Thread: 3 cyl Pip engine |
22/12/2018 14:47:14 |
I also need two centres through the crank pin axes for machining the big end.
To do this the bar is fitted to two 'V' blocks and clamped in my mill vice on the mill.
I centred the mill spindle over the first centre drill and then moved the mill table
over to the crank pin axes and put a second centre drill. The bar was flipped 180 degrees
while still clamped to the 'V' blocks and the process was repeated.
|
22/12/2018 14:46:56 |
Crankshaft. This starts off with a piece of 6'' by 1'' E19 steel round bar.
The bar is placed in the lathe , faced off and centre drilled both ends.
These centres are through the main bearing axes and will be used to mount
the steel for machining.
|
22/12/2018 14:45:02 |
The gear is parted off and machined to the correct thickness, then heat treated to harden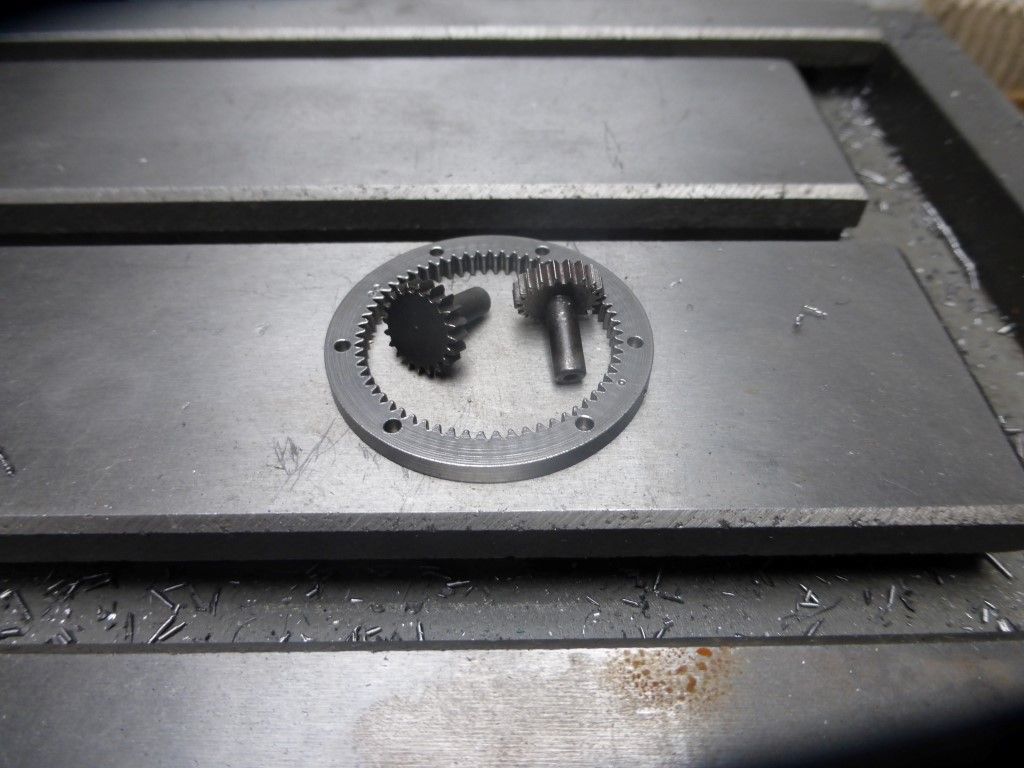
|
22/12/2018 14:43:58 |
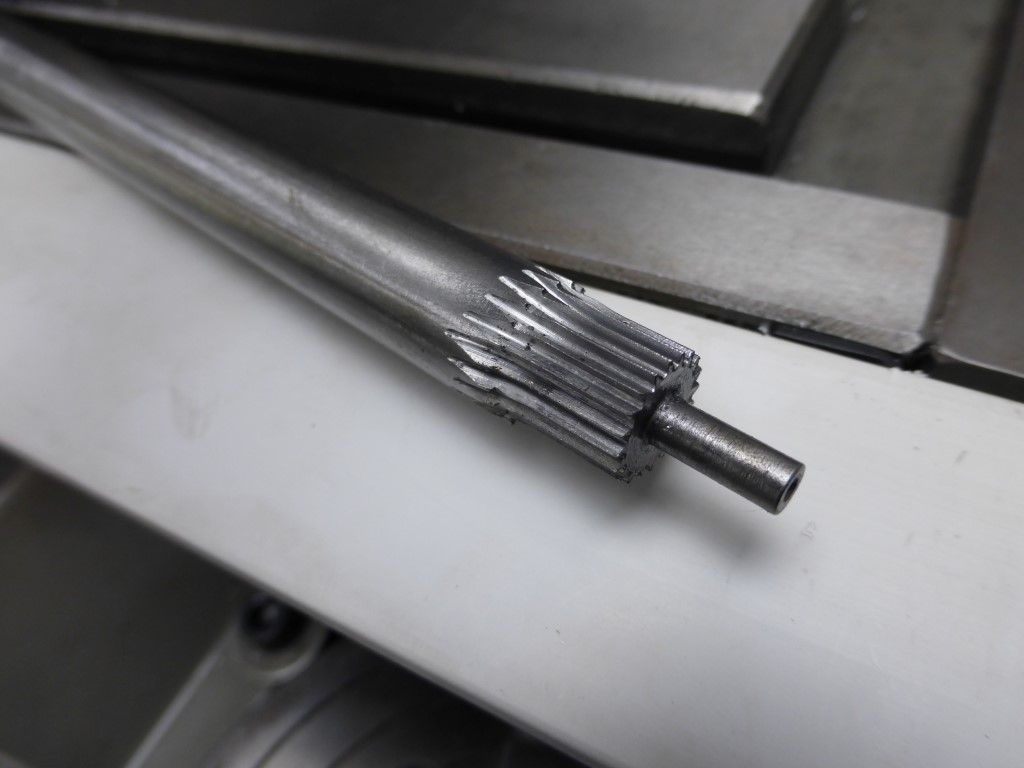
|
22/12/2018 14:43:23 |
Setting the cutter dead centre I cut along the shaft at slow speed with plenty of cutting fluid.
Each tooth is cut in one pass.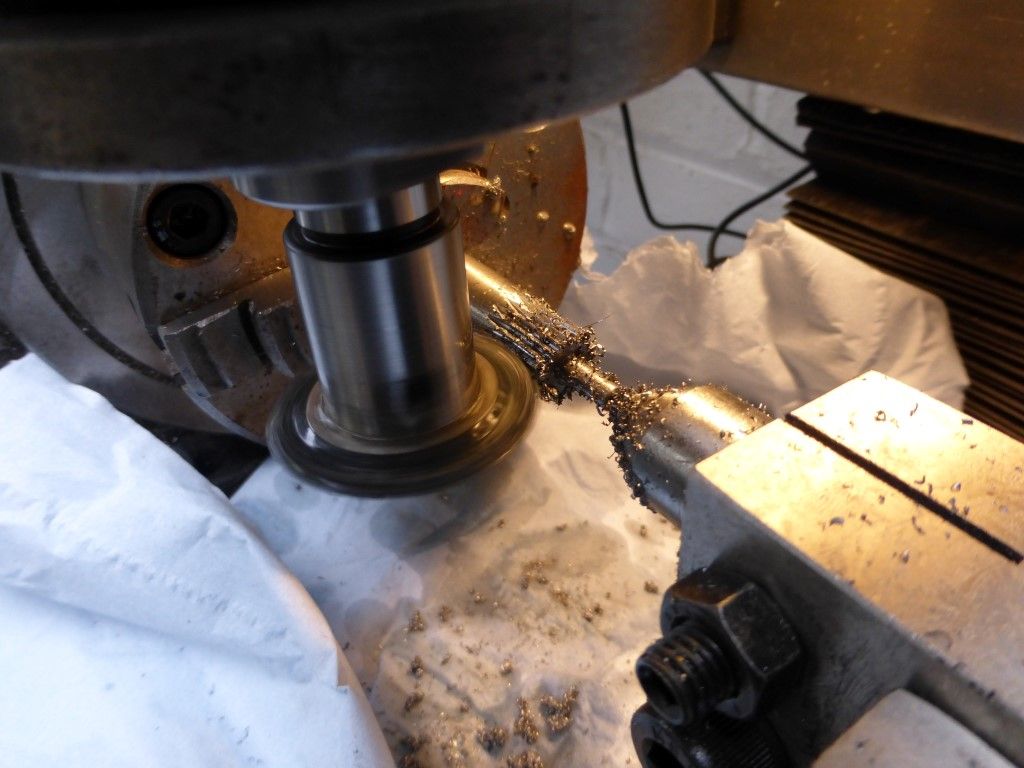
|
22/12/2018 14:42:28 |
I turned the gear blank onto the end of some silver steel then mounted it in the rotary table
on the mill.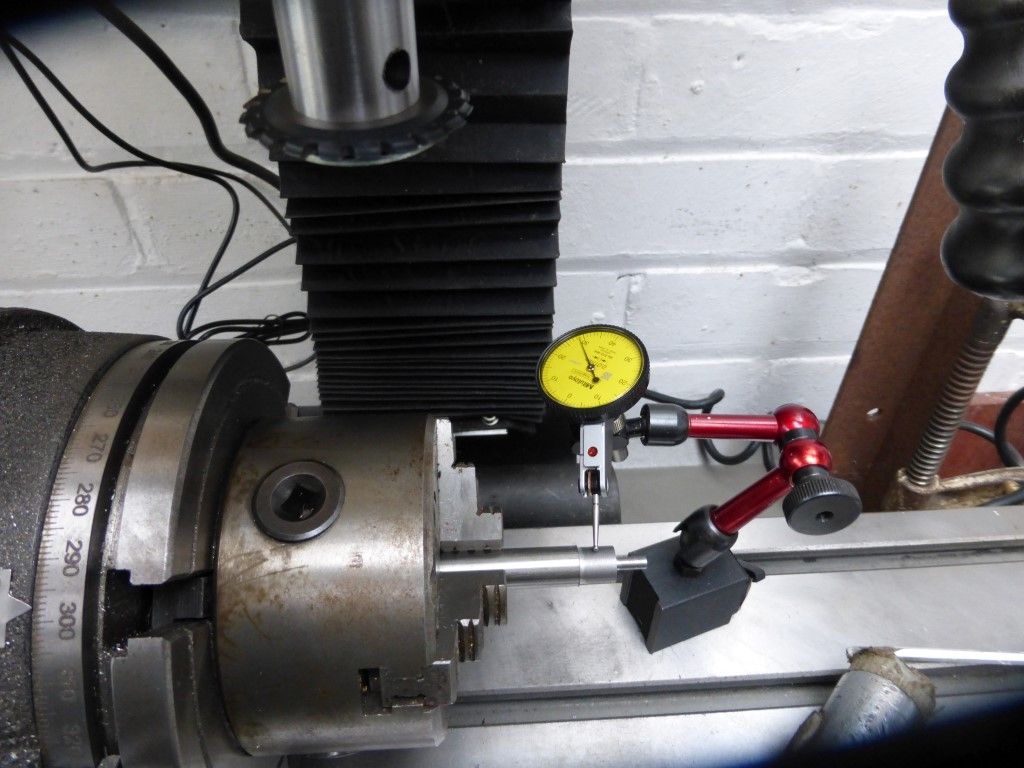
|
22/12/2018 14:41:49 |
The planet gears in the plans are made from shop bought gear stock, this is basically a length
of bar with gear teeth cut along it and you cut and machine up your gears from this.
I could not find any bar stock for a reasonable price as its usually made to order so I decided
to make my own gears.
|
22/12/2018 14:38:58 |
Yes the broken tap was not too costly this time, although I have managed to go through a few M2 taps.
|
21/12/2018 17:27:34 |
Trial fit of cylinders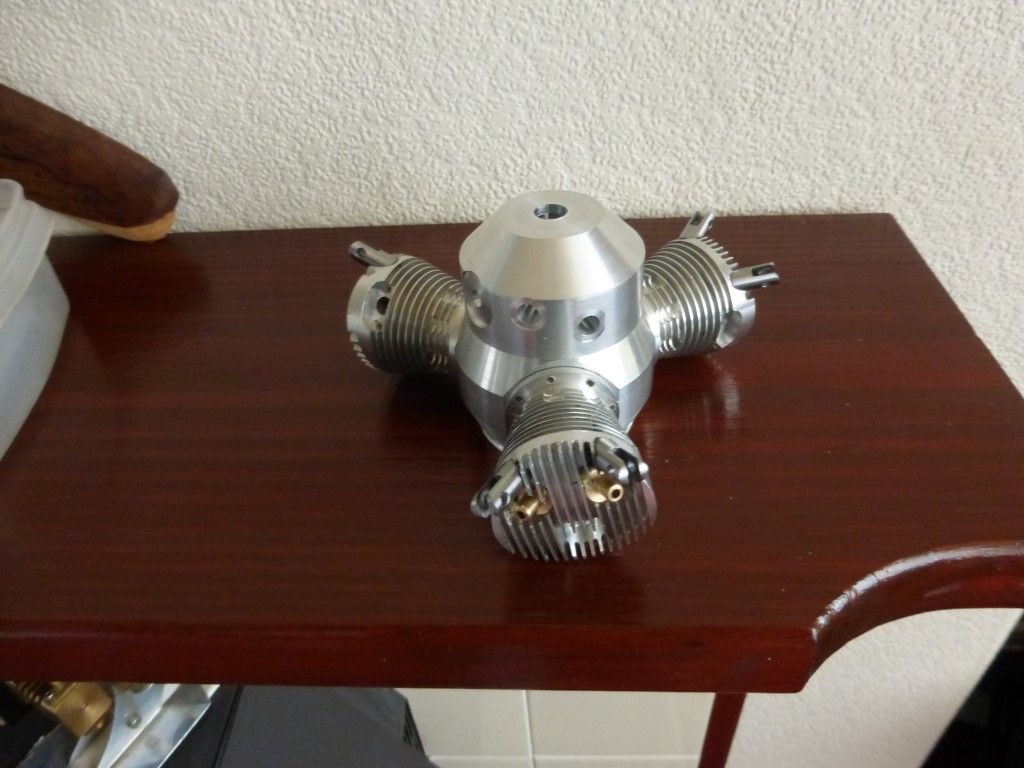
|
21/12/2018 17:23:14 |
Ring gear holes lined up
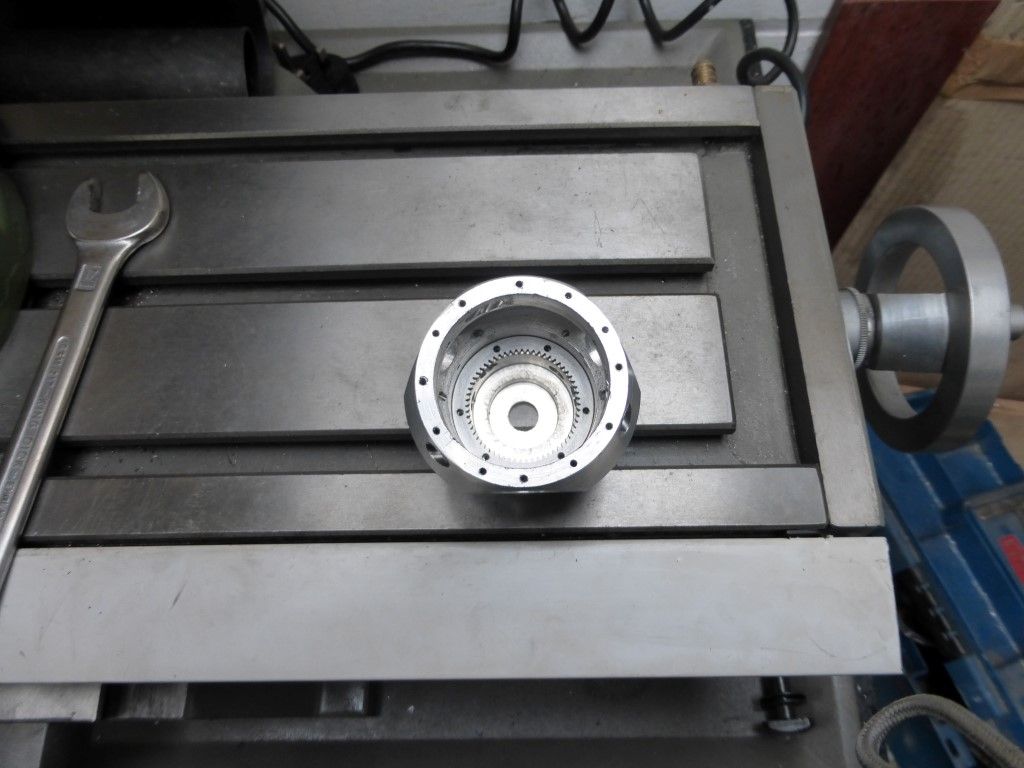
|
21/12/2018 17:22:15 |
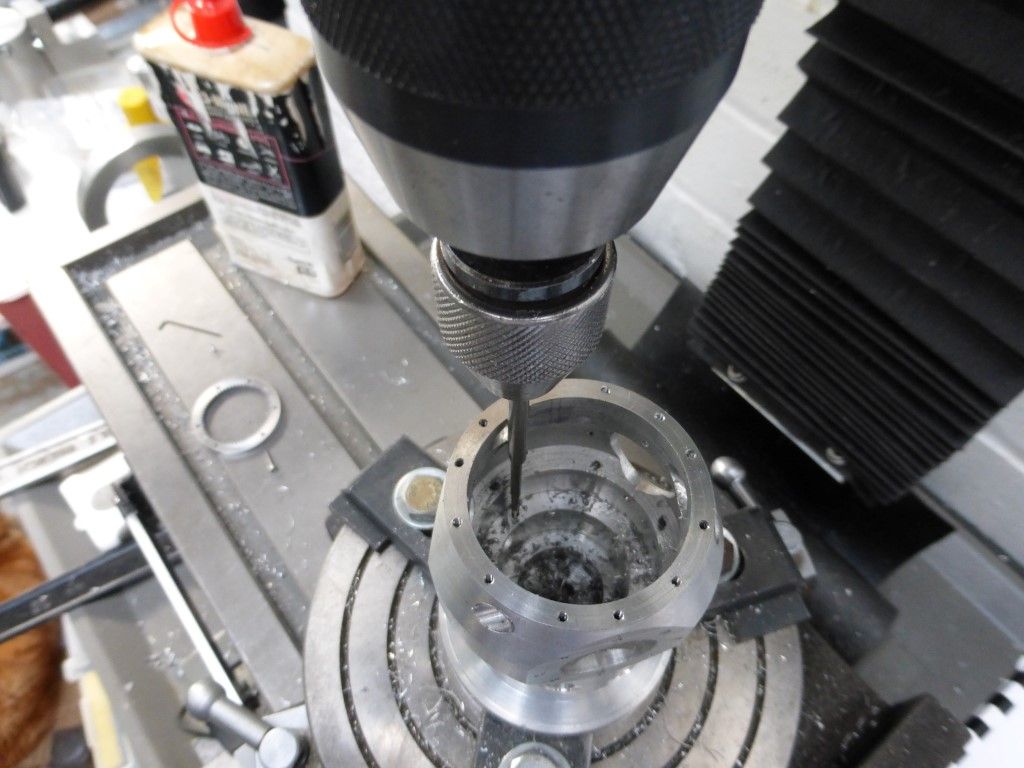
|
21/12/2018 17:21:36 |
The locating holes for the timing gear are drilled and tapped inside the crankcase. For this I
had to buy an extra long centre drill and make an extension for the M2 tap.
You can see the timing gear resting on the mill table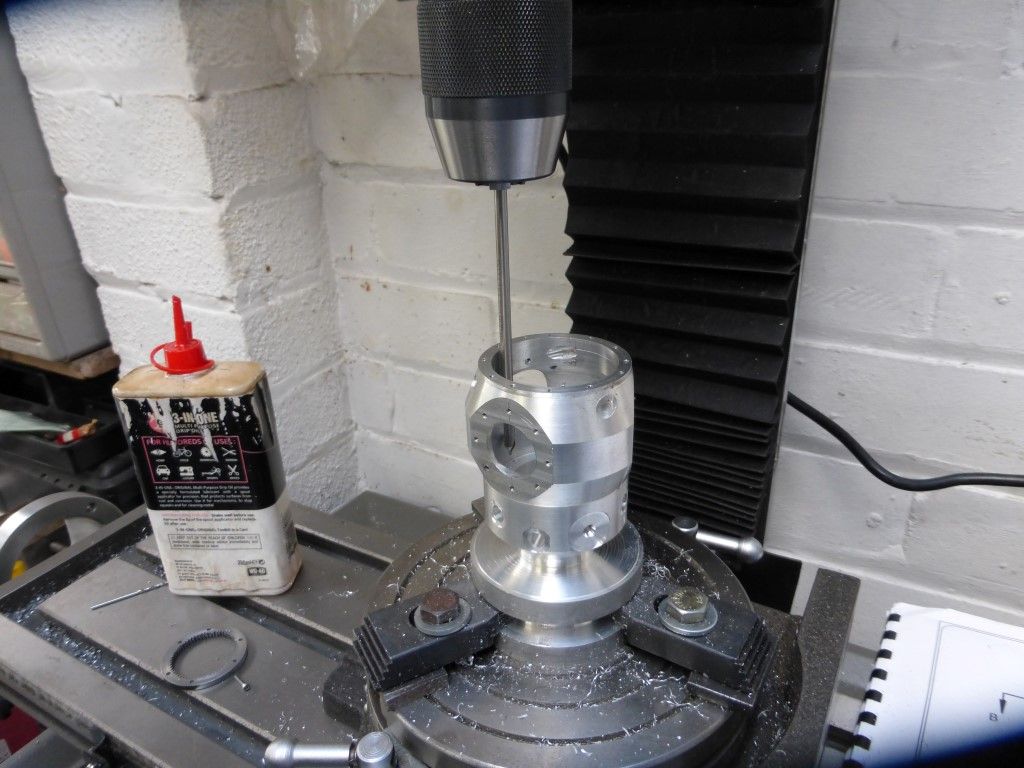
|
21/12/2018 17:20:50 |
Centring the rotary table flat on the mill I then centre drilled , drilled and tapped
the M2 holes for securing the end plate.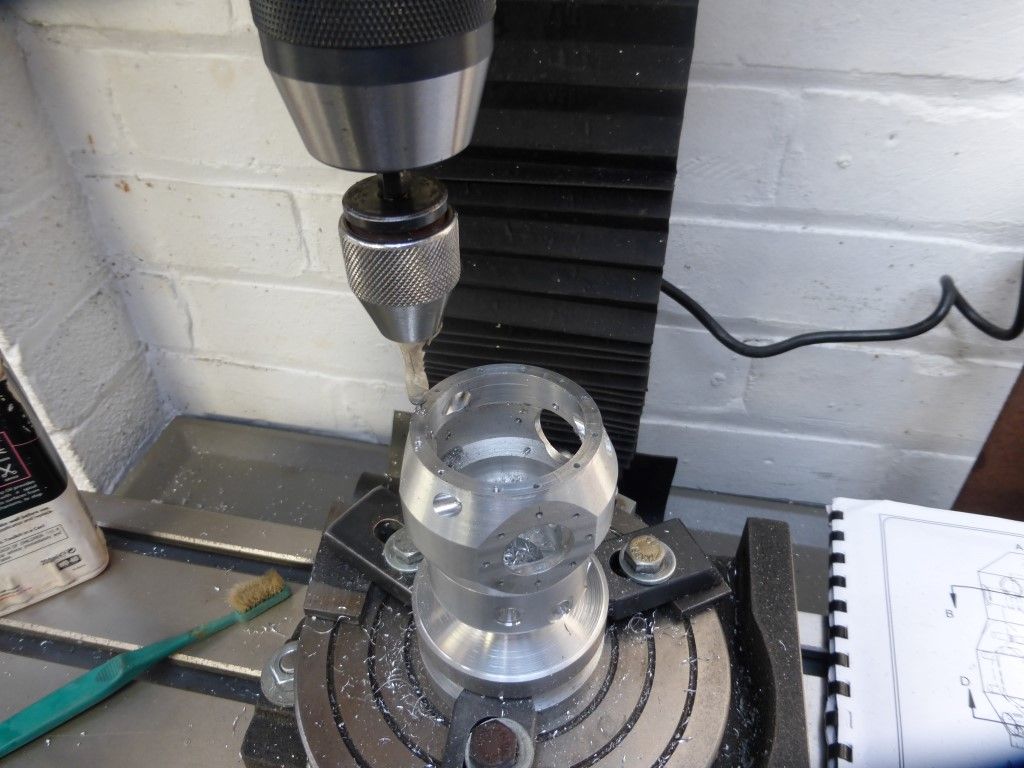
|
21/12/2018 17:19:40 |
A flat is milled and centre drilled ready for the carburettor mount hole. I am not sure on the
carburettor I will be using yet so I will complete this when I buy the carb.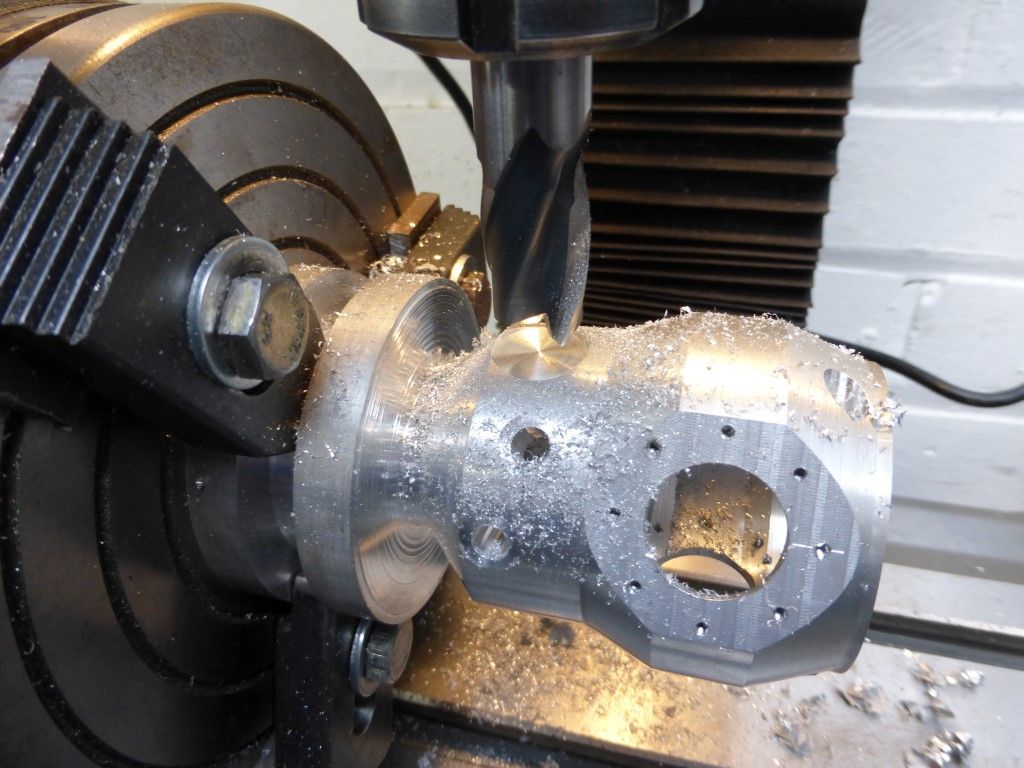
|
21/12/2018 17:16:23 |
Then drilled the 3 holes for the inlet manifolds which will be in copper tubing .
The engine works a bit like a 2 stroke in that the carb feeds into the crankcase
and then the charge is transferred up to the inlet port. 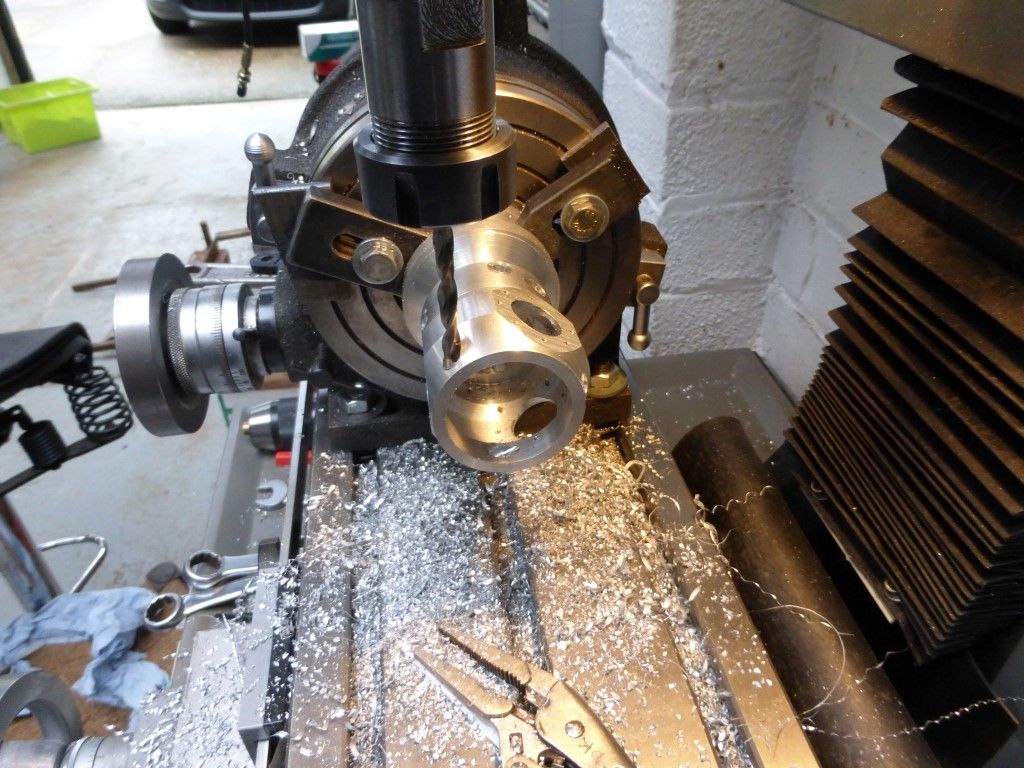
|
21/12/2018 17:12:27 |
Once the chemical metal had set I finished the remaining holes then moved on to drilling
the holes for the 6 push rods [ 2 per cylinder ]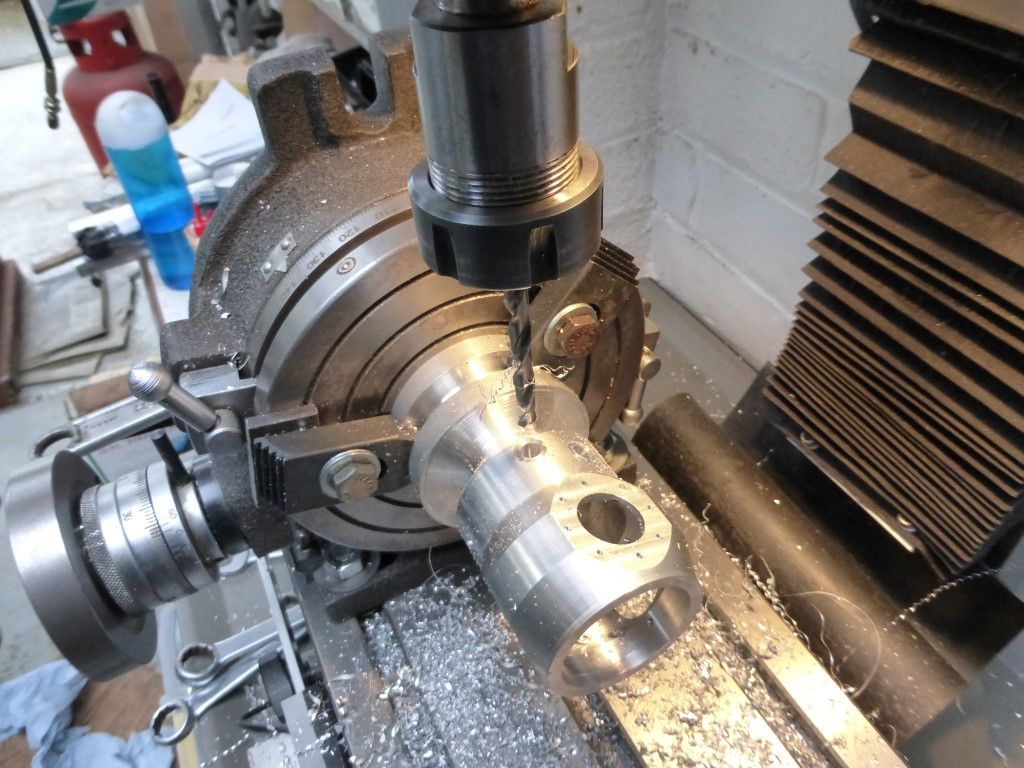
|
21/12/2018 17:11:04 |
Luckily I had enough of the tap to grip and remove so after completing this hole I then drilled
the next holes in the wrong place. Time to walk away and have a cup of tea, but not before
filling the wrong holes with chemical metal.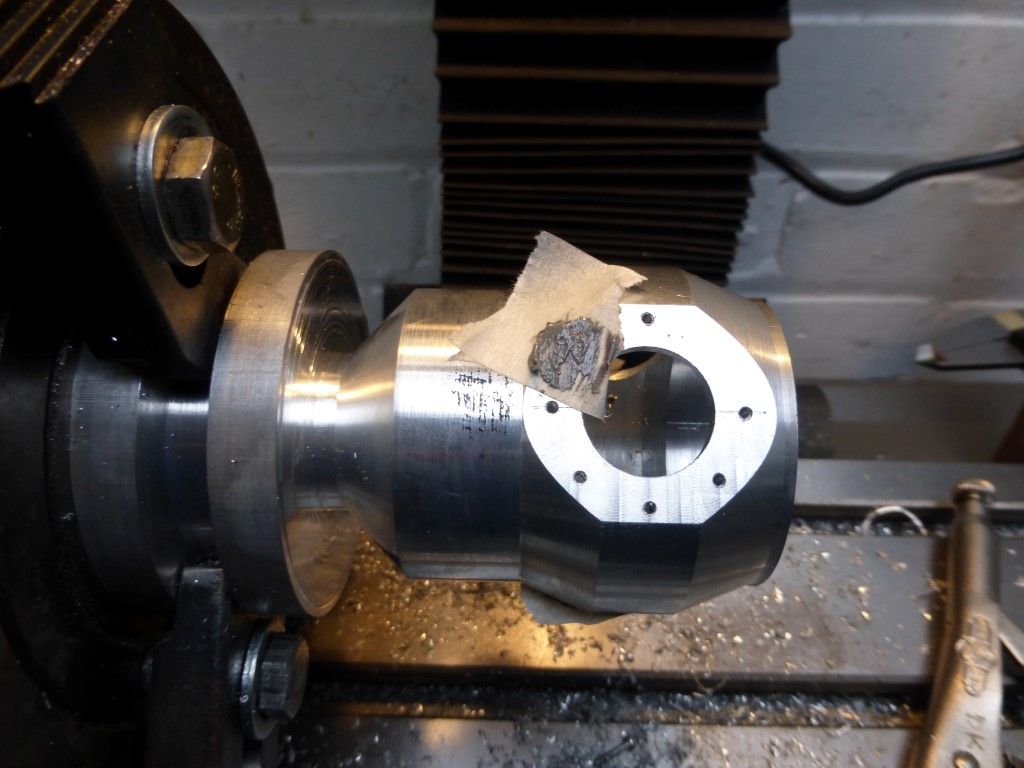
|
21/12/2018 17:10:32 |
8 holes for each cylinder so 24 in total, on the 20th hole this happened, 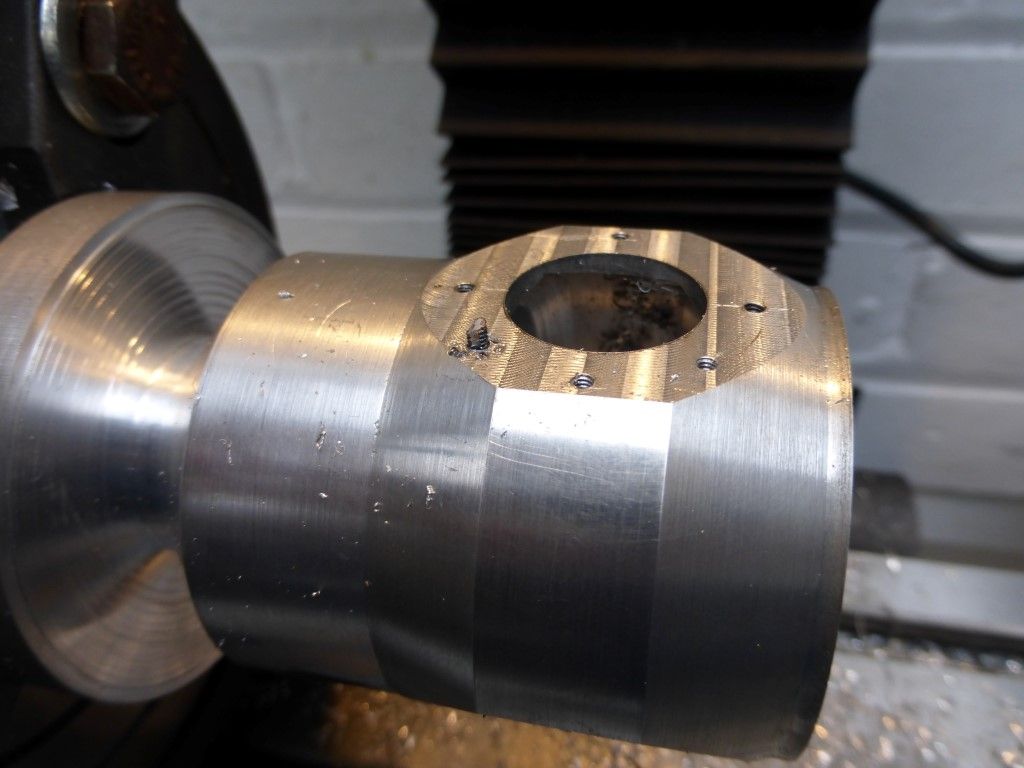
|
21/12/2018 17:09:07 |
M2 mounting holes are then drilled and tapped to match the cylinder mounting flange.
You can see the false cylinder I made which I used to check the alignment of the holes
before drilling. 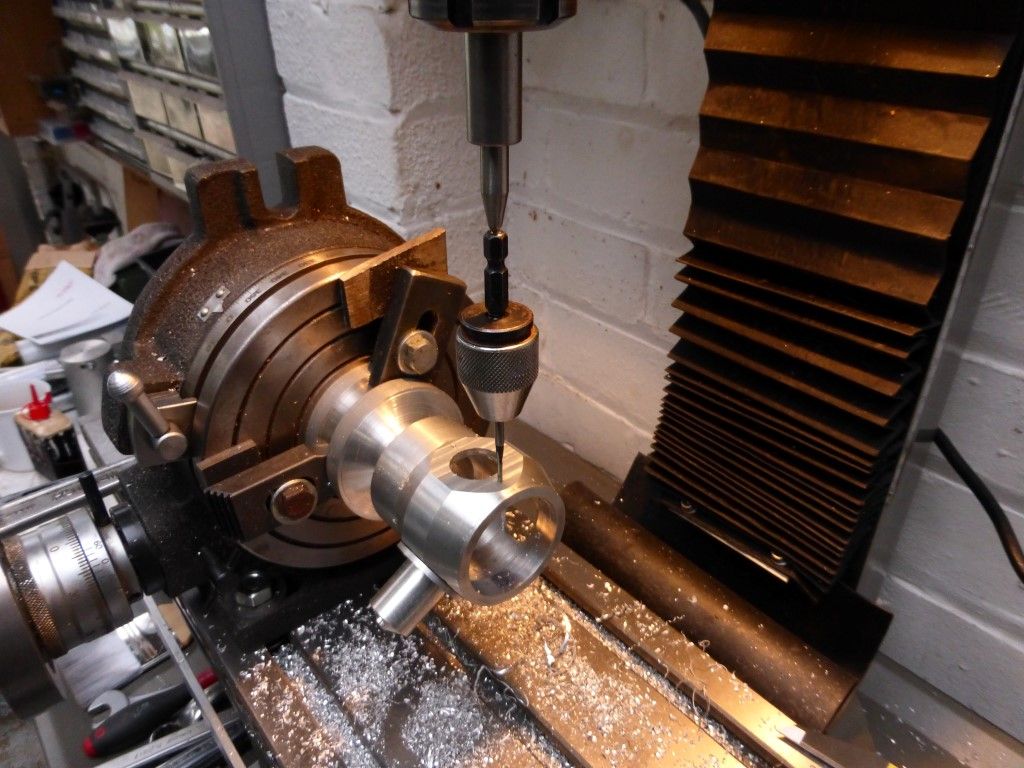
|
21/12/2018 17:08:08 |
The crankcase is transferred to the mill and a flat is milled at 120 degree intervals
and a .75 inch hole is turned central on each flat for a snug fit of the cylinder liner.
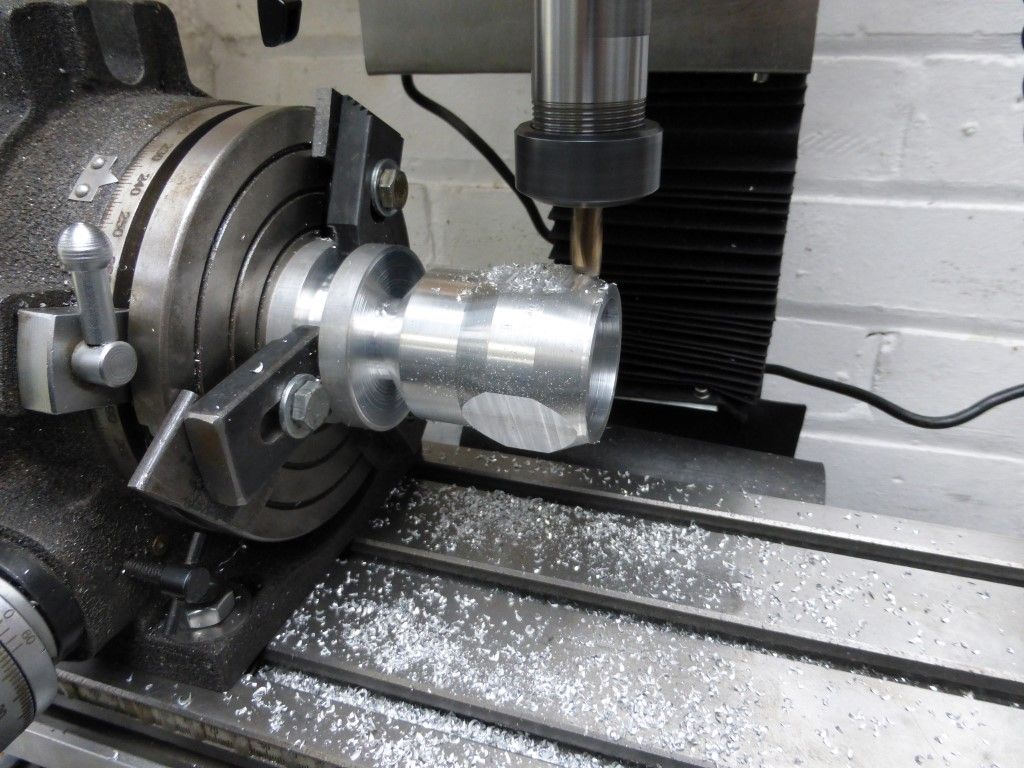
|