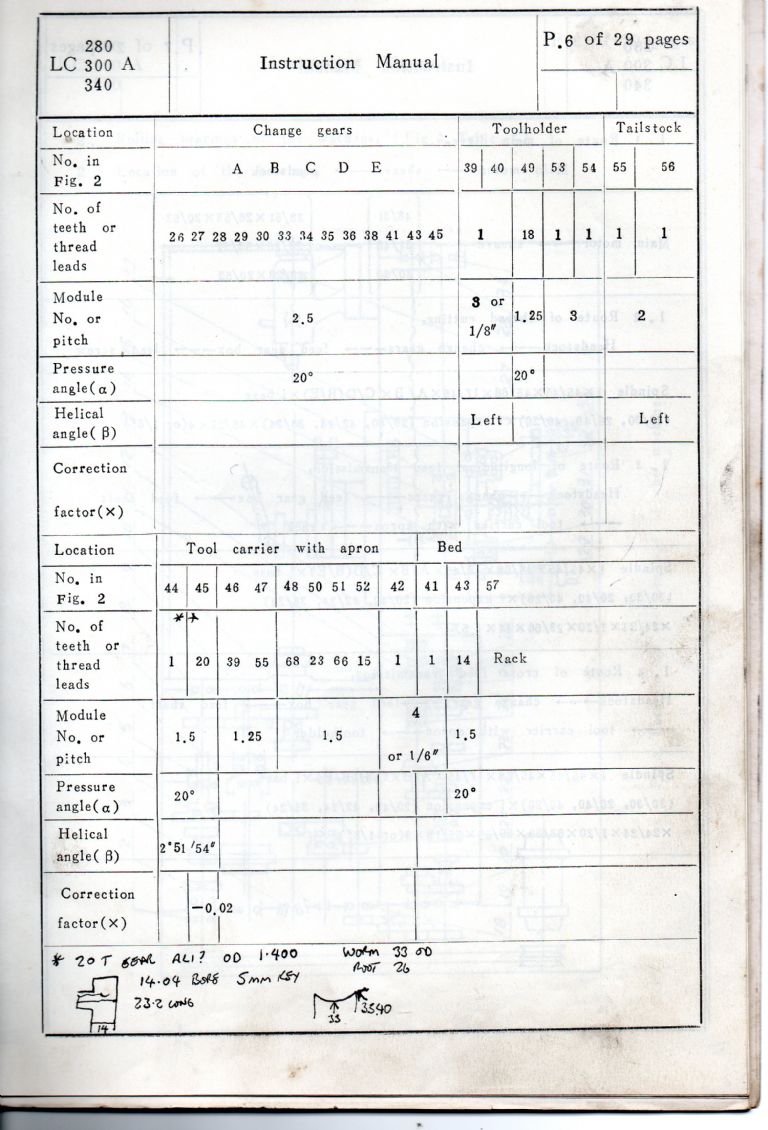
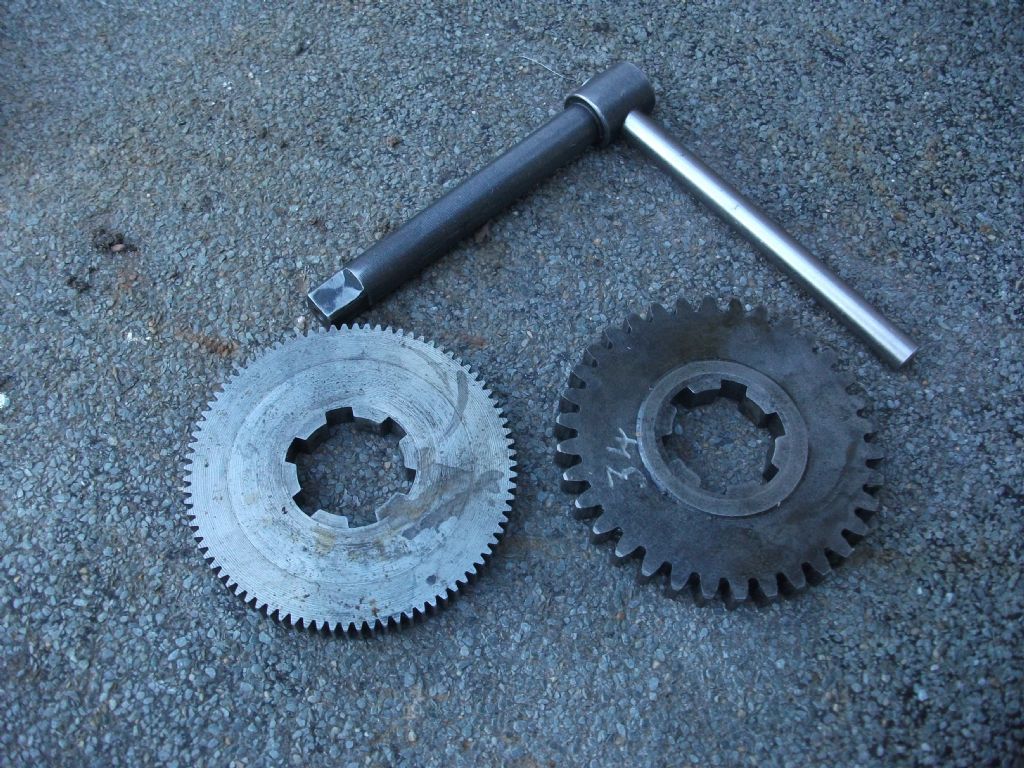
|