Thread: NEW CONTACT EMAIL FOR MEW EDITOR |
26/04/2022 11:08:06 |
Posted by Luker 26/04/2022 06:54:46
I really do feel for the editors of these magazines, it’s an unforgiving job juggling
everyone’s ‘wants’ while walking the financial tightrope!
I think authors that are innovative, can do their own designs and still string words
together coherently are very rare. Then of course they need to have the time to
do all the drawings etc. for very little money. I wonder how many pages
(in a magazine) can be filled with articles from this dying breed of writers! I
personally enjoy reading the ME magazine; it has a nice balance of
journalistic articles and technical articles.
--------------------------------------------------------------------------------------------------
When Neil became editor his 2 page future outlook for the magazine
was real killer , for your statement " I think authors that are innovative, can do
their own designs and still string words together coherently are very rare"
I scrapped a complete machine build article that i was writing to send to
MEW because of this ,many of the authors of these type of articles jumped
ship to ME they mostly seem to have vanished by now.
The shopping list approach to article submission just stifles imagination,
many of the subjects within this posting here
https://www.model-engineer.co.uk/forums/postings.asp?th=179124
would most probably exceed his own set page limits or be so short
to be of little use .
----------------------------
What happened to David Clark's posting of 25/04/2022 22:12:26:
was it taken down by Putin's press office.
-------------------------------------------------
I know how difficult it can be to write a long construction article,to get the
sequencing for machining operations do all the drawings etc ,unfortunately
magazines don't seem to be interested in publishing these any more .
ME almost seemed interested in this
https://www.model-engineer.co.uk/forums/postings.asp?th=87736
but seemed to spend a lot of time working out how publish it but not
in the magazine ,8 years later its still at the bottom of the heap,if they
haven't lost it again.
Is it any wonder that authors would not bother to write such things
and just leave it to the Drawbar and tool holder brigade.
Just as an aside getting back to when David Clark became editor
and put the page rate to £50 the cover price for the magazine
MEW Was £3.75 the last issue i had when i cancelled my subscription
at 302 was £5.75 if the page rate had changed in the same proportion
within this period it would now be £70.
John
|
25/04/2022 21:08:13 |
Posted by Brian Wood 25/04/2022 15:39:37
I can now answer my own question. Mortons pay £45 per article page, MTM uses to pay £50.
-----------------------------------------------------------------
If you look up the Guidelines for both MEW and ME they naturally have not been
updated to reflect the new ownership ,ME payments are listed as £30 To £50
per page and MEW are £40 to £ 50 per page.
I seem to remember that when David Clark took over as editor and saved this
magazine he immediately put the page rate from £35 up to £50
per page.
Looks as if it has been going backwards ever since he was replaced
as editor.
Considering it was around February 2007 when he started as editor and the page
rate looks be going down 15 years later ,who's the parent company P&O ?.
John
|
Thread: Home made furnace |
16/04/2022 21:48:41 |
Hi,
Further to the posting earlier i found this
it seems that this company folded for the reasons
shown in the link here.
https://www.asbestos.com/companies/m-h-detrick-company/
This appears to be an American company ,there may of course
be no connection with the company here that is still is in business
making refractory products but seems as if they have only been registered
with CH since 2008 which was long after the article that was published
in ME about the furnace linings , seem to remember that was before 1994.
This is their new address
+44 (0)1695 589540
M H Detrick Company Limited
14 Gorsey Place
East Gillibrands
Skelmersdale
Lancashire UK WN8 9UP
[email protected]
John
|
16/04/2022 16:05:25 |
Posted by Dougie Swan 16/04/2022 15:46:03
Hi
Somewhere back in the mists of time there was an article printed in the mag where
someone described making a furnace using ceramic as the insulation
I was a lightweight material, I got in contact with the makers of the insulation
and bought some for myself,
Now more than 20 years later I need to replace it.
Can anyone tell me the issue the article was in, I seem to recall the
insulation manufacturer was based around Cumbria but can't remember the
name. I'm hoping they still make the stuff
Any help would be appreciated
Thanks
Dougie
If this is the same company that i bought some insulating sheets
from the address that i still have is .
The material was Debac 1300 GA pads.
M H Detric co ltd
Priors Wood Place
East Pimbo
Skelmersdale
Lancashire
Wn8 9QB
I think they have long since gone i believe there was some
H and S problems and some legal claims and the company
folded as a result although there still seems to be a listing for them.
Give them a try.
Hope this is of some help.
John
Edited By John P on 16/04/2022 16:07:35 |
Thread: An ER32 MT5 collet holder |
16/04/2022 11:49:39 |
Hi Calum
Something that you should consider before committing to 5 MT tooling,
you need to check the the spindle taper runs true at both the top and bottom
of the taper ,the sleeve that was supplied with my machine runs out
in the 3mt part i think that there is a slight error also within the machine taper.
This only matters if you were to buy a ready made piece of 5MT tooling.
As you can see here from the photo the 5 mt sleeve is only 3.570" long.
As at some time in the future you have indicated that you will buy a milling
machine a useful option may be to buy a 3 MT ER collet chuck or an R8
and machine a sleeve to fit the lathe and then machine this in situ to suit the
the chuck not forgetting to engrave a mark on the spindle and sleeve and chuck
so they will line up in future.An ER 25 R8 chuck as seen here has a maximum
diameter 1.265" and the sleeve maximum diameter is 1.760".
John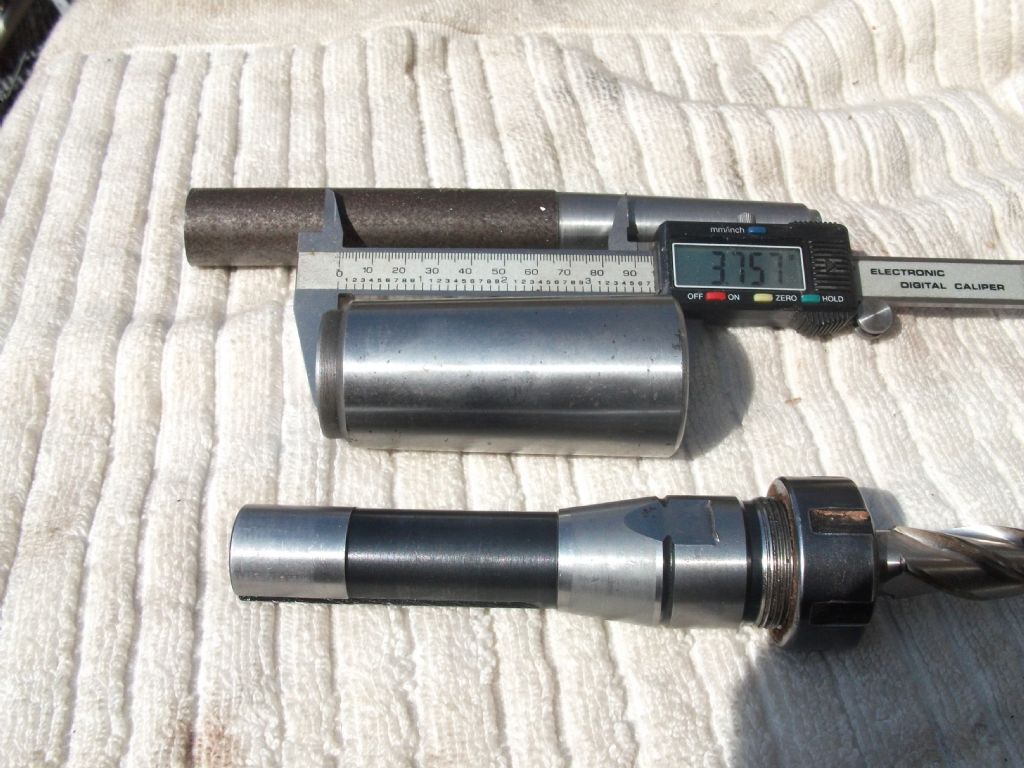
|
Thread: Gear hobbing |
15/04/2022 11:03:14 |
Posted by uli Schnelzer 15/04/2022 10:12:07
I remember several articles of Gear hobbing in ME and MEW. in one they use the
DP thread cutting feature of the machine to drive the hob. And then the building
of a complete one purpose hobber in MEW iirc from the numbers 245. At the
moment I try to make a similar project with my little Emco C5. I want a life
toolholder from a CNC lathe with a motor and an encoder. The measure
of the encoder will divide with an arduino or simpler an oldschool ttl-ic circuit
to the desired tooth number.
If I use an 500 cpr encoder so I get 2000 peeks/rev with the decoupled
spindelmotor. I want to drive the spindle with a 10/1 geared stepper motor,
so I get 2000 steps/rev of the hob. The divider give 1 peek out per tooth
of the gear. the feed of the machine can be made with the normal feed
of the machine from the spindle.
The biggest problem for me, is the electronic part. It were good, if I
can start with the index peek from spindle and hob encoder, so I can
go a bit deeper, if the geartooth isn't deep enough, but I haven't any
idea, how I can realise this.
----------------------------------------------------------
Hi,
This may be of interest was seen in MEW 193 ,this Syncron system as far
as i am aware is still available in Pcb form ,if you are interested
send a PM with your e mail address and i will try and find out if they
are still available.
John
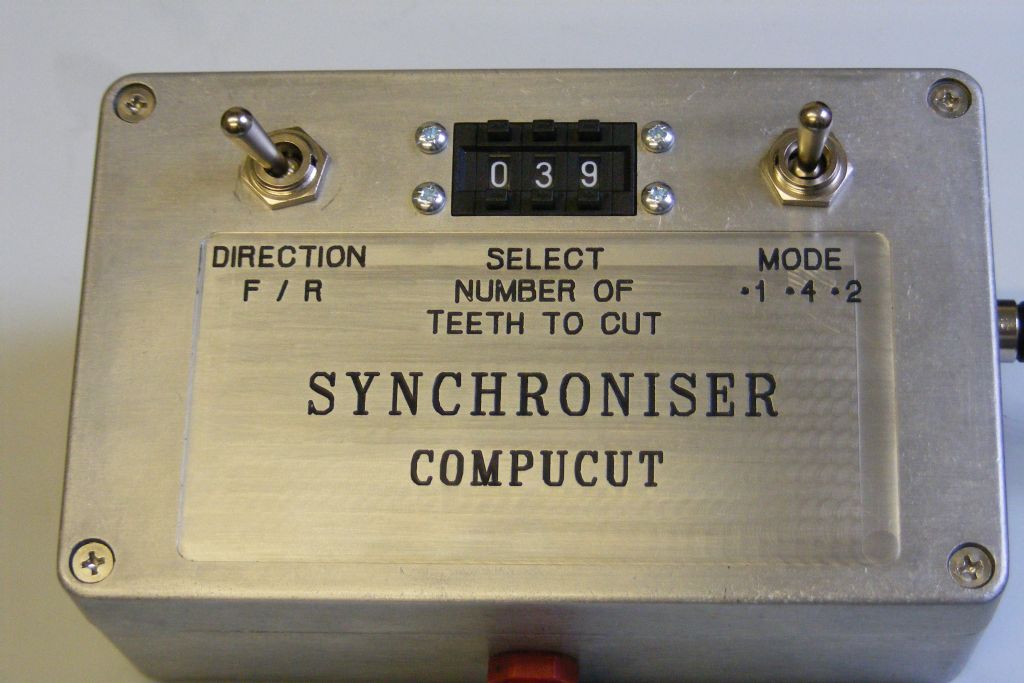
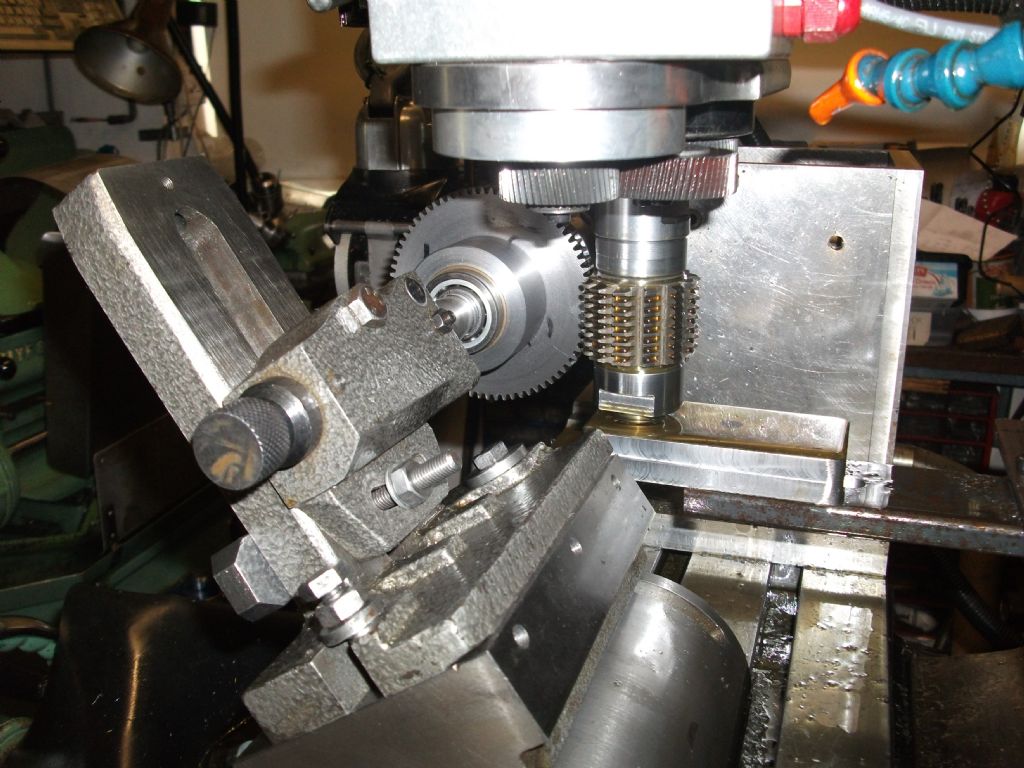
|
Thread: Making gears in the lathe |
11/04/2022 21:51:35 |
Posted by Bazyle 11/04/2022 19:02:00
If D is driving E you don't need the specific values - just something to give
you a 1:2 ratio. Since you have a 36 you could make an 18 to give you that with less
effort unless they are needed elsewhere.
-------------------------------------------------------
The problem with doing this is if you would wish to keep the original
splined hub ,the od of the splined hub on this machine is 34mm,
the OD of an 18 tooth gear would be 50mm and the the root diameter
is 38.5mm which means that there would be only 2.2mm from the bottom
of the tooth to the od of the spline.
The maximum that the gear could be profile shifted is about .9 then the
tip diameter becomes 54.5mm and the root diameter would be 43.1mm
and would be about 4.6 mm from the root of the tooth to the spline ,the
tooth height is about 5.5 mm.
This would almost certainly need to be a generated gear ,solving these
sort of problems are not always that easy.
You can see the sort of problems that this can cause here with this
gear to fit on this type of lathe at 1.0 mod and 40 tooth even when
it is cut oversize there is not much left below the tooth roots.
As when it is used the lathe spindle is revolving below 2 rpm
so it is transmitting little power and is safe to use.
John
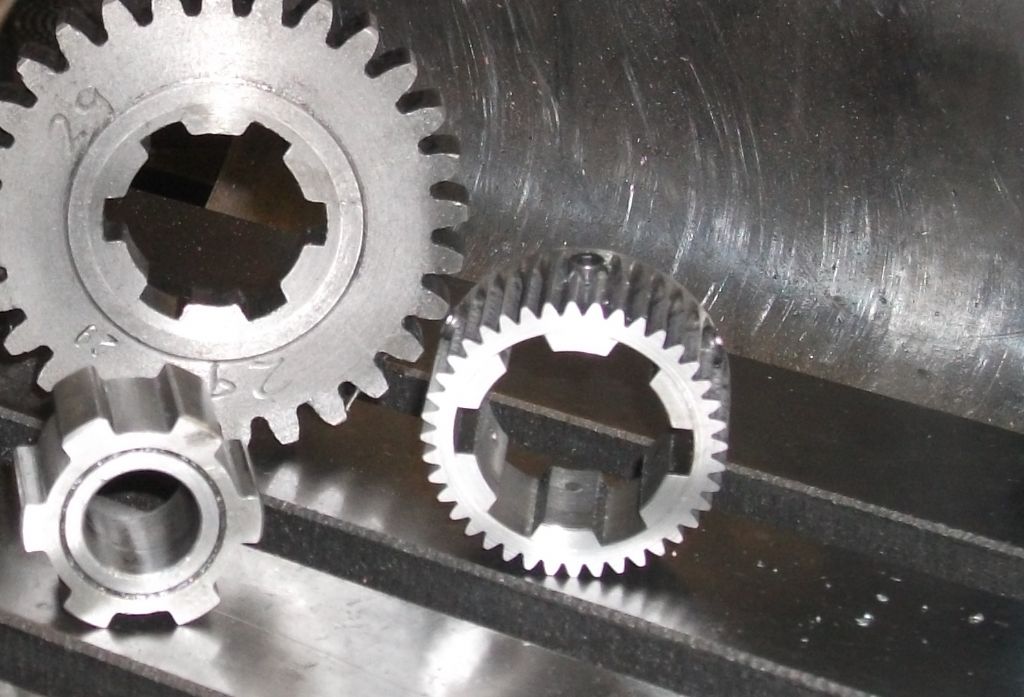
Edited By John P on 11/04/2022 21:53:17 |
11/04/2022 15:18:20 |
Hi Calum
Here is the change wheel list from the Warco GH1000
lathe ,i expect the internal gears will be the same but they
have replaced some of the changewheels.
The third list down has the same result as your listing
but the gears in the first rows are altered.
John
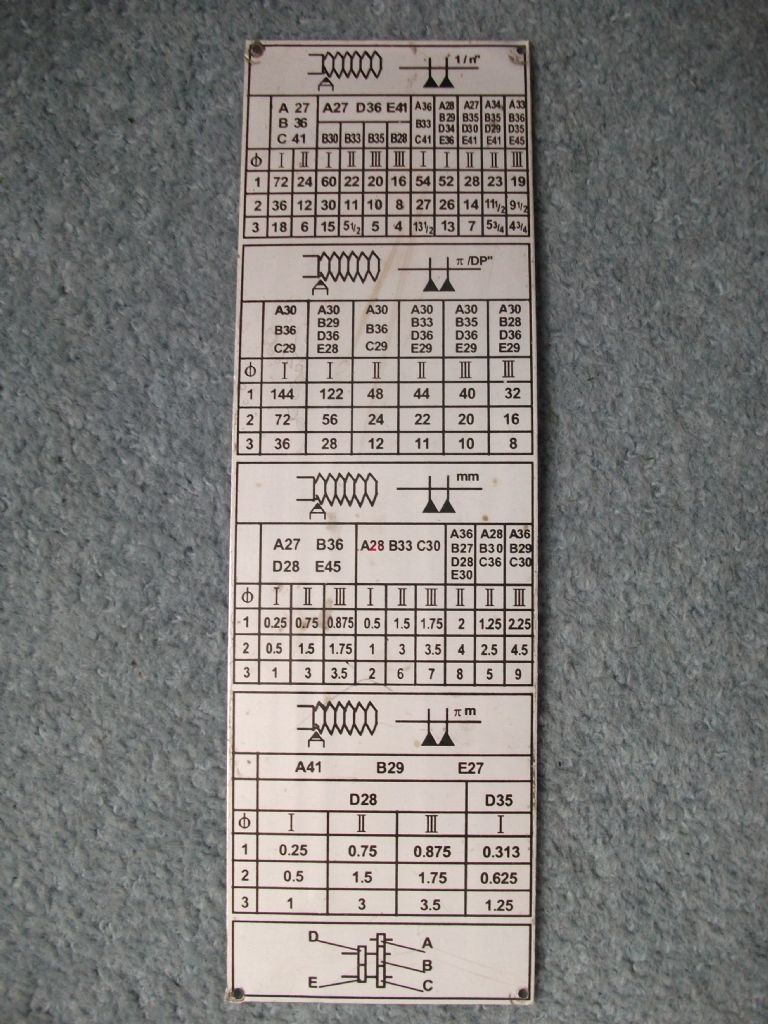
|
Thread: Install & commission of a Chester Cub 630 (Warco GH750) |
11/04/2022 13:26:32 |
Posted by John P 10/04/2022 22:49:12
When the auto feed clutch is in the other position (it is quite poorly drawn)
gear 48 drives gear 47 through gear 46 to gear 48 which is part of the
crosslide leadscrew.
------------------------------------------------------
This should have been,
When the auto feed clutch is in the other position (it is quite poorly drawn)
gear 48 drives gear 47 to gear 46 to gear 49 which is part of the
crosslide leadscrew.
49 is not listed as a gear but is the crosslide leadscrew at the top of
the page 6 of the manual and is part of item 40.
John
|
10/04/2022 22:49:12 |
Posted by Calum Galleitch 10/04/2022 17:22:06
I'd like to have a go at making gears to make up the missing changewheels that
I have - I think I'll do a separate thread about them as it may be of more general
interest but I'm just trying to understand the gear train of my lathe:
Beginning with the spindle, wheels 13,17,16,18, 19 and 20 have 45, 45, 45, 68, 17
and 45 teeth, so for one turn of the spindle A will be turned 45/68*17/45 times = 1/4
which is what John P wrote last year...so far so good!
Q. Where/how is the reverse in this diagram? Physically on the lathe it's somewhere
round the wheels labelled 17-18 but unless the reverse mechanism is not drawn
I don't see how it works.
In the quickchange box, 21/22/23 mesh with 29/30/31, giving ratios of
20/40, 40/20, 30/30 which corresponds with the 1/2/3 knob. Like wise the
second knob, 24/25/26 mesh with 32/33/34 giving 20/40, 42/24, 36/24 (1/2, 7/4,3/2).
Finally, if the leadscrew is selected the drive is fed through wheels 36 to 28,
which are 45/21.
Q. Am I right in thinking the manual states it is a 4mm pitch leadscrew?
Slightly alarmingly it gives "module no. or pitch" as '4 or 1/6" '. Now 4mm is
close to 1/6" but it's not that close!
Putting all this together, If I choose to cut a 4mm thread,
I take A,B,C,D=36,27,28,30 teeth from the front chart and
select 2,II (30/30, 36/24). One spindle revolution then gives:
1/4 * 36/27 * 28/30 * 30/30 * 36/24 * 45/21 = 1 turn of the
leadscrew, so if it is a 4mm leadscrew we've got a 4mm pitch. Phew.
When the feed is selected, the 45/21 drops out and the feed rod turns.
Q. What is happening at 44/45? Clearly this is where torque is being taken
off the feed. Then (assuming carriage feed engaged) 48 drives 46 which
drives the wheel engaging the rack? But what are 50/51/52 doing?
Similar for the cross-feed I assume 47 engages 48, in turn driving 49.
I'll add the manual pages for the gear list to my lathe album should anyone
feel inclined to try and make sense of it!
----------------------------------------------------------------------------------------
Hi Calum
The gear chart is depicted as a diagram and as such lacks the detail
needed,the reverse feed is the 16 and 17 cluster gear ,in reality
the gear 13 directly meshes with gear 18 ,i think the gear 18 slides along
a spline and sits in the gap between gear 16 and 17 for neutral
and connects to gear 13 via 17 and 16 to 18 to reverse the rotation.
It is some while since i have had the lid off so this is from memory.
Gear 44 is a worm that engages with the slot on the feedscrew that drives
wormwheel 45 and is the input drive to the apron.
The auto feed clutch dog either drives the apron along the bed through
gear 50 to 51 ,51 is connected to gear 43 which drives along the rack
57 under the bedway.
When the auto feed clutch is in the other position (it is quite poorly drawn)
gear 48 drives gear 47 through gear 46 to gear 48 which is part of the
crosslide leadscrew.
There may be some differences from the 750 machine that you have and the
GH 1000 i have as if you look at the photo's the handwheels are in different
positions ,this may not affect the operation but the gears may not be the same.
John
Edited By John P on 10/04/2022 22:50:03
Edited By John P on 10/04/2022 22:52:48 |
Thread: Mill lead screw thread size |
08/04/2022 18:24:38 |
Posted by kevin parr 08 04 2022 17:23 :13
Hello all ,Hope your keeping safe.
I have a chester 16 milling machine and i want to convert the x-axis to have a
stepper motor so it does all the hard work for me so how do i find out what
lead screw or ball screw to get i have taken the bed off to get at the lead
screw ( sorry if that the wrong name ) but there are no markings on it to
tell me what the pitch is so how do i find out this information
many thanks for your time.
kevin
From what you have written here you don't need to
replace the lead screw at all as it seems you only
want the stepper motor to provide a power drive.
As the machine it seems will still be used as a manual
machine a ball screw is more trouble than it is worth.
John
|
Thread: How to choose a high quality end mill cutter? |
29/03/2022 10:47:29 |
I buy end mills now from Ali******s as seen here in the photo,
the 4 mm are about £1 each and the 6 mm £2 each
delivered ,they are most probably the best cutters i have ever
bought .
At least one of the suppliers mentioned on this thread
had supplied me with cutters in the past that were blunt,
after an exchange of words with the proprietor he actually
admitted that he knew of the problem and came out with
the old excuse lots have others have had them and not
complained .I sent them back and was refunded i only wish
that i had sent back the supposedly ball end mills as well
as the were also rubbish.
These Ali******s mills are carbide TiAIN coated and most
on here would call them cheap cutters ,perhaps it would
be as well to remember that all of the cutters that you
buy over here are most probably also made in China.
John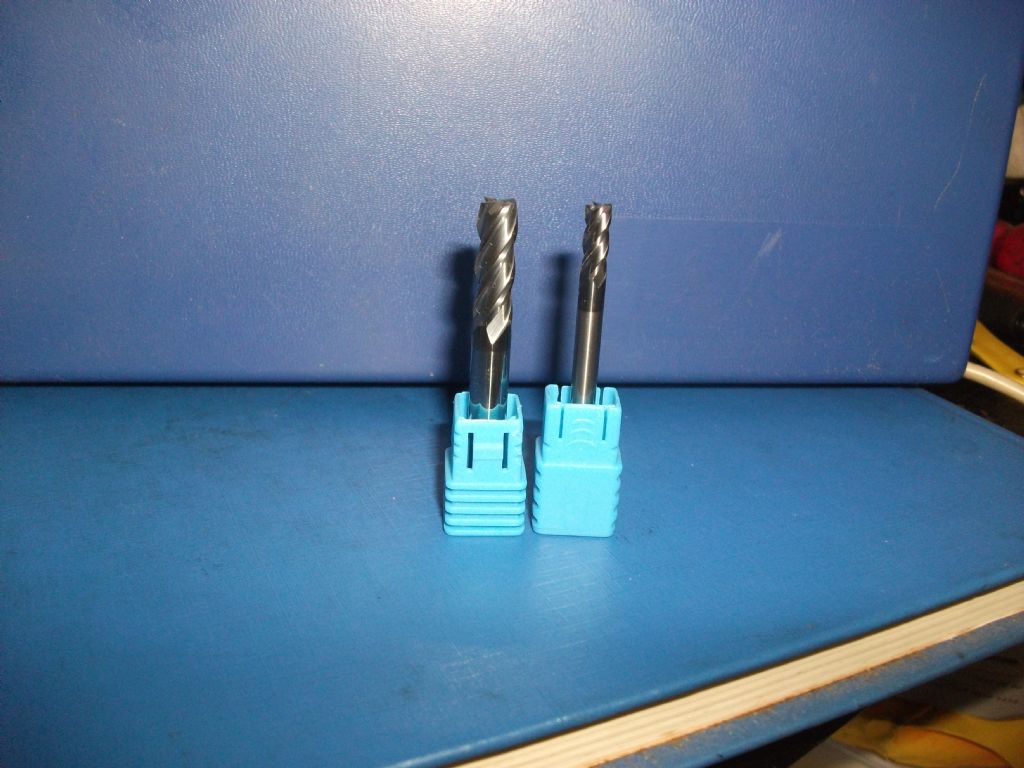
|
Thread: Bevel Gear Replacement for Astra L2/L4 Mill - any ideas? |
23/03/2022 14:30:27 |
If your friend has all the parts for this still to be a working
horizontal mill and a dividing head ,all you need is a copy of
Ivan Law's book Gears and gear cutting and make a set of
parallel depth bevels as replacements.
These gears here replaced a steel and nylon gear set that
had gone the same way as your set .In this sander the pinion
runs a 18000 rpm.
Providing that you harden them they will last a lifetime
John
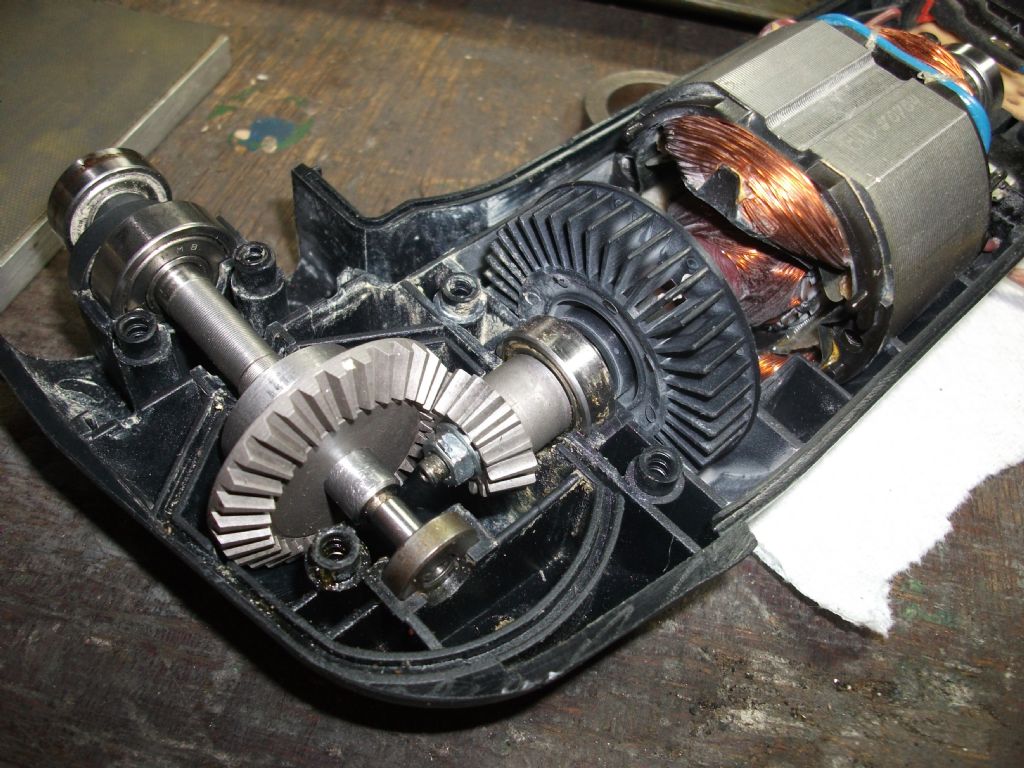
|
22/03/2022 12:02:00 |
Found this photo of the head drive gear on an Astra L2.
Is this the same setup as you have , is the nylon gear
fitted on the shaft of the vertical milling head.
Some other photo's of this machine here
https://www.stationroadsteam.com/astra-milling-machine-stock-code-2977/
John
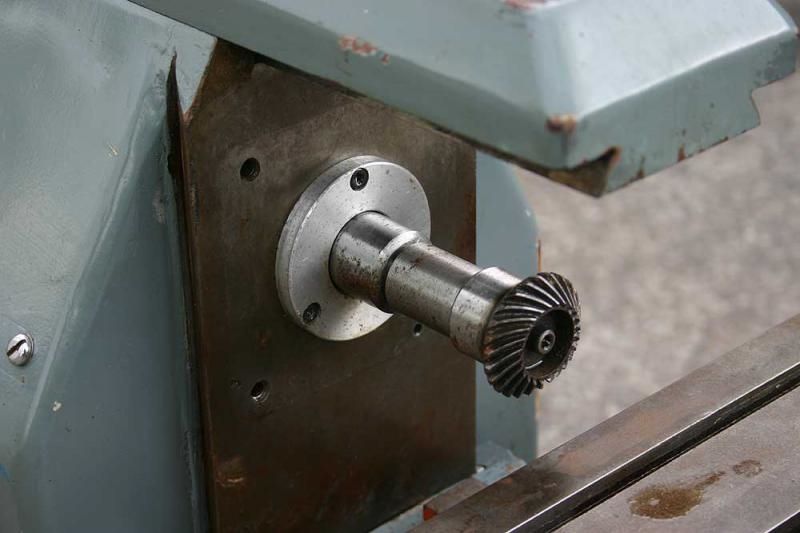
|
Thread: Engineering tuition recommendations |
19/03/2022 20:34:25 |
Posted by David-Clark 1 18/03/2022 08:46:06
Notable moment in Model Engineers’ Workshop, yhe CBC Tool and Cuter
Grinder, I think a world first.
So, self taught is good.
Hi David,
Sorry to hear of your past and present problems.
I am in the self taught camp as well.
It is now nearly 14 years since the Cnc cutter grinder article was published
in MEW ,i wonder if any others have been made ,there seem to be
plenty of similar setups working in the same way on You tube now, but back
then i don't know , most likely as you said " I think a world first".
I seem to remember there were some dissenting voices on this
when you published this same statement when you left as editor, naturally
there was no alternative methods proposed by these folk other than chop of
the end of a cutter with an angle grinder and spend nearly £1000
on an Arc euro grinder.
Here is the certificate and bronze medal that i was awarded thanks to you
for encouraging me to enter this machine in the 2012 Model engineer exhibition.
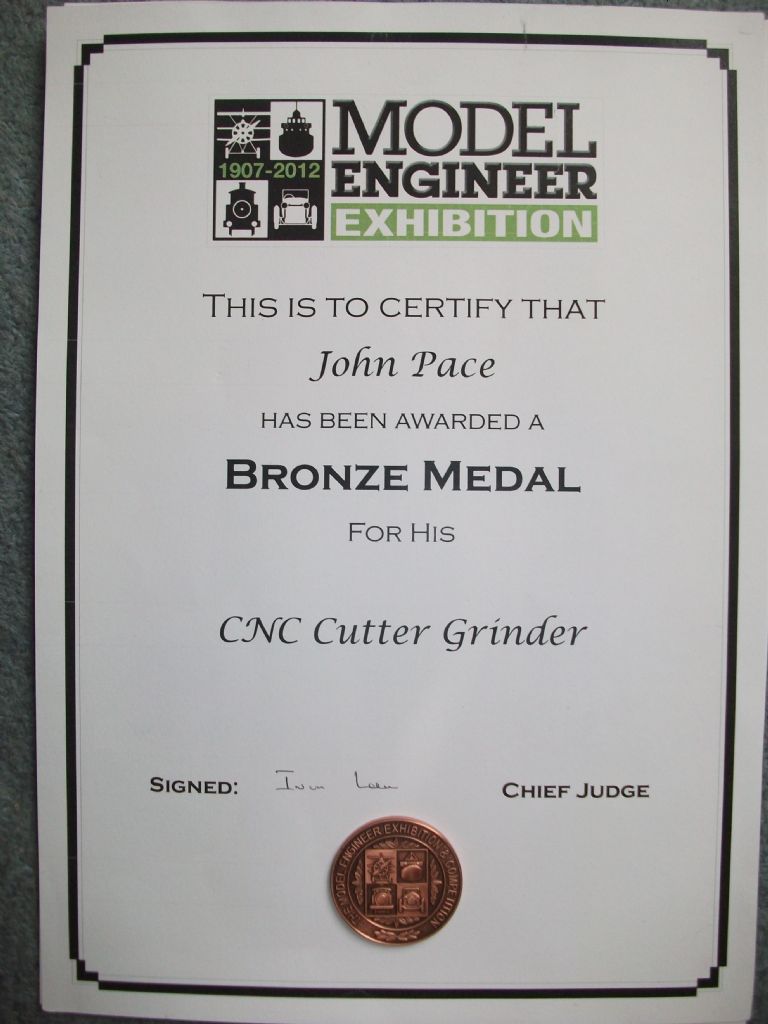
Sadly the magazine no longer seems to have had any proper machine
type builds since you left it is all short and repeated subjects,the
300 anniversary issue was i thought very poor the last straw for me
was the skeleton on a bicycle two issues later on was
enough for me to chuck in the subscription for this magazine that i had
for many years.
John
|
Thread: Help needed to lift bandsaw curse. |
16/03/2022 12:44:58 |
Posted by Bill Phinn 15/03/2022 22:27:12
Sadly, the bandsaw saga continues.
Earlier I was cutting a piece of 1" x "5/8" mild bright steel into T-nut sized chunks on
speed 1 on my Aldi Scheppach bandsaw. I was using a Tuffsaws Vario 14-18 blade
that has cut only about thirty pieces of steel and brass mostly smaller than the present
piece since it was fitted new around six months ago. I cut one chunk off without any
issues. I came to cut my second chunk off and the blade snapped instantaneously
as the blade contacted the work, even though I contacted the work ever so gently,
as I am always careful to do. The workpiece was very firmly clamped in the vice
and did not move. There are no broken teeth on the blade; the blade is
barely "broken in", in fact, and the teeth are virtually as sharp as they were
when the blade was first fitted.
Can any one suggest how this can be avoided in future? A lifespan as short
as this for a blade is clearly undesirable.
----------------------------------------------------------------------------
I suppose the obvious answer is buy from a better supplier.
The better option is to buy blade on a reel and make your own.I have not bought
a made blade in over 20 years .
An article written by me appeared in Mew 166 August 2010
and shows how to do this just by Mig welding.
The fixture here is a piece of copper bar ,the blade is clamped in
the slot with some mole grips and mig spot welded through 2nd photo.
They last long enough sometimes to resharpen but if they do break
as in your photo you can just re weld them.
John
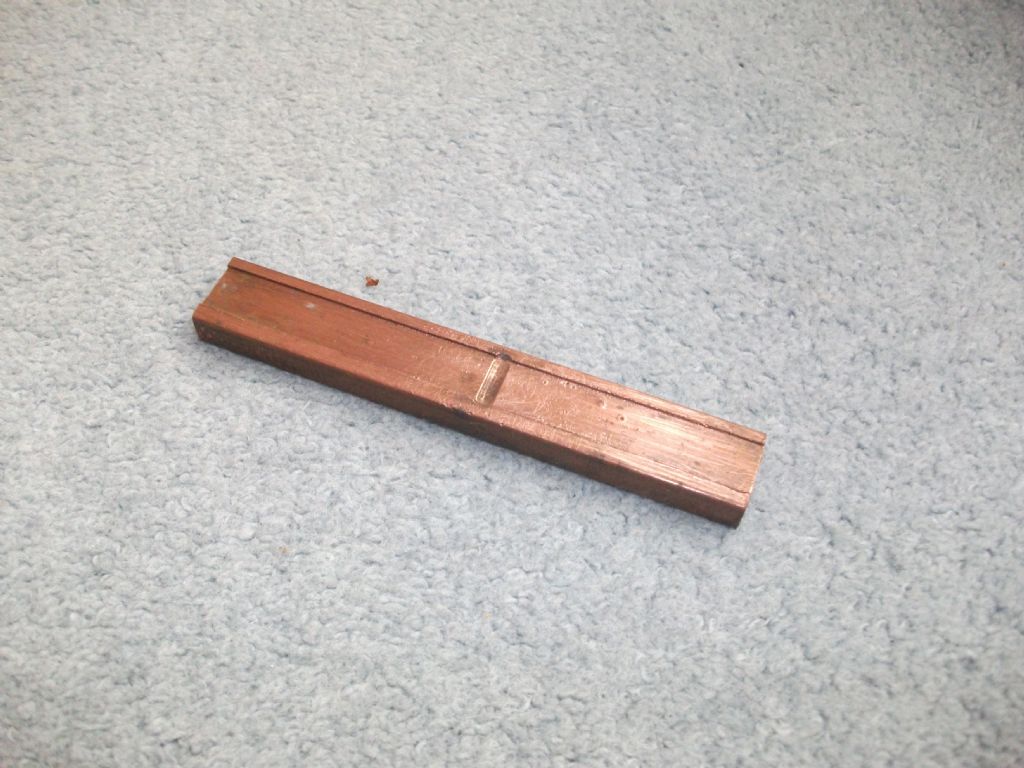
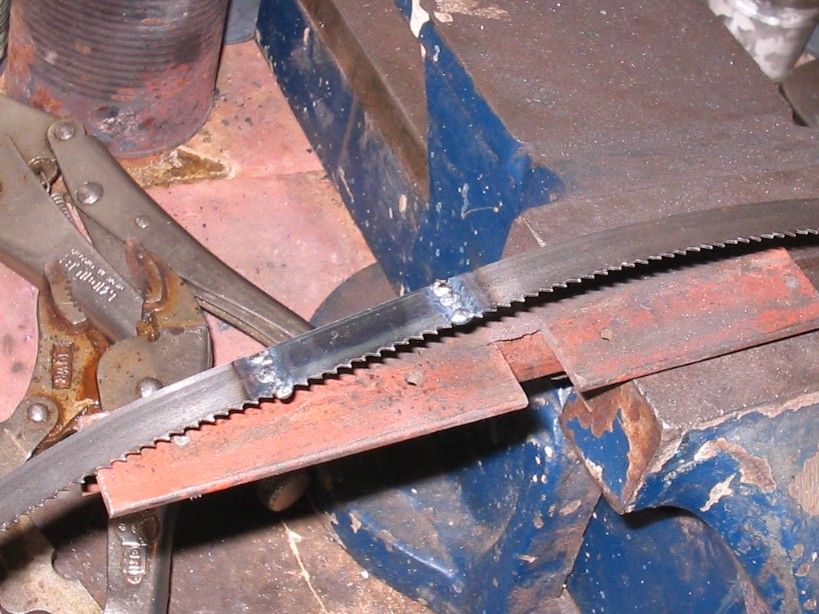
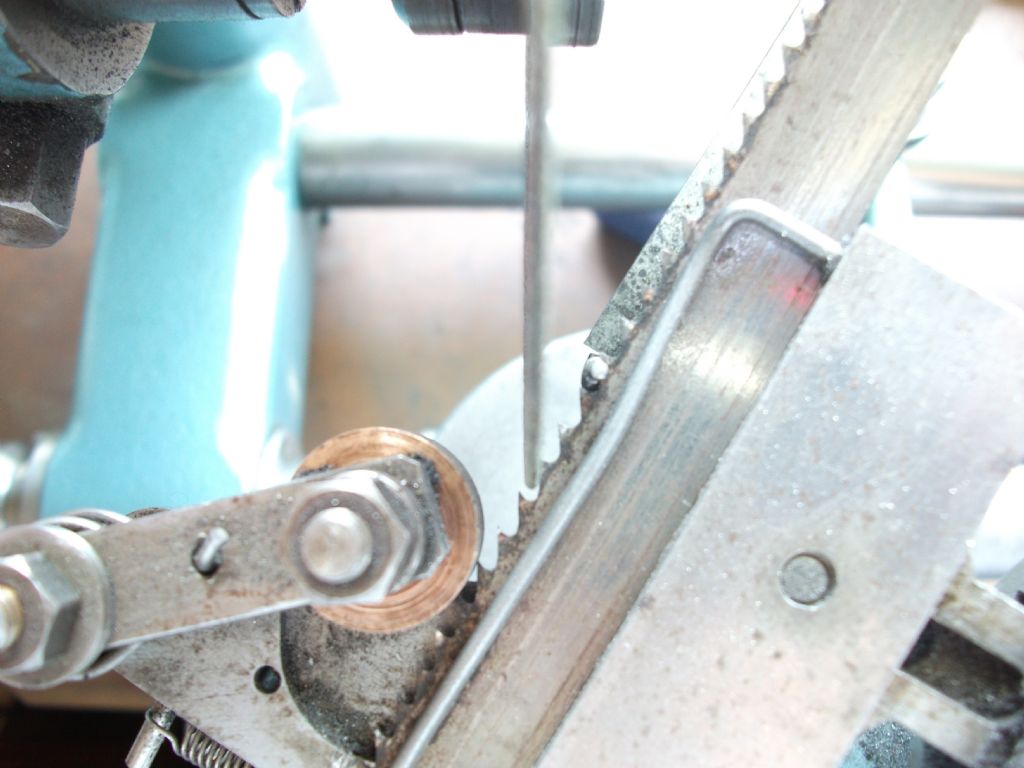
|
Thread: Myford ML7 feedscrew misalignment |
11/03/2022 10:04:29 |
Posted by Chris Bill 09/03/2022 21:57:14
Hi all,
I just replaced my imperial, standard length feed screw on my
ML7 for the long cross slide metric one.
Seeing the problems that you are having with this ,there was no
indication from where that you obtained this replacement leadscrew.
There have been 2 such similar threads on replaced Myford
leadscrews that have had the same problems as you have.
Just as a matter of interest did this screw come from RDG.
The two similar thread postings are below and may be worth reading .
https://www.model-engineer.co.uk/forums/postings.asp?th=175278
https://www.model-engineer.co.uk/forums/postings.asp?th=173467
John
|
Thread: Cross-slide fixture plate considerations |
06/03/2022 20:53:25 |
I should have added in the last post on this about using
a thick plate instead of a thin one as Callum has suggested.
The 2 tee studs that hold the top slide on are in a radial
tee slot ,these can only be removed by removing the cross slide
lead screw as the access hole is above the lead screw,if you
use a thin plate it is very likely that the studs will protrude
above the surface of the plate ,if you need to set up as in
this photo here the studs would have been in the way.
Using a plate of this depth the studs sit in holes drilled through
the plate and below the surface. A piece of steel plate is
likely the cheapest option in these sizes ,i recently
bought a similar size plate 25 mm thick around 6 inch wide
2 foot long for around £70 . The extra weight it adds to the cross
slide is no disadvantage in milling operations.
John
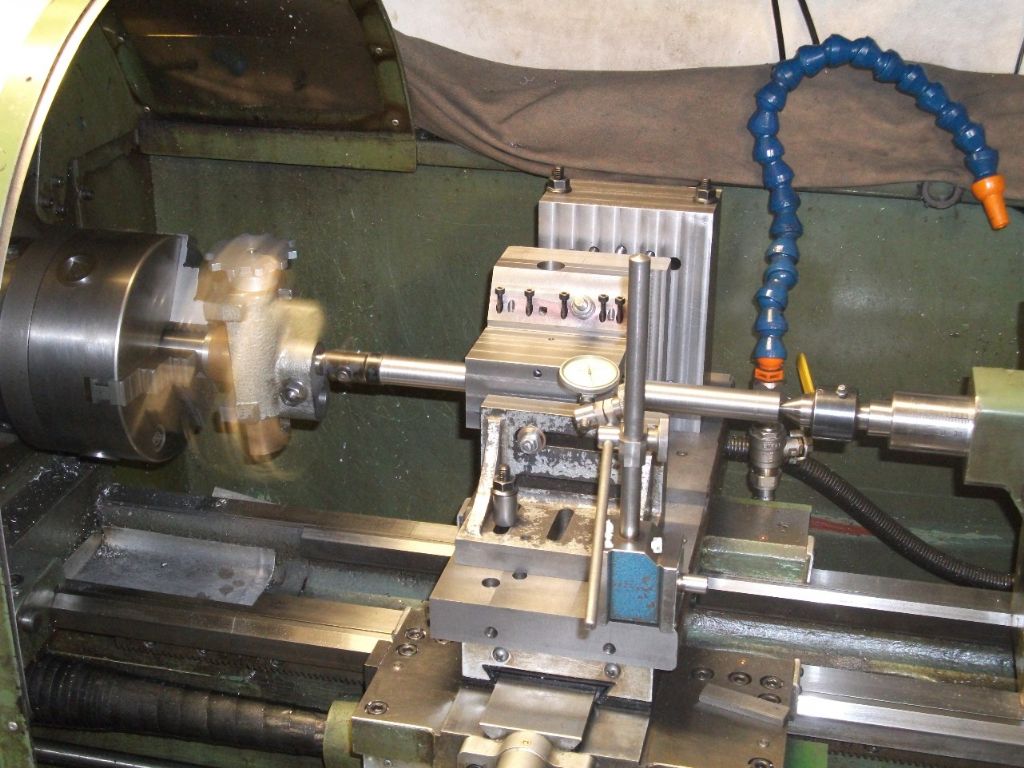
|
06/03/2022 16:49:35 |
Posted by Calum Galleitch 06/03/2022 13:52:11
As a milling machine is not an option for the foreseeable, I'd like to undertake light milling operations
in the lathe as well as other operations involving attaching things to the cross-slide. However, the
cross-slide on my lathe is not big enough to consider adding T-slots. In the long run manufacturing
a replacement cross-slide would be ideal, but I'd need both a big enough mill and the skills to do it!
So my thought is to make a fixture plate in aluminium which would be bolted to the cross-slide.
I don't require repeatability of fixturing, I think, so the aim is purely to create a secure platform
to hold things down.
The cross slide is something like 350x120mm: so my first questions are: how thick
should the plate be, and how securely should it be attached, to be reasonably rigid?
Recognising of course that "rigid" is a relative concept! I don't imagine myself milling
to accuracies of a tenth: more like holding a vertical milling slide to make things like
T-nuts or a QCTP. I was thinking that six mounting holes in total would be adequate,
in the corners and half-way along.
Looking online I see I can get a bit of 16mm plate for about £35. I am thinking
of an array of tapped M10 holes at say 30mm centres - does this seem
reasonable? Or would it be simpler and more flexible to just drill and tap
holes as and when I need them?
Tap drilling aluminium: I may be looking in the wrong places but aluminium
drills in 0.1mm increments don't seem to exist. I can find an 8.8mm carbide
stub drill on eBay: to go through say 16mm, will this be up to the job for say 40-odd holes?
-------------------------------------------
I have the similar machine to the Cub 750 in the Warco GH 1000 ,i also have plate
mounted as in the photo here it is 15 " long 6" wide and 1" thick at its machined size.
There are only 6 off 6 mm cap head screws to fix it.
I think you will need to re think the "I was thinking that six mounting holes in total would be adequate,
in the corners and half-way along" .
as you will find the cross slide at the back end is just a thin shell to cover the lead screw over
a length of about 4 inches and will not provide much of a secure fixing.
The cross slides on these machines are not that rigid ,a thick steel plate would be more
the thing to go for if you are unable to machine a cast plate as i have ,the aluminium
plate will add little to the rigidity of the cross slide.
John
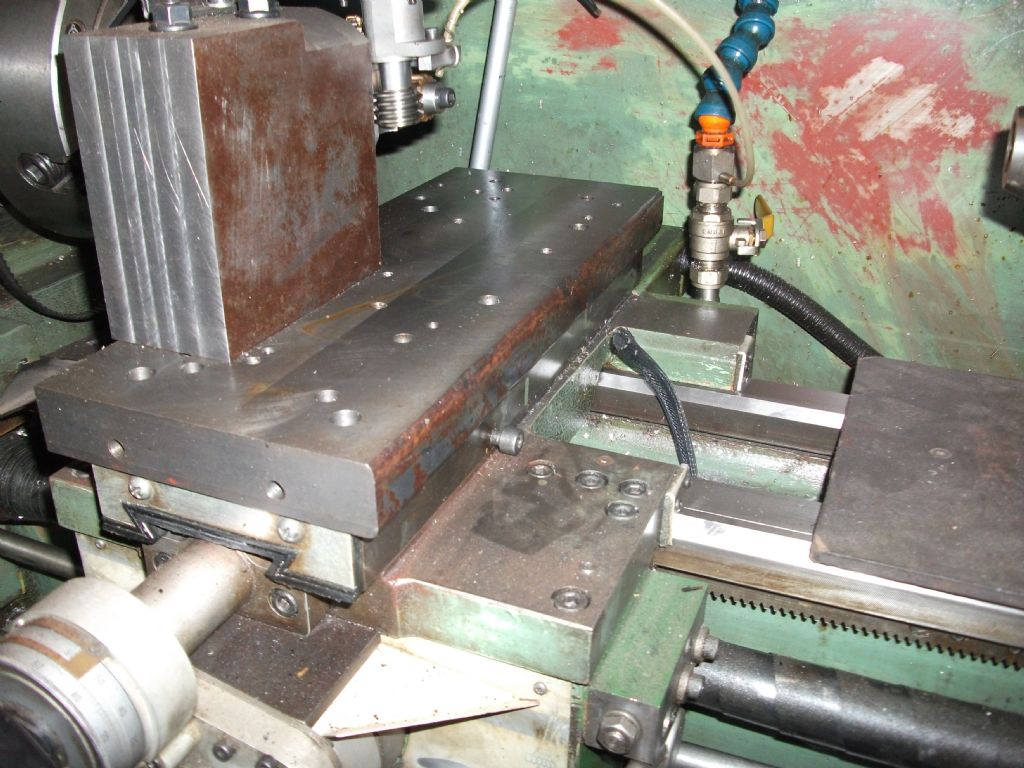
|
Thread: Precision ground flat stones in UK? |
28/02/2022 13:31:28 |
Here are some flat stones that made some time ago ,as Brian Wood has
said they can be easily formed by rubbing in three's to eventually get to
a flat condition, two of these three i already had but were badly hollowed
the third i bought from a second hand shop in much the same condition.
Using two concrete slabs that are fairly flat to start with and some sharp sand
they can be conditioned to bring them to a flat surface and from
there on the oil stones can be flattened to take out the dips,it is a long
process and best done in short sessions,Final finish using wet and dry
paper on a surface plate with paraffin as a lubricant and then lapping them
together.
You can not get to the same finished edges as described in
Robin Renzetti's video here
https://www.youtube.com/watch?v=DVLXsq7pi9Y
but they work well enough on just plain flat surfaces, not worth doing
if you don't have a surface grinder to finish work in the first place.
John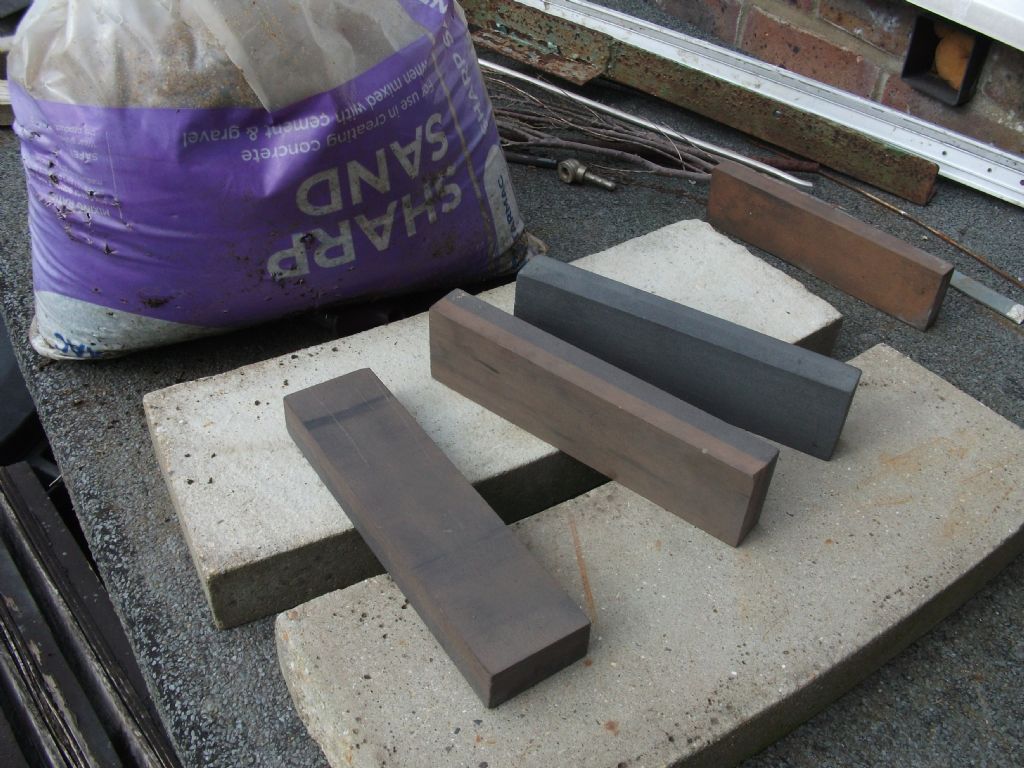
|