David K | 22/12/2018 14:47:14 |
258 forum posts 259 photos
|
I also need two centres through the crank pin axes for machining the big end.
To do this the bar is fitted to two 'V' blocks and clamped in my mill vice on the mill.
I centred the mill spindle over the first centre drill and then moved the mill table
over to the crank pin axes and put a second centre drill. The bar was flipped 180 degrees
while still clamped to the 'V' blocks and the process was repeated.
|
David K | 22/12/2018 14:48:13 |
258 forum posts 259 photos
|
Now I have the centres I mounted the bar first between the mains and then the crankpin to remove
the bulk material. 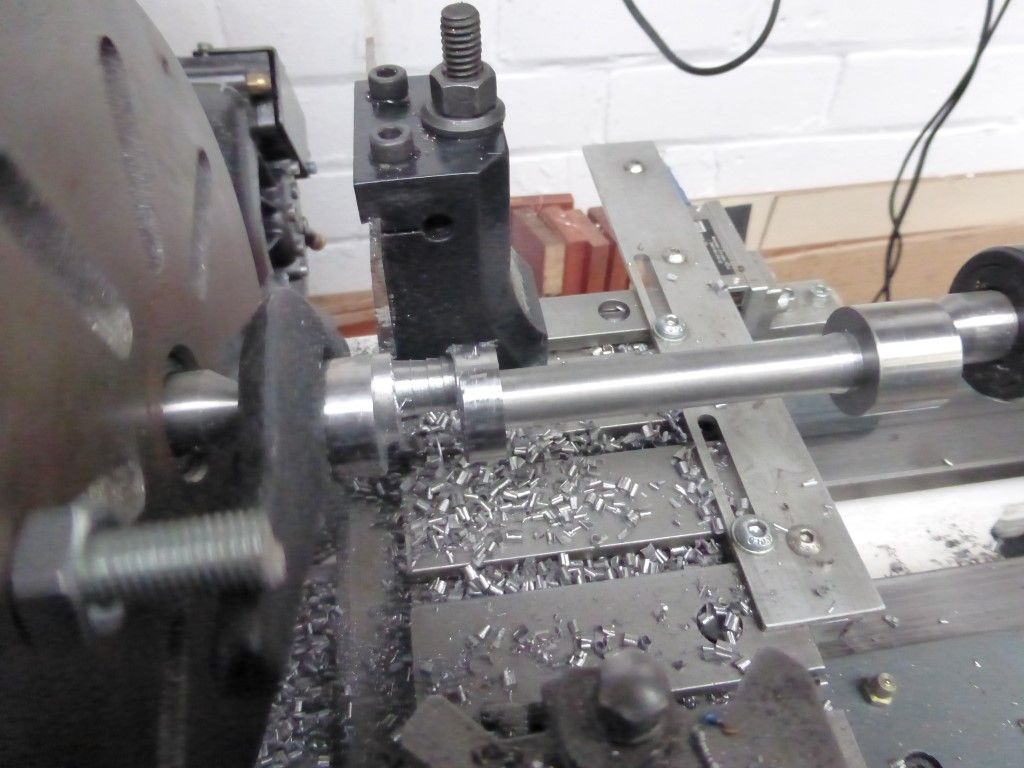
|
David K | 22/12/2018 14:51:28 |
258 forum posts 259 photos
|
Then more material is removed to form the basic shape
![]()
As I get down to the final sizes lighter and lighter cuts are used to try and get a nice finish.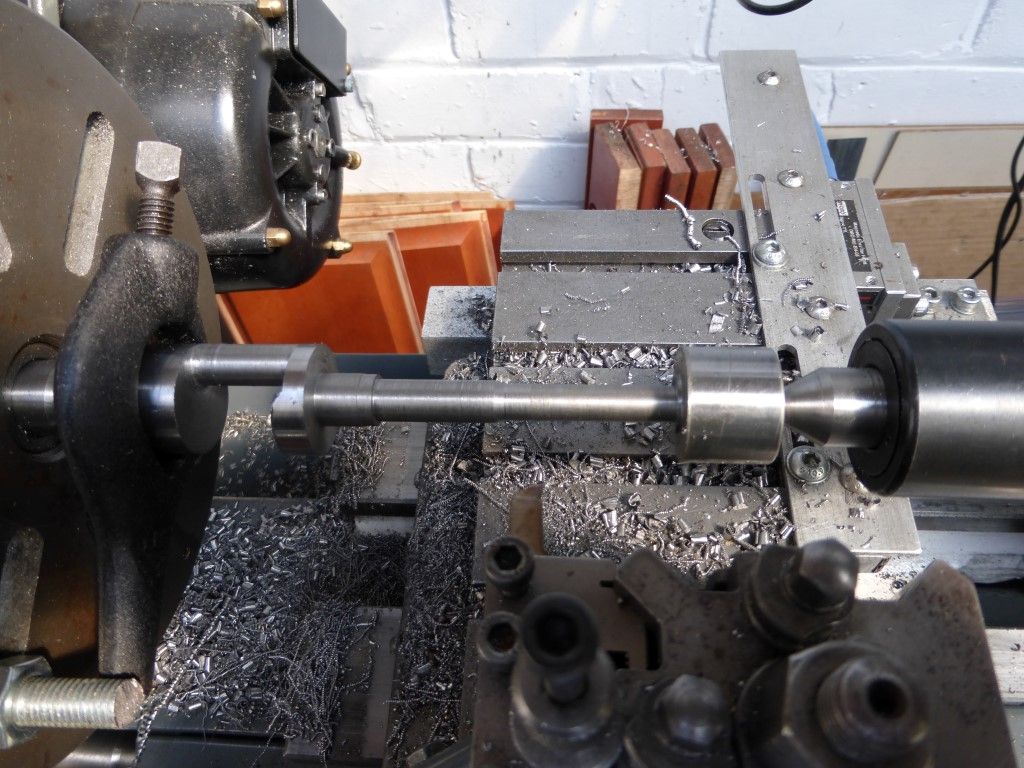
|
David K | 22/12/2018 14:52:44 |
258 forum posts 259 photos
|
Back on the mill table I need to cut a 20t 48dp gear on the crank to drive the planet gears
I made earlier. I could not use the gear cutter I used on the planet gears as the gear is cut
close to the crank web and needed to be a smaller diameter cutter. So I made cutter from
silver steel , there is plenty of info about making gear cutters on the internet so I won't describe
it here.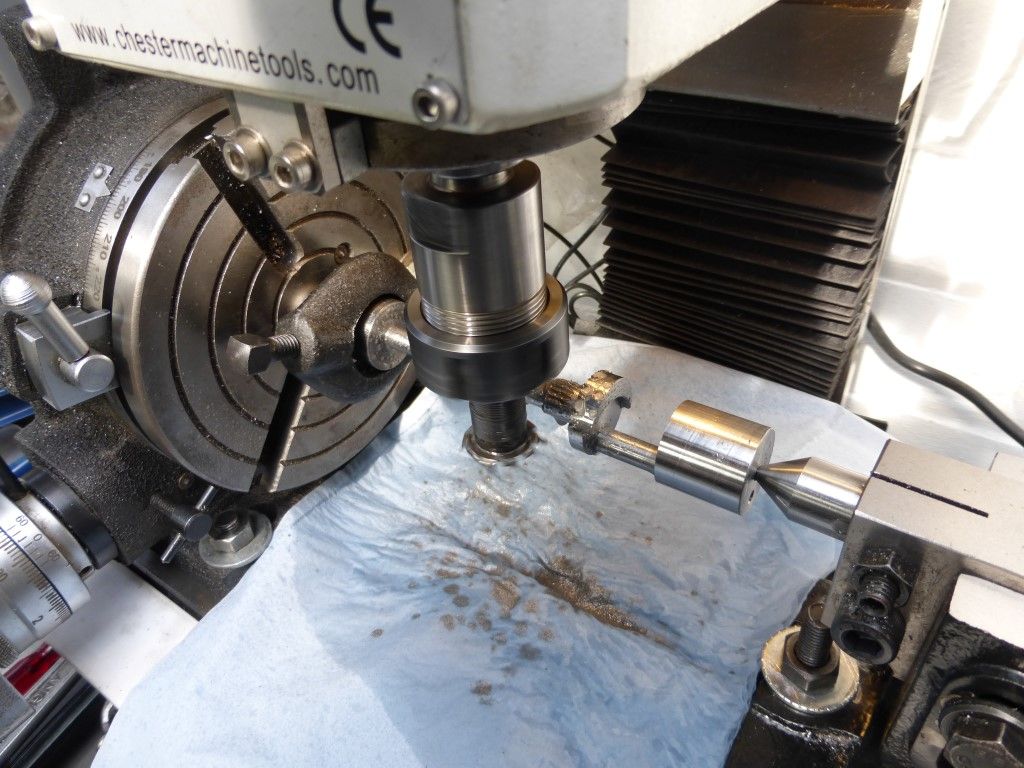
|
David K | 22/12/2018 14:53:45 |
258 forum posts 259 photos
|
With the gear cut I used a milling cutter to form the crank web 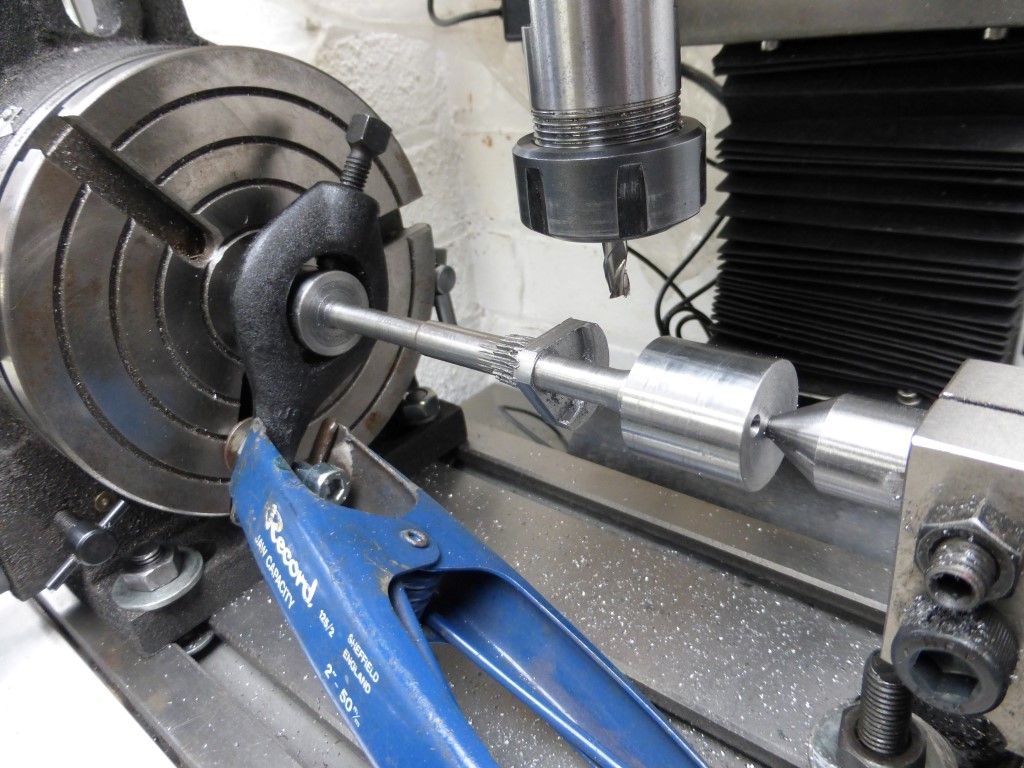
|
David K | 28/12/2018 20:37:35 |
258 forum posts 259 photos
| The crank needs extra weight to balance the engine so I turned and milled a counterweight
out of mild steel.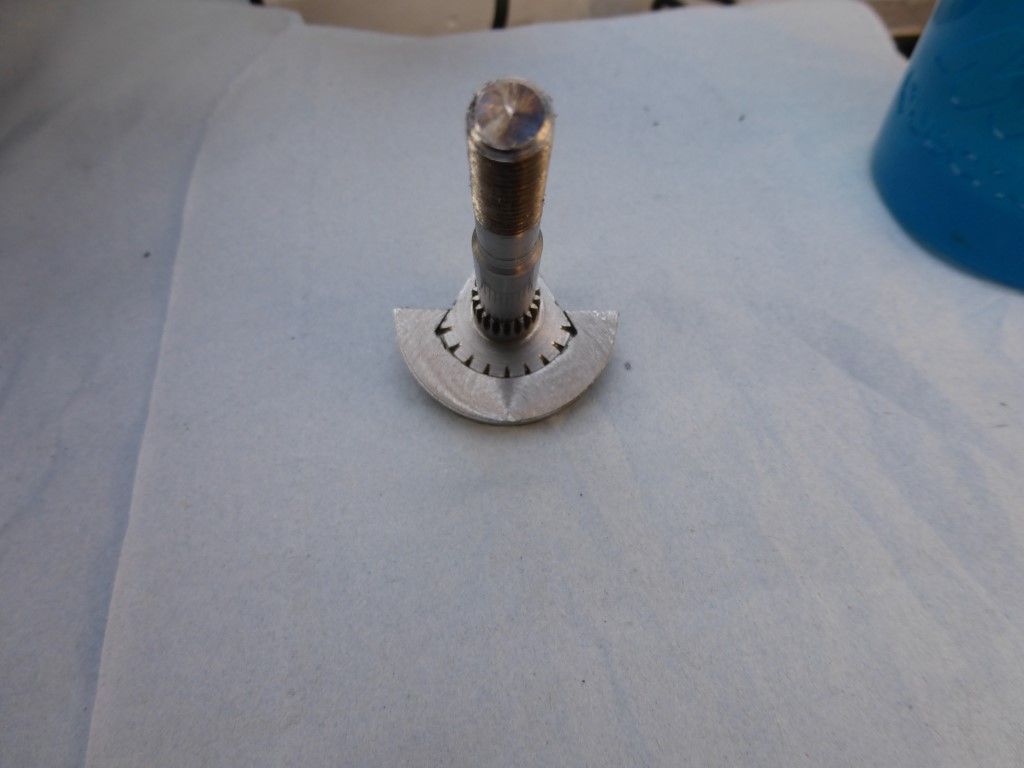
|
David K | 28/12/2018 20:38:23 |
258 forum posts 259 photos
|
Then it is pinned in place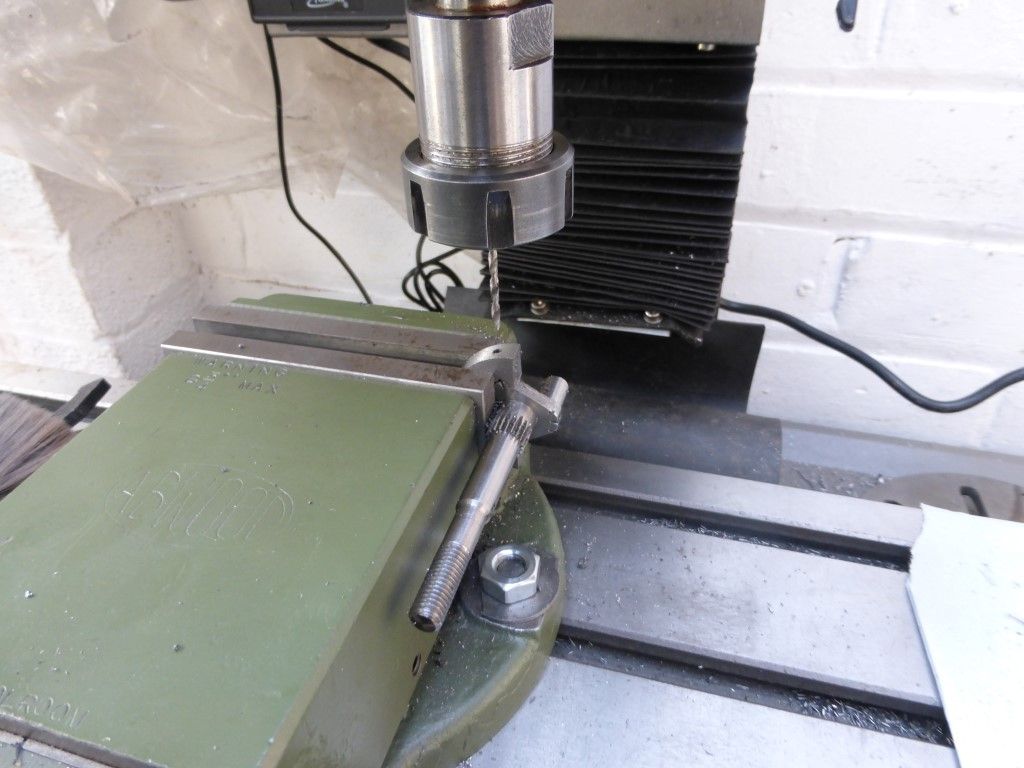
|
David K | 28/12/2018 20:39:34 |
258 forum posts 259 photos
|
Once pinned I silver soldered it in place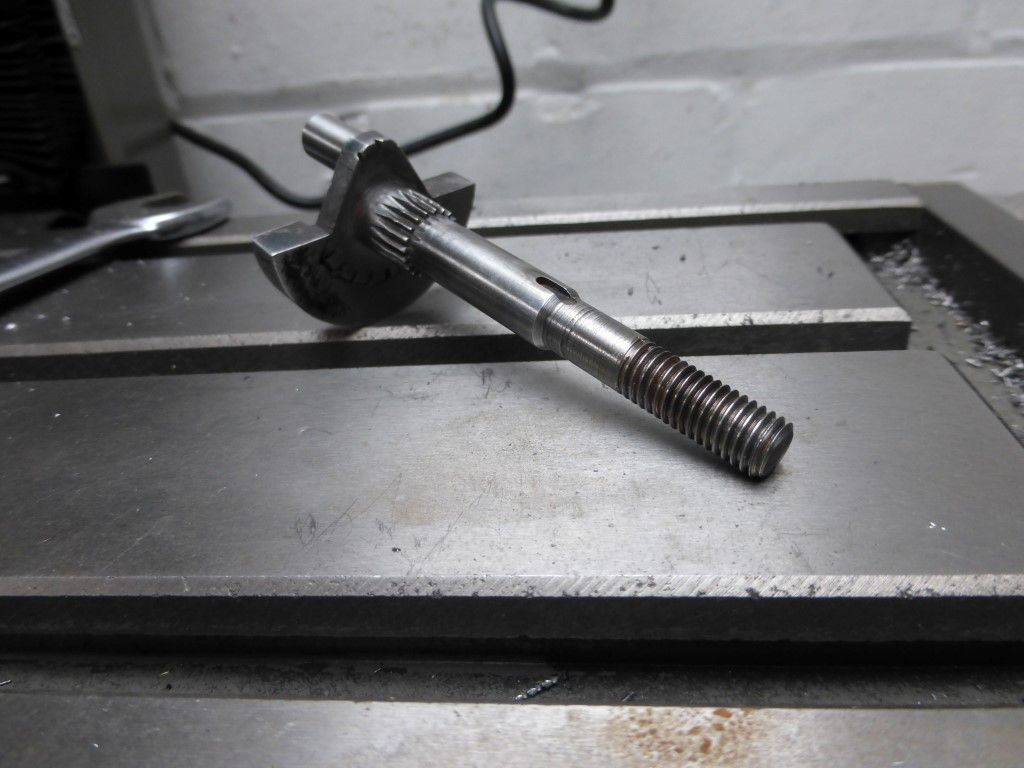
|
David K | 28/12/2018 20:42:31 |
258 forum posts 259 photos
| Camshaft, the camshaft is made from 1.25'' silver steel round bar.
First I turned a piece down to size and then turned a small shoulder on the front.
|
David K | 28/12/2018 20:43:22 |
258 forum posts 259 photos
|
The centre is then drilled and reamed ready to accept a bronze bush. Using a
parting blade I made a thin groove which is used to separate the inlet lobe
from the exhaust lobe then parted the piece off.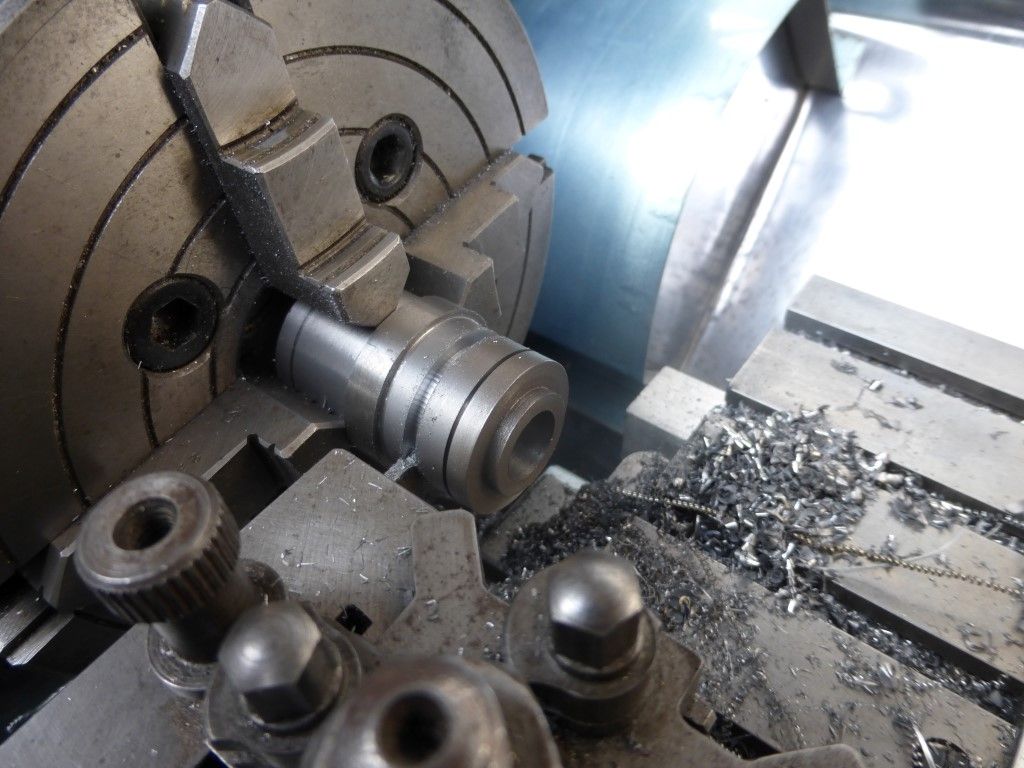
|
David K | 28/12/2018 20:43:58 |
258 forum posts 259 photos
|
With the piece mounted on the mill I drilled and reamed the two holes which the planet gears
will run in. These holes were drilled through into the mounting block so I could fit two
pegs in to help locate the piece.
|
David K | 28/12/2018 20:49:13 |
258 forum posts 259 photos
|
Next job was to mill the sides away to form the inlet lobes , only milling down to the grove used to
separate the lobes. Then the piece was flipped over and the exhaust lobes were milled in the same way. 
|
David K | 28/12/2018 20:50:05 |
258 forum posts 259 photos
|
The piece is then heat treated to harden the silver steel 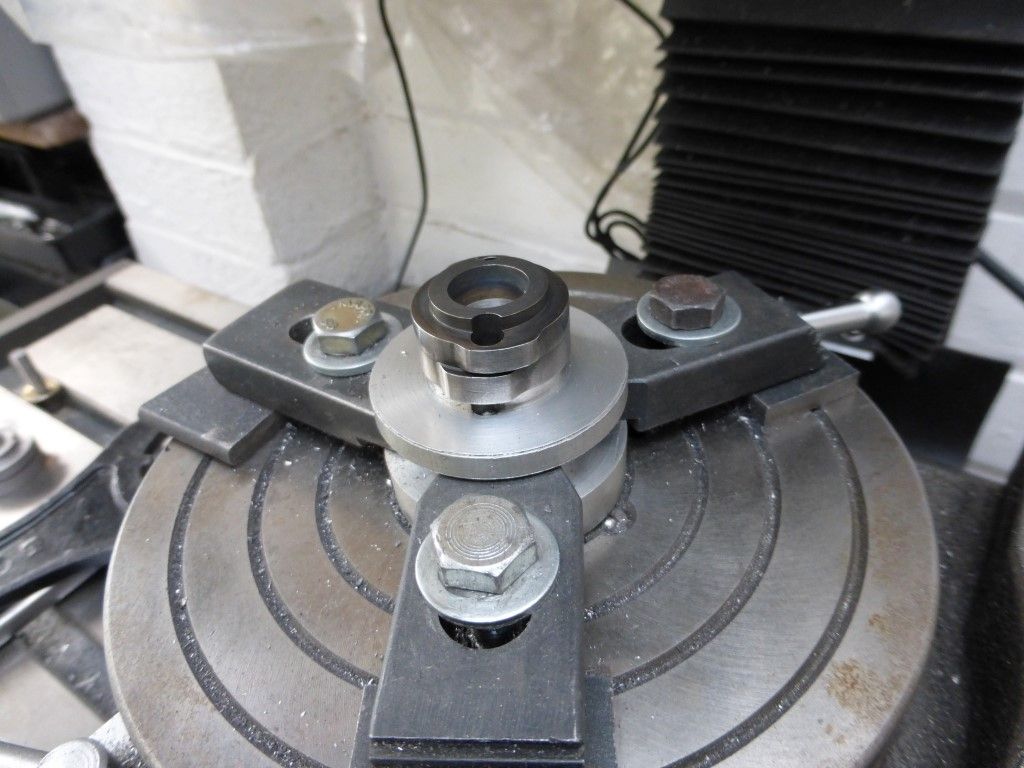
|
David K | 28/12/2018 20:51:19 |
258 forum posts 259 photos
|
Made some bronze bushes and pressed them into the Cam 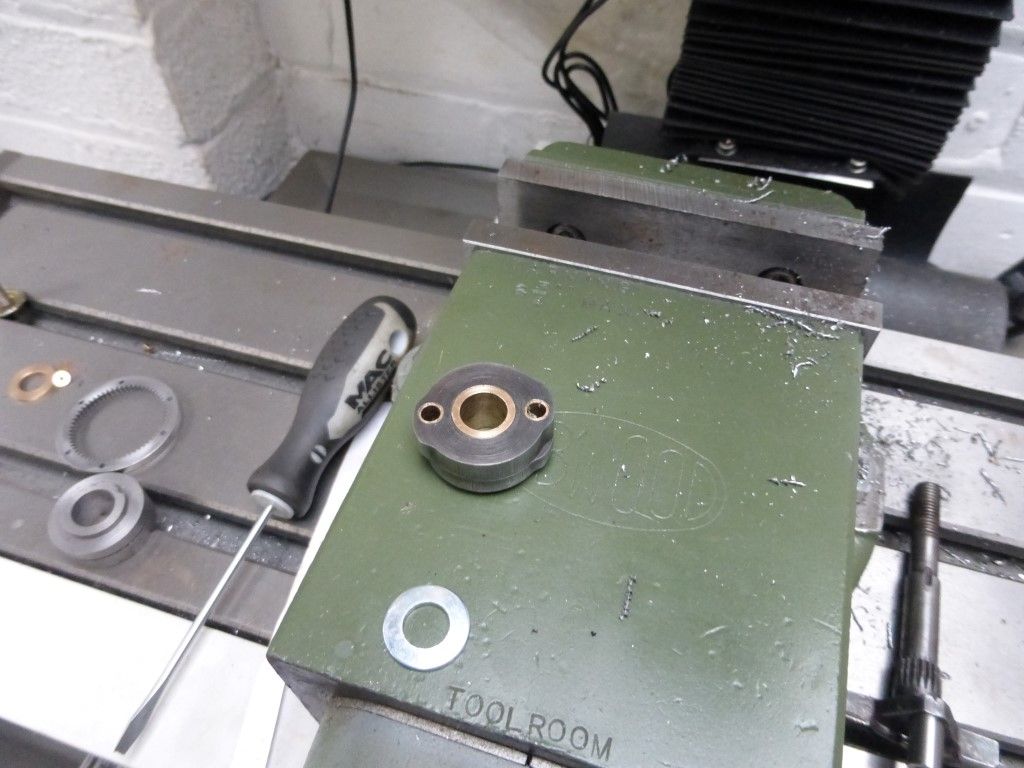
|
David K | 28/12/2018 20:53:21 |
258 forum posts 259 photos
|
All the items for the cam drive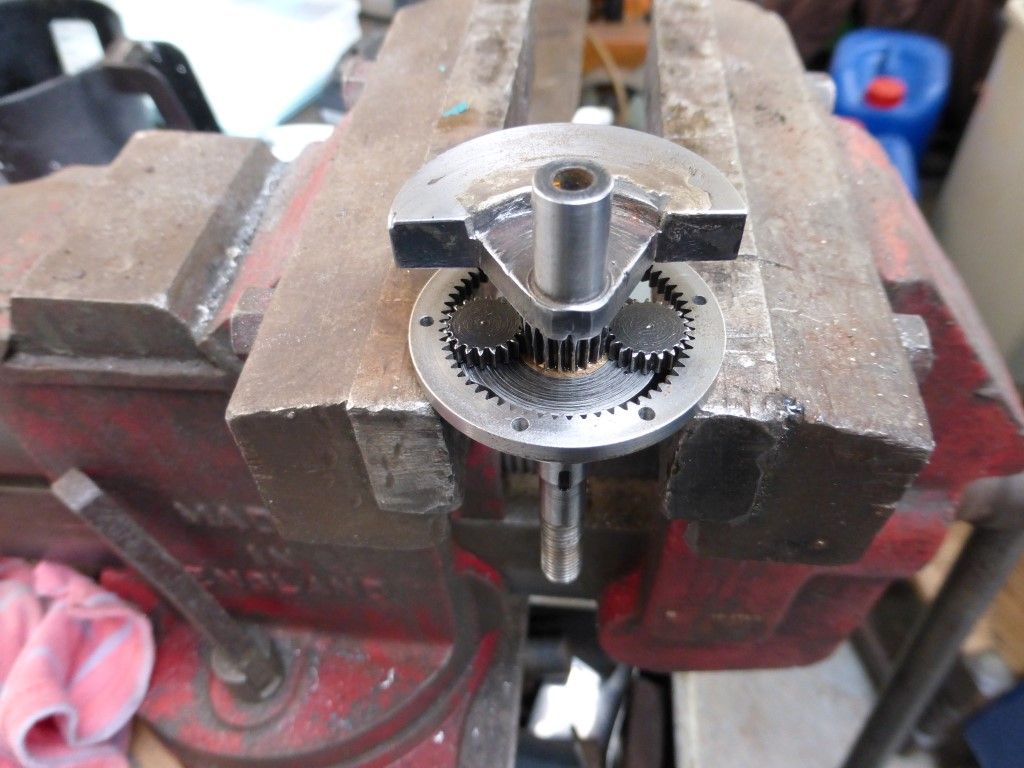
|
David K | 28/12/2018 20:53:53 |
258 forum posts 259 photos
| 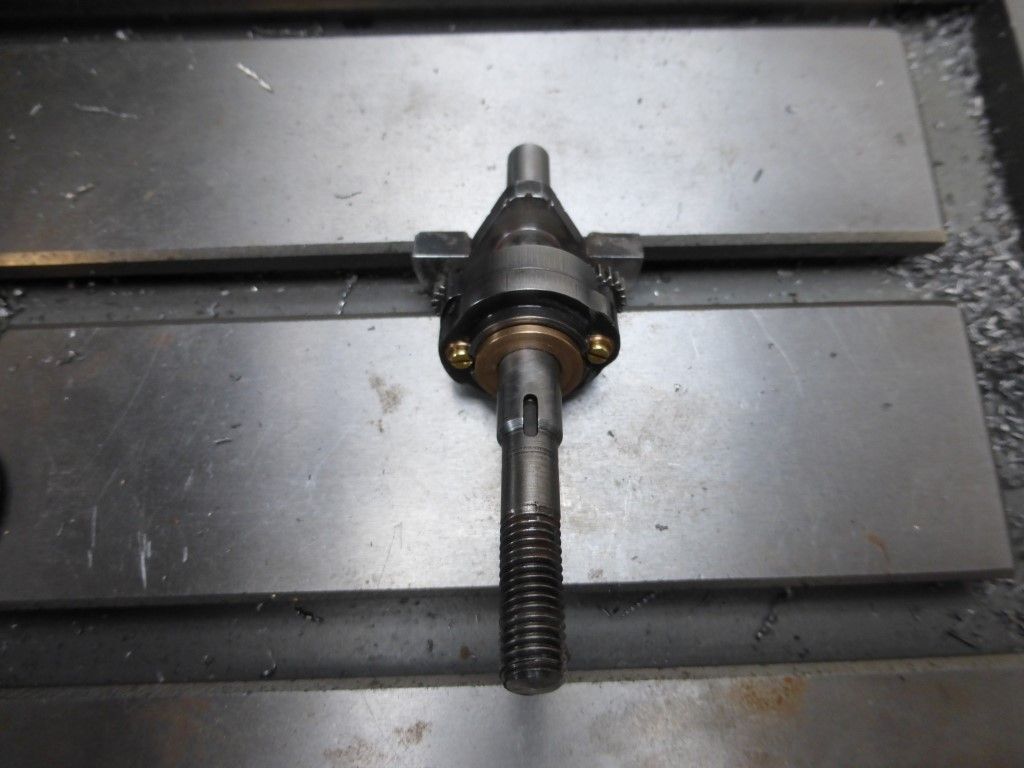
|
David K | 28/12/2018 20:54:55 |
258 forum posts 259 photos
|
I made the big end bearing from phosphor bronze, the bearing is threaded into
the master con rod to help with assembly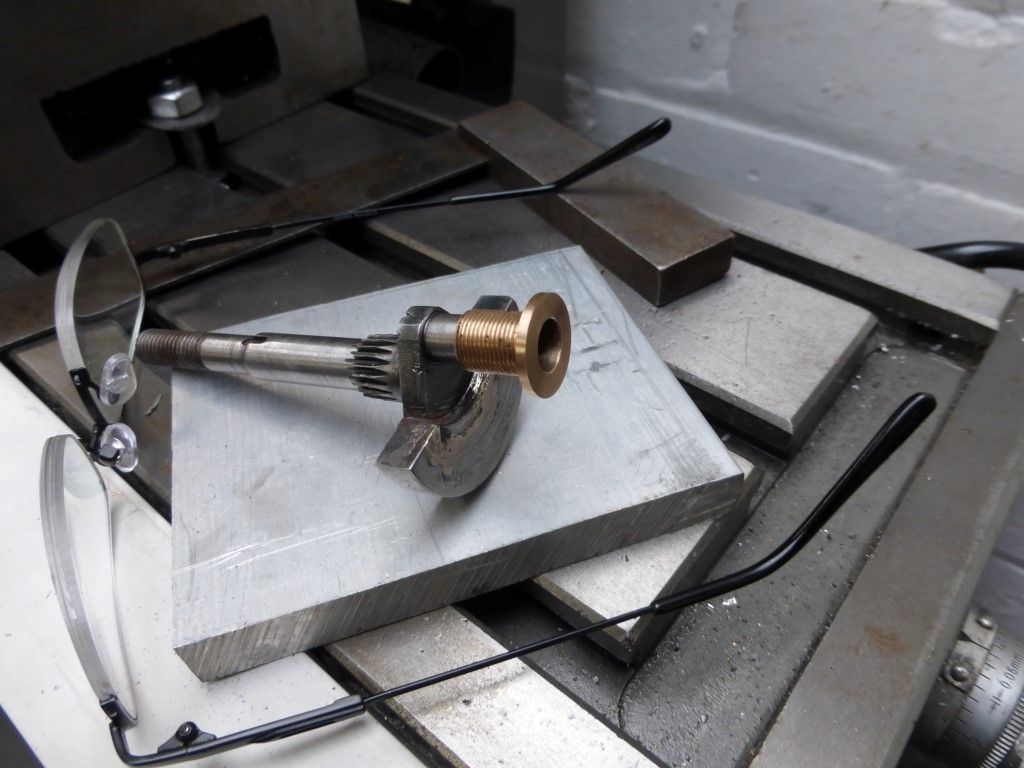
|
David K | 28/12/2018 20:56:01 |
258 forum posts 259 photos
| Then I started the con rod, this is made from 6061t alloy which has a greater mechanical strength than
the 6080 I have used for the crankcase.
|
David K | 28/12/2018 20:56:51 |
258 forum posts 259 photos
|
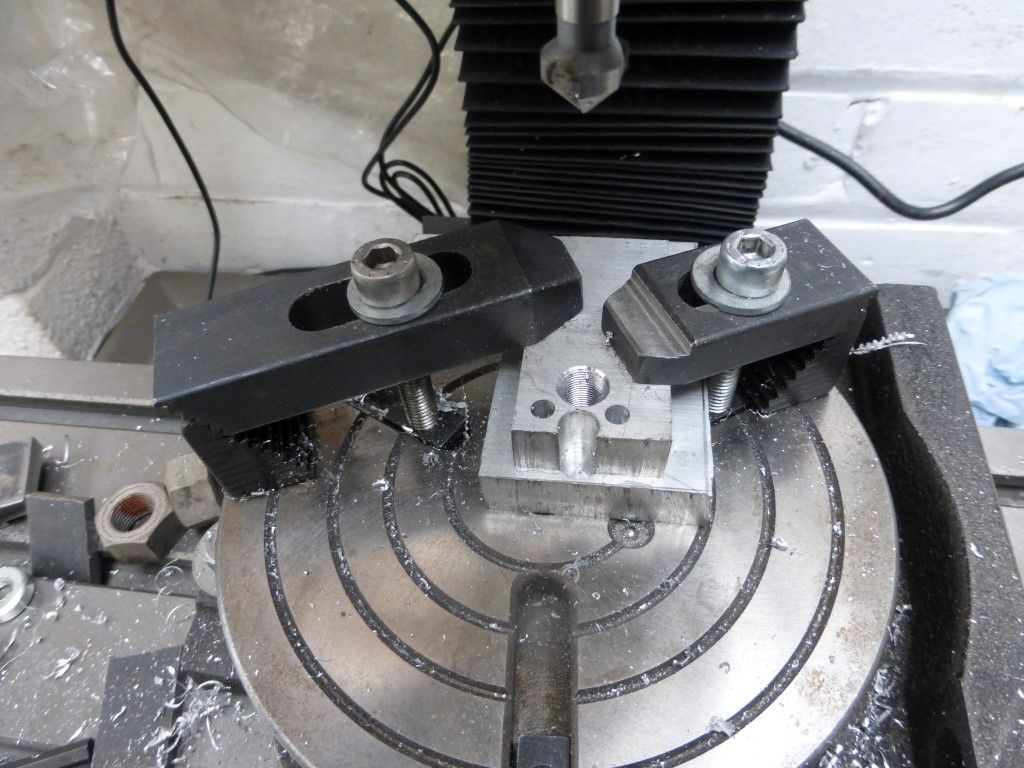
So I mounted a piece of alloy on the mill centred over the big end , I used a scrap piece of alloy underneath
to save damaging my rotary table.
I centre drilled ,drilled and tapped m10 fine through for the big end bearing then moved the table and
drilled , tapped m4 the holes for the slave rod pins.
|
David K | 28/12/2018 20:57:57 |
258 forum posts 259 photos
|
The slave rod holes were then opened out to 6mm for half the depth of the rod. The big end bearing is screwed
into the rod by hand, I machined a slot and tightened with a screw driver then using an m6 end mill I relived the
bearing were it covered the slave rod holes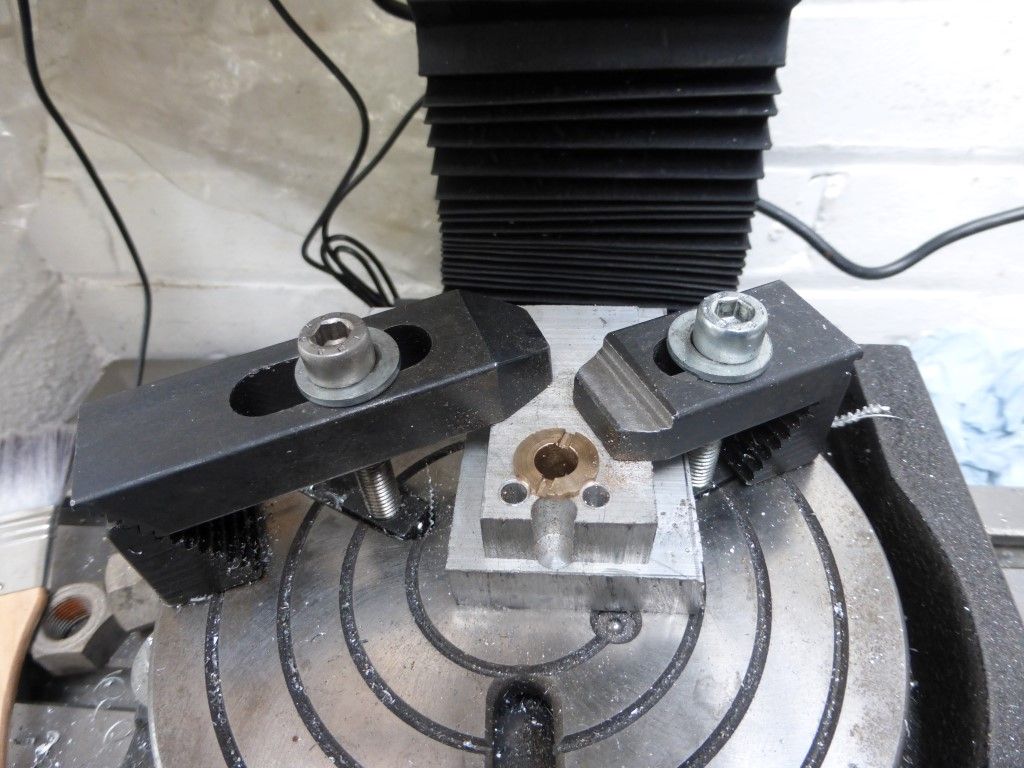
|