Thread: What did you do today? 2023 |
05/10/2023 07:25:01 |
As to recent infornmation and learning, I am going to make 1-a dual indicator tramming device for mill, I got the parts, some turning milling & drilling and small boring for a good fit, then see where it lands. 2-to try to fit a normal indicator onto a coaxial indicator to try to monitor what it is measuring, and see if the basic design of it is usable without the indicator fitted to it.
Edited By Chris Mate on 05/10/2023 07:25:54 |
Thread: Tramming your mill(/dril) head:A theoretical question-Idea came up |
04/10/2023 15:45:51 |
OK, I had determined that as everything is connected(Not to same point) I get 1 mark on screen movement for coaxial indicator(as in photos) and .03mm movement for a dial indicator pointed at the MT4 collet chuck position clamped to the vice rear. .....This was manupulating the Z2-Axis, by changing it from the Z1 axiss it rides on.
I accomplish the movement by adjusting the head bolts added to this mill for minimally aljusting the head, forcing the head down, as the head "lean back" slightly as was said. With this mill you can do this, I have however seen that newer models from same supplier this function was abcent, so your head stay as its bolted(3x bolts) to slide on column. I used this in the beginning after getting the mill and trammed it the usual ways.
There is no way I can manupilate the X-axis controllably(Hap hazard by tapping it) by bolt adjustment, unless I make up a sturdy 2x bolt contraption to accomplish this to my liking of doing it
Yes, I accept this mill is probably worse than a 1960 farm tractor in build, but having low standards help along, and assisting me in making things for myself its more valuable than I though after buying it, its just interesting getting deeper insight into things as I go along..
The fact that surface grinding technologie/machines exist, make me feel better.
Edited By Chris Mate on 04/10/2023 15:50:21 |
04/10/2023 06:13:25 |
Just to desribe my own understanding right or wrong as I see the Vertical(s) squared to the bed.
-The bed=X & Y axis.
-The rear fixed vertical with slide column=Lets say this is Z1 Axis.
-Lets say the Quil slide movement is called Z2 axis.
-Lest say the spindle movent with the quil is called Z2_1 axis, the spindle has no choice it can move with the quil or with the head crank up or down.
-Lets say the spindle turning arc is called Z3.
-The head and all in it can be cranked up or down in a fixed(Shimmed) vertical plane-Z1
-The quil can be cranked in or out at whatever angle the head is -Z2
-The spindle can go in or out of the head via quil- Z2
-The spindle can turn the arc is -Z3.
However the head Z1 is cranked up or down does nor represent the tramming to 90 degrees to bed of the spindle arc=Z3. If the head is at 45 derees, and the head is cranked up or down it will still move according to (shimmed) Z1 axis, however the spindle if quill is not moved will cut a round grove as the head is cranked up or down as a result in the work.
Only when the quil is cranked the spindle will cut at 45 degrees into the work wherever it is positioned(Z1) to the work.
If everything is square to the bed the spindle arc wil run a horizontal circle on the bed or on top of the work, and then its called trammed in square to the bed, it will then run a perfect horizontal circle in a perfect barrel inside.
Is this explained understanding basic of me correct-?
Edited By Chris Mate on 04/10/2023 06:24:42 |
03/10/2023 22:40:58 |
Max, I was thinking about a taper roller bearing, but it would cost a lot for a large one, I will see if I can get an old unsold for years/discontinued one from local farm shop.
Jason, here is added photo, I cut 3 rows right to left(X-Axis) and back over same cut, similar for other two.
-The cutter have 6 inserts and the cut was .65mm. See if you can make something from it.
-I can remove 5 inserts and cut again and see how that looks.
-I can recut same depth from the Y-Acces the same way.
-I cannot feel the rifs one see in photo, neither measure it with an .01 indicator.
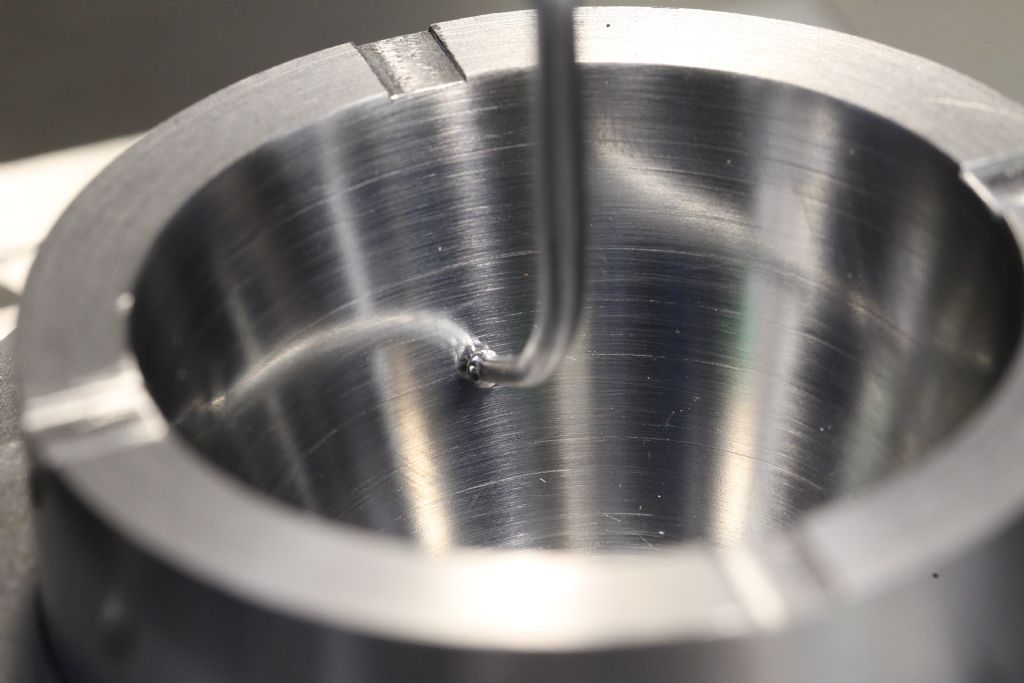
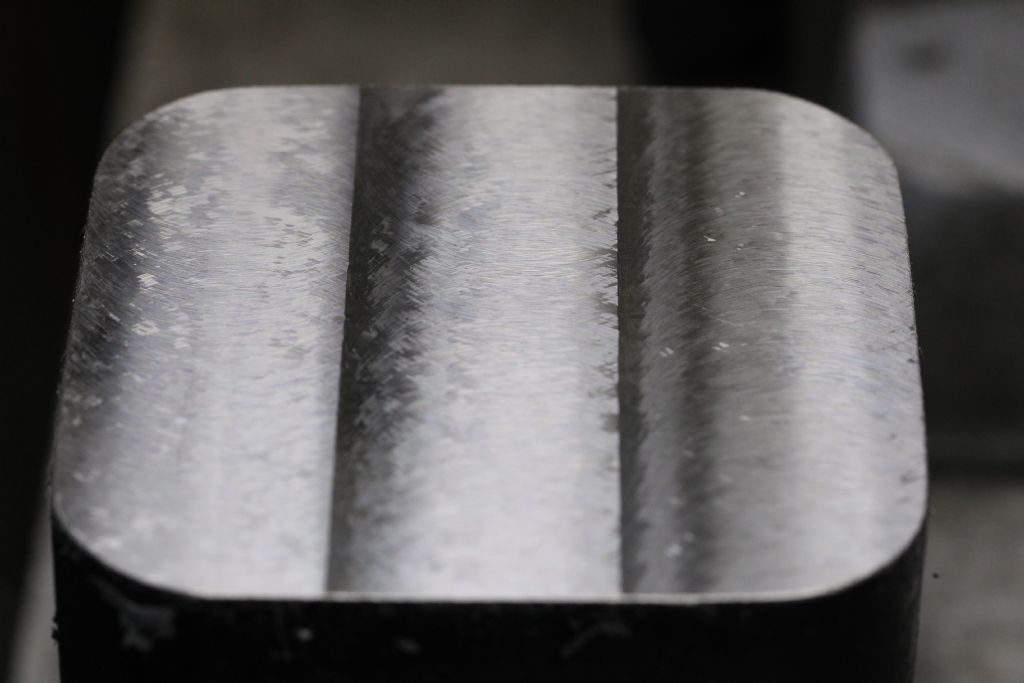
Edited By Chris Mate on 03/10/2023 22:45:52 |
03/10/2023 18:05:05 |
I re-indicate it with coaxial indicator today at the top with quil extended everything locked-Ok
I then moved quil up, and lowered head to bed, check indication and it was off X-axis.
I then installed vice, re-indicate it in vice and it was spot on all directions. I took a cut ar flat piece of steel with shouldermill with etal inserts. I can see the 3x cut lines like in CNC work, but could not feel or measure the lines with -.01mm dial indicator. I also had the level box at 90 degree on left side of head, and it did not change from 90 degrees the whole time, not 100% accurate, but at least it did not move withing its limits of 1 degree either side of 90. I am happy with the front and back cutting as it cut forward(Conventional) and backwards(Climb milling).
This crap mild steel block, so it was not a mirror finish like I get with aliminium on same cutter.
So my next step is to buy/make a short arm for attaching a dial test indicator in spindle to the taper as well and see if I can determine if the coaxial indicator is more sensitve in visible movement per line as the test dial indicator .01 will show. I can see if I wind the quil down, the tip of lever touching the taper seems to move half the distance as to one line on coaxial indicator to next line. Will have to see how that compares to the test dial indicator.
What I do like is dialing it in in X1/X2 & Y1/Y2 points is actually quick and easy after chosing a position on taper, and you get all directions in one go while the indicator stay facing you. So it looks like the verical area around the vice jaws are ok till/if proven wrong by dial test indicator
.
|
02/10/2023 20:56:44 |
Thanks for all the info and opinions, I appreciate it, and chewing through it.
If proper mills has issues this thing can only be worse.
So in short its safe to say if you want to tram the mill, its best to tram it in the vicinity to the vertical height you going to mill with as little quil stickout as possible. I always mill with no stickout of quil to start with, however I never trammed it specifically to the vicinity of the vertical height of operation.
Well, the stickout of the quil with head advanced to the top, I was thinking more leverage to pick up inaccuracy in tramming effort, and all of this giving me more perspective over the range of possibilities, and as I learn to know my mill, I will settle somewhere with knowledge thats best to use, understanding where its coming from.
Just for fun I will tram it this way with the head on top, quil most advanced and everything locked, then lower it right down with quil retracted and head as near bottom as possible, and not the variation, I am sure it may not be pretty....I know understand why the precission grinding machines were invented.
As soon as I am happy with the method of tramming, and actually moving the head by fractions controlabl(I will have to make something to accomplish this so it not bumping), I want to experiment with the cut quality finish of a good quality facemill, to see how slightly on/off tramming effects it under some load of cutting(not as much as a heavy proper mill) X/Y choice of movement/locked, and back over the work, versus all around conventional milling around the work...etc.
|
01/10/2023 13:15:57 |
30mm x 90cm aliminium bar bolted to head to make it easier to move, tap with fist.
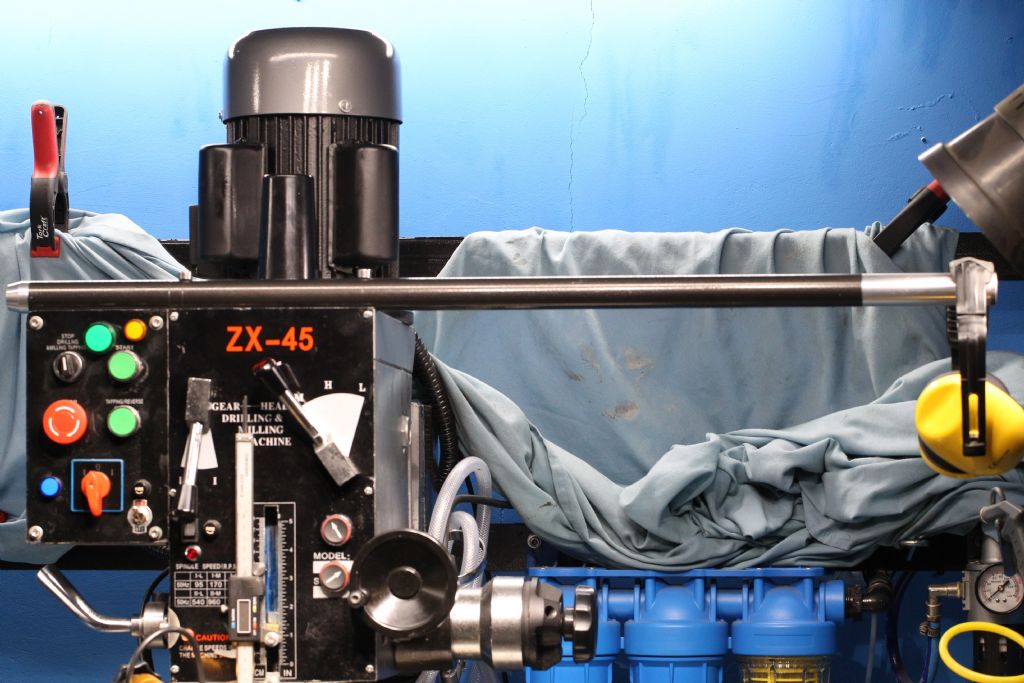
|
01/10/2023 12:23:32 |
Hi Neabb, I did bolted a long thick aliminium bar to the top of my mill head to assist in moving the head, and it does help a lot making it easier, the leaverage is such I can bump it wih my fist, however I see in future I will make something "fexable" to adjust it accurately with two opposing bolts, like I do with vice and zeroing the X-Axis swivel function, no bumping.
Here are two photos added:
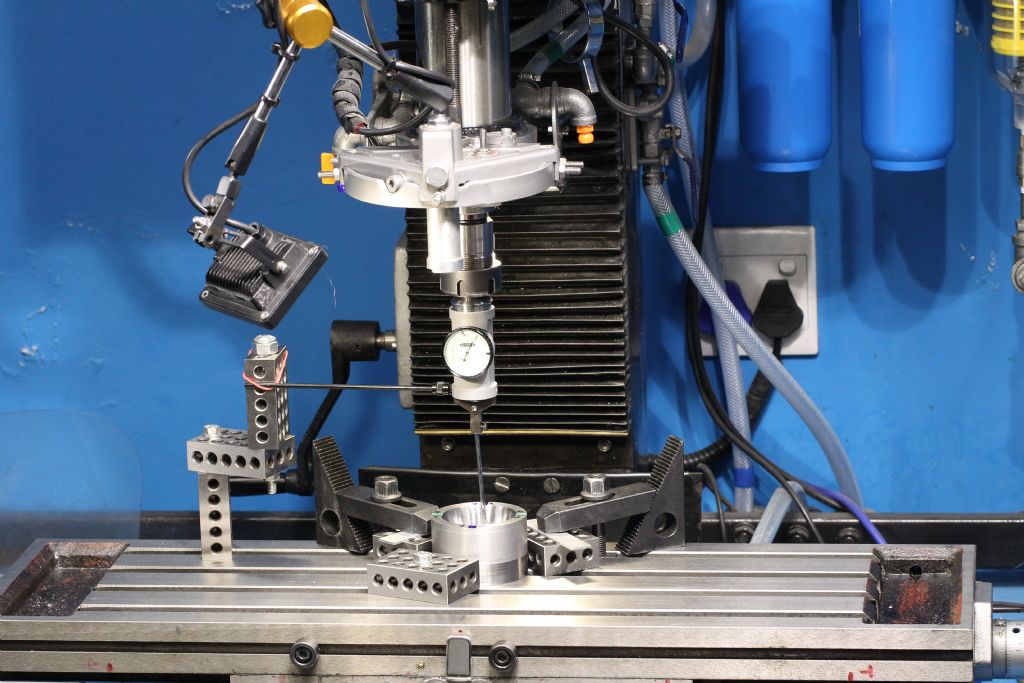
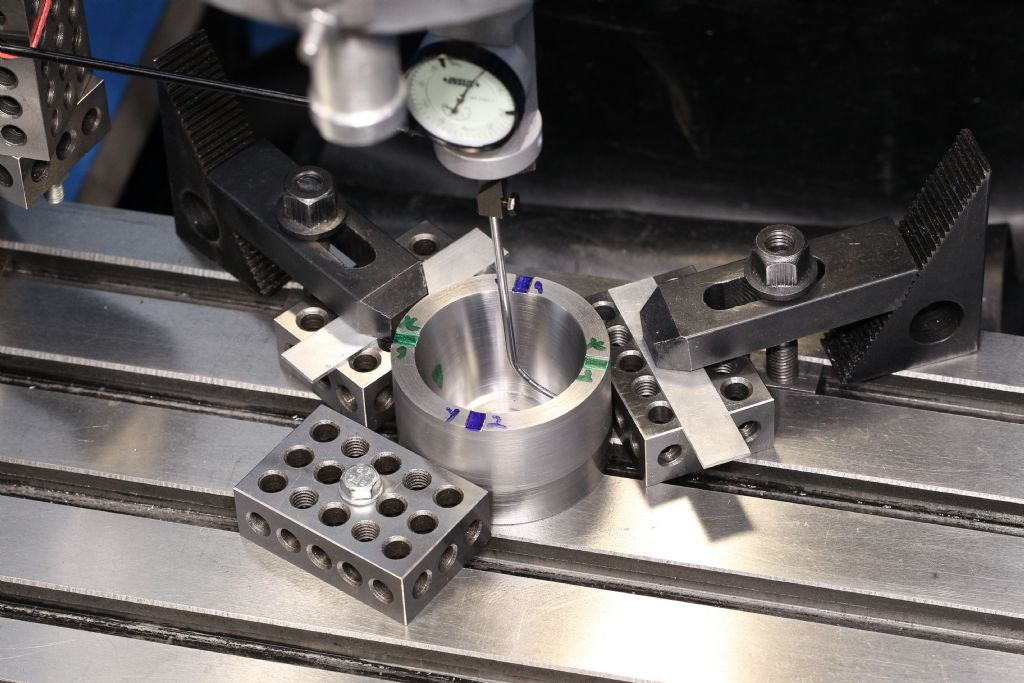
Edited By Chris Mate on 01/10/2023 12:24:52 |
30/09/2023 17:39:03 |
Ok, thanks for info. This morning I decided to make the "jig" clamped to mill table. Decided to cut the inside to 18 degrees due to height of round block. At the bottom I left material, then drill a small hole which is concentric to the taper. This hole was drilled with the smallest centre drill with short taper for the punch bit from the coaxial indicator.
I then installed it to the centre of the mill bed. I played for two hours with it. I think I like it for now, must still prove if it has the practical value I want from it, and that is to have something simple enough to tram the head so I can get a smooth cut backwards and forwards in all directions by slight adjustments, and with this I monitor all 360 degree in one sweep, I like this.
1-So I 1st centred the spindle with Coaxcial Indicator installed in 10mm collet/MT4.
...I ligned up the punch bit from indicator so it ran true as possible, this is now at the bottom of "jig" right on bed. I know that depensding on head this may not be 100% yet, but a start.
2-I then fit a longer bit to coaxial indicator and chose a spot around the middle of the taper height.
....Now from here I marked the Y-Axis(Short one) as Y1 and and Y2 on opposite side.
....I then marked the X-axis on "jig" as X1(Left) and X2(Right). So now I have 4 points to concentrate on to make adjustments moving the Bed a bit.
3-I got the Y-Axis which was shimmed by factory and it has "tention" like bolts on top for a slight adjustment which I used after I got the mill. Not all mills has this feature.
...Off the batt I could see I dont have a problem aligning it to the Y-Axis.
...I could also see I have a probem with the X-Axis get it to alighn, I could not initially. I then loosed the 3 head bolts slightly, place the degree box on the quil extented, head adjusted to the top of travel.
......Only after I adjusted the head slightly, the quil now show 90 degree to bed(This of cource is not 100% accurate , but at least an idication),.Only now I could get the coaxial indicator set 100% by adjusting the X-axis more thabn the Y-axis(Very slighty) by moving the bed under the spindle.
....What surprises me the most is that the coaxial indicator stay on zero through the 360 degrees around the taper, with bit of oil on tip. This as a surprise.
At the moment I like the fact that I can monitor 360 degrees turn with one indicator in one sweep around.
I am pretty sure the head is now 90 degrees as close as I can get it, tighning of 3x bolts included.
Note: Using the coaxial indicator with a boring head, I never thought of the importance of the head to be 100% 90 degrees to bed to get it set up well. At least I learned something from this around the whole plot of using a boring head.
I will take a photo tomorrow to illustrate the setup. Everybody may not like it, but if it allows me to adjust the head slightly to give me a good cut backwards and forwads over the work under load(Not boring head use but normal milling), thats where I am heading, hoping if I have to adjust it slightly off, it will not cut an oval hole with the boring head when that is used, or if it workd for normal milling head slightly off to one side, it may have to be corrected if boring head is used..
I have a good quality shoulder mill with 6 inserts from Walter to proof it for normal milling.
Edited By Chris Mate on 30/09/2023 17:44:10 |
29/09/2023 03:03:09 |
For those that know all sort of geometries well, I would like to hear your opinion regarding this idea.
I am aware of the current methods used to tram heads with up to two indicators used, and I can do that, but I like how the coaxial indicator works and dont work, really jnteresting.
From that my theory is:
1-You take a block of round bar say 70mm wide by 60 mm in height, put it in lathe and machine the outside diameters, for this case the outside does not matter much.
2-Now you bore it out except you left a bottom of say 5mm not bored out, with a wall thickness of say 15mm. Do not remove from chuck now till finished.
3-Now you drill a very small hole in the bottom centre without removing it from lathe chuck, this is to centre this piece under the spindle using the coaxial indicator with its punch adaptor, this would be like a flat plane start.
4-Now you turn a steep taper of say 15 degrees into this hollowed out bar to near the bottom with concentric hole. The use of the taper would be to "multiply" the effect of it head is out of tram similar to the lenght of bar used with conventional methods for leverage. The taper will give the leverage now, as the coaxcial probe will not run in a perfect circle around the taper if your head is not 100% 90 degrees vertical(Spindle to bed).
5-You can see this as a jig made once to use with the coaxcial indicator to square up the head/spindle to bed(Tram).
I dont want to compare this with the other methods, just opinions in theory regarding this idea. I do see some sort of a simplicity in it. What do you think of the idea in theory-?
|
Thread: 'Cutting Edge Engineering' attempts to repair a large casting |
25/09/2023 00:25:39 |
Primary:Factory
This was an interesting one, looking at the failures//cracks before he attempted to repair, my thoughts were poor quality casting by factory, maybe a batch like that, and the torgue spec applied to all those bolts and over time heat & cold cycles it cracked like that. Maybe get that cast iron tested and compared to another similar part not cracked.
2ndary:Repair attempt
After I saw how a cracked head was repaired in a 4th world country, where they heated up the complete head in a coal fire, wild job, I think he's heat was not enough for the complete casting doing such a repair, only then one would know if its actually repairable.
|
Thread: What did you do today? 2023 |
21/09/2023 22:51:48 |
Some time ago I bought a "Precission" 90 degree square, very well made on the face of it. The other day I want to use it on the mill, I dicovered its loose, can't believe it was a pressfit glued(Was used before, maybe solvents effected the glue). So today was my 2nd attemp to clamp it between 1-2-3 blocks properly like a jig at 90 degrees and properly clamped. I switched the blade around and redrilled 6mm holes to fit two hollow pins, then glue those innersides with strong cement rawbolt glue. So I will know tomorrow if this attemp was successfull testing it with the line drawmethod using the same square.
Edited By Chris Mate on 21/09/2023 22:53:46 |
Thread: DROs etc |
21/09/2023 22:43:17 |
Still no DRO...
Steve I am in similar situation than you, this is totally different than I did before, however I grew up fixing my own stuff as far as I can. I watch youtube videos for 3 years to get the feel of if it, how they talk about the operations, tools used etc. before I bought a lathe 1st, then a mill. I now like the mill more and more as I use it, and wonder why I did not buy this with my 1st house/garage already. I still dont have a DRO, the one I saw 1st hand and like is still too expensive at stage as I buy the tools I feel I need 1st and that will continue for some time.....I usually learn something from each video, although some creators are hard to continue watching. Forums you get more to the point info asking about something specific. With an open mind you can learn a lot by yourself from others, pick and chose and experience. I learned that patience and a plan is a good thing.
|
Thread: Milling Advice |
20/09/2023 16:35:13 |
So far till further experiments I got the best milling finish with a Walter 6x insert shoulder mill with the head roughtly tilting 2 degrees left accidently. I then mill conventional milling using the X-Axis from right far to left, then I go back without adjusting the Y-axis on same pathe instead of going horizontally...I then adjust the Y-Axis on, and repeat.
It seemed to smooth out the cut on the backwards milling on same track.
Recently I went and adjust the head 0-Degrees in relation to bed, however this was a digital level meterbox, so not accurate enough.
I was thinking of getting one of those Zero setters to follow one insert placement in 180 degrees on bed, which will reflect the adjustment from actual cutter insert perspective and adjust head accordingly, not sure which method will relate to best results.
|
Thread: Hosepipe delemas-Plastic Fittings kick out |
12/09/2023 01:36:47 |
Wife bought good quality hosepipe & fittings etc recently. Yesterday she got hosed again after fitting slipped out. I tried everything I could think of before, but they failed all.
I went into garage and was looking for something else to try like an O-Ring, but then saw a selution staring me in the face....Its called a Copper Tube Sleeve(Just google the picture), use with copperpipe connections screwed on, not the soldering types.
Now the sleeve approximate the size will not fit, but you cut it through, then slip it over the hosepipe, ignore the 1-2mm gap now in sleeve. Now fit the pipe in connector at Tap or End of pipe, slip this sleeve over and in, now screw on the plastic nut which now will positively clamp the fitting.
The idea felt good trying to wiggle the pipe at fitting and even with high pressure did not kick out.
You may try it if you have such problems.
|
Thread: Diamond Inserts |
04/09/2023 05:39:25 |
I got 4 of them, given by another machinist, but have no toolholde for it. He told me I can dress my grinder wheel with it, so I milled and glued one of them into an Aliminium handle I made, and sure as hell I can dress the grinder wheel no problem. In the mean time I got a kennametal book with info on toolholders, but had not got to it to make a toolholder for them with correct geometry. Would be interesting to see how they cut metal.
|
Thread: Drill press vice jaws |
02/09/2023 06:39:14 |
I have two of those similar vices, jaws are springy hard, then I got one "free" with the mill similar but with V-groves with this one in operation the worse of the lot. At least if I drill through them it won't hurt my feelings, I hardly use them anymore, sometimes to hold pieces I am painting. I also has a smaller one, half the size for small drillpress use, and this one is better seeing everything is shorter.
|
Thread: How irritating |
31/08/2023 13:18:57 |
I bought a Vertex 50mm-MT4 and had a choice of any arbour I want, Straight, R8 or any morse taper.
I clamped a 6mm Iscar small boring bar(It has squared sides) in its 12mm hole, adjust it's centre using the boring bar insert tip as a guide 1st outside then inside the hole with mill switched off, turn spindlec with hand, and to my surprise it bored just fine, no problems with quil going up or down, light cuts.
|
Thread: 12 or 16mm tools |
30/08/2023 06:14:33 |
12mm:
I use 12mm (330 swing lathe 160mmm chuck) most of the time, however the 10mm set I got has better inserts and sometimes on aluminium I use these. I also have 16mm HSS tools which I sometimes use.
I got some tuff doublesided inserts from somebody and made a 12mm toolholder for it as well as modified a less used 12mm toolholder for it. These inserts required a 9 degree modification to cut properly, but they last.
I found the inserts that cost a packet the same as one quality insert, does not last well, and I probably won't buy them again once depleted..
|
Thread: Insize Coacial Indicator used in Vertex Boring head |
30/08/2023 05:59:53 |
I was trying to illustrate that the offset movement of the Coaxcial Indicator when fitted to the boring head as oppose to a collet does not effect its working due to how it works and dependant surfaces, which I found interesting, and in my opinion its still moving around an arc from the spindle centre, similarly as if you not having a coaxcial indicator and using a boring bar/ insert tip to centre the thing either in a bore or around another circular feature visible after the bore was woreout and out of round and you want to bore it out but keep the original geometry of the mesching of the gears making a sleeve. So in this case a Coaxcial indicater would not be usefull, a case like I might be facing if my plan-A in restoring a bansaw & gearbox does not work, so basicly I am just thinking about all of this in all directions and thanks for all other opinions. So its just a theoretical thing, not to say you must do it this way.
Edited By Chris Mate on 30/08/2023 06:02:29 |