David K | 19/12/2018 15:44:58 |
258 forum posts 259 photos
|
Here you can see the cylinders just needing the second slot finishing on the left
hand rocker posts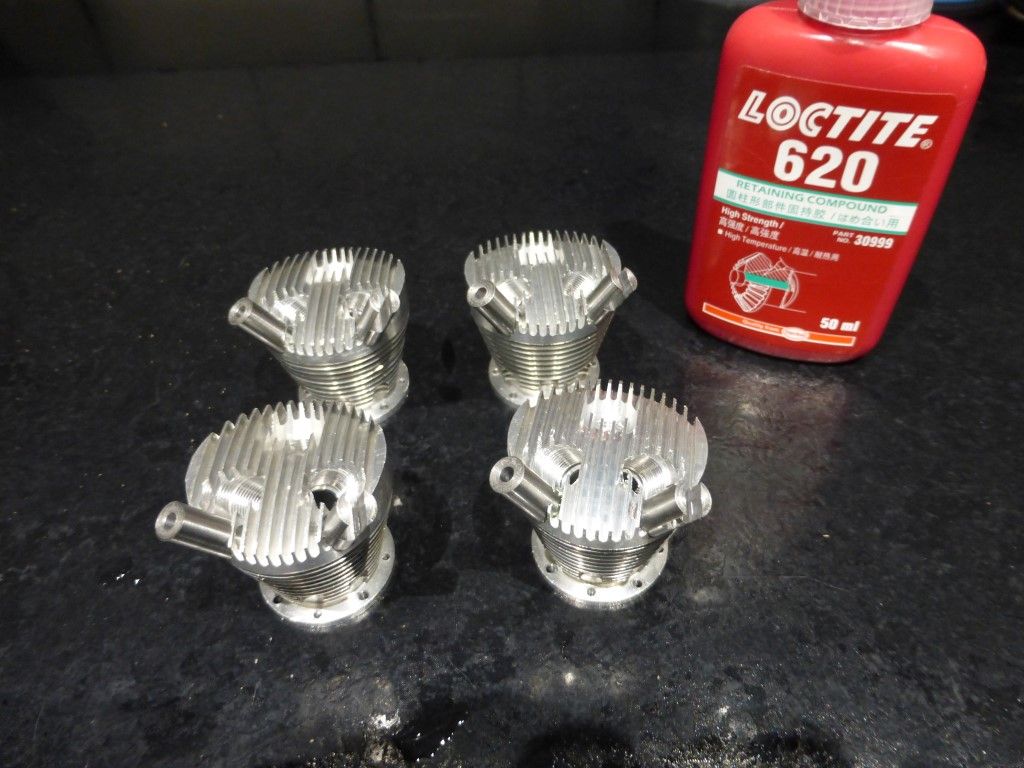
|
David K | 19/12/2018 15:49:59 |
258 forum posts 259 photos
|
With the cylinders drilled and tapped I need to make the valve seats/guides.
These are made n one piece out of 660 phosphor bronze.
A piece of bronze is turned down and threaded m10 fine to match the Cylinder, then
the first 2mm is turned down to 8mm and the step is turned a 45 degree taper.
|
David K | 19/12/2018 15:51:20 |
258 forum posts 259 photos
|
continued from above
This taper will be the seat for the guide when screwed into the cylinder.
A 3mm hole is then drilled and reamed through the centre, the front half is opened
out to 6.5 mm then a 45 degree valve seat is formed as in the pic below. 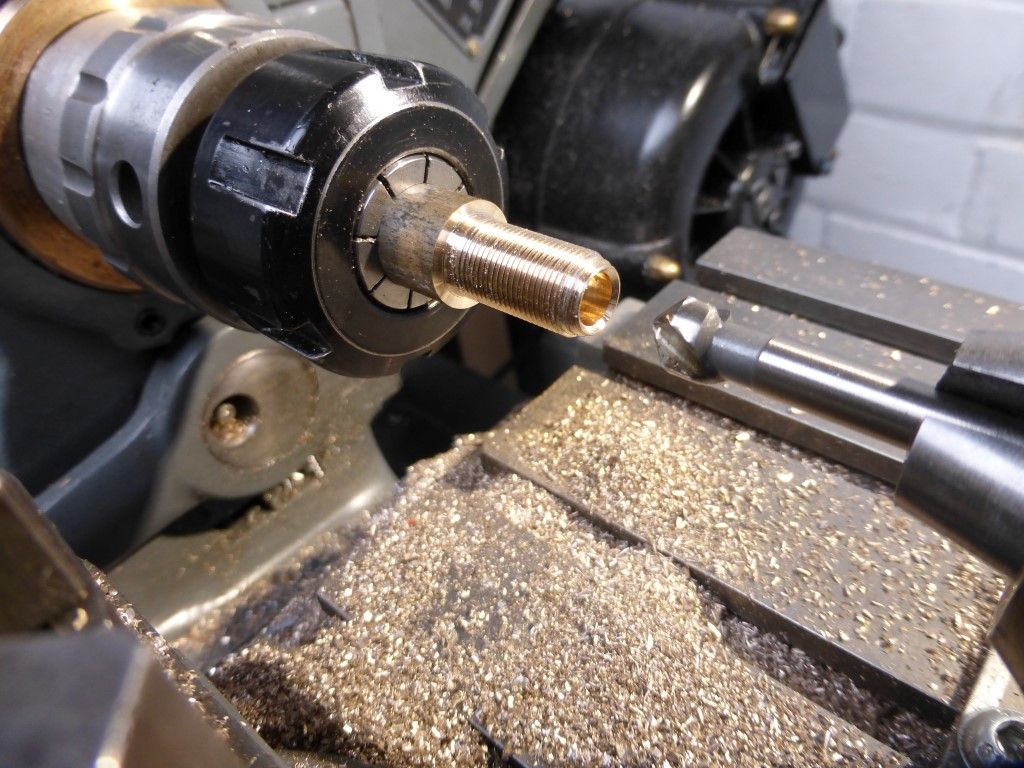
|
David K | 19/12/2018 15:52:25 |
258 forum posts 259 photos
|
I then placed a bit of alloy in the lathe , tapped it m10 and screwed the guide into this
so I can reduce the top halve to form the guide. Two small holes are drilled either side
of the valve guide and a tool is made to insert into these which will allow me to screw the
guides in.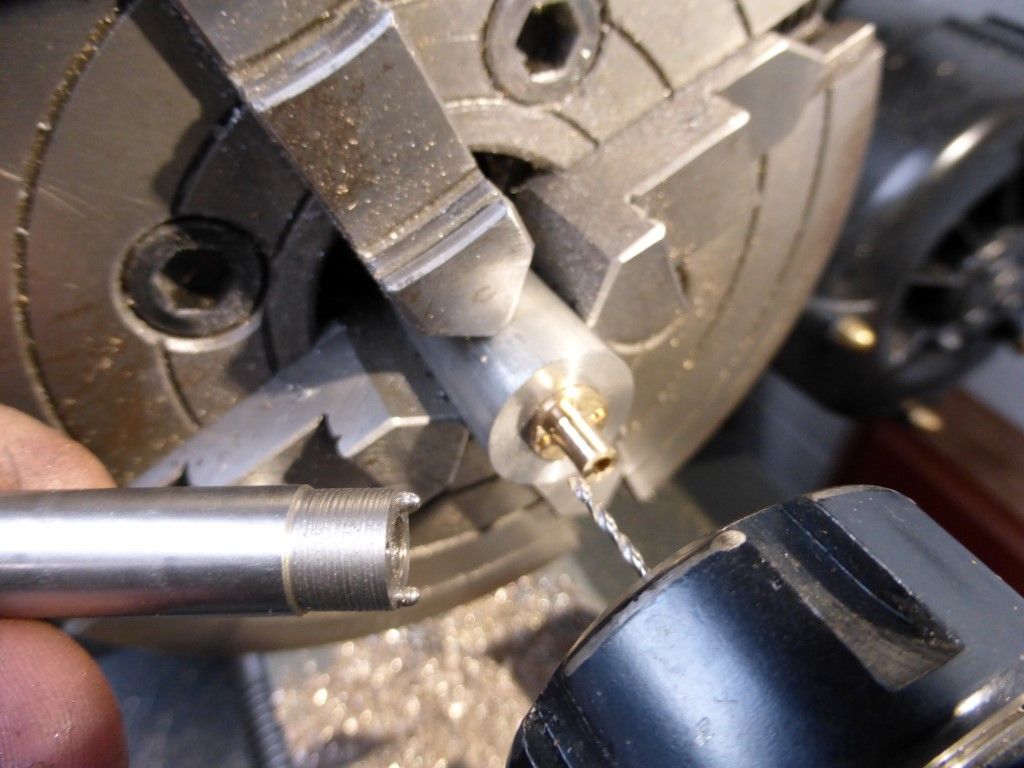
|
David K | 19/12/2018 15:53:05 |
258 forum posts 259 photos
| finished guides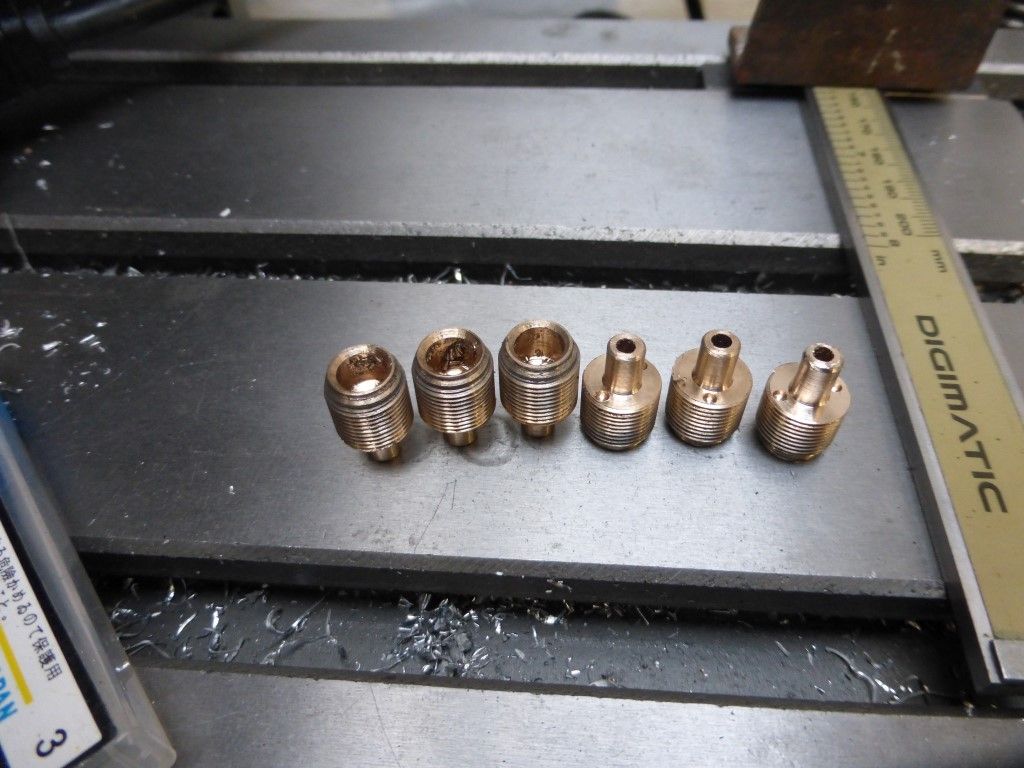
|
David K | 19/12/2018 16:01:07 |
258 forum posts 259 photos
|
While I was making the guide I made a small collet to slide over my 90 degree
cutter to enable me to keep it square while I cut the seat for the guide. 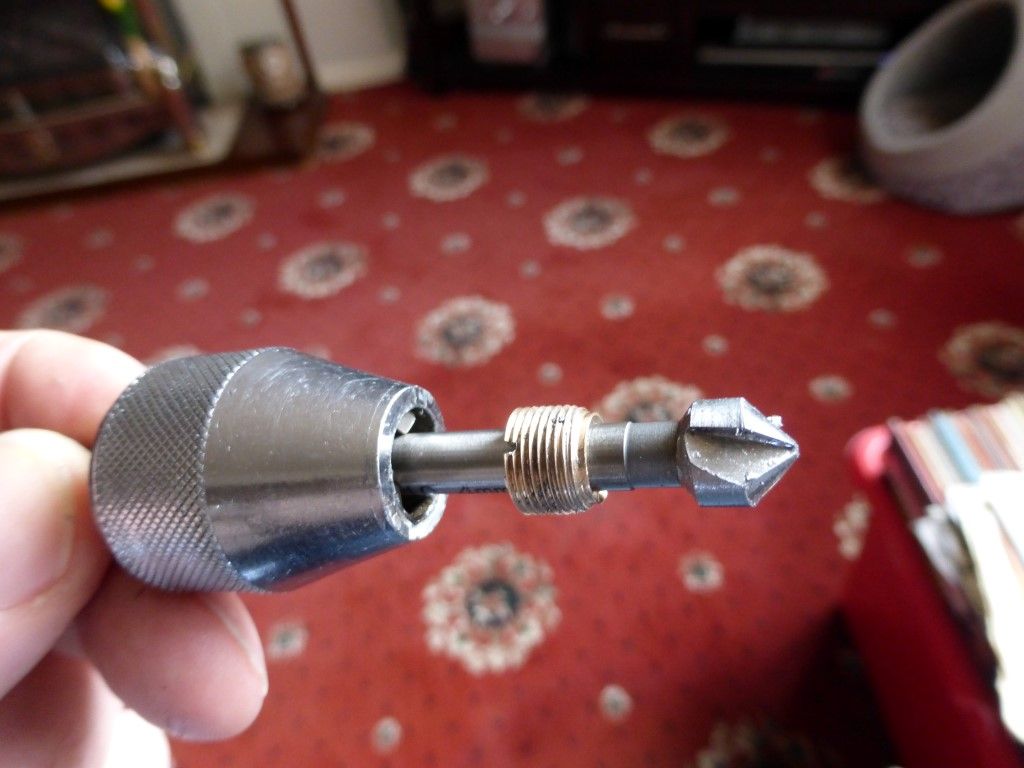
|
David K | 19/12/2018 16:01:49 |
258 forum posts 259 photos
|
cutting the seat 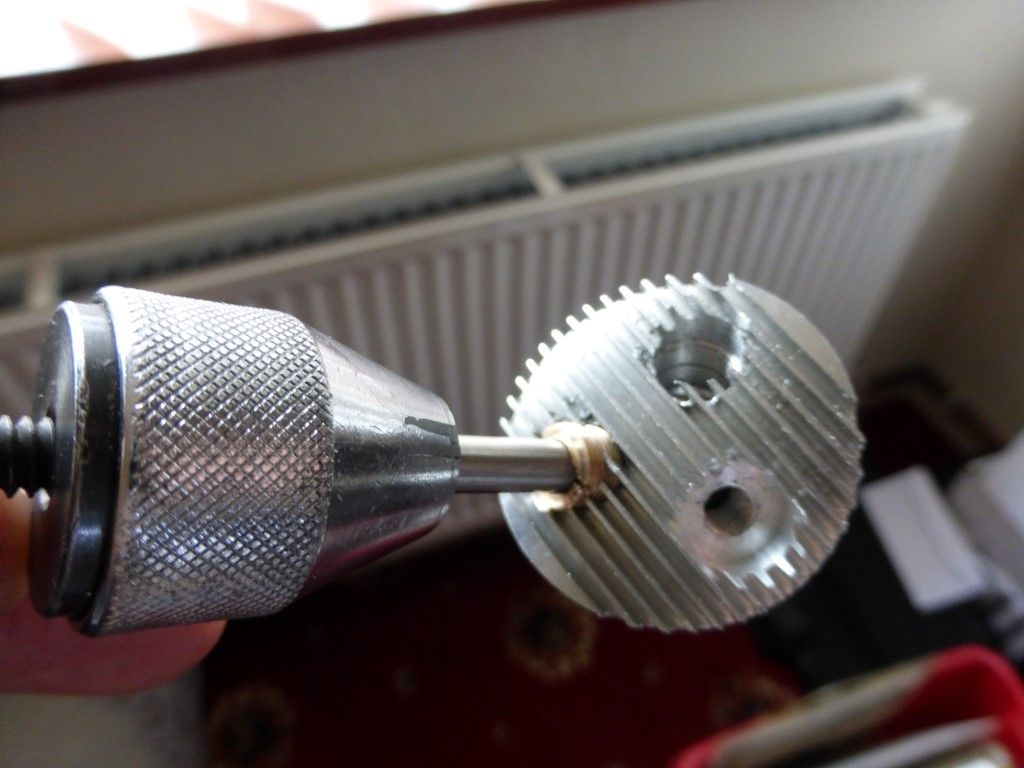
|
David K | 19/12/2018 16:05:12 |
258 forum posts 259 photos
|
The guides are screwed in with green permanent Loctite
the holes drilled in the cylinder head actually
came out in the correct place in the combustion chamber. I am happy to say the jig did its job. 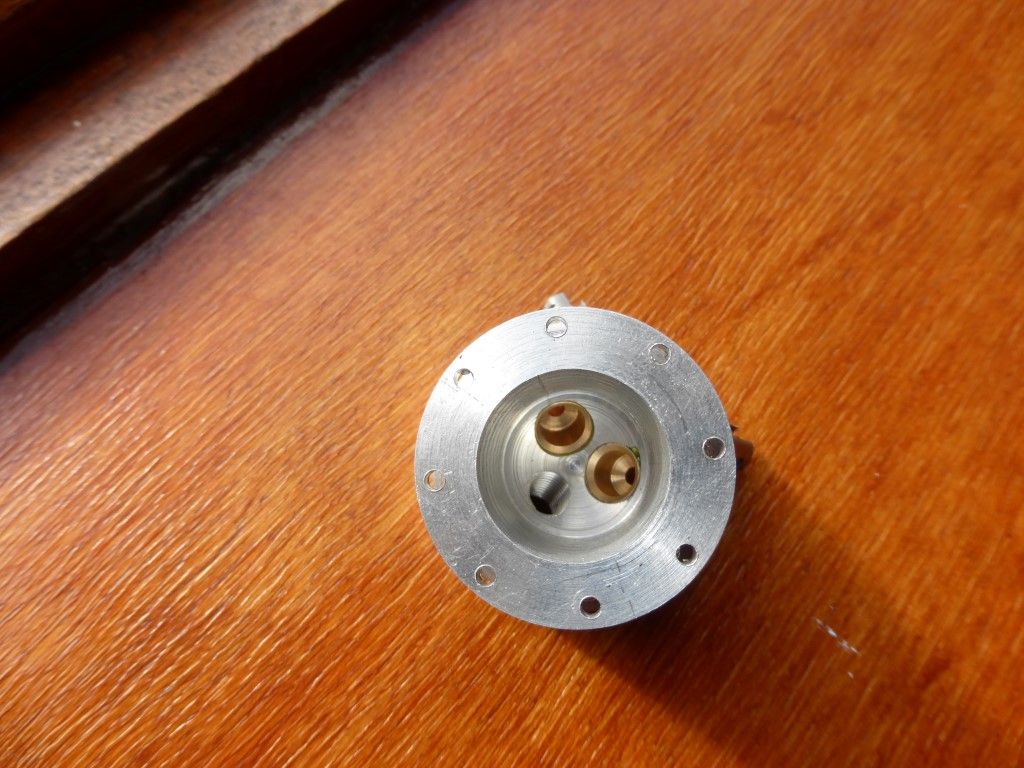
|
David K | 21/12/2018 16:50:30 |
258 forum posts 259 photos
| Next job is to drill the inlet / exhaust ports.
These are drilled from the centre at a slight angle to the valve guides.
The cylinders are nearly finished so each operation becomes more nervy ,
I would be gutted to mess up now.

|
David K | 21/12/2018 16:51:35 |
258 forum posts 259 photos
|
You can see from this picture were the drill breaks into the valve guide. 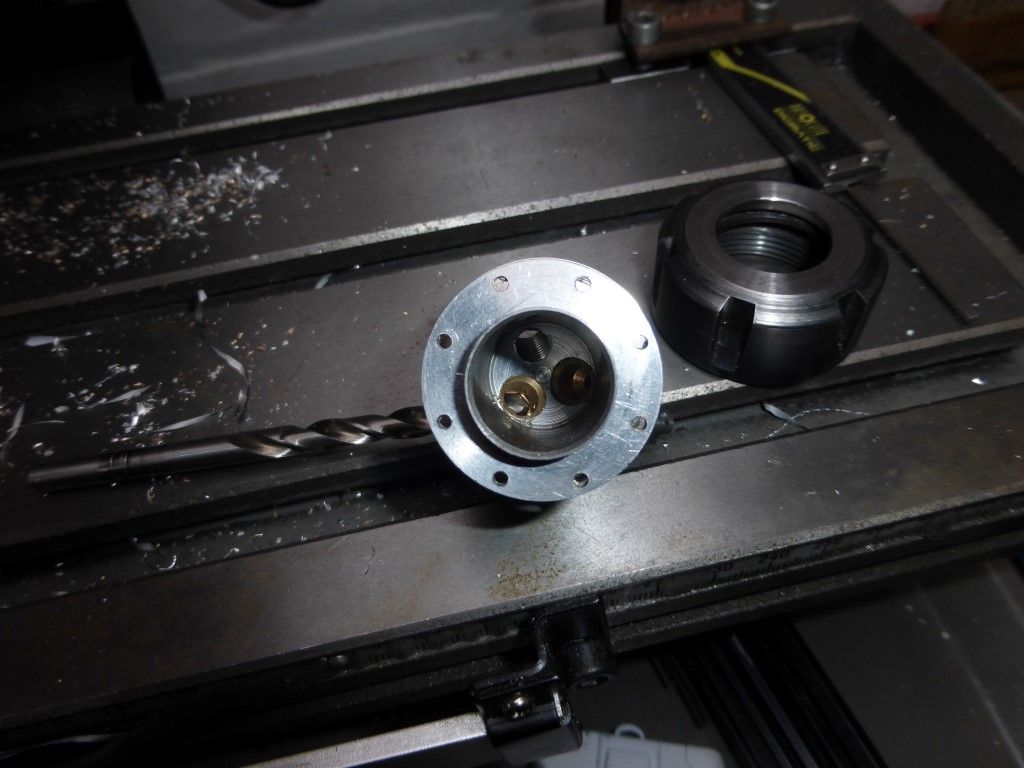
|
David K | 21/12/2018 16:54:53 |
258 forum posts 259 photos
| Finishing off the cylinders, I made a jig to cross drill the rocker posts and then
rounded the tops with a file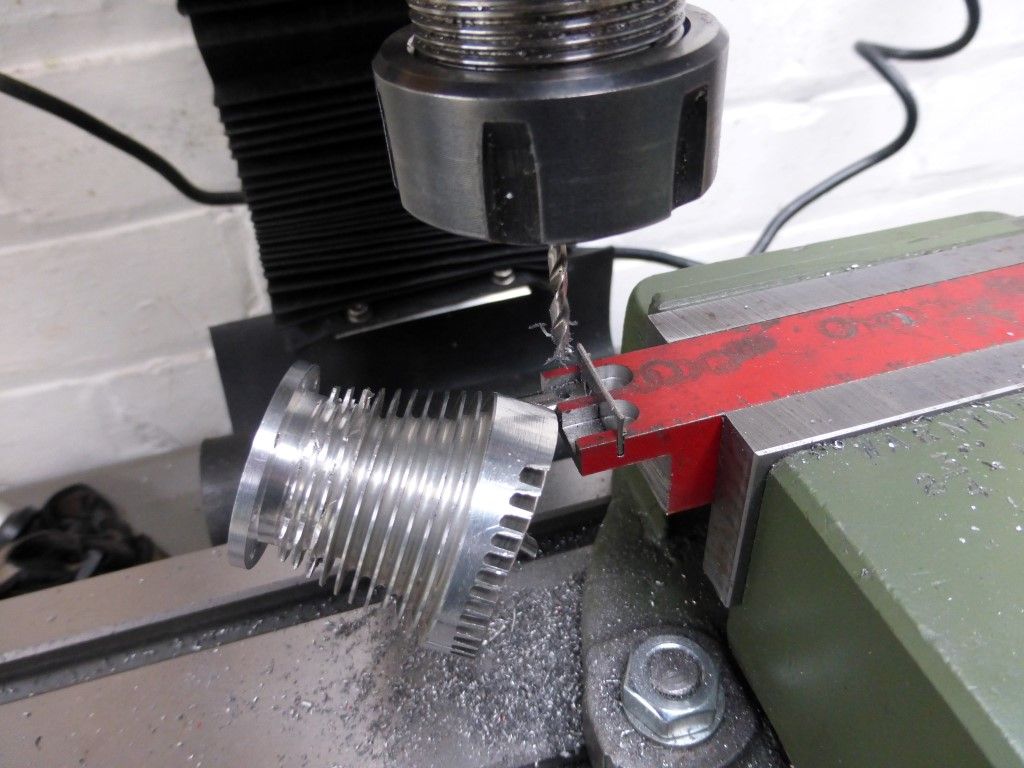
|
David K | 21/12/2018 16:55:51 |
258 forum posts 259 photos
|
The cylinder liners are made from seamless 4130 aircraft grade tubing. The tube will only
need a light hone ready for use.
I made an expandable reamer to hold the tubing while I cut the short lengths so I didn't
crush it. I turned a small chamfer on the inside edge to make it easier to fit the pistons.
These will be a push fit held in with Loctite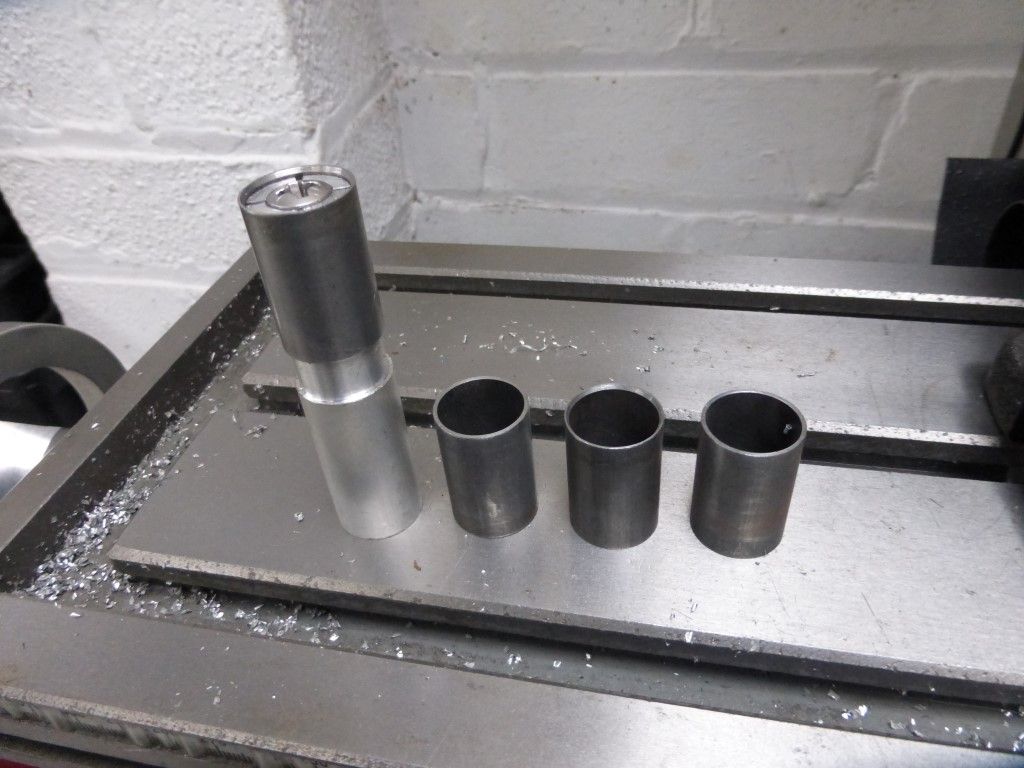
|
David K | 21/12/2018 16:56:50 |
258 forum posts 259 photos
|
That's it , all cylinders done , crankcase next 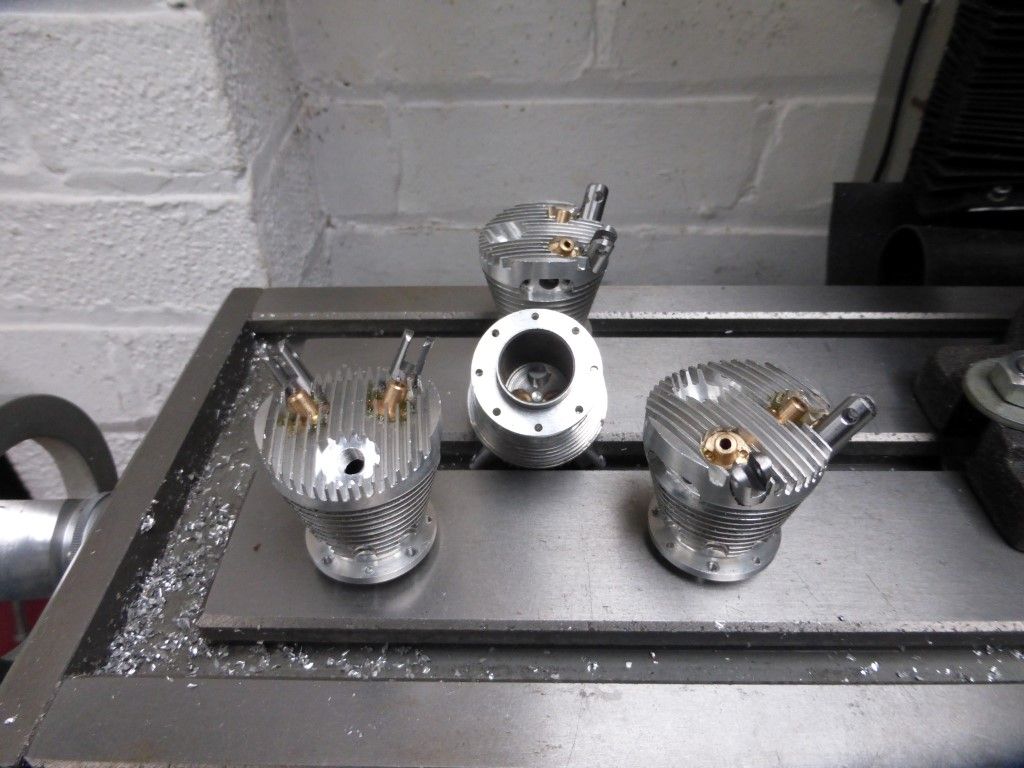
|
David K | 21/12/2018 16:58:59 |
258 forum posts 259 photos
| The crankcase has a timing gear fitted inside, this is one of the few items I need
to buy for the engine. It is an internal ring gear , 60 tooth , 48dp which I managed
to buy from HPC gears . The gear will need reducing in width and diameter so I
turned a boss on the end of some alloy bar. The gear was then tapped onto the boss and this was enough to hold it
in the lathe.
|
David K | 21/12/2018 16:59:18 |
258 forum posts 259 photos
| 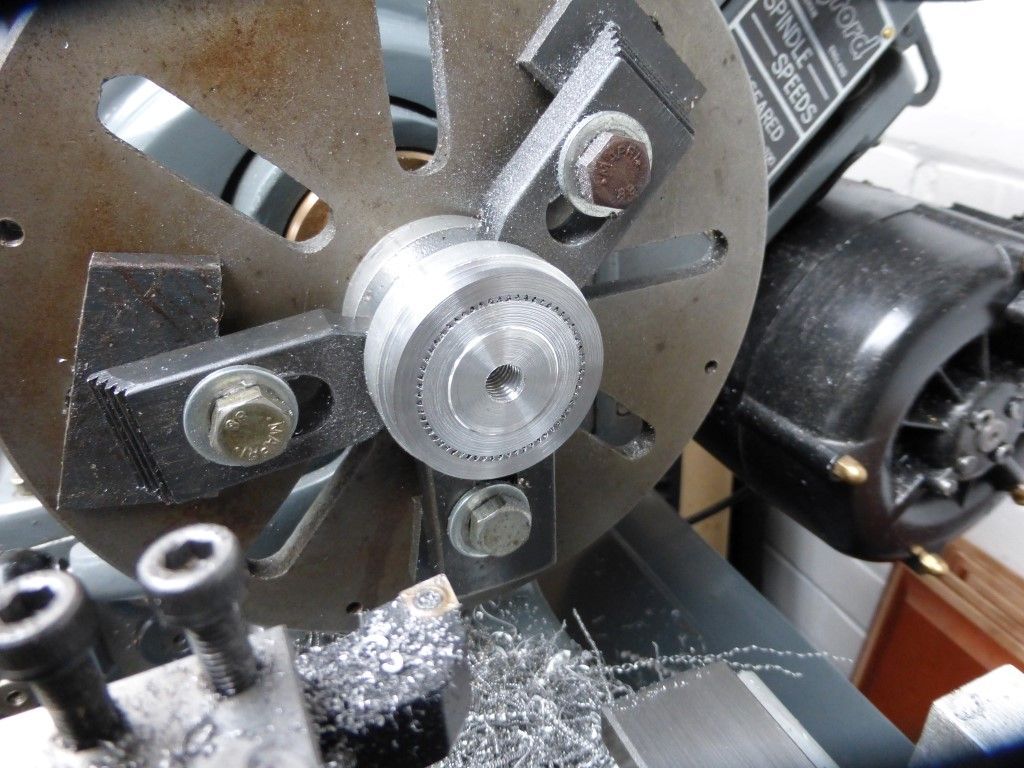
|
David K | 21/12/2018 17:00:18 |
258 forum posts 259 photos
|
I then transferred it to the mill and drilled the holes for mounting . 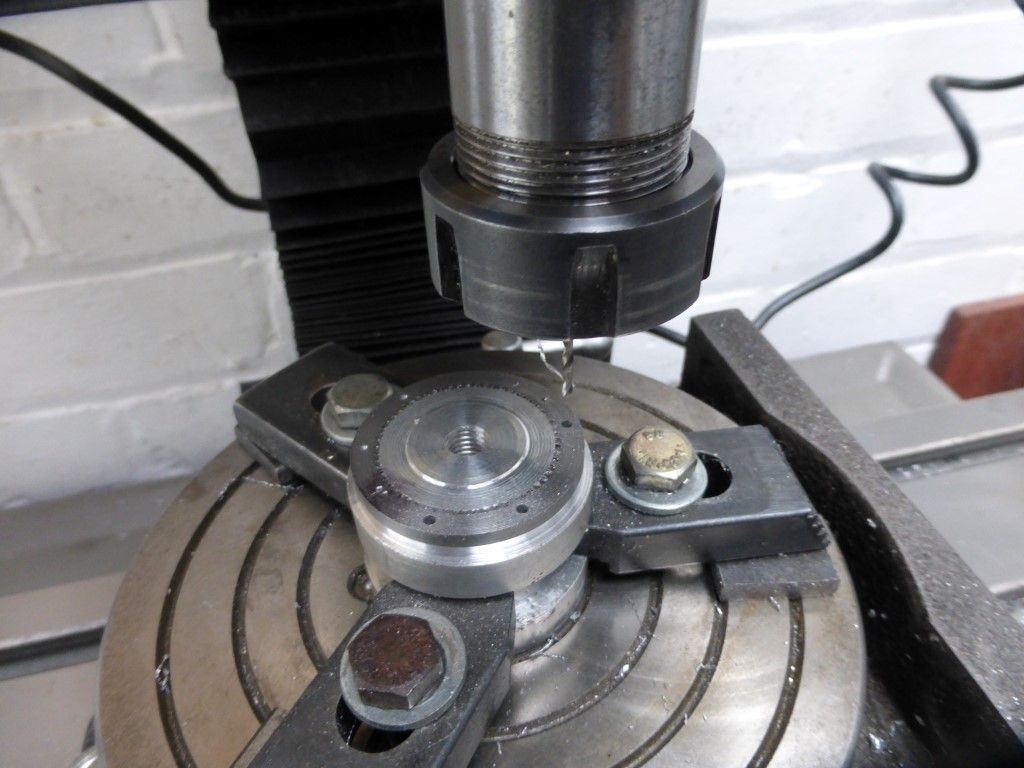
|
David K | 21/12/2018 17:01:30 |
258 forum posts 259 photos
|
To start the crankcase I cut a piece of alloy bar and mounted in the lathe.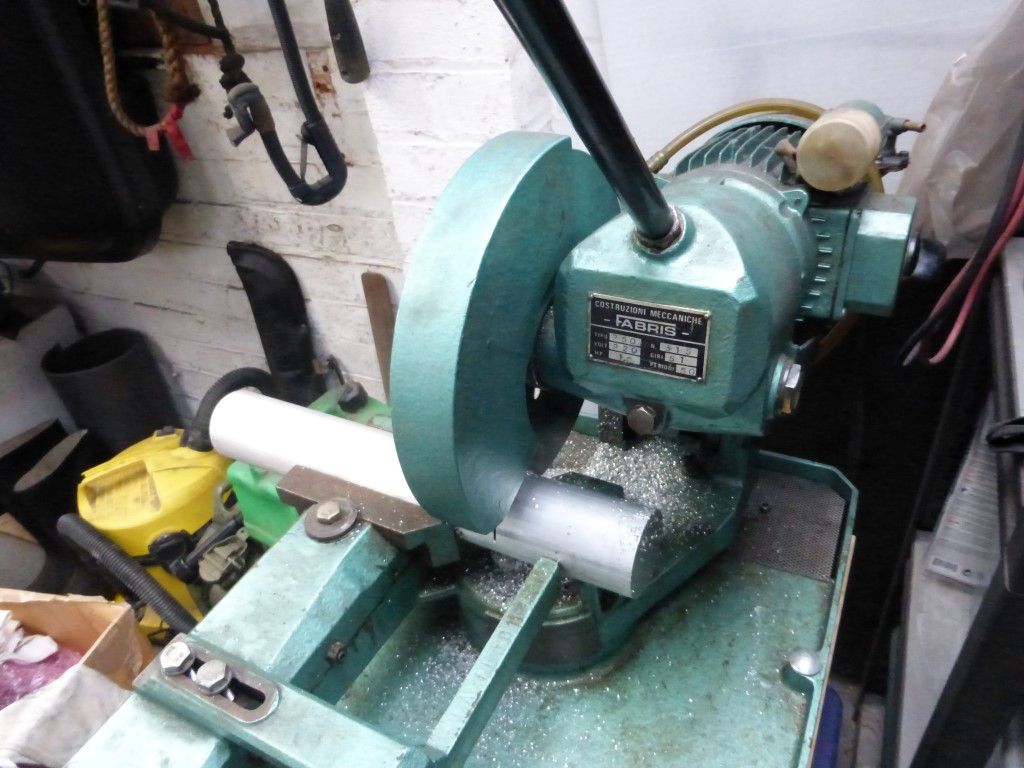
|
David K | 21/12/2018 17:02:27 |
258 forum posts 259 photos
|
After turning the ends square I started to turn the inside to the dimensions shown
in the plans. These consist of shoulders and pockets for the bearings, ring gear and clearances
for the crankshaft.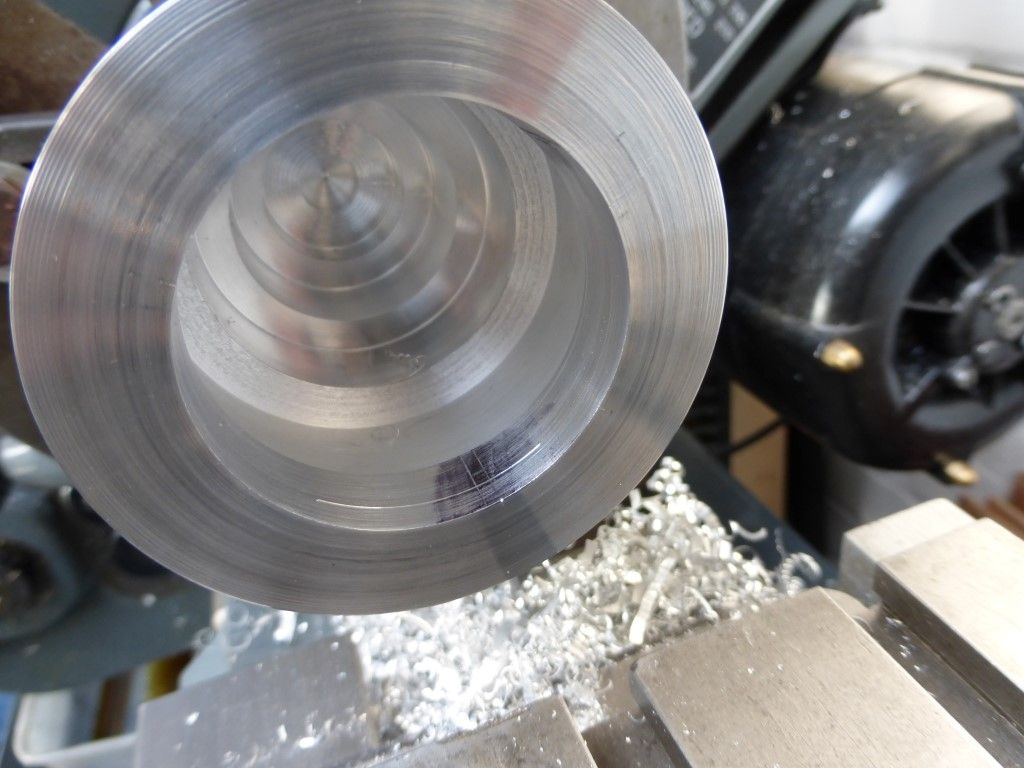
|
David K | 21/12/2018 17:07:14 |
258 forum posts 259 photos
|
Then the outside is turned to shape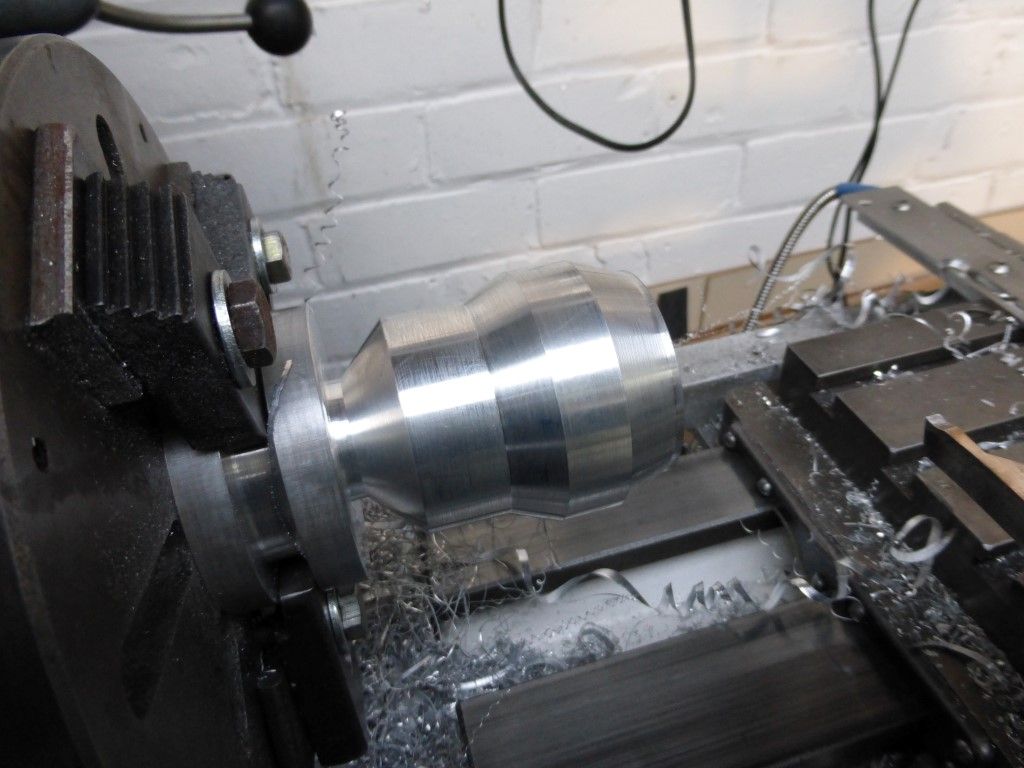
|
David K | 21/12/2018 17:08:08 |
258 forum posts 259 photos
| The crankcase is transferred to the mill and a flat is milled at 120 degree intervals
and a .75 inch hole is turned central on each flat for a snug fit of the cylinder liner.
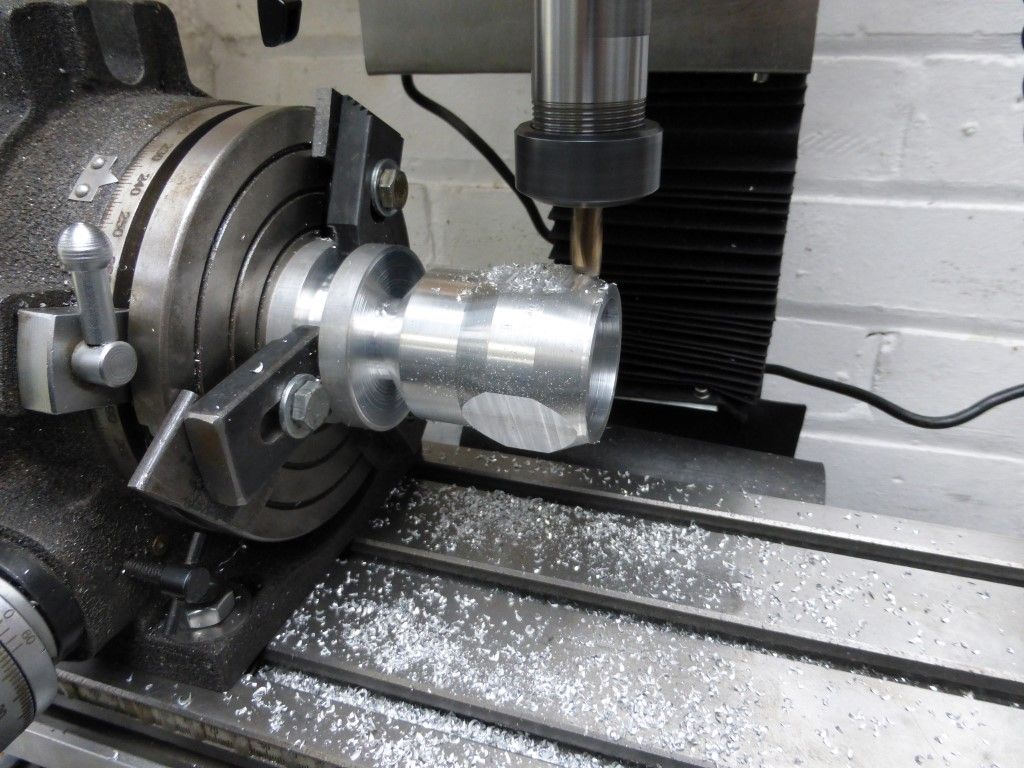
|