Thread: How can I convert a 0.5 inch benchtop grinder to take 1inch wheels? |
07/12/2021 20:06:23 |
OK that sounds reassuring that I definitely should be able to fit the wheel with a 1 inch onto a 0.5 inch spindle. So I shall just go ahead and order the machine and the 3M deburring wheel.
Nicholas - yes, deburring will be crucial, not least because the 45 degree chamfer will create a dangerously sharp edge. But to get clear I shall still need to finish off the grinding by hand (using my diamond hone) in order to get a decent magnetic mating surface on the chamfers.
Further questions:
1. If it turns out that the deburring wheel doesn't come with filler bushes, would I need know exactly how thick (deep) the deburring wheels is in order to order the correct adaptor?
2. [Probably a stupid question but...] will I be able to fit a 20mm thick wheel onto the end where the (white) 40mm thick wheel is? i.e. Do you think that the fatter housing or attachment mechanism could be problematic?

Edited By John Smith 47 on 07/12/2021 20:11:53 |
07/12/2021 17:38:22 |
Hello
Is there a way to convert a benchtop grinder with a 0.5 inch spindle to take 1.0inch deburring wheels?
BACKGROUND
A friendly supplier has suggested that I buy a 6 inch benchtop grinder and fit a deburring wheel. He recommended a 3M Scotch-Brite fine deburring wheel.
I rather like the look of the:
"Charnwood BG6 6in Bench Grinder"
**LINK** (www.charnwood.net/products/product/p6-bench-grinder-20mm-grey-stone-40mm-white-stone-bg6)
...which seems to have a reasonable build quality and to run nice & quiet.
However unfortunately it seems have a spindle diameter of 0.5" (12.7mm) whereas the 3M Scotch-ScotchBrite deburring wheels only seems to come with hole diameters of 25.4 mm (1in) or 76.2 mm (3in).
**LINK** (www.3m.co.uk/3M/en_GB/p/d/b40065315/)
DETAILS
I need to make about 200 of my small steel parts. Fwiw, they are now 32x8xI.2mm grade 430 stainless steel, (although some I will need to cut down to a shorter length). I shall get the steel laser-cut. I have a choice of:
A) Get them cut using a 5-axis laser to create the 45 degree chamfer (which I can finish off by hand) but that will cost £2.30 each.
B) whereas I can get them cut in 2D for just £0.32 each, and then could take them to a machinist to mill the chamfers for another £0.75 each ==> total cost of £1.07 each, but this will involve a significant delay.
Either way, getting someone to deburr the steels seems like a bit of a waste of money for something that only takes a matter of seconds per part... Plus there is much greater flexibility if I decide to change deburring radius.
Any thoughts?
J
Edited By John Smith 47 on 07/12/2021 17:41:07 |
Thread: How can I cut 0.8mm thick stainless steel sheet more accurately by hand? |
01/11/2021 22:20:51 |
Yes, Platinum King blades sound like good advice as they are made from much harder metal than Super Pike, and I have bought some.
> tilt the blade slightly away from
To get clear, you mean that if the sheet of metal is held vertically in a vice, the tip of the blade is down, yes?
Oh, and teeth in any saw should always be pointing away from the handle, right?
(i.e. So that the cutting stroke is when you push the saw away from you.)
Wait, or is it like a "Coping Saw" where the cut is on the pull stroke?
> just seen your mention of the Eclipse junior hacksaw blades…
> do bear in mind that, because of the wavy edge, those produce a rather wide kerf.
Yes that's a good point. Do all 150mm hacksaw blades have that wavy edge?
Because I'm now wondering being a wavy edge plus a wider kerf will also stop it from cutting very straight. Presumably they make them like that to stop them from jamming, but I'm thinking that if I remember to lubricate (with nose grease or whatever) may I would be better off without the wavy edge...
J
Edited By John Smith 47 on 01/11/2021 22:25:50 |
01/11/2021 14:48:01 |
Posted by Roger Woollett on 01/11/2021 14:31:58:
When curtting a straight line with a piercing saw I find it easier to tilt the blade away from me rather than have it vertical. This puts more teeth in contact and makes it easier to sight along the line you are following.
If you do need more depth fretsaw frames will take piecing saw blades. A lubricant helps, jewellers use candle wax and I find trefolex good on steel.
Yes, good idea about cutting at an angle. That should help slightly at least.
...But what I fear what I really want is need is something fine-toothed that isn't a piercing saw!
That's a good thought re lubricant. Trefolex looks slightly expensive but I have some Rocol RTD Compound, maybe that will work just as well... (??)

J
PS Meanwhile I have bought some new hacksaw blades ("Eclipse 71-132R Junior Hacksaw Blades 32tpi" ) to practise further with...

Edited By John Smith 47 on 01/11/2021 14:53:14
Edited By John Smith 47 on 01/11/2021 14:53:57 |
01/11/2021 14:27:08 |
Posted by Dave S on 01/11/2021 14:05:48:
The simple answer is you need more practice.
I’ve never seen deeper jewellers saw blades.
I have had better results on stainless with Platinum King blades than with Super Pike ones.
Dave
Possibly!
Where do you get yours - esp if you need them in a hurry?
J
|
01/11/2021 14:20:31 |
Posted by David George 1 on 01/11/2021 13:53:52:
Have a look at a fret saw or a deep throat jewellers saw. Cooksongold or others.
DescriptionEclipse Fret Saw 70-FS1R
Adjustable Saw Frame 6" Deep
Metal frame with wooden handle. Depth of frame = 6". Maximum cutting depth = 6"/150mm (due to depth of frame). Adjustable in the direction of the blade - loosen screw, slide arm along to required position, tighten screw. (Useful for re-using broken blades!) Holds saw blades up to 150mm in length. To fit blade: Loosen the screws, insert the blade ensuring the teeth are pointing towards the handle and facing away from the frame. Tighten one screw, then push the frame against the bench and tighten the other screw, keeping the frame under pressure. The blade will be held taut in the frame. Other adjustable models available: 999 735, 999 73B and 999 3059 (3" frame depth), 999 736 (4", 999 737 (5". For 3" Fixed Saw Frames see 999 73A & 734. For Piercing Blades see 972 010-110. Never use pliers to tighten the nuts on the frame as this will damage the screw thread.
Edited By David George 1 on 01/11/2021 13:57:08
Edited By David George 1 on 01/11/2021 13:58:00
Sorry I think I wasn't clear enough... I think I need the blade itself to be deeper (in the direction away from the blades). I have a metal frame with a 5" clearance which is ample for me...
Meanwhile I think shall buy some more fine-toothed hacksaw blades from 'junior' sized (150mm) hacksaw. Maybe I need to find a higher quality make of blades... any specific recommendations?
With thanks
J
|
01/11/2021 13:38:25 |
Hello
I am finding it hard to cut thin metal sheets of stainless steel (aprox 0.6mm to 0.8mm) accurately, when cutting by hand.
I have tried using both a full-sized (30cm) and a junior sized (150mm) hacksaw with fine-toothed blades (32 TPI)

But I find it very easy for my cut to stray by 1+ mm.
I have had better luck using Super Pike Swiss Saw Blade
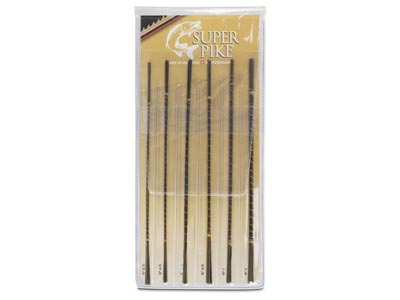
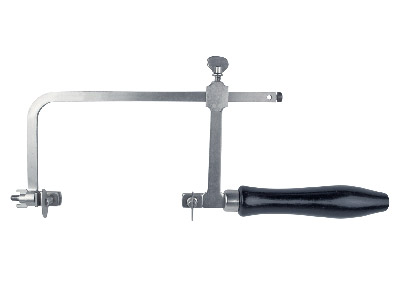
...which make a very fine cut (0.30-0.65mm) and have up to 30 to 16 teeth per cm [not inch!]. And with care good accuracy is possible, but there is very little 'depth' to the blade s(in the direction away from teeth) and this makes a cut difficult to keep straight, (even though it also makes it easy to correct!).
Any tips/suggestions?
- Do they make deeper blades for jewellers saws?
- Do they make hacksaws with a higher number of teeth than 32 TPI?
With thanks
J
|
Thread: From where I might be able to source some 1300 micron (1.3mm) mild steel sheet? |
30/10/2021 02:05:14 |
Posted by John Haine on 28/10/2021 10:14:36:
Posted by John Smith 47 on 26/10/2021 18:40:31:
.....
In my experience everyone thinks that they understand magnetics but is an extremely hard subject.
It turns out that in practice (magnetic) "Permeability" is almost irrelevant and the only number that really matters for magnetic latches using permanent magnets is the (magnetic) "Saturation Flux Density".
Nobody will tell you this, but my understanding is that (roughly speaking) Permeability is how easily a material can start to be magnetised by a weak magnetic field, but Saturation Flux Density is how much you can magnetise a material... and it's the latter that matters most in practice!
....
Hmmm. How close you can get to saturation depends on the flux density produced by a given magnetic field, and so on the permeability. So for the unmagnetized polepiece of a latch you want a material that has high permeability but also a reasonable saturation flux density, but low remanence so it doesn't itself get magnetised. There's a distinction between field and flux, which roughly speaking correspond to voltage and current. But in the end mild steel is probably a reasonable compromise and for most simple magnetic devices is as good as you need.
**LINK**
Permeability vs Flux Saturation Density
I notice your link fails to even mention Mild Steel.
Well, when I first researched this topic, I thought sounded like it would be all about (magnetic) Permeability. And the Permeability numbers certainly vary dramatically, as your link demonstrates.
If you also think Carbon Steel is close enough to Mild Steel, think again because Ferritic Stainless Steel has a much higher Relative Permeability. "100" plays "1000 – 1800"...
i.e. If it was all about permeability Ferritic Stainless Still would have at least x10 the magnetic pull compared to Carbon Steel (and you might thought Mild Steel). But we know that if anything it's the other way around!
[See how "tricky" this topic is!]
The fact is that in practice, when using standard modern high-strength neodymium magnets, it turns out that the saturation flux density is vastly more important than Permeability. For example in my experiments both in FEMM and in the real world, a Ferritic Stainless Steel will have c. 30% to 40% LESS magnetic pull than Mild Steel has.
And in this regard the best ferromagnetic steels available don't perform all that much better than mild steel. From memory the uplift in magnetic pull was only something like +30% or +40% (??) and meanwhile the costs started to escalate.
"magnetic field" and "magnetic flux"
TBH, I never did feel that I 100% understood the difference between "magnetic field" and "magnetic flux". I think magnetic field can be thought of as the strength (i.e. total energy) of a magnet, whereas the flux is how concentrated those lines of force are within a specific area.
Remanence
My thinking is that I don't care about remanence AT ALL. The latches are not being turned on/off electrically. In fact they are using permanent magnets and simply use physical separation. i.e. The are very similar to how a magnetic kitchen/wardrobe door closure 'sandwich' works.
i.e. When the door is open the magnetic sandwich is far enough from the steel that they close on to as to not have any tendency to close the door. i.e. If the steels within the 'sandwich' stay magnetised that isn't a problem. Likewise if the steel that meets them stays magnetised (by them) that sounds fine to me too. So unless any remanence is fighting the magnet, I think I can forget about it.
One thing I have noticed is that even though when you separate the steel from the magnets, the steel do not stay significantly magnetised, if you leave the magnets in place for a few seconds the magnetic pull SEEMS to gradually get quite a lot stronger in a matter of say a few seconds. This may be some kind off illusion I'm not sure, but I as far as I can tell it doesn't appear to be caused by the magnets slowly moving closer to each other. Either way if the magnetic pull is good enough immediately and if it gets say twice as strong in a few seconds that's fine by me.
But the main point is that my magnetic assemblies work really well which is all I really need to know!
|
Thread: How can I make an accurate 90° grind using a diamond whetstone? |
30/10/2021 00:39:52 |
Posted by Michael Gilligan on 29/10/2021 16:32:05:
Posted by Howard Lewis on 29/10/2021 16:06:36:
Be wary of using terms like "Absolutely flat"
[…]
.
Very wise words, Howard
… especially, perhaps, if one has a patent specification in mind.
MichaelG.
Yes, fair cop.
Try "I need it to be as flat as I can get it as within a reasonable period of time and at a reasonable cost."
The point being that in the early stages of developing a novel concept, it's often not remotely clear what the tolerances will prove to be.
e.g. When I recently outsourced some work the engineers quite rightly asked what tolerances I needed it made to. So I asked "What tolerances do you normally work to without breaking sweat?"
The answer came back as "0.2mm"
So I said "OK, do that".
Edited By John Smith 47 on 30/10/2021 00:50:54 |
28/10/2021 23:12:28 |
Posted by JasonB on 28/10/2021 21:02:01:
Water works just as well to keep the surface from clogging but best not used dry particularly on softer metals and even more so when using the finer grades
Opinions seem to vary on that one. The Trend lapping fluid that I use does seems to get very good reviews overall, with a number of users saying that it actually improves cutting performance through lubrication and also avoids any theoretically possible risk of rust.
To get clear, obviously don't use the diamond hone if there is a lot to come off. For filing by hand, I have two sets of superb Bahco Engineers Files, one course set and one fine. The course is bit of a beast that takes a LOT of metal off really fast even after a history of quite a lot of rough use on random hard metals.
They weren't cheap but they are absolutely superb.
If I have the big heavy disk/belt sanding machine, then that is both more accurate in terms of angle and faster than hand files, although for small parts I have taken to regularly dipping them in water to keep the heat down to avoid burnt fingers. In my experience, were the sanding machine falls down is when a longer dead-flat surface is required.
But either which way, if I need an absolutely flat finish - which I sometimes definitely do - I still need to finish off using the fine side of my diamond hone, (which from memory is Sharpal 325+1200).
==> Hence this thread.
|
28/10/2021 20:46:25 |
Much appreciated, Jason.
Peak4 - Wow, "Woodworker's Shooting Board" is a genius concept. Yes very clever indeed, particularly the way it hooks onto the bench to stay in place and how the plane doesn't cut into the supporting structures. Thank you so much for pointing it out to me.
In my case, given the way that my diamond hone's diamonds go right tot the edges, as you say, I'd need to find a way to create a running surface in addition to to holding the hone vertical.
Fwiw, by way of fine-tuning, I suspect that think one would need a small trench so that the filings don't start to get in the way.
Many thanks 
J
P.S. On reflection my slight concern is that the diamond hone seems to work much better with some lapping fluid on it, as this helps to stop the diamonds from getting clogged up with grindings.
There again, maybe if the hone is being held vertically on its side then to some extend gravity becomes one's friend and would help to pull them away, and the hone might work okay dry... What think you? [As I'm quite keen to not destroy my rather valuable diamond hone just yet!]
|
28/10/2021 17:45:39 |
> I wish you good luck with your project
Thank you.
>>>
...but based on what I have gleaned from the various threads I would say its doomed to failure. I'm not trying to depress you or dissuade you from continuing but the reality is that to get the project to a state where it is protected by patent you will need to invest quite a lot of money (say compared with the tools and machines you have mentioned).
>>>
Wrong. Like I have already said, several times in fact, this is well in hand and has already been done. [Shesh!]
Ian P, in the nicest possible way, I think your all of your strategic advise is doomed to failure.
>>>
One observation, as you say the magnetic attraction between two parts can be seriously reduced if the parts do not fit together well and it sounds like its the 1mm wide face that is one of the abutting surfaces, It would need seriously strong magnetic force for your metal strip to stay at 90 degrees if whatever is attached to it is going to do anything useful.
>>>
Wrong again. The magnets work absolutely perfectly. I'm actually serious.
Now, if you no further suggestions on the topic "How can I make an accurate 90° grind using a diamond whetstone" please stop.
|
28/10/2021 16:14:23 |
Posted by John Haine on 28/10/2021 15:54:40:
I give up. Some people just can't be helped.
There we agree.
|
28/10/2021 15:12:43 |
John H
On the face of it your Makespace is a good one. Yes, I had been using them, however as you know it is crucial that I am not seen to disclose what I am doing in any public form or further patent claims & sub-claims will not be possible. Either way I have not been using them since the Covid-19 pandemic and with 1 million people infected with Covid right now, now is not the time to start.
Yes I have done multiple prior art searches and yes, I have filed patent claims.
But do I REALLY have to answer all your invasive questions?
Look is it too much to ask for you folks to just confine yourself to answering the simple questions that I have raised?
Why does everyone keep trying to re-design my product for me?
PLEASE just let me dig my own grave, if that's what you think I'm doing... but please can everyone keep their self-righteous egos out of my designs.
If, unprompted, you do choose to make design suggestions, that's up to you and in general I am grateful but the down-side is absolutely no way can I go into details about the reasons for my design decisions. So if that's frustrating please do NOT make design suggestions.
Nicholas Wheeler
Sorry Nick offensive as your personal attacks are, you simply have no idea what you are talking about and it would take too long to correct you. Yes I have done a lot of outsourcing where appropriate.
No, straight of the guillotine bends the plate. It curls on one side and rounds the edge on the other. We all know this. So why am I wasting my breath?
You don't sound like you have much if any experience of fine tolerance and strong magnets. Because if you did you would know that in practice, unbelievably small machining errors can easily cause a x2 change in magnet pull.
Final words
Okay that's it. No more person attacks, please. And no more re-design suggestions, please. If you don't enjoy reading threads that I have started... if you still want to make your personal attacks, if you still want to offer what is completely unsolicited re-design advice PLEASE GO AWAY.
Please can we all just stick to the materials, tools, technology and techniques... and stick to the topics in the actual question!
|
Thread: What spray do you use to stop your tools from rusting? |
28/10/2021 14:30:05 |
Temperatures
Yes everything you say makes perfect sense. i.e. Simply put, temperature gradients are the enemy.
It has been a great surprise to me that my tools kept outside in all weathers and within 2 layers of plastic boxing ,that is deliberately NOT gas-tight, has NOT resulted in any significant rusting of my tools, irrespective of weather conditions throughout the year.
My one slight problem is that in winter if I bring very cold tool indoors, then condensation will immediately form... So once needs a nice warm workshop to warm them up quickly and once they are the temperature of the room, dry off at a reasonable speed.
I also have a fan heater which I sometimes apply to help bring the tools up to the room temperature quickly.
Sweat
Rust from sweat is an altogether different problem and can occur even when everything is at the same temperature and there is no water in sight. This is caused by the salt which is hydroscopic - i.e. it drags water out of the air. AFAIK the amount of salt in your sweat isn't really about age, it depends primarily on how much salt you eat in your diet. (think: bread, crisps, salted peanuts, breakfast cereals, soya sauce, marmite etc).
In my case both indoors and outdoors tools have suffered slightly from fingerprints. (Too many crisps!)
|
28/10/2021 13:14:19 |
Posted by Russell Eberhardt on 28/10/2021 09:40:41:
When I was doing metalwork at school we were taught to put two drops of machine oil on our hands and rub it in as soon as we entered the workshop. I still do that and never put any oil to protect the metal except on moving parts. Never have any rust problem.
Russell
Machine oil on hands
I'm sure that would work, however I have to ask - how is your health?
The reason I ask is that it is thought that in general at least 60% (maybe 64%) of everything you put onto your skin is absorbed into your blood stream. This is a monumental and seldom talked about problem. e.g. Facecreams & hand creams that seem to get absorbed... where else do you think they go? For example it turns out that the mild from (human) mother's is often heaving with what is effectively suntan lotion, that has been stored in the mother's fat cells.
I don't know about machine oil in particular, but I would strongly caution against putting anything that is not broadly edible onto your skin.
Renaissance Wax
This sounds interesting. Why did you start using Renaissance Wax in particular? It sounds like museums use it... Is this a known thing that lots of people in workshops do or did you come up with the idea for yourself?
The was has quite a high melting point 75 to 80C, but maybe there is just enough creep to seal any molecular-sized cracks that might from in the wax to keep H2O and O2 at bay. Once it gets very old does it start to harden/flake off at all?
Also what form do you apply Renaissance Wax in - Can you obtain it in a light easy to apply spray form?
e.g. "Renaissance Metal Decorroder" or just plain "Renaissance Wax" that you buy in a tin and apply with a cloth?
Once the volatiles have "dried off" is the final surface slightly slippy (like that of say a candle)?
Have any of you tried both Boeshield T-9 and Renaissance Wax? How do they compare in practice?
|
28/10/2021 01:30:54 |
Posted by Pete. on 28/10/2021 00:33:11:
That said, I often spend time in the West Highlands of Scotland and in my experience for any steel product where rust has already started to penetrated the paintwork... when it is going to be lashed with wind-driven salty rain, my bet is that none of the above would last 6 months!
Edited By John Smith 47 on 27/10/2021 23:29:35
Could you explain exactly what you need protecting from corrosion, I read the opening post and got the idea it was for small hand tools, now you're talking about paintwork and salty wind driven rain making me think Land rover off roading in Scotland, what are you trying to achieve?
Me culpa please ignore the stuff about Scotland. Just an aside. No, I am looking for a fluid/spray to apply to my steel tools to stop them from rusting when they are are kept either indoors, or kept inside 2 layers of plastic boxing out of doors.... in a rather damp, but otherwise civilised valley in England.
|
Thread: From where I might be able to source some 1300 micron (1.3mm) mild steel sheet? |
28/10/2021 01:23:11 |
Posted by Dave S on 26/10/2021 19:51:09:
I’m not sure I agree with “Tricky Stuff”.
Possibly “narrow specialism, niche application stuff”
Magnetic properties of materials is a specific area of materials science, and a well studied one at that.
The information is available, it’s just not actually that critical to most applications.
Dave
You could probably say the exact same thing about doing surgery on the human brain or about sending a rocket to the moon. In fact.. just a wild guess, Dave, but... maybe you do! ;^P
J
|
Thread: How can I make an accurate 90° grind using a diamond whetstone? |
28/10/2021 01:08:45 |
Posted by Jon Lawes on 27/10/2021 20:32:47:
What is this for? Is it a commercial enterprise?
I guess that's a reasonable question, since this is a 'hobbyist' forum.
Look, I'm not remotely 'commercial' because I'm doing this project with VERY little money.
I am working in my own shared rented home... and (compared to other members of this forum) I freely admit to definitely being a 'workshop novice'. I am working with very limited funds, and without a dedicated workshop space. I am developing an inventive (patent pending) concept for a novel product. I have only strictly limited personal funds... and raising funds is difficult & extremely expensive as I do not yet have a proven track-record at doing this. So I don't have much money.
Nonetheless my concepts have been well received and I now have introductions to senior management at several of the largest manufacturers in the world of office suppliers/stationery sector, but I MUST have credible prototypes, and I need to make them on a shoestring budget. No, I am not planning to do any actual 'manufacturing' myself, but in line with modern "Lean Startup" thinking, I need to 'iterate' and do quick turnaround physical testing of concepts on users. But... I don't have much money. The intent is to generate "looks like, works like" models of the proposed product with which I can prove that the product(s) can, in principle at least, be manufactured in both A. small and B. in larger scale/mass production, and thereby make a compelling proposition to target licensees. But... did I mention that I don't have much money?
Yes, the intent is to become 'commercial' some day... however the funding is emphatically at the 'hobbyist' level!
Edited By John Smith 47 on 28/10/2021 01:14:32 |
Thread: What spray do you use to stop your tools from rusting? |
27/10/2021 23:28:48 |
I've had a quick look at Ballistol, ACF-50 and Boesheild T-9. They all sound quite compelling.
In truth it sounds like there are a fair number of fine oils that one could use that would stop corrosion quite well in a workshop situation. However I don't like the idea of something which stays sticky, attracts dirt and gets basically everywhere.
Ballistol
I may be incorrect but Ballistol Universal Oil sounds like even after it has been applied as a thin film that it stays liquid. It also claims to create "an alkaline film" which helps stops corrosion from hand sweat. Intriguingly they claim that it is "widely used in the precision gauge and tool industry".
ACF-50
From what I have read, ACF-50 also stays liquid. This is good because it will work well at getting into the finest, molecular-sized cracks and driving out water.
The manufacturers say: "On new metal ACF-50 forms a self-healing barrier that prevents corrosion from starting. ACF-50 remains physically and chemically effective for up to two years."
However by staying liquid this it is bad because it may prove to be slightly sticky.
Worse, they seem to be saying that ACF-50 is also working chemically and for this reason it does need to be reapplied every year.
Boesheild T-9
From what the manufacturers are saying Boeshield T-9 does sound slightly different in that they say that it "dries to a waxy, waterproof finish without leaving a sticky film to attract dirt, dust or mud." and "T-9 dries to a clean, waxy, waterproof film that won’t wash off in rain, puddles or mud."
Tricky.... At the moment, for indoor use and well-box outdoor use, I am leaning towards, Boesheild T-9 - in fact I have just bought a small sample. And yes, my more delicate / precious tools are staying firmly indoors.
My thinking is that if something stays significantly liquid it's hard to imagine that it won't come off on your fingers and basically get everywhere, whereas a waxy finish may not.
That said, I often spend time in the West Highlands of Scotland and in my experience for any steel product where rust has already started to penetrated the paintwork... when it is going to be lashed with wind-driven salty rain, my bet is that none of the above would last 6 months!
Edited By John Smith 47 on 27/10/2021 23:29:35 |