Thread: Where to buy small quantities of 316 steel 60mm (2 3/8 inch) diameter |
08/07/2022 10:49:10 |
Try metal 4u
https://www.metals4u.co.uk/materials/stainless-steel/stainless-steel-round/1254-p
60 mm dia 316 x 120 mm long £ 54.35 + post
John
|
Thread: Home made jet engine |
05/07/2022 15:35:50 |
Posted by Andy_G 03/07/2022 21:26:15
(There is nothing available via the GTBA - I am a member.)
About the only non-Chinese source is Jetmax, as you say, but taxes and shipping
pretty much double the advertised 230 euro cost of a 66mm turbine wheel
(and you'd probably want the matching inconel NGV which would cost the same again.).
There are cast turbine wheels advertised on Alibaba and other Chinese sites
which are about half the cost of the Jetmax ones.
In any case, I thought that was too much money to sink into a project for me
(I didn't want a jet engine, particularly: I wanted to *try to build* a jet engine) - the
Kamps design is one of the few still available that will tolerate a home made turbine
(even a stainless one), albeit ar reduced performance, which is why I chose that design
- I was very tempted to try one of the original FD3 variants (since this is what had sparked
my interest, back in the 1990s) but the Kamps is a much better design.
If you just want a jet engine, the answer is to buy one! :D
There is a GTBA project engine coming to fruition that uses a radial inflow turbine
(rather than an axial turbine as used in most of the model jet engines) that would
allow turbocharger turbines to be used.
------------------------------------------------------------------------------------
First of all you have made an impressive job on this Kamps engine design ,the EGT
is very low ,did you find out the top end speed and have you done any thrust measurements?
I used to be a member of the GTBA but let it lapse when they went on line only
as back then i had no internet connection , i still have one of the original GTBA
commissioned turbine wheels seen here in the photo along with a Wren
MW 54 wheel also there is a 66 mm wheel and stainless cast NGV
also from Wren. Since they disappeared these parts i guess have gone.
Some of these parts are seen here ,on the left Some Wren mw 54 parts
a bought turbine wheel , milled NGV centre from 316 ss , compressor wheel a
free-be from a collection of them, 3 off part machined diffusors.
Towards the centre top some milled 718 turbine wheels and the GTBA and
Wren wheels ,on the right some FD 3/64 parts , in the lower half a nearly
reclaimed disc of inconel most probably 713 from a scrap radial
inflow wheel.
I seem to remember that before the availability of cast turbine wheels
inconel slices about 6 mm wide were around the £35 mark ,that was over
20 years ago , by buying a length of inconel bar brought that price down to about
£8 to £10 ,of course you still have to slice it up by whatever means and the mill
the blades.
That is why that i said it would be a better option to buy a ready made wheel
as the real cost is only the difference from buying the material and the tooling
and the time minus the cost from the ready made item.
With that in mind the home made compressor wheel milled from the solid
seen here and in previous photo's is a similar situation the aluminium blank
probably about £5 or £6 plus all the work to get to finished job when you can buy
a new cast wheel for £14 + vat and free shipping does not make it really
worth while.Although i have to say that you do learn a lot in doing something like this
also as i wanted a reverse rotation wheel it is a simple matter to change
some of the axis polarities to be able to do this ,in the photo here is a wax
test cut reverse rotation wheel alongside the aluminium one.
Seeing the last part that you had written about the GTBA radial inflow project
is not really surprising as a complete rotor set is only about £35 for an engine
similar to the original JPX type engine .
The last photo here shows the much modified Shreckling FD 3/64 engine
installed in an airframe ,you can just see parts of the fuel tank in front of the
engine ,its bigger than the engine,the model has never been flown.
Most of the parts seen here were made 10 to 15 years ago.
John
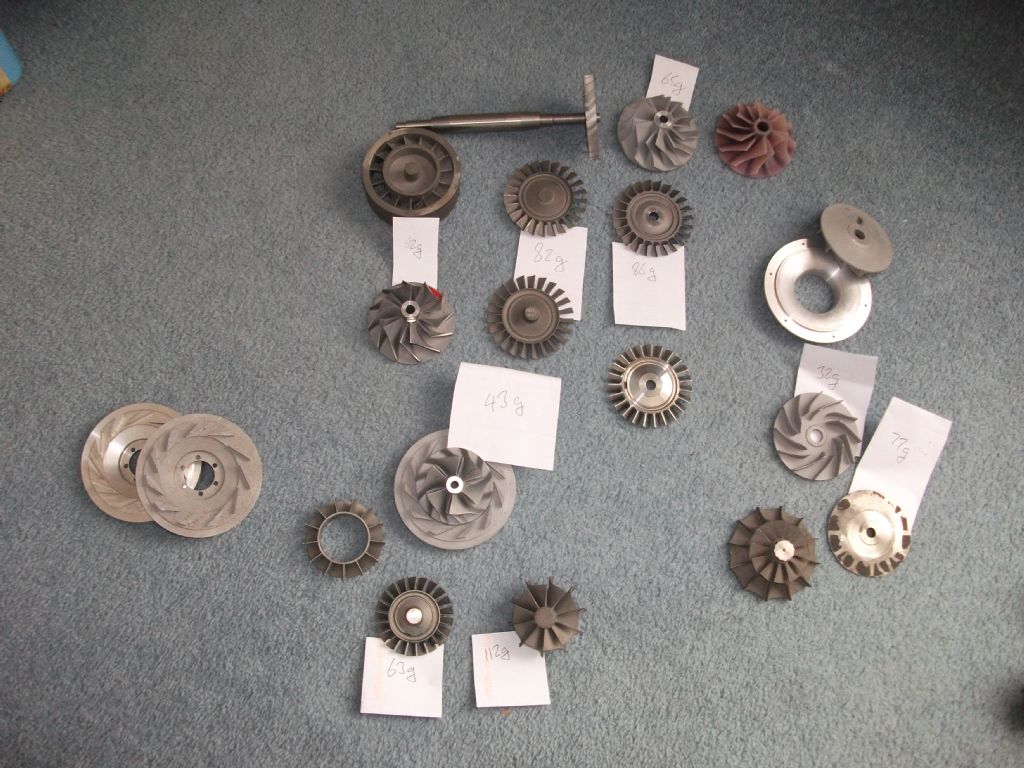
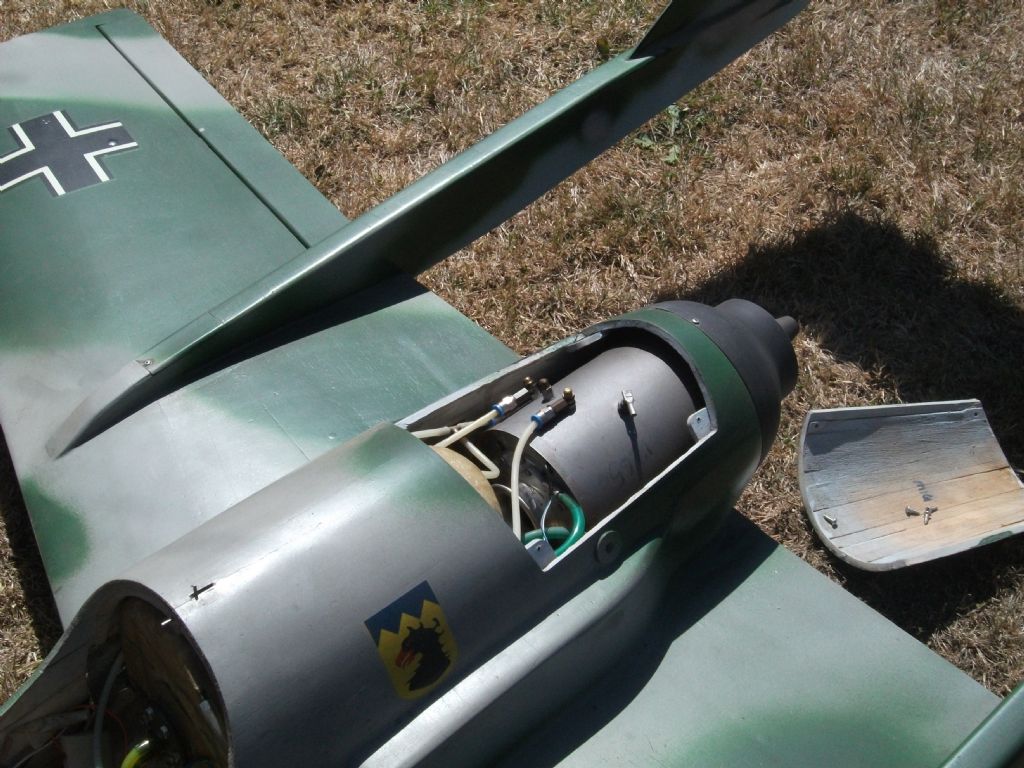
|
Thread: Casting Advice (no laughing please) |
02/07/2022 20:08:54 |
Posted by Steve355 02/07/2022 09:54:21
Morning
Is there anyone out there who has advice for a total beginner at sand casting?
I made a waste oil burner and furnace, after a lot of tinkering it’s working pretty well and can
get up to 1100 deg C or so without too much trouble.
My first project is to make some brass sanding blocks for making woodwork moulding planes.
I made a pattern on a 3d printer. I used play sand (fine and consistent) and about 10% fireclay
as DIY greensand.
I used a cast iron flask, packed down the pattern in the sand vertically and removed it carefully.
I melted down the brass and poured it in. The result was, well, roughly the right shape, but it had
a big nodule on the bottom (presumably caused by the pouring brass) and a terrible pitted finish.
of course I can sand out some of the pitting, but that’s not the point.
Does anyone with experience have any tips? See pics. Yes it’s terrible, I know.
Steve
---------------------------------------------------------------
I started casting around 1984 ,i was at a Model engineer show and one of the stands
was selling crucibles along with give away leaflet , i bought one i think it was about tenner.
That was about as much as i knew about casting,back then there was no internet and
there was no one that i knew of that had done any casting,first problem no sand, i had a ring
around after looking through the Yellow pages most of these were industrial type suppliers
and came with the warning of the usual that's too dangerous you'll end up killing yourself
(much the same as you often see on this forum), we only supply 20 tons at a time.
I phoned around some local foundry's and they were most helpful ,bring some buckets
and you can have some ,i still have the same 2 dustbins full of sand now.
My first castings were done using an old tin oil drum full of coke and an old cylinder
vacuum cleaner to provide a draught, some of the early castings were nothing more than
useful blobs of metal but you learn as you go along.
Eventually i got fed up with the tin can and coke furnace and built this modified Dave
Gingery furnace (in about 1989) supposedly will melt 20 lb of cast iron in 45 min i don't know if it will
I've never tried it with iron , an A8 crucible will fit inside.
(First Photo)
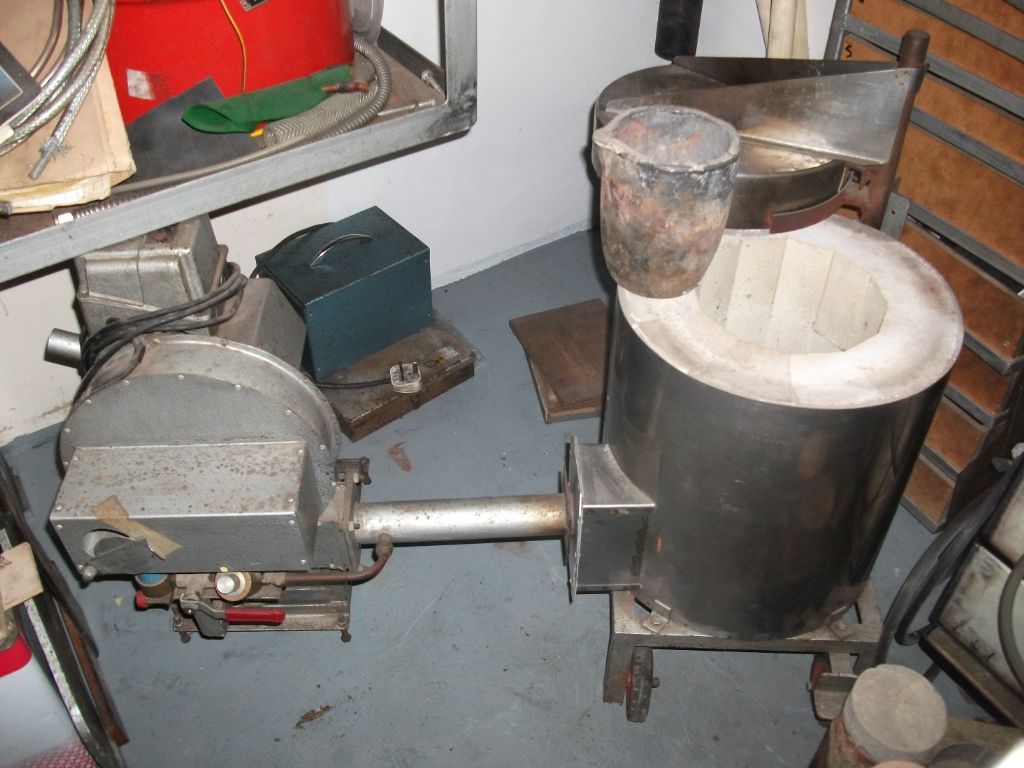
The thing is when you have done some of this you tend to forget how much equipment
that you have accumulated over time, the furnace the crucible some sand and then all of the other
stuff that you need lifting and pouring rings , moulding boxes, patterns and some
decent safety equipment and so it goes on ,it all adds up to some expense in both
money and time.
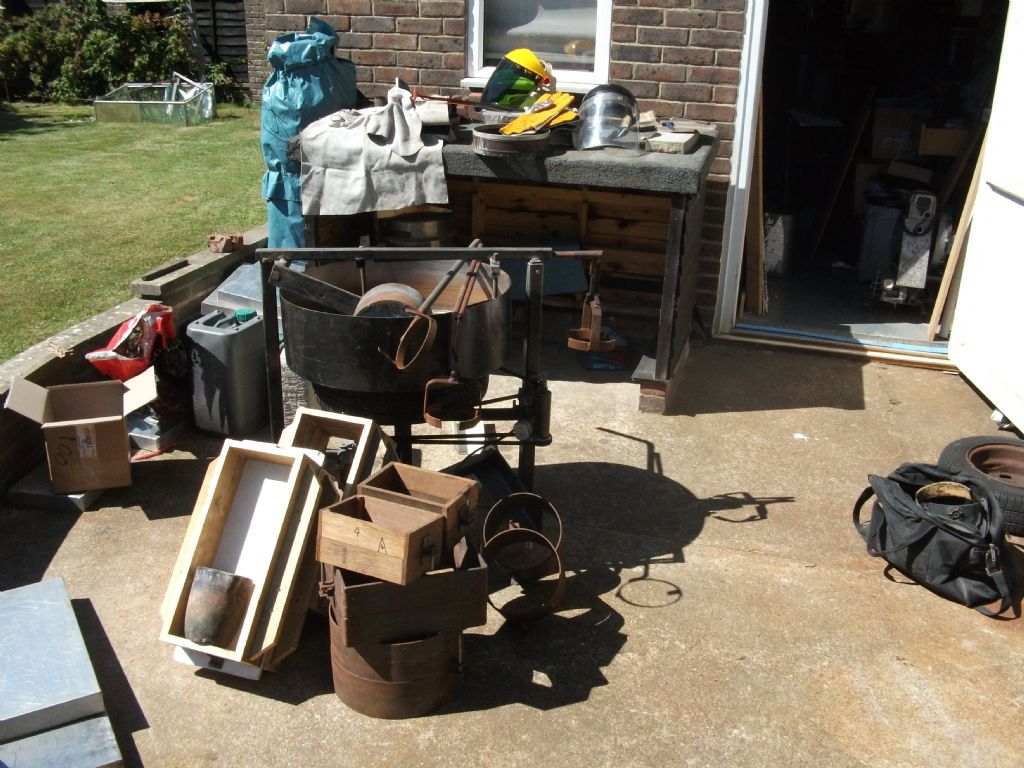
The 2nd photo here shows some of this stuff in the foreground some moulding boxes,
crucible , lifting tongs, pouring rings , behind , a copy of Luckygen's sand muller a recent
addition ,at the back leather aprons leggings face shields and gloves.
I don't do much foundry work the last time was about 15 years ago but in the next week
or so its getting fired up again if the weather stays fine. 3rd photo.
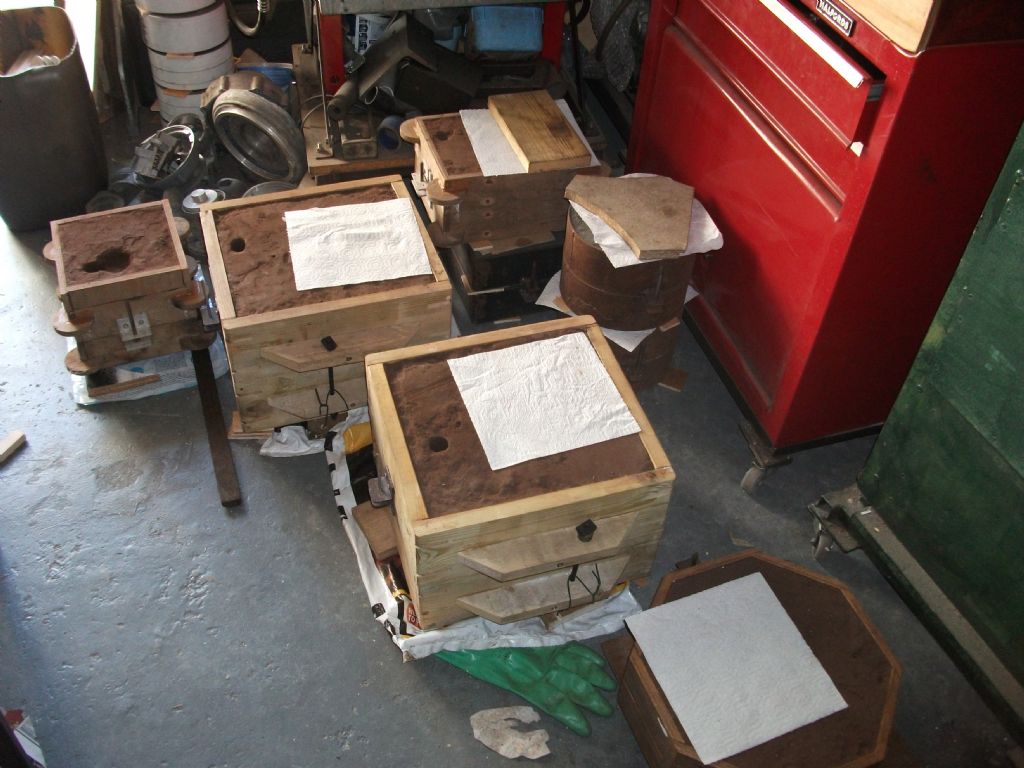
It should be much easier than when i started as there is so much stuff available now and
useful advice , there's Luker, Pat J, and Noel Shelly ,worth looking at the videos
from Luckygen ,Old foundry man and Myfordboy they will all have something that
will be of use to you.
You just have to stick with it ,work carefully follow some of the advice and watch some
of the videos .
John
|
Thread: Home made jet engine |
02/07/2022 17:26:35 |
Some useful download plans can be seen here from Gerald Rutten (zip files)
http://www.gerald-rutten.nl/turbines.htm
They use the same gas container as the early Shreckling engines ,the most thrust obtained from the engine that i made was about 6 lb ,i think the GR 180 in the plans above produces about 36 lb.
---------------------
https://www.turbomaster.info/eng/applications/compressor.php
shows the sizes of nearly all made compressor wheels and is a
useful reference.
-----------------------------------
The 2 compressor wheels here (1st photo) were from Aliexpress ,the one on the left
is a K27 wheel 47.3 dia inlet and 73.9 dia od 14 blade
the one on the right is a TO4B 45.8 inlet and 70 mm dia od 16 blade.
------------------------------------
The 2 compressor wheels shown here (2nd photo) , on the left milled from
2014 t6 aluminium 68 mm od for KJ 66 engine , the one on the right
is a KKK 5326 123 2038 cast wheel also for a KJ 66 engine.
---------------------------------------
The turbine wheel seen here (3rd photo) is for Shreckling FD 3 /64 turbine engine
milled from 718 inconel 20 years ago, perched on top of the remaining 17 inch
of 2 3/4 inch dia inconel 718 bar .
It is perhaps not worth making a turbine wheel from solid these days
unless you already have the material and the means to mill them ,back then
ready made wheels were only just appearing from the GTBA when they had a
batch made for members of the organisation.
www.jetmax.ch sell ready made wheels from about 66 to 82 mm dia from
about 165 Euros which suit the KJ 66 engines and also the Gerald Rutten
turbines.
John
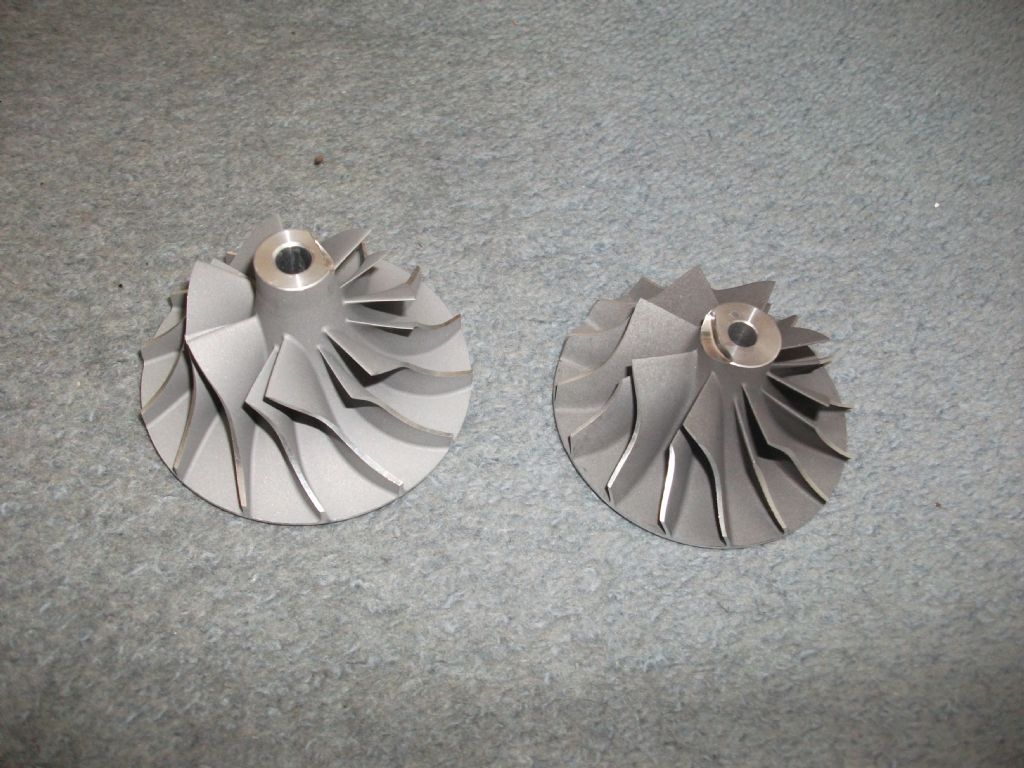
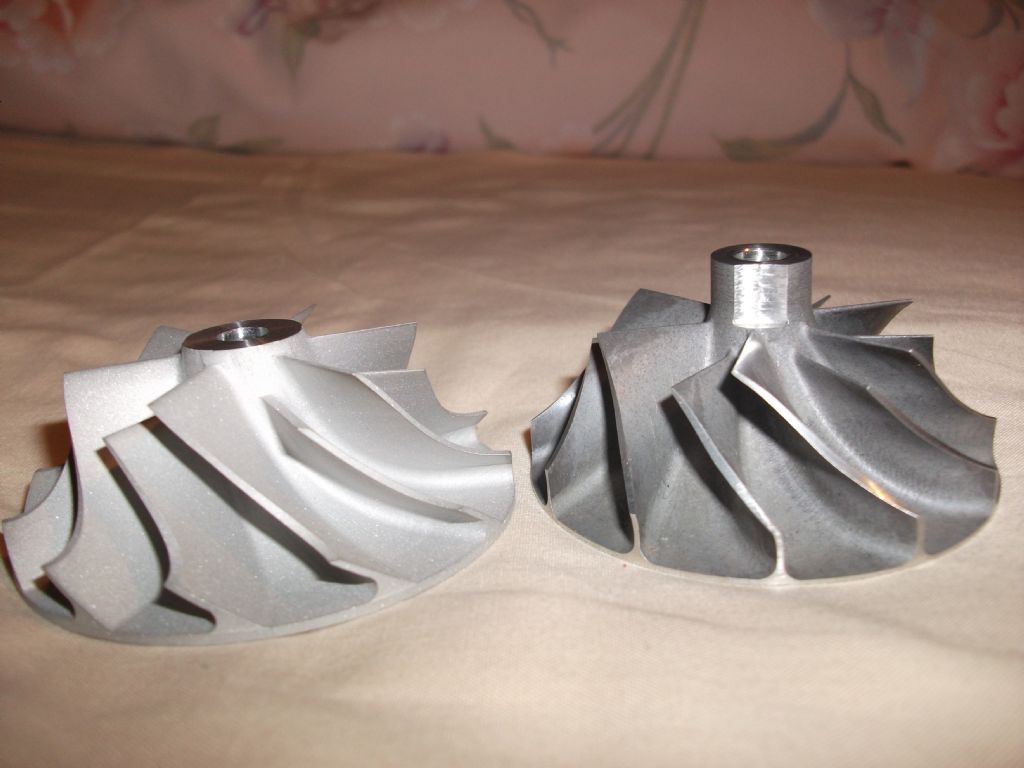
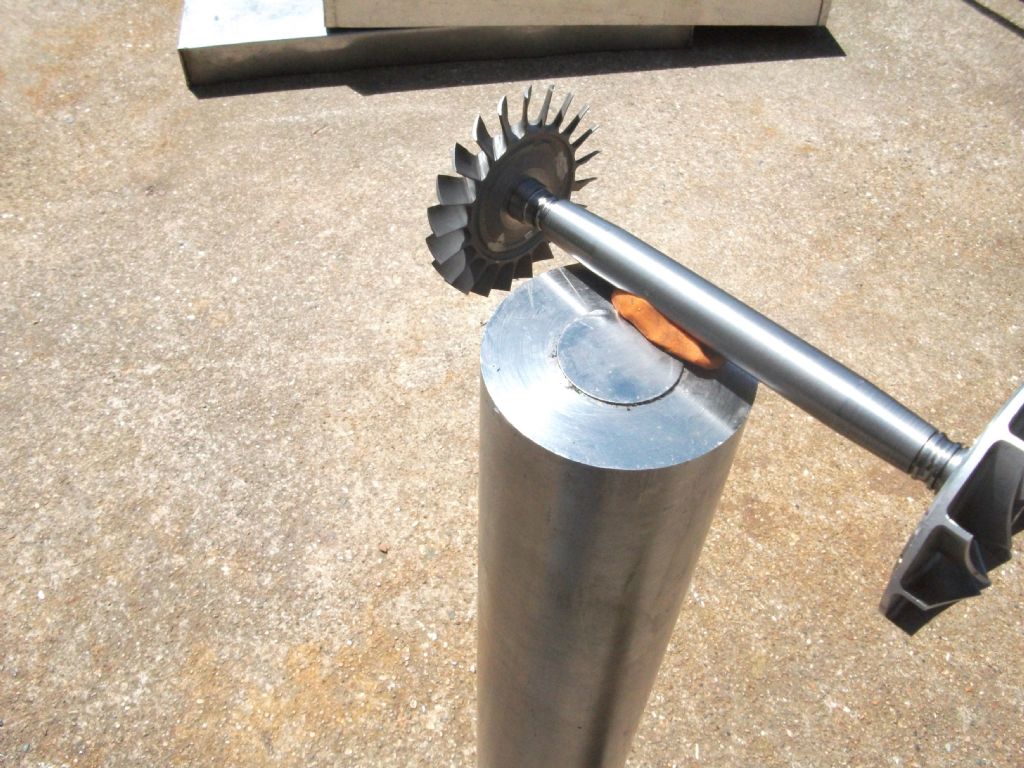
|
Thread: See Through Jet Engine |
30/06/2022 17:11:45 |
Posted by Brian John 30/06/2022 13:07:03
Watching this makes me want to build one just for the sound alone !
---------------------------------------------------------------
Some useful download plans can be seen here from Gerald Rutten (zip files)
http://www.gerald-rutten.nl/turbines.htm
Photo here of some Wren MW 54 parts and some KJ 66 parts.
On the left wren MW 54 ,in the centre KJ 66 milled from the solid
compressor wheel and blank behind .
New compressor wheels can be found on Aliexpress for less than £20
like these here in the 2nd photo.
Standard 608 bearings can be used and are good to about 120,000 rpm
but have a short life . A cheap alternative is to re-ball a standard bearing
with Si3N4 ceramic balls ,the inner race needs to be reground to be able to
fit with a phenolic cage or fill the whole bearing to make a full compliment
bearing.
John
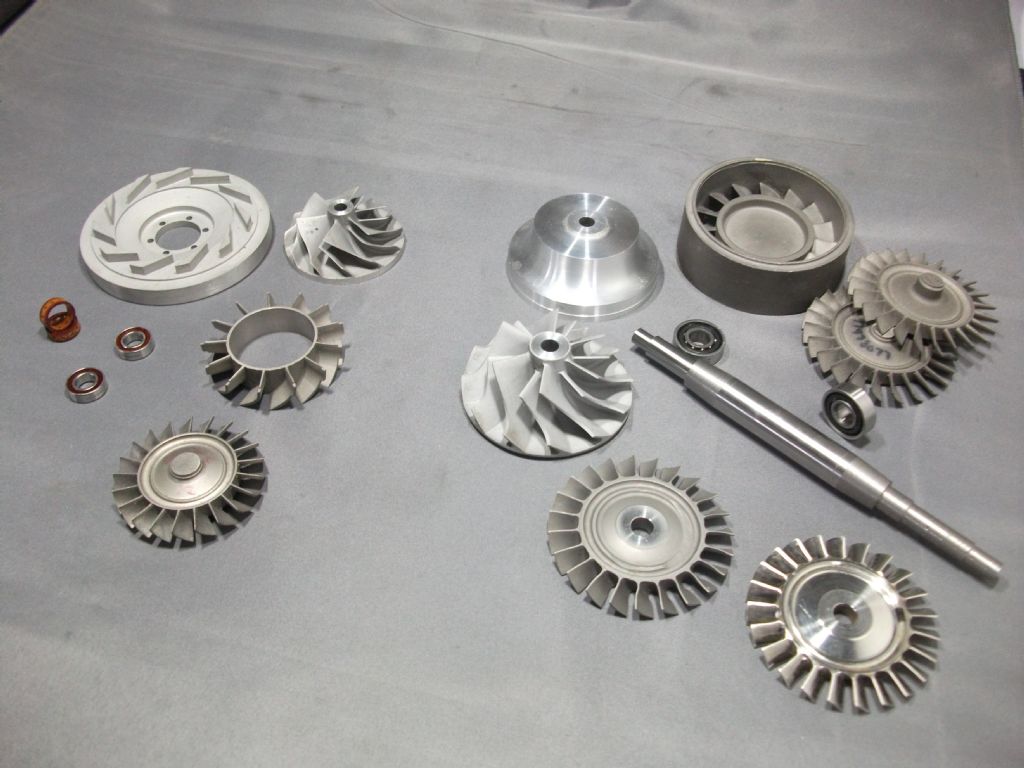
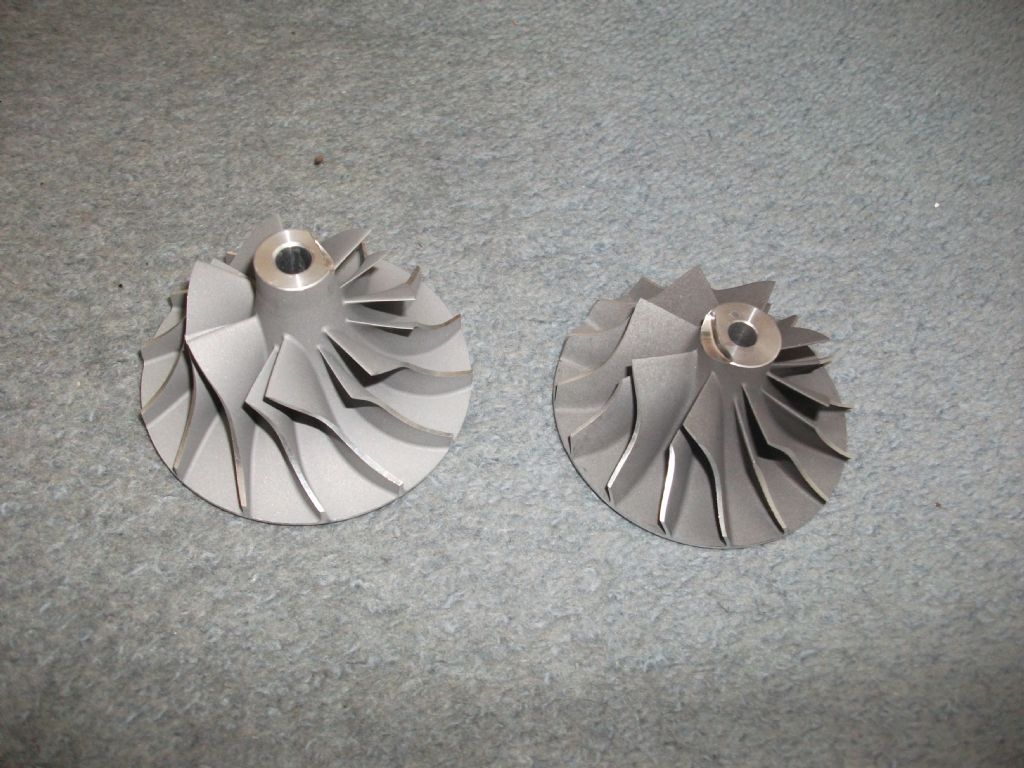
|
Thread: Four Index Thread Indicator |
21/06/2022 13:59:29 |
Just as an update on threading indicators see this on lathes uk
http://www.lathes.co.uk/universal-thread-dial-indicator/index.html
John
|
Thread: Bearings or bushed |
31/05/2022 20:41:02 |
Aliexpress sell full ceramic bearings for somewhere around £4 each depending on size some will work up to
800 C only at low rpm (200) there are hundreds of them , type in " ball bearings high temperature" to scan through,not able to put reference on here as it will be taken down.
John
|
Thread: Model Turbines |
23/05/2022 09:48:34 |
Michael
This looks about the same size as the one in the springer link .
Good luck!

John
|
23/05/2022 09:22:29 |
This may be of some interest for making a high speed machine spindle.
https://link.springer.com/article/10.1007/s40684-019-00105-5#Fig7
John
|
Thread: mini grinders |
20/05/2022 11:39:26 |
Posted by ega 20/05/2022 10:59:48
John P:
Is that a Quorn spindle in your photo?
----------------------------------
No, it is 1 of 3 spindles made for this machine as internal
grinding spindles ,this one has a Quorn nose and can use all of the
Quorn wheels that i have.
Similar construction to the Quorn spindle but slightly larger ,uses
17x35x10 mm bearings .
John
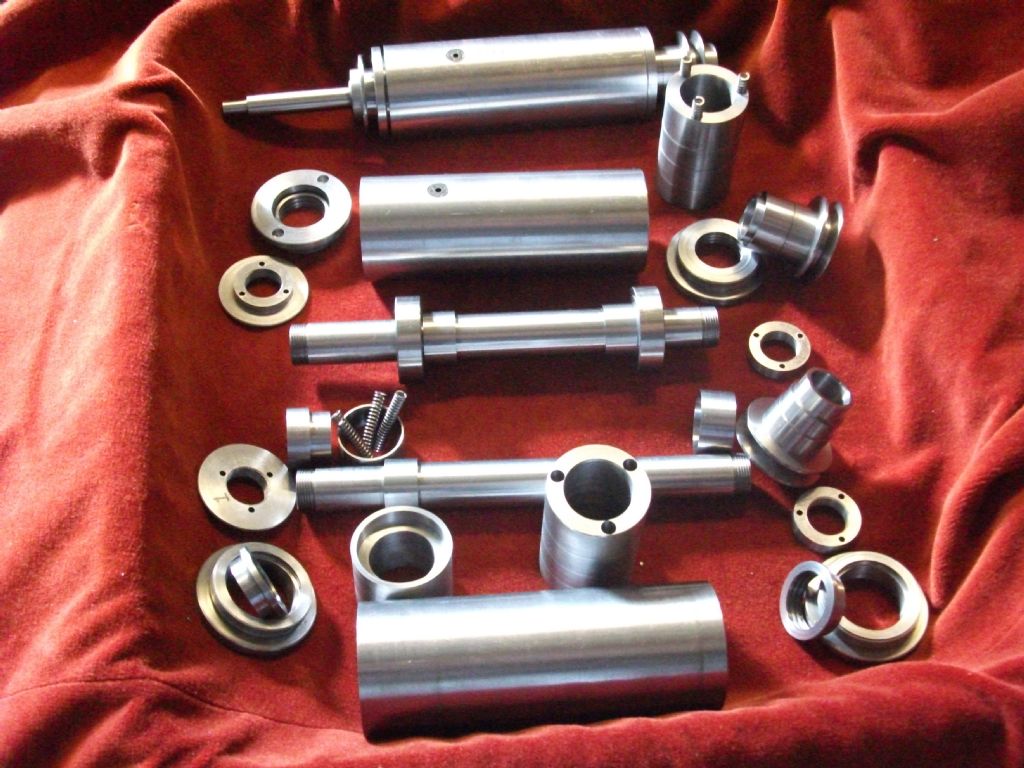
|
19/05/2022 20:47:06 |
Posted by William Chitham 19/05/2022 18:55:52
Never used one but a pencil type air powered die grinder might be an option,
maybe they don't use so much air as the standard sized ones. Very fast and
not too expensive if you already have a compressor. I noticed this one in MSC's
last advantage sale:
Jupiter Micro Die Grinder
William.
--------------------------------------------------
This is the same pencil grinder from J&L ,runs through an air
pressure regulator at 90 psi from a 2 HP 25 litre tank compressor.
Compressor will cut back in after about 2 to 3 minutes to keep it running .
Same sort of pencil grinders from Aliexpress from about £12
and free delivery.
John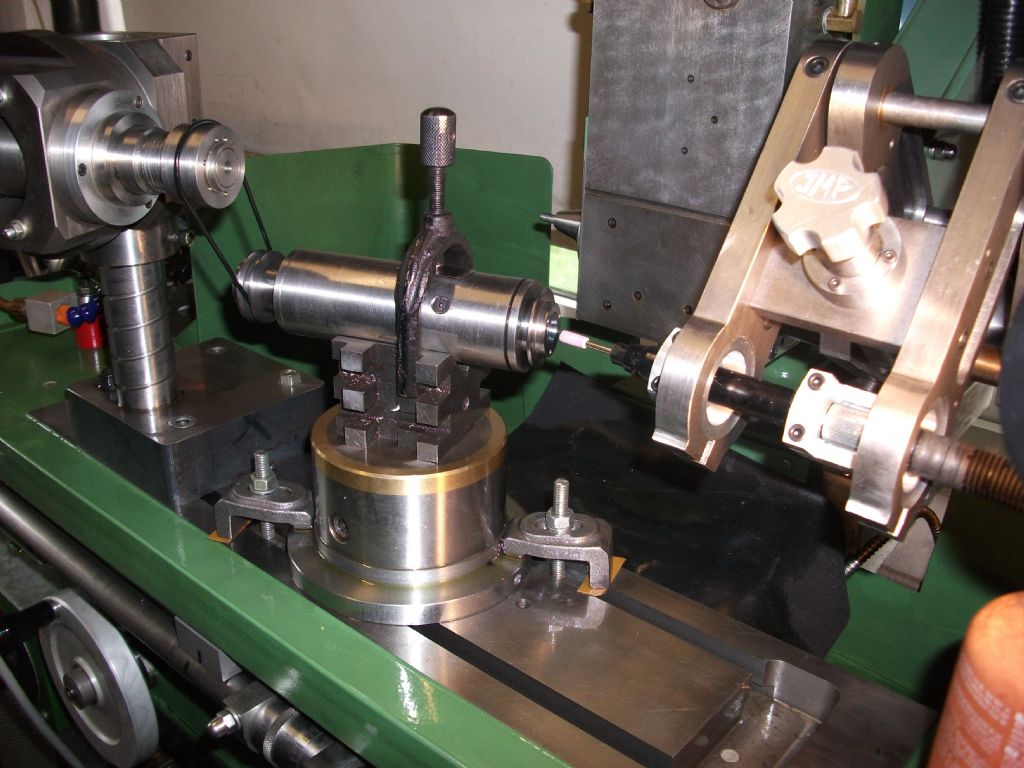
|
Thread: Re-boring Grind Wheels |
15/05/2022 10:26:37 |
Posted by Mark Rand 15/05/2022 09:39:49
I'll leave people to their apprehensions and assume that none of them have
ever had to do any form grinding, face grinding or endmill sharpening.
-----------------------------------------------------------------------------------
How very true ,bring up any of these grinding type of threads and you see
the same old stuff about the dangers .
I sharpen my milling cutters using a cnc machine ,add in the mix of grinding
wheels and computers to run them and a whole new bunch of scared to get out
of bed types will be posting on here.
Despite the abundance of so called experts on grinding there seems to be
very little or none written on the practicalities of actually doing it.
John
|
Thread: Minimum depth of cut possible with carbide tooling on S7 |
13/05/2022 14:38:47 |
Posted by Andrew Johnston 13/05/2022 14:07:26
Best to sit down and put on the seat belt before looking at prices for CBN inserts.
Andrew
Cheapest price on Ali******s iv'e seen is £4.59 for a VNMG160408 and free shipping.
John
|
Thread: Re-boring Grind Wheels |
13/05/2022 13:27:03 |
Buying a reputable make or from professional suppliers is no guarantee of getting a good
wheel these days.
The wheel seen here on the left is a Norton wheel from RS not cheap ,the mounting area
was like a rollercoaster track ,the balance was poor but easily corrected when mounted
on this heavy hub ,the centre of gravity is moved to the back of the wheel where there are
two balance rings to even things up .
The other three wheels here all from China all cheap and very well made without the
problems the Norton wheel has , the 2 Quorn wheels are perfectly balanced as is.
John
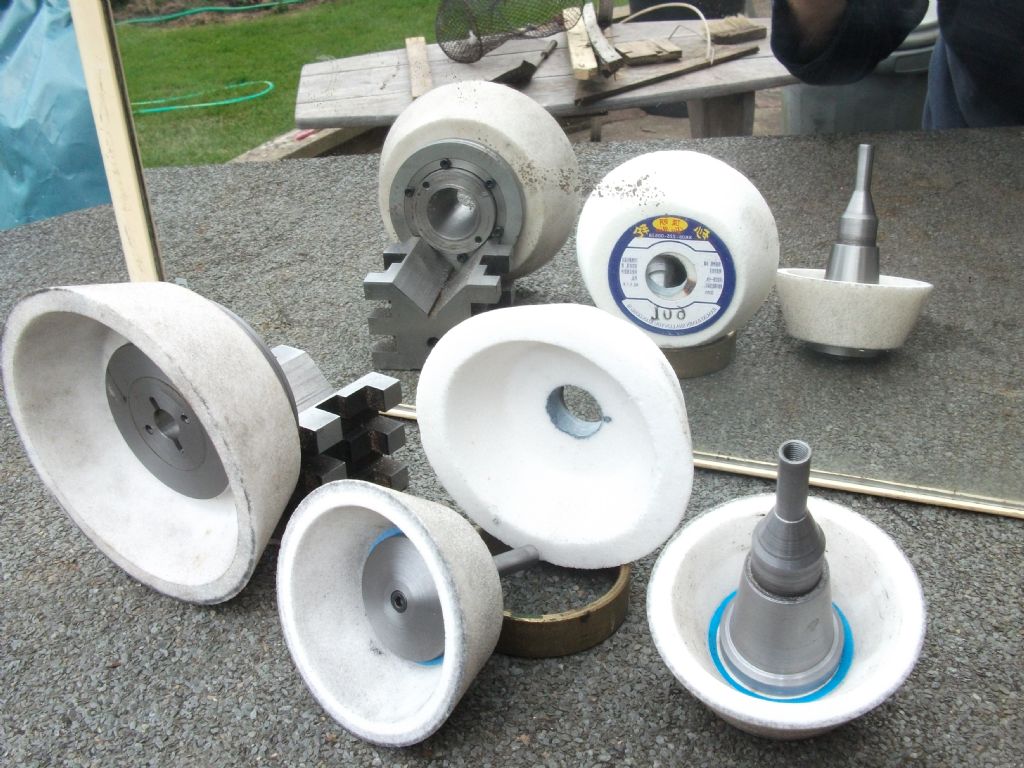
|
13/05/2022 09:17:18 |
In this video Dan Gelbart shows at about 5 minutes 45 some reworking
of grinding wheels.
https://www.youtube.com/watch?v=sFrVdoOhu1Q
For those of us who don't have such facilities China is your friend
via aliexpress who sell diamond core drills which can easily
modify or make up stones from old or even new grinding wheels
such as these.
John
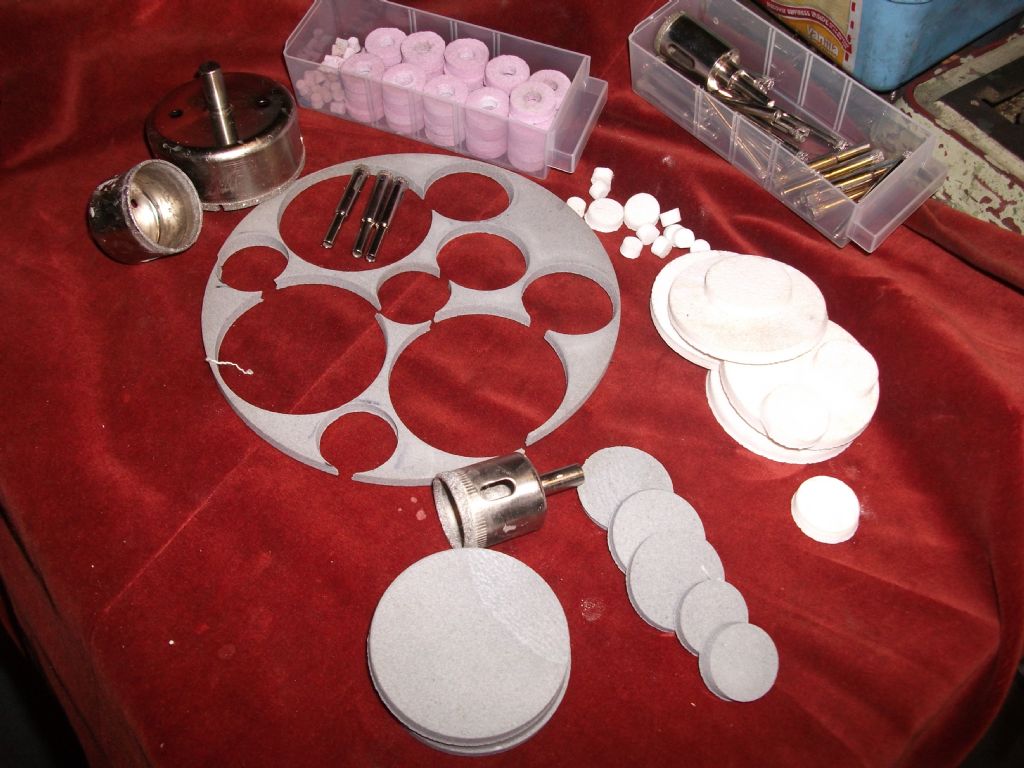
|
Thread: Adding a leadscrew to a lathe ? |
09/05/2022 14:51:02 |
Posted by Rich2502 09/05/2022 14:15:41
Any one retro fitted a leadscrew to a small lathe? ( 15-20" between centres )
There are now motor controlled set ups withh off the shelf ballscrews that require
no gear train so that would cut out a lot of the work.
Is this a practical project or a rabbit hole ?
------------------------------------------------------------
Warco cnc conversion Mew 207 through to 212,
a bit bigger than your machine but the principle much the same.
John
|
Thread: Thread gears for Warco GH-1322 lathe. |
04/05/2022 10:08:18 |
Hi the plate you have shown is the lathe feed chart.
In this video there should be above this at 1.03 minutes
shows the listings for pitch. TPI ,module and DP.
https://www.youtube.com/watch?v=d3km1zmAasY
John
|
Thread: machining a t5 pulley |
29/04/2022 09:31:50 |
Hi, Fabio
If you look at hpc gears and the T5 pulleys it will give you
the sizes for PCD and pulley OD .
https://www.hpcgears.com/
The calculation is for example your 80 tooth pulley is
80x 5 = 400 divided by Pi 127.33mm = PCD
127.33 - 0.83 = 126.50 mm pulley OD.
Looking here will give you the pulley tooth belt profile.
https://us.misumi-ec.com/vona2/detail/110300406820/
-------------------
An article Form relieved toothed belt cutters published
MEW 164 June 2010 shows toothed belt cutters
made using the Eureka form relieving tool which may be
of some interest.
I have recently done something similar using a ground fly
cutting tool to cut 1/5 XL pulleys the photo here
shows a 66 tooth pulley being flycut / hobbed
takes about 4 minutes to cut all the teeth.
A gear tooth caliper is a useful thing to have when grinding
these sort of profiles ,they can be had from China these days
for around £25.
John
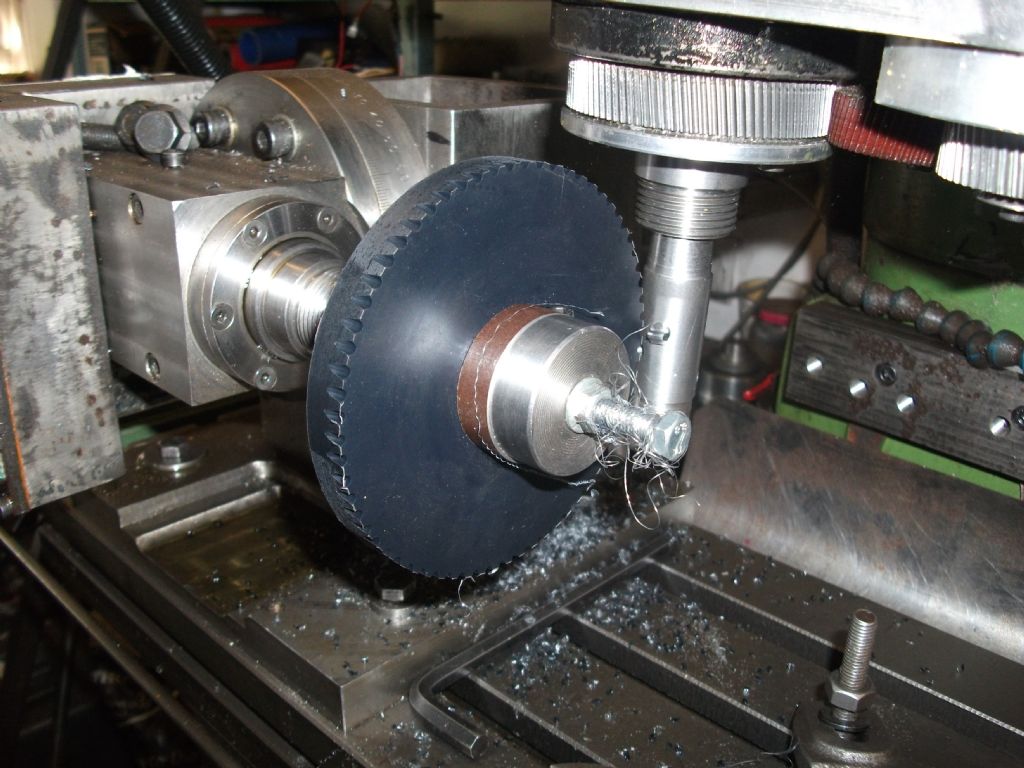
|
Thread: NEW CONTACT EMAIL FOR MEW EDITOR |
26/04/2022 16:45:16 |
Posted by JasonB 26/04/2022 14:07:43
Well as it looks like the three current editors don't want the article in it's current format why no
just put it on the website as a form of build thread, just host the drawings somewhere and link
to them as I have done on several engine builds in the past. That way anyone interested benefits,
nobody misses out and those that don't want to read it won't feel they have spent money on
something not of interest.
Half measure may be to do as I have done on my published builds and Luker has followed
suit is to reduce the content of the published article and post what you cut out on the forum,
I tend to only use about 2/3rds of the photos I take for publication but put the rest into the
thread. Would work for all as I seem to remember complaints about bulking out articles
with gratuitous photos in the past.
--------------------------------------------------------------------------
Strangely enough i though i was posting to correct Neil's previous errors ,since you seem to
have decided no one is interested in this you have the satisfaction of knowing there will
be plenty of room for some of these regurgitated type of articles ,but what do i know
i'm not the expert on these.
-----------------------------------------------------------------------------
Posted by Neil Wyatt 26/04/2022 11:41:41
David,
I'm sure with your past experience you will be well aware I can't leave up posts with potentially
commercially sensitive information in.
I understand you have an axe to grind and that your approach to editing MEW was
different to mine. Can you just accept that and move on, I'd rather not have to endure petty sniping.
Neil
---------------------------------------------------------------------------------------------
Seems almost a waste of time trying to hide this sort of thing when by typing in this here
brings up the entire history.
Mortons Media Group Ltd companies house ( Net Worth: £3,420,879.00)
My time media companies house ( Net Worth: £1,624,550.00)
John
|
26/04/2022 13:44:59 |
Posted by Neil Wyatt 26/04/2022 11:53:38
Posted by John P on 26/04/2022 11:08:06:
I know how difficult it can be to write a long construction article,to get the
sequencing for machining operations do all the drawings etc ,unfortunately
magazines don't seem to be interested in publishing these any more .
Hi John,
When I came to MEW, the commonest gripe from readers was that there were two very long
ongoing series occupying a significant part of each issue. Naturally, I responded by going the
other way.
Since then, I have relaxed a bit, using some medium-length constructional series in three to
four parts, or asking authors to split longer topics into shorter instalments. When I have exceeded
the three to four instalment length, I generally receive negative comments.
As I explained, the article you submitted to me last year would have run to around 170 pages.
At eight pages per issue, that would be about 21 issues.
Could I justify about 20% of the contributor content of each issue being occupied by the
same author and project for nearly two years? I think the majority of readers would prefer
to see greater variety.
My advice was that the article, which was very well written and presented, would best be
published as a book.
Model Engineer, with its two issues a month, can split ongoing series into alternating
issues and its readership seems more content with series lasting over several years.
Neil
Hi Neil
Just to put the record straight on some of the points that you have made above.
1/ I have never directly offered you the article for the Universal grinding machine,
the proposed article was offered to Diane around 11/09/2013 at the time
of her first posting on the above thread ,about 6 months before you were editor of MEW ,
it was submitted to Model Engineer on the 19th September 2014 and
then again resent to Martin Evans in the middle of October 2019 after
he said that he had no record of it.
I don't know it it was offered to you at some point via Model Engineer.
2/ The last article that i had published in MEW was in year 2017 /18
mew 257 . I have not written or submitted an article since before that date .
The balancing machine that you were interested in i never bothered to
write up as the page length you required was far too short, however
one forum member benefited from this as i sent him the drawings and an
explanation of the operation of this unit ,i must say i received some useful
feedback from him and friend on this , but of course every one else has
missed out on this.
I was writing up the second half of this Universal grinding machine but have given
up now as there seems little likelihood of it ever being published and
less so if the page rate has been cut.
John
|