Thread: Calculating Mount Point Speeds |
25/02/2022 12:19:14 |
Google grinding pin speed there are plenty of examples out there
giving wheel diameter to rpm and metres /sec
like this one below
http://www.denchong.com/E/body.php?web=14&PNo=2007110150
John
|
Thread: Delapena External Hones |
20/02/2022 13:44:31 |
Have a look on Ali*****ss probably thousands of choices grits up to 3200# for these type of stones can't give any reference numbers on here as they will be taken down almost instantly.
John
|
Thread: Neat cutting oil. (recommendation) |
17/02/2022 12:15:50 |
Posted by Richard Brickwood 17/02/2022 10:12:47
Regrettably Morrisons now only sell CoraB in 25 litre or 250L quantities. 25L is ~£160+VAT - which is
a bit much for me in both quantity and price. Anybody got any suggestions for an
alternative? Many thanks.
There are some cheaper alternatives i use Exelcut 401 for most all machining works well
on aluminium brass and cast iron , Exelcut 433 is used for cylindrical grinding .
J&L MSC sell it , these here sell Exelcut 432 and seem to be a bit cheaper
than some others and free delivery ,there are plenty of others
that seem to sell this ,just Google around.
https://www.lubetechshop.co.uk/product/excelcut-432-quantity-25-litresheavy-duty-chlorinated-oil/
John
|
Thread: Drain cleaning brushes |
12/02/2022 10:40:53 |
Posted by Robert Dodds 11/02/2022 21:20:21
Oh for the days of coal fires and a Flue Brush.
Bob D
Happy Days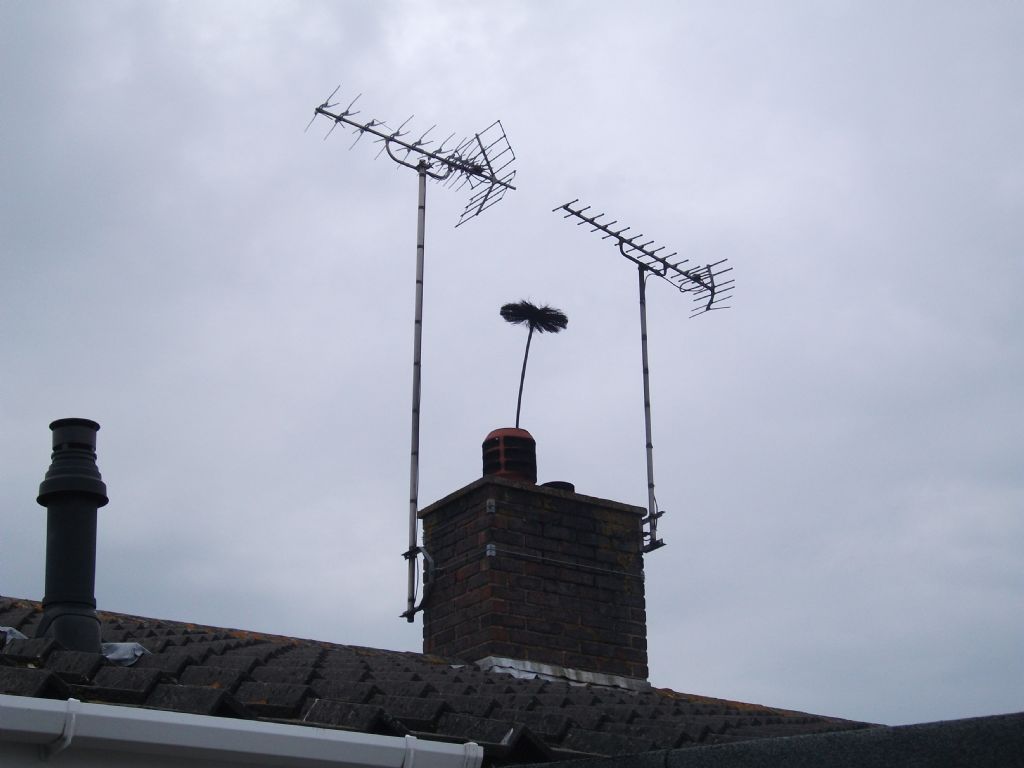
|
Thread: I am getting shorter - how about you. |
08/02/2022 16:49:00 |
Does it really matter, so long as your feet still reach the floor.
John
|
Thread: Gear cutters for clock wheels |
08/02/2022 12:37:42 |
Posted by Jouke van der Veen 07/02/2022 22:35:10
Hallo John,
I think you are right. On the other hand I think an Eureka device is a step to far for me.
I preshaped the gear cutter with a “standard” cutting tool in 8 steps to a tooth thickness
of (approx.) 1.7mm.Then I changed over to the radius tool and needed again
8 steps, of course, to reach the final thickness of 1.57mm
With this method I had to repostion the gear cutter on the excentric mandrel
several times.It was my second trial. I started with a M1.27 in mild steel with
a less precise result. The second trial was the M1.0 shown in this topic. I am
convinced that I can do better. But remember, I have to do this on an Emco Compact 5.
How accurate should tooth thickness be?
Regards, Jouke
A lot of your problems can be resolved by boring and facing one side
of the cutter blank and marking that side and later on using this side
as the datum for mounting the blank of the finished cutter on the arbor.
The other side of the blank must be parallel to the datum side to
0.00 or as close as.
Secondly a two button tool will automatically give a constant width
on all of the cutting teeth. Referring back to the photo in my previous post
these 2 button tools some have parallel turned buttons that are hardened
and then loctited into the holder,in the absence of a dro system a cheap
clock gauge about £10 from China can easily be set up to give the
required spacing, a metric clock gauge reading in .01 can be easily
read to subdivide that to half or quarters.
The holder seen here is the one in the book Gears and gear cutting
and the clearance is provided by the 5 deg angle on the front.
The only problem that you face then is the minimum spindle speed
of your lathe which seems to be around 200 rpm ,to cut silver steel
with hardened silver steel tooling at the diameter that you have you would
need to be below 50 rpm , if you are unable to make adjustment to the
machine to get down to these speeds the next best thing is to
use a mandrel handle.Coating the tooling and cutter blank with RTD
will make it a lot easier.
John
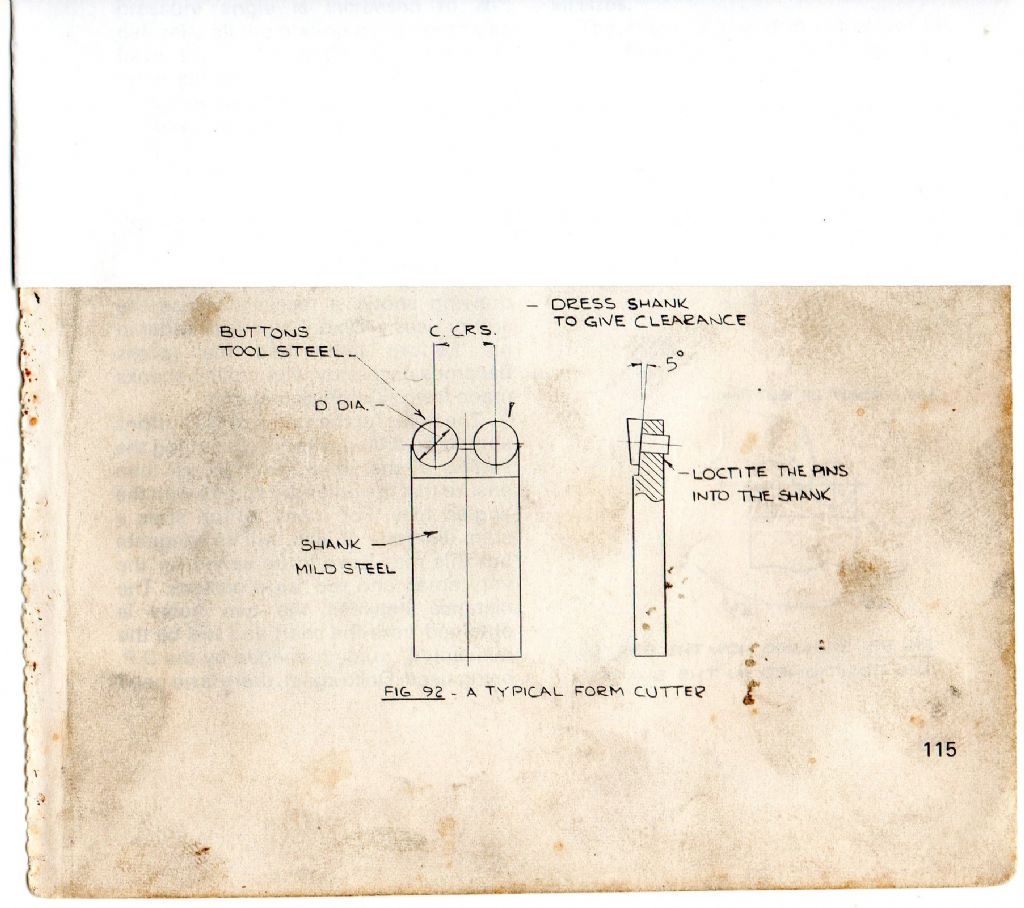
|
07/02/2022 22:09:07 |
Posted by Jouke van der Veen 07/02/2022 21:42:17
Dear forum members,
Could you have a look at my album “Radius tool for gear cutter”?
I am open for comments and suggestions.
Accuracy of tooth thickness of gear cutter has to be improved, at least.
Regards,
Jouke
Varying tooth thickness ,cause the sides of the cutter blank not
parallel.
Build a Eureka device and or make a two button tool
to cut both sides of the gear cutter at the same time.
John
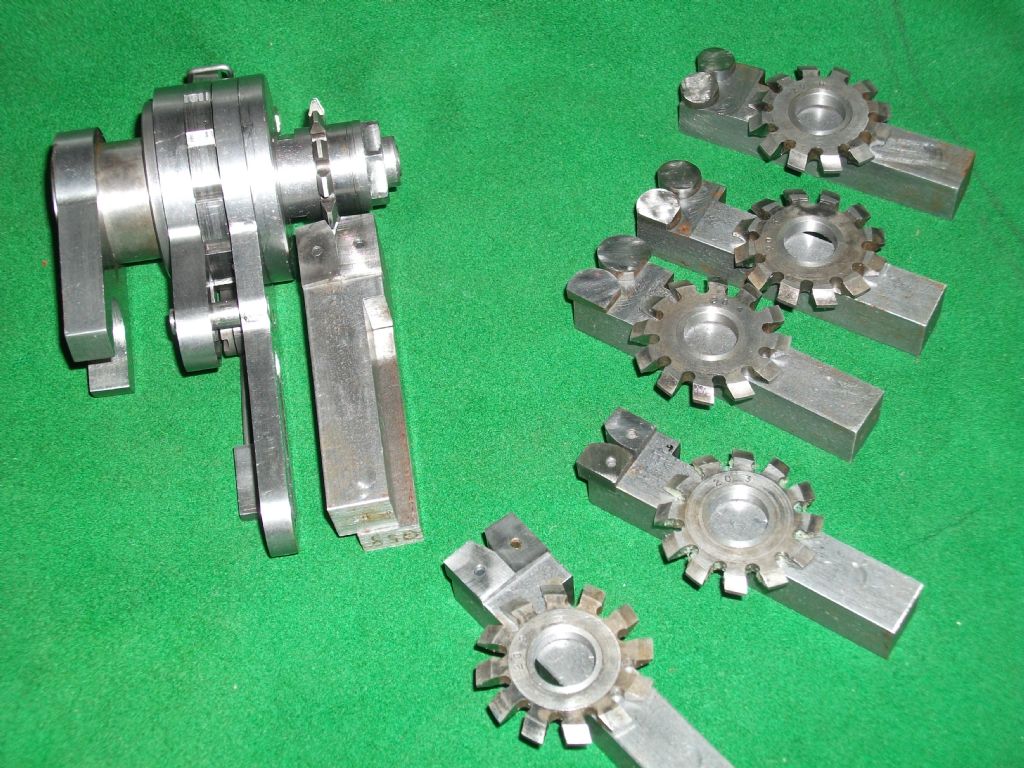
|
Thread: Four Index Thread Indicator |
06/02/2022 20:55:36 |
Pete ,
You need to read the full article it covers all the pitches.
John
|
06/02/2022 19:16:59 |
Hi Franco,
i have sent you a PM .
The article shows all of the information required ,Unfortunately you have the disadvantage in having a screw cutting gearbox ,i think there is lash up arrangement using 33 and 34 tooth gears which is not as good as a true 127 for imperial to metric conversion ,this would work for you if you could fit in a 127 gear some ware in the gear train ,i have a change wheel machine and find that is far better than a boxed machine.
John
|
06/02/2022 17:16:36 |
This is the article i referred to in the the posting at 05/02/2022 22:11:28.
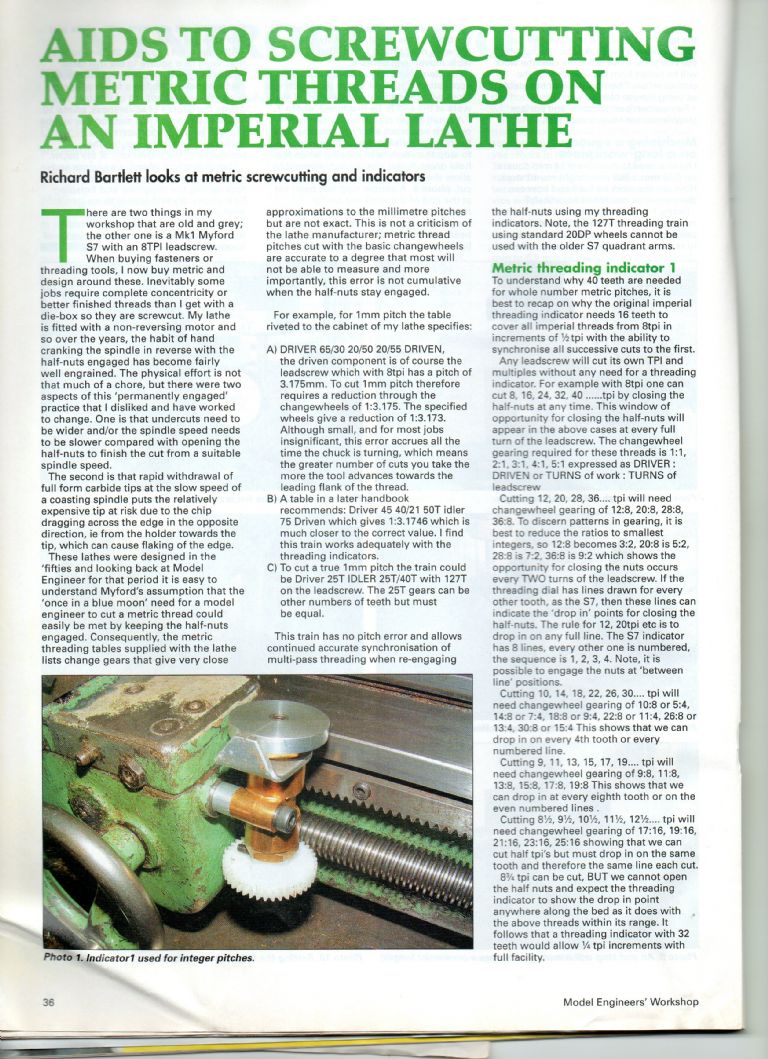
Using this method allows the motor to remain running ,the spindle
can be left turning ,the half nut are dis-engaged at the end of the
pass the carriage returned to the start position ready for the next pass.
To get the best use from this a true 127 gear for metric conversion
must be used.
The article is worth reading and covers all of the points the OP
asked for.
I use the same 127/60 tooth gears as in the article,here is
the change wheel list for all the metric pitches.
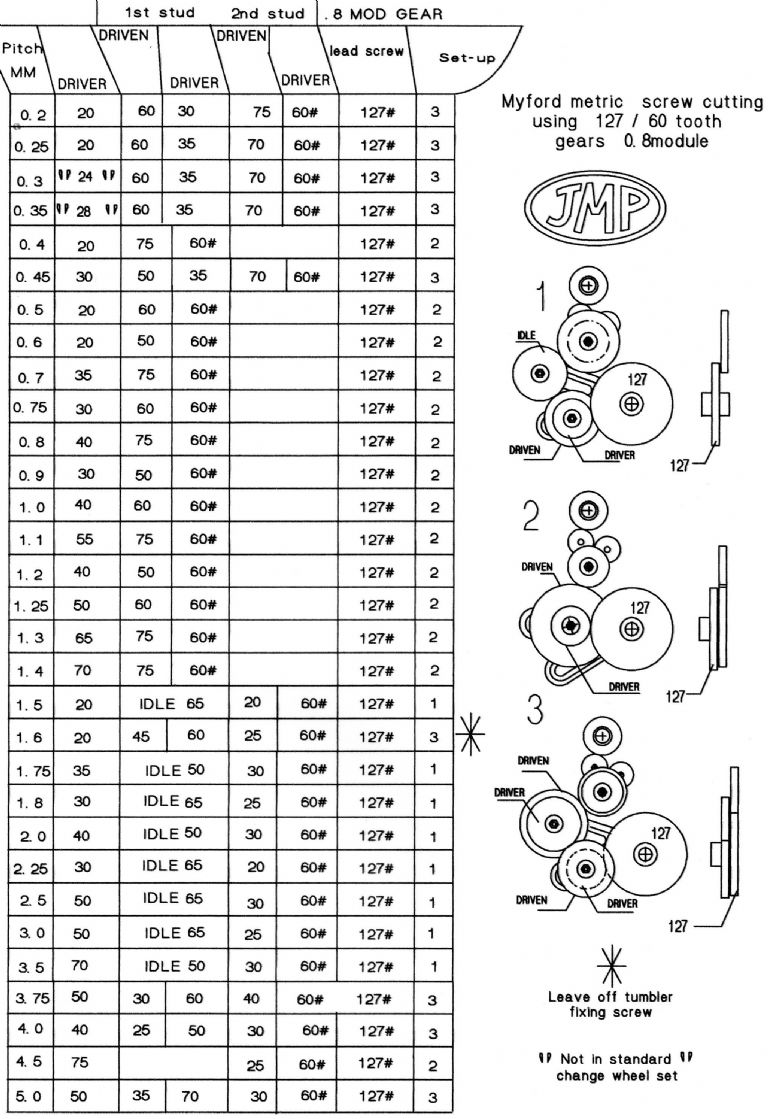
John
|
05/02/2022 22:11:28 |
Posted by Franco Convertini 05/02/2022 17:48:34
On my super 7 when I do imperial threads the Four Index Threads Indicator works well, I can
unhook the carriage from the lead srew and start re-reading again.
This system does not work for metric threads. For each metric thread I
waste a lot of time because for each pass I have to stop the lathe motor, make it
turn backwards until the thread begins and start a new pass.
I wanted to know if there is a dial indicator for metric threads?
Edited By Franco Convertini on 05/02/2022 17:49:11
Yes it can be done,
In MEW 149 an article by Richard Bartlett on
page 36 through to 40 describes a method
for metric screwcutting on a Myford with an 8 Tpi
leadscrew and by dis-engaging the leadscrew.
John
|
Thread: 80mm ARC Versatile or 73mm Precision 3? |
27/11/2021 14:55:54 |
Posted by Thomas Gregory 1 27/11/2021 14:09:28
Oh and whoever mentioned the MSC Advantange brochure, please can you forward me
your contact details so I know where to send my wife when she sees the credit card statment!
Contact me at Neil at My time Media
John Neil
|
27/11/2021 08:37:30 |
Posted by Pete 26/11/2021
Have a look at the thread I started on 'Arc Euro Type 2 vices' someone linked some similar vices on sale at a good price, not sure if if they're still on offer though.
-----------------------------------
They still are, on MSC Advantage December as QGVMP 85220J @ £31.99 and QGVMP 85320K @ £41.99 .
John
|
Thread: Gingery size shaper speeds |
18/11/2021 14:12:13 |
Posted by Bricky 18/11/2021 12:31:24
I couldn't stand to scrap my late friends project of a small shaper,he had 80% finished it ,but
unfortunateley for me he used two sets of plans.There are no gears involved
in his construction and it seems he was relying in the scotch crank driven
I think direct from the motor.I think a lot of reduction will be needed and
advice on the speeds of these small shapers would allow me to work
out the correct pulleys and intermediate pulley for reduction.
Frank
---------------------------------------------------------------
I have a part built shaper of a similar size to the Gingery shaper and
it is based on the Gingery machine.
I changed the drive system to use toothed belts a 5mm htd for the main
drive to the ram and a 1/5 " XL as the primary reduction.
The pulley sizes for the primary reduction are 24 /60 tooth and for the secondary
27/95 tooth.
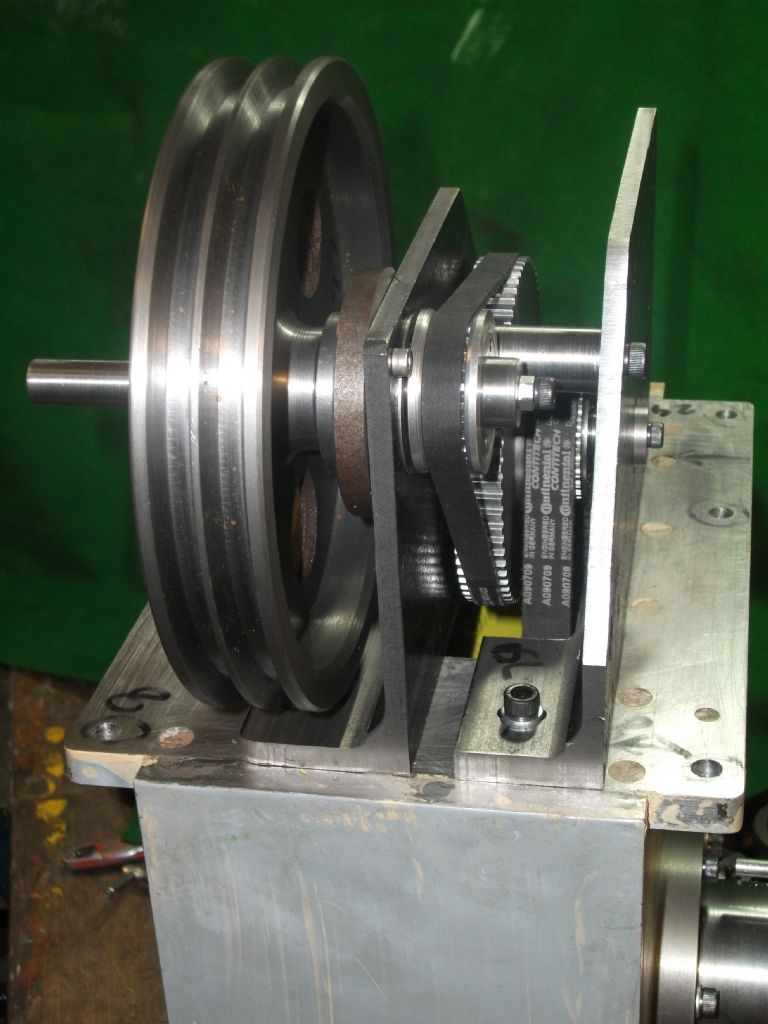
The reduction at the input pulley seen here in the photo is about 9.96:1
with a 1425 rpm motor about 143 strokes /min, a belt reduction from the
motor of 2 to drop to 71 and 3 to 47 .An inverter drive to fill in the gaps.
I know that you will not perhaps have a similar set up but the ratios that
you need will be similar.
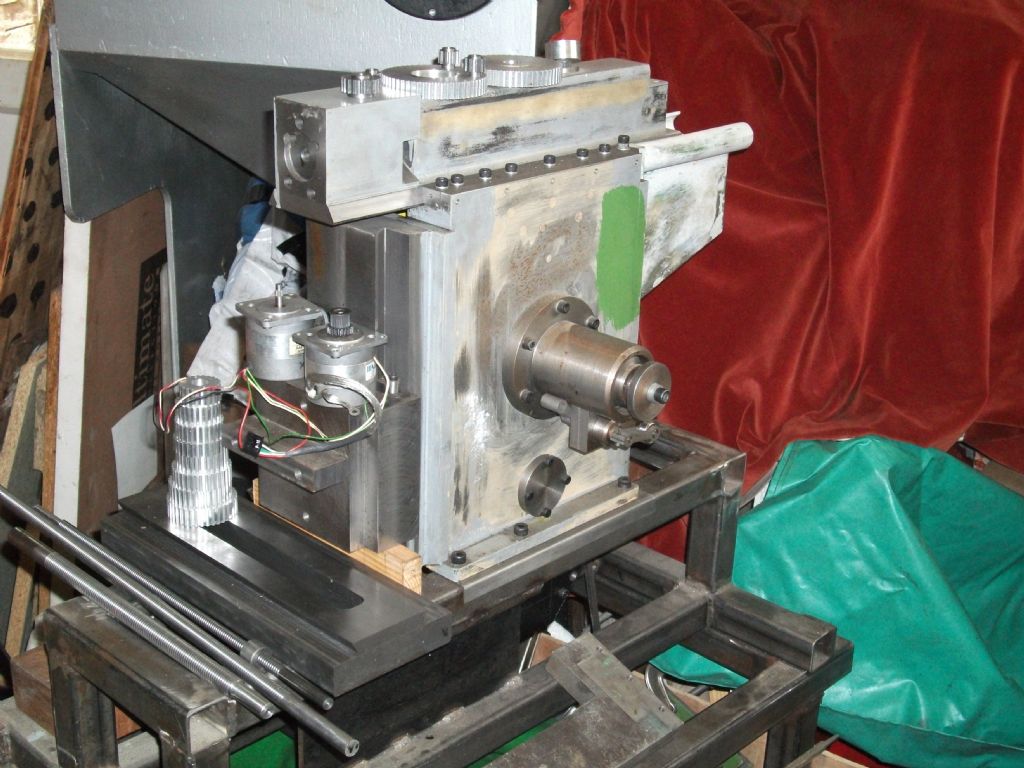
John
|
Thread: Grinding Spindle |
15/11/2021 14:19:43 |
Posted by Mark Rand 15/11/2021 10:33:49
------------------
Posted by John P on 14/11/2021 22:27:02:they are only limited by the drive belt
which gives up due to the centrifugal force flexing the belt as seen here ,the belt
has so much tension it needs some effort to fit over the pulleys but turns into
chewing gum at high speed.
------------------
For future designs, would it be better to use nylon reinforced flat belts? They are
nowhere near as stretchy as the round polyurethane belt.
-------------------------------------------------------
Hi Mark,
Most probably .
Like most things some compromises have to be made,
manufactured belts are fixed sizes and as such what they fit on has
to be designed to make them fit ,that would have caused me somewhat of a
problem as to accommodate the swing up head seen here no adjustment
is possible to tension the belt.
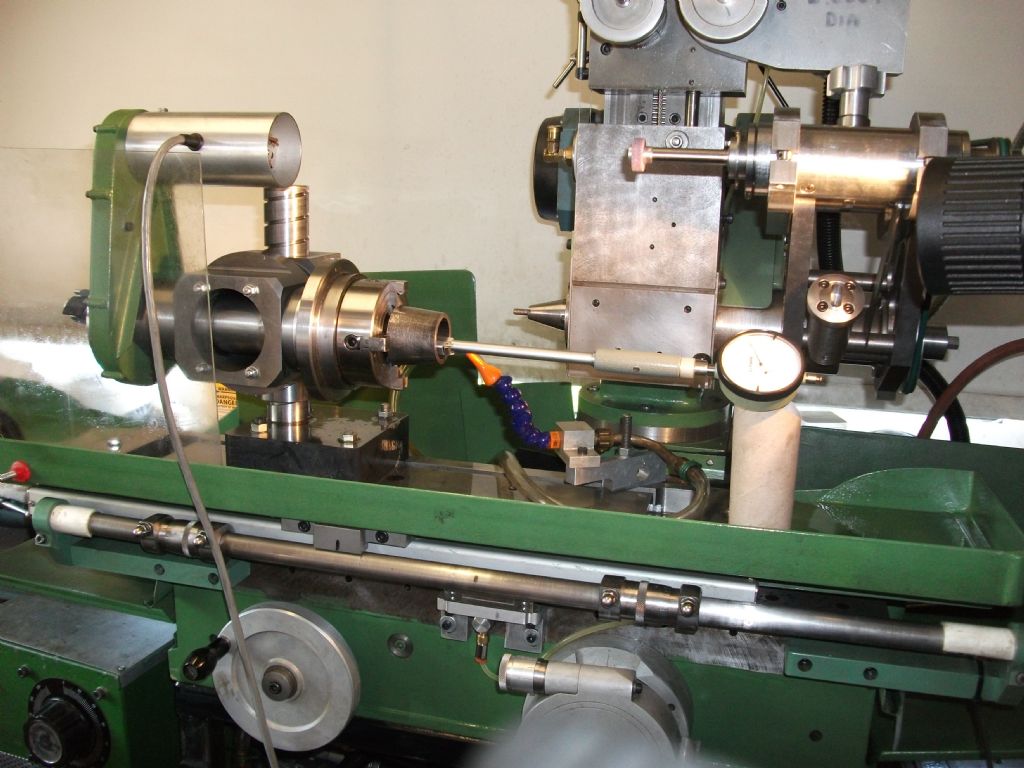
As the spindle has a working speed from about 4,000 to the
31,000 rpm accomplished via belt changes and inverter
regulation additional problems with other fixed belt sizes would undoubtedly
be present, the heat joint belting gets around these complications just by
being able to be made to suit, the inconvenience of the belt flexing
only occurs above the 31,000 rpm which is more than enough for
the internal grinding for which it is designed.
Looking on the lathes web site at some of the past type grinding machines
this machine does rather well in spindle speed terms some examples:-
Crystal lake grinder internal spindle speed 17,500 rpm
Jones and Shipman Universal Grinding spindle 11,600 to 16,200 rpm
Jung internal grinding machine 30,000 rpm
Mipsa Swiss 23,000 rpm
Duplex toolpost spindle 18,000 rpm
Jones and Shipman 36"x 12" 3080 to 33,000 rpm
These are just a few ,i am sure there will be some more ,i guess there is
an upper limit on driving a spindle by belts,it would seem that i am already
up at the top end compared with some of these well made names.
I have an air spindle that runs at around 50,000 rpm for those times
when that this may be needed.Since the machine was originally designed
as a cylindrical grinder and is also a surface grinder along with the
internal facility some inevitable compromises have been made ,it just
what you have to do to build something like this.
John
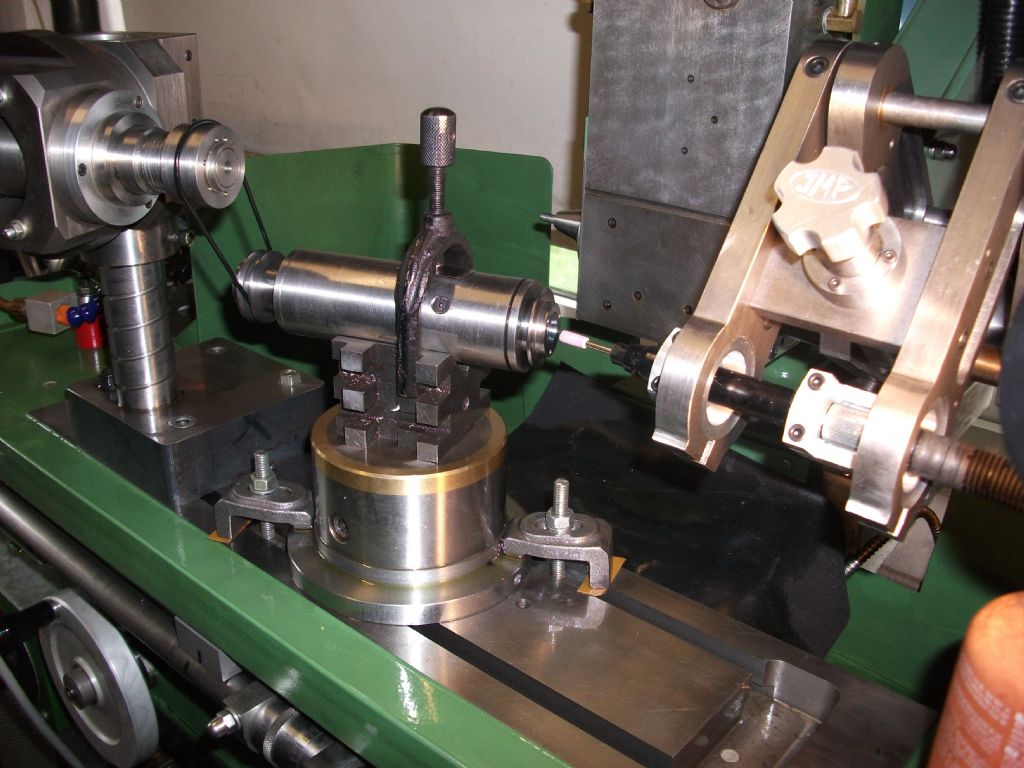
|
14/11/2021 22:27:02 |
Hi John,
I had come to that same conclusion using the disk springs in the way that you describe ,the Quorn spindle is not that demanding , it is lightly loaded and does not run that fast to be a problem ,the 3 spindles seen earlier run to 31,000 rpm they are only limited by the drive belt which gives up due to the centrifugal force flexing the belt as seen here ,the belt has so much tension it needs some effort to fit over the pulleys but turns into chewing gum at high speed.
John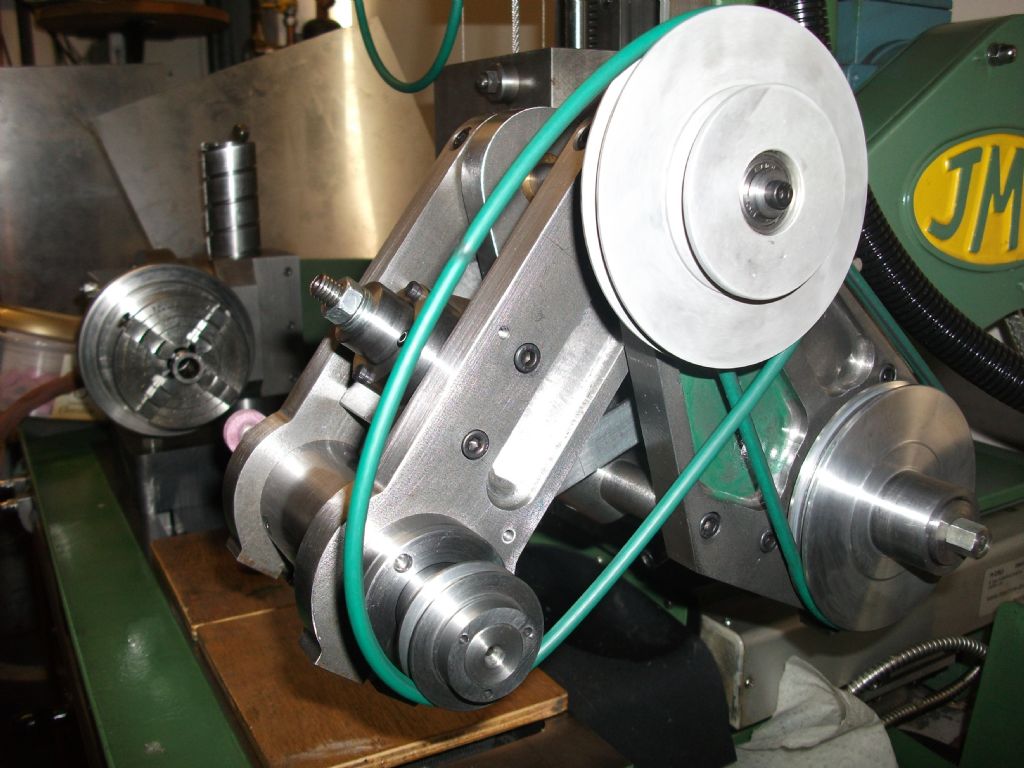
|
14/11/2021 21:13:37 |
Posted by John Purdy 14/11/2021 18:20:18
John
I'm curious as to why you think the spring box arrangement for preloading
the bearings is superior to the disk springs washers. Could you elaborate?
When I built mine I used the disk springs as I felt it would be easier and
produce a more uniform preload. In use it has been perfectly satisfactory,
and I feel was easier to make.
-----------------------------------------------------------------------
Hi John,
I don't think there is any problem with the disk springs being used
for the pre-load on these bearings it is more the way they have been
used directly against the rear bearing ,in this way there is little support
for the bearing, in the D.H. Chaddock design and also most spindle
bearing designs use a sliding sleeve which is sprung loaded against
the bearing outer ring since the sleeve is longer than the bearing
diameter it ensures the outer ring is held square within the spindle body.
The photo of spindles shown earlier are similar to the Chaddock
designed spindles except for all the machining operations are
done at a single setting with no turnaround setting up including all of the
labyrinth seal parts with the exception of the rear end cap retaining
threads in the main spindle body. The spring box length is about 2 x the
bearing diameter ,each of the 3 springs the pressure is set individually
by drilling the holes too deep and dropping in a spacer to set up the
spring pressure .
In the Quorn Universal tool and cutter grinder book Prof Chaddock
makes reference to this very point about the spring box on page 53
in which he writes,
" The other bearing is firmly clamped on the inner ring but the outer ring
is pre-loaded by means of a spring-box .This enables the spring
pressure to be carefully controlled and providing the spring box
has a length approaching its diameter and is a close sliding fit in its
housing ,ensures that the spring pressure is applied squarely to the
outer ring"
The washers as in the Broadley design which has recently been
seen on the Quorn user group website albeit printed in reverse
has none of these features and is entirely reliant on the springs
to ensure this squareness.I suppose another failing with this
arrangement , a spring box is in close contact with the end of the
bearing ring and as such allows a path for some of the heat from
the bearing ring to travel away ,with the cone spring arrangement
there is only a a very small contact area all of the heat has only the
contact of the bearing ring on the outer sleeve.
The OP had asked for an opinion on the the 2 designs of spindle
for his machine. This is perhaps a more detailed response to that
original question.
In any event i suppose he will have to decide this for himself.
John
|
12/11/2021 20:33:18 |
Haven't built the Broadley spindle but looking at the pdf
drawing here " Broadley F.pdf - Home Model Engine Machinist Forum"
I would stick with the original Quorn designed spindle.
The Broadley designed unit is similar to the Quorn design
probably a little easier to make i think the spring box arrangement
of the Quorn is better than the dished washer set up of the Broadly
design.
I built my Quorn spindle to the Chaddock design in the book
35 + years ago never had it apart, still runs quiet and smooth.
There are many ways to make a better spindle that is stiffer that
the Quorn ,these 3 here are slightly larger than the Quorn use only
standard SKF eco bearings 20 lb preload run up to 31,000 rpm
at 65 deg c .
John
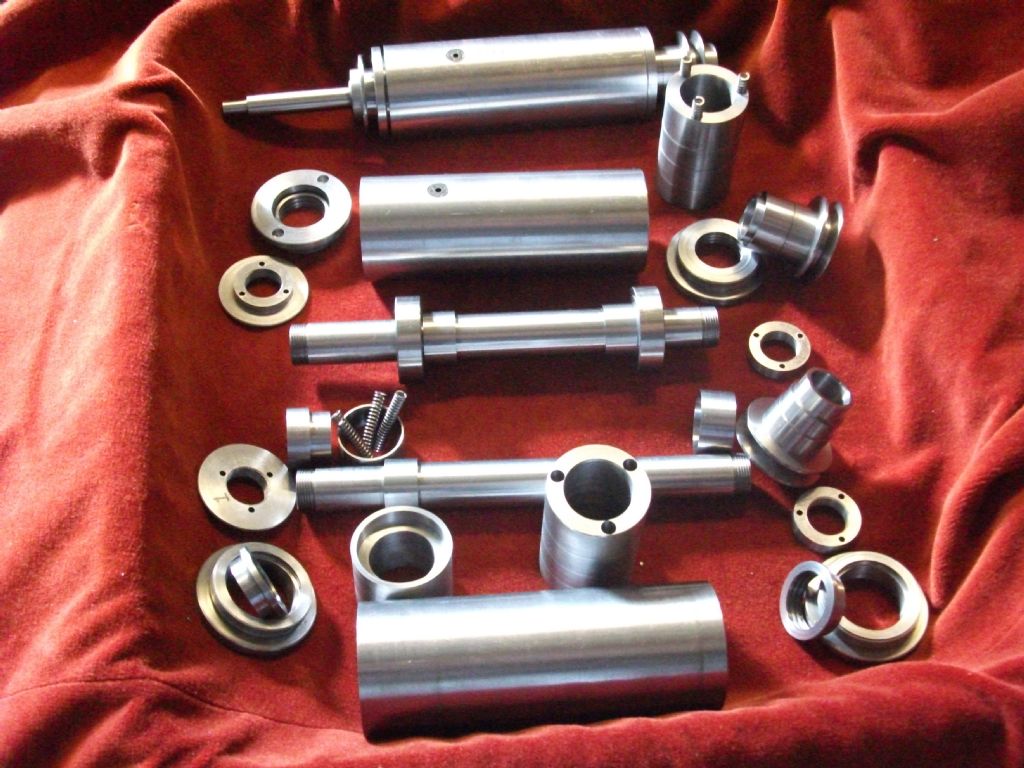
|
Thread: Guillotine |
10/11/2021 14:57:20 |
Posted by john fletcher 1 10/11/2021 14:00:51
Back again folks, the guillotine is one similar to the picture John P posted, thanks for
that John. I would like it to cut ex washing machine, cooker, and fridge sides which
I hack out using my angle grinder, ready for making a cabinets for another WS
projects. John
---------------------------------------------------------------------------------------------------------
I use mine sometimes for recycling old washing machine or tumble drier
sheet metal it cuts it very well.
The formit that i have is the 24" version like all stuff from China it is
made down to a price ,i have had mine since about 2001 and it has been
used regularly ,these things will never be as good as a proper guillotine/box
folder and roller but for the price and the compactness are good value.
Some other photos here shows this mounted on this floor stand which
provides some additional support to the lower blade it was made from
some scrap 4" angle iron welded as a box below the lower blade as
can be seen.
It cuts the full width of 1.2 mm sheet steel and will cut stainless i find it
helps if the blades are smeared with Trefolex, very little curl or distortion
to the work and with care have rolled some 2mm sheet steel about 8 inch wide
into a 25 inch drum.
John
View from front of lower blade the two bolts apply a little pressure to the front of the blade ,the single bolt provides some additional support below the blade.
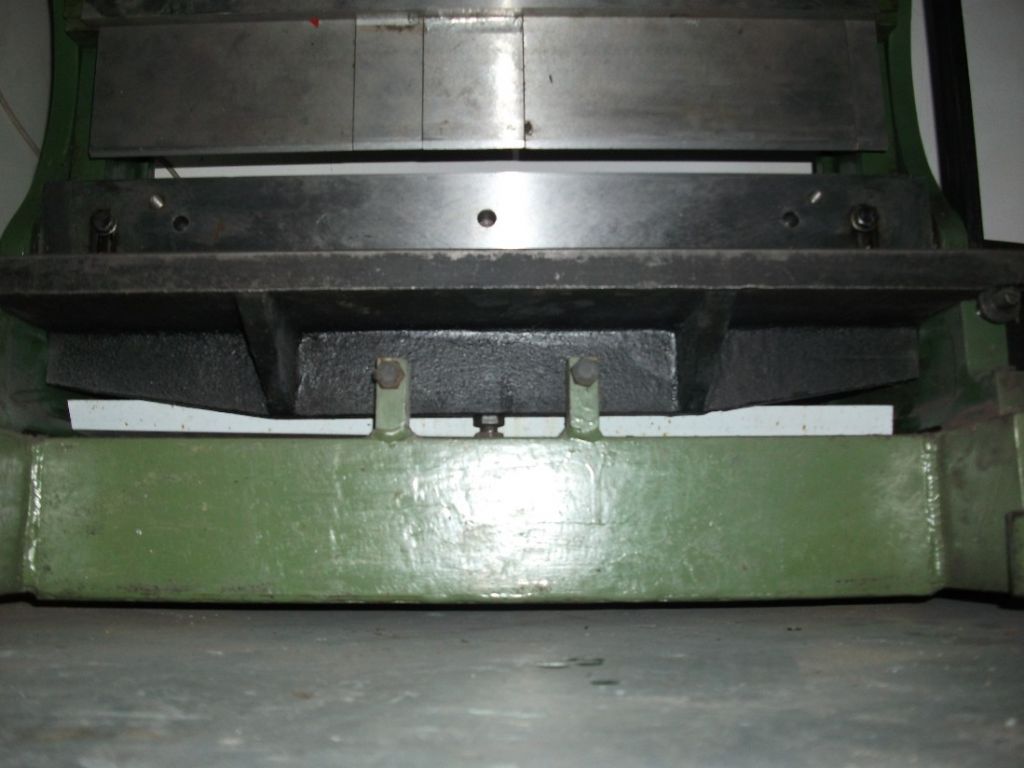
View from the rear of the machine
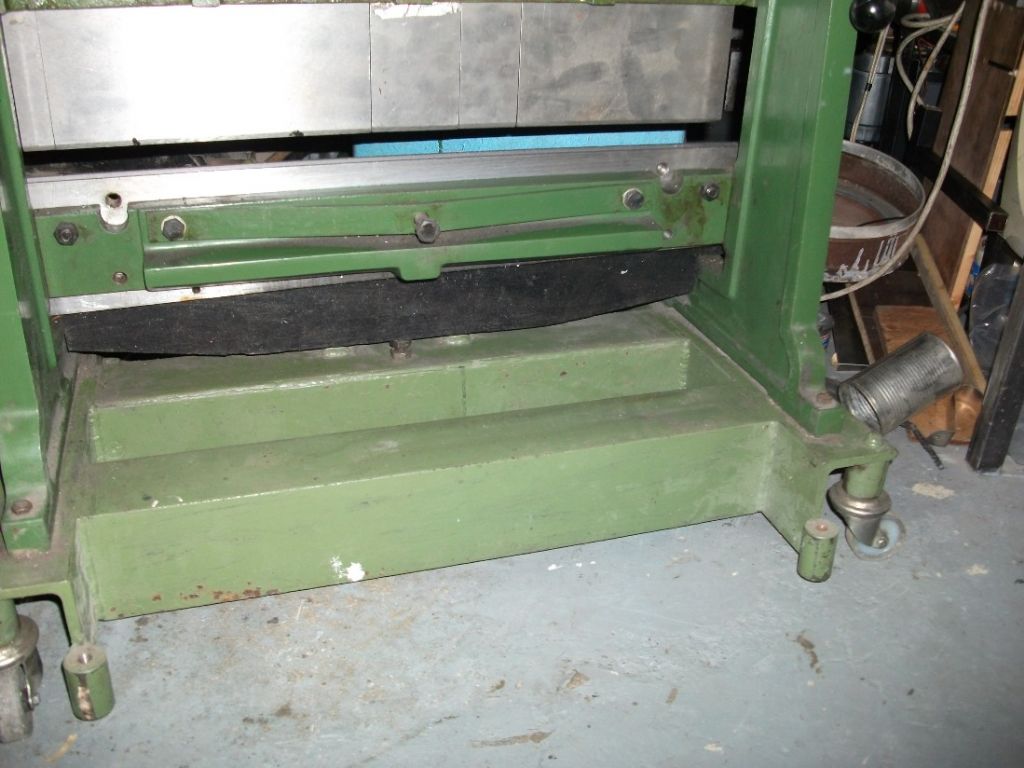
Had an accident with this trying to fold some 1/8 steel the end bolt was not tight and twisted and broke the casting ,Warco have some spares re-tapped both holes and fitted some longer better quality bolts.
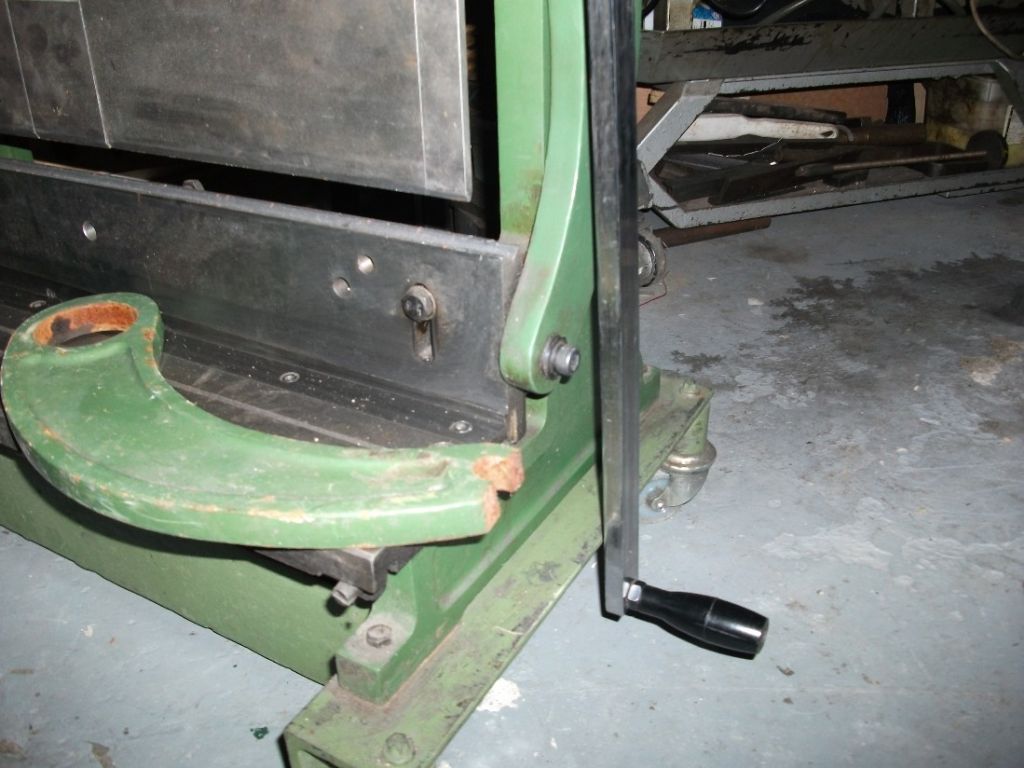
|
09/11/2021 20:10:35 |
Is this the sort of thing that you are asking about.
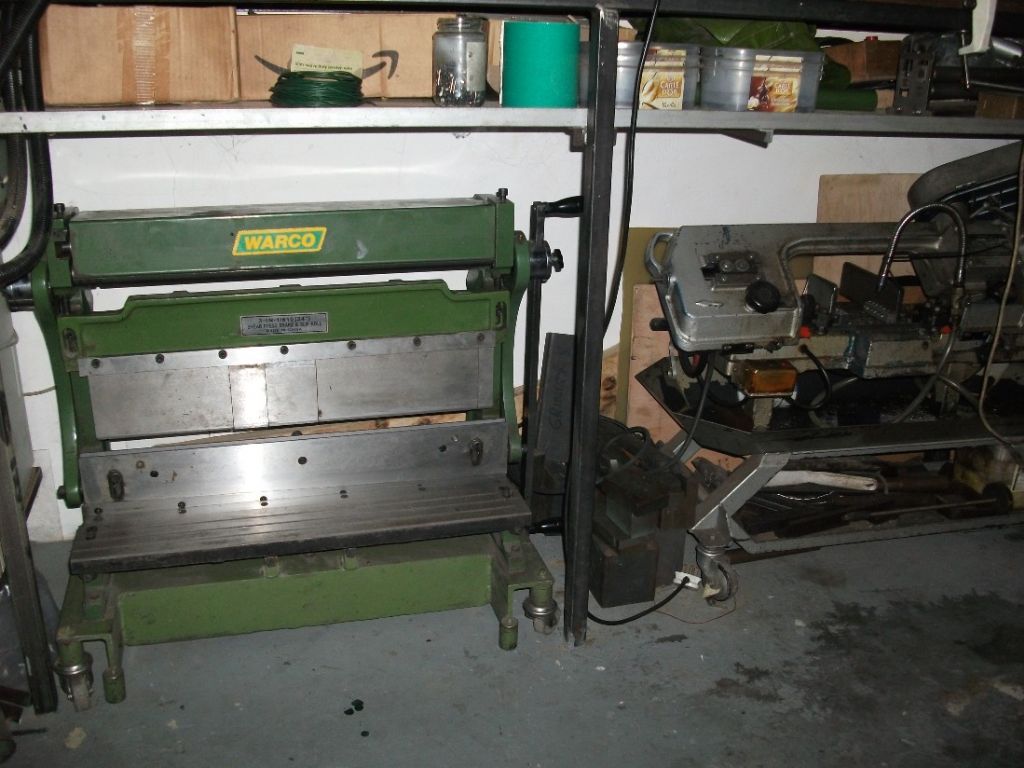
|