Thread: 16mm IDRIS |
24/04/2015 18:14:11 |
All the bushes are made.
I now have holes in the boiler tube for all the bushes.
Everything is a nice fit, just tight. By the time it's all cleaned up we will be spot on.
The end caps are bored for the fire tube. I decided on the thickness of the flange + 1.5mm for the fire tube height.
That way it is just above the radius on the end caps.
One thing I have learned. Don't solder the copper tube into the Steam bush before you try and fit it. I may have to remake this one. I'll flux it well and drop a ring of solder over the tube so that it as good as solders itself with the bush. Lets hope we don't block the tube in the process !
Other ideas welcome.
My Soldering plan very much follows Martins idea.
High temp for all the bushes in the boiler tube.
High temp for 1 end of the fire tube in it's end cap. Probably the one with the steam gauge.
The boiler tube I plan to heat from the inside with my larger torch. Once it's hot use a small torch on the outside just to run the solder.
I can then use Lower temp solder for the end caps and the other end of the fire tube.
Mental note: Need more pickle.........
|
21/04/2015 18:05:42 |
Hi Martin and thank you very much for your comprehensive reply to my questions.
I can get on and complete the Boiler at this point.
Roundhouse certainly appear to have the Axles, wheels and Safety valve.
I'll get them ordered over the next few days.
Another Q for you.
The Gas Tank. Do you plan to provide drawings for that ?
They seem rather costly to buy and I have a spare ~5" length of 2" tube.....
|
Thread: Know nothing |
18/04/2015 22:42:25 |
Just had a look at your photo's. You have a nice looking machine there and a lot of tooling and kit.
If I were to list this lot on ebay:
The tap and die sets sell separately as sets.
The Tool chest is desirable as an item on it's own. Hard to judge a value.
The items contained in the chest. I'd probably sell lots of similar items. Mostly not of great value.
Used milling cutters on their own have low if any value. List those as lots.
The devices and Instruments picture. The vertical slides list separately. they'll fetch ~£50 each.
The dividing head I'm interested in. ( The round disc with the holes in it and associated bits ) Message me.
Bottom L is the Std tool holder. Sell that with the Lathe. Should also have a spring.
In 'Tools' you have the Chuck Jaws. They go with the chucks and are important. Prolly go with the Lathe.
In Spares & Accessories #2 you have a plate that goes with the other similar one and Dividing head.
The angle plates have small but good value. Probably list those individually.
Most of the rest list individually.
Spares & Accessories #1 Most of that can go with the lathe.
There are companies that clear workshops. If the Ebay idea sounds like a lot of work ( it is ), they may be able to help.
There is also a "For Sale" section on here. I'm sure that will generate some interest.
|
17/04/2015 21:28:15 |
Hi Nick. Myford ML7's can go for as little as £300 when they are badly listed or Photo's are poor.
A well listed with good Photo's ML7 can make £800 and sometimes more for a good example.
You may well be better off selling the Lathe and a basic set of tooling as 1 Auction Lot and the 'nicer' accessories as separate lots.
When you describe your ebay items be Brutally Honest. If the paint is bad, say that the paint is bad, If it's rusty say it's rusty and take pictures.
Being Honest will often attract more bidders and a higher price.
Driils, taps, Dies metal stock and the such sell as job lots. 20 - 30 items at a time.
It might be worth some mixed lots for any left overs.
Finally, work out what it will cost to post any items. Weigh them and use the price calculators from all the postage co's. People hate vague or excessive shipping costs.
Good luck and hope you get good money for your stuff.
|
Thread: 16mm IDRIS |
14/04/2015 18:36:29 |
Hi Diane. Thanks for the update.
|
14/04/2015 18:07:14 |
Took the plunge and cut the Boiler tube tonight.
Drawing says 6.400"
My cut is at 6.470" less than 1/2mm to big. That'll do.
I mounted the tube on 2 cones on a bit of 8mm rod between 2 vices.
That way I could spin the tube to scribe square lines. I then did up the grub screws to stop thing rotating as I made the cut.
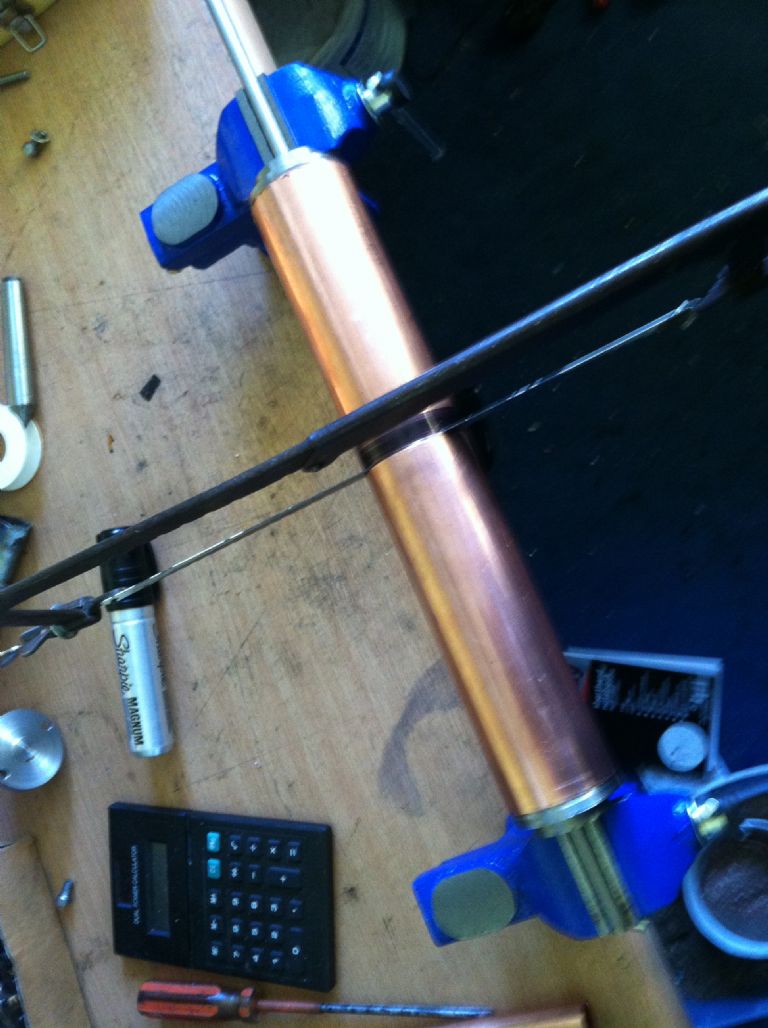
Overkill ?
Well I got a nice square cut very close to the correct length. I say it worked just fine.
BTW, The cones real life job is to hold my Milling Vice on the mill table.
I'm going to make the wheels. Cast Iron or mild Steel ? I have both in a suitable dia.
Axles will be Silver steel, probably 6mm rather than 1/4 " as I have loads of 6mm silver steel rod.
|
13/04/2015 19:18:41 |
Steven. This is my first Loco build and great fun it's been so far. I have made a couple of Stationary Engines. (Puddleduck and Dads n lads). This is quite ambitious for me.
I need:
Wheels, Axles, Cranks, Safety Valve are the items mentioned in this edition.
Wheels I can make if required. I have MS and Cast Iron. 1 1/2" flange. 1.323 tread.
Axles I can make - but have no drawing or details. Looks like they are 1/4 " dia from the Bush drawing.
Crank webs I can make.5/16 Throw - I guess that's enough info.
Safety Valve I'd rather not make.
Sounds a bit like I'm moaning, That's not my intention........
Alex.
|
13/04/2015 18:20:43 |
Hi Guys. Just had the latest ME drop through the door.
Martin makes Reference to www.brandbright.co.uk
Heading to the website, they are retiring and may or may not have the various required items available.
Can anyone suggest other suppliers of similar items ?
|
12/04/2015 12:20:52 |
Hacksaw it is then. Thanks 
|
12/04/2015 11:41:09 |
Forgive me if this has already been covered....
I have an 18" length of 2" Copper tube.
Whats the best way to cut it ?
A Pipe Cutter will curl the ends in.
I thought about a Parting tool in the lathe with the tube held in cones.Could get Messy!
I have a Band saw but the blade is fairly corse.
I'm not the best with a hacksaw.
Thanks
|
11/04/2015 12:41:43 |
Water gauge bushes made. 5/8" Round PB made square.
Waiting on 3/16 Tap for the final bushes.![img_0922[1].jpg img_0922[1].jpg](/sites/7/images/member_albums/103995/595003.jpg)
|
10/04/2015 18:35:24 |
Hi John & Dave.
Thank you both for your replies. I knew there must be a reason.
The Chemistry there makes sense as well.
Looks like I need to buy or make some square Phosphor Bronze.
|
10/04/2015 18:18:41 |
Another Q for you all.
I notice brass is not used for Boiler Bushes and Fixings. It's all Phosphor Bronze on this and other Models.
I guess there is a reason for this ?
The Water Level glass bushes call for Square Phosphor Bronze and I have little desire to buy some.
I do however have suitable Square and Hex Brass. I suppose I can make square from Round .......
Can I use Brass for the water gauge Bushes soldered to the Boiler ?
Thanks
Alex.
|
08/04/2015 18:11:23 |
Taps n Dies turned up yesterday .
I made a clamp to stop the (now soft from soldering) copper tube from expanding as I threaded it.
Put the Gas Valve back in the 4 jaw. Drilled and tapped the Gas Jet. Tapped the outside to fit the tube.
At the weekend I made the formers for the End Caps and made the 2nd end cap tonight.
They are a really nice fit in my Boiler tube.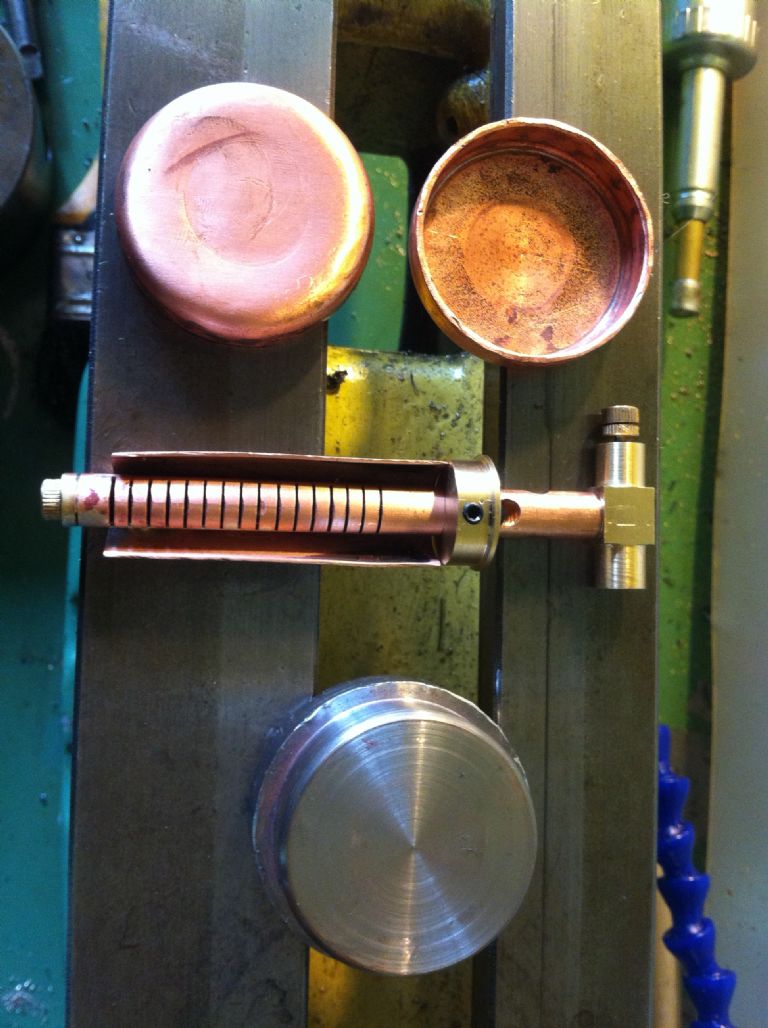
All looking rather good.
|
Thread: What did you do today (2015) |
07/04/2015 20:00:27 |
Made a former for the 16mm IDRIS boiler end caps at the weekend.
Started making the boiler end caps tonight.
Apparently quenching red hot bits of copper in the bathroom sink is not acceptable.
I'll use the loo next time !
1 end cap completed 2nd is cut, just needs forming.
|
Thread: 16mm IDRIS |
05/04/2015 08:11:04 |
Hi Jason. The taper fits exactly as it should (MT2) in the spindle.
However there is not clearance to make the cuts. The pipe fouls the headstock. A larger (4" saw would resolve this.
I'm aware that this setup is less than ideal and agree that for heavier work this would be unsuitable.
I like your Tailstock idea. Noted for future ref.
|
04/04/2015 19:19:35 |
Just sussed out the photo thing....
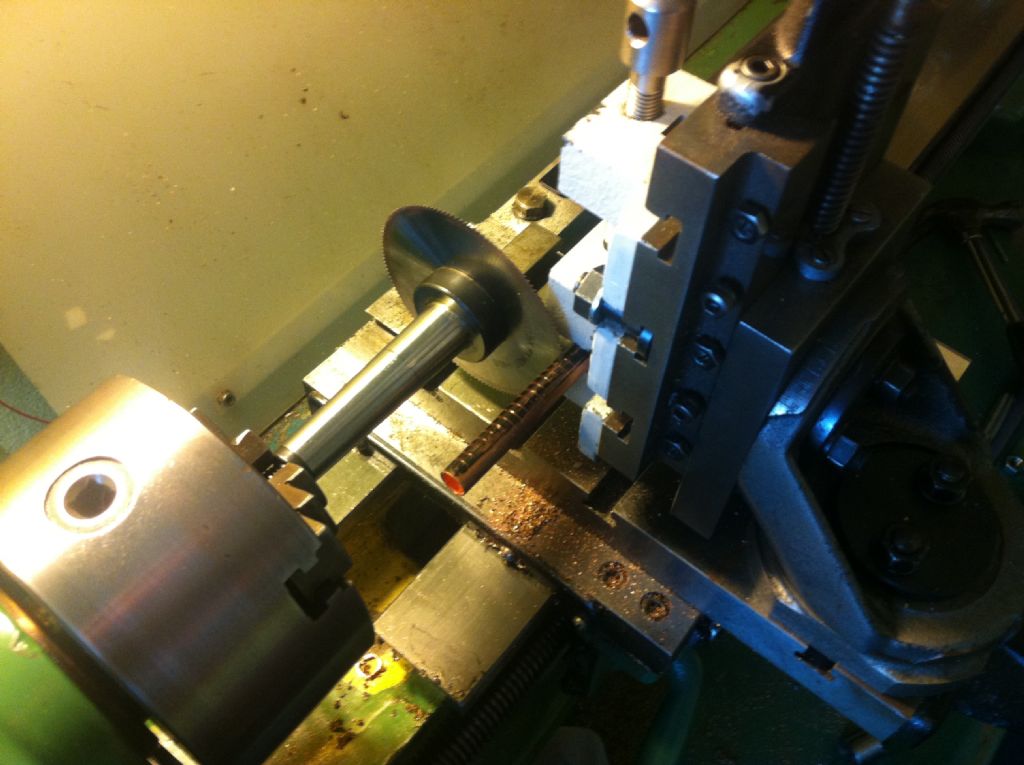
|
04/04/2015 17:28:57 |
Hi All. Got a little more workshop time today.
Made the Burner tube.
My Myford Lathe made this very easy. (8 TPI Lead Screw)
I used a 0.5 mm Slitting saw mounted in the lathe chuck to make the cuts.
3/8 Copper Tube in my vertical slide with a small milling vice.
Set the Lead screw dial to zero, Engage the lead screw and take up the lash.
Line up the first mark, make a 3.5mm cut.
1 full turn on the lead screw and make the 2nd cut. Rinse and repeat until you have all 16 slots.
Deburred the inside with a suitable size drill.
|
01/04/2015 22:18:05 |
Hi Jason.
Rest assured I don't intend to start cutting £40 worth of copper until I can see and understand 100%where I need to get to.
Tomorrow I intend to complete the Burner pipe. Waiting on Dies for the gas valve which is otherwise complete.
Thanks for your answers.
|
01/04/2015 19:23:05 |
Hi All.
Not sure where to ask these. If here is not appropriate please point me in the correct direction.
This will be my first Boiler but I have done a fair bit of silver (and soft) soldering before.
It'll no doubt be a challenge and I have enough metal for a 2nd attempt.....
Couple of Q's for you.
Am I better off Pilot drilling all the Bushes then Drill / Tap them to size later ?
I'll make a former to make the boiler end plates. I also have access to a press.
How high up should the Fire tube be ? It's not shown on the drawing.
And Lastly. The water gauge bushes.
I guess they are drilled through and outside hole plugged.
The drawing shows that they are not drilled through.
Thanks
Alex
|